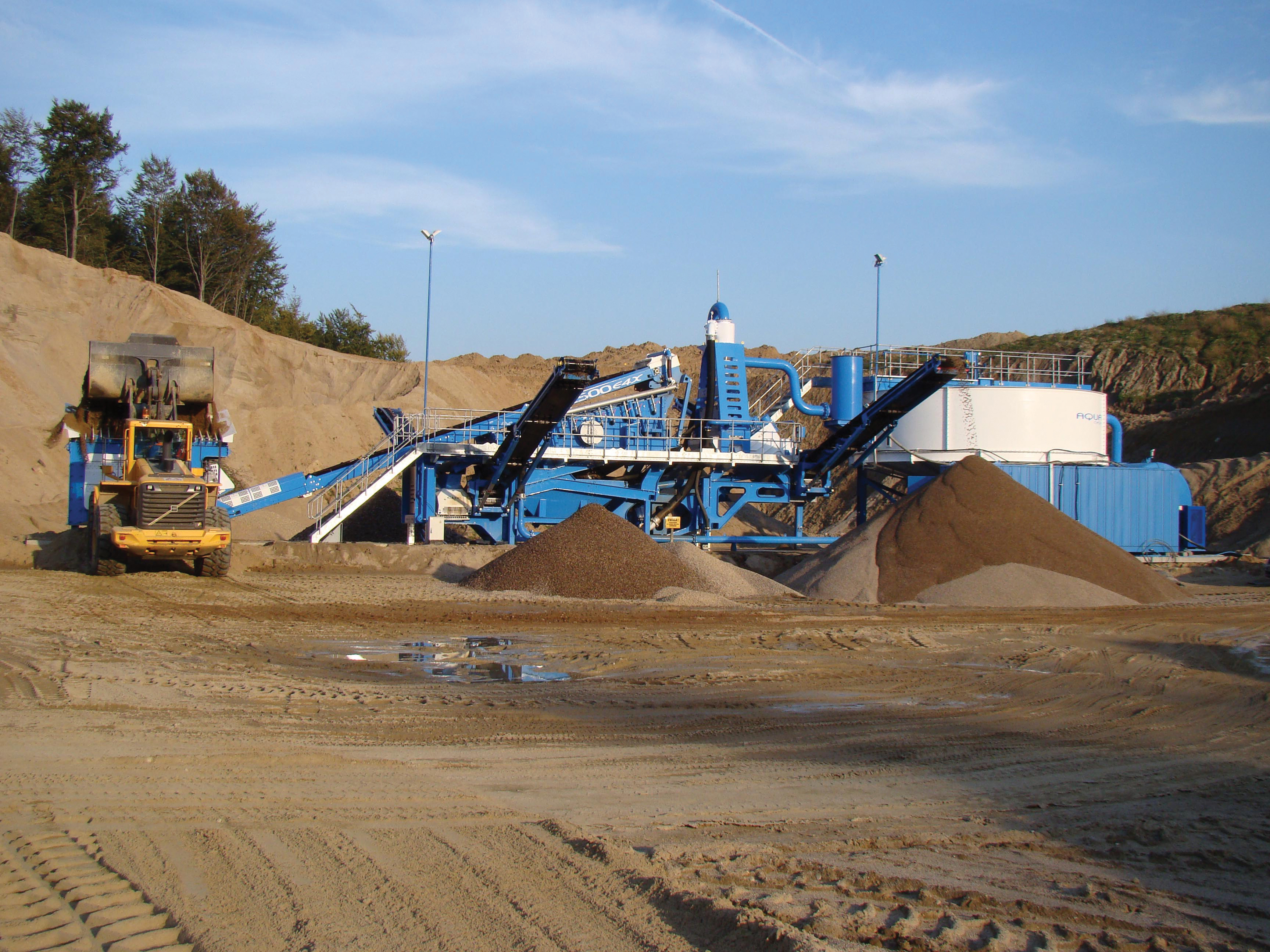
Suppliers of water filtration and recovery equipment are installing ever more sophisticated plants and there is more to come as a number of factors drive forward technological developments. Jon Masters reports
If there is a standout characteristic of water treatment to be observed in aggregates sectors, it is its very bespoke nature of a highly variable kit of parts. This may sound like stating the obvious, but there is a direct relevance to this in how dewatering and water recovery equipment is developing
There are trends emerging of more technologically advanced equipment, sometimes designed to process large quantities of material, or to provide efficient full processing with minimal loss of water in enclosed systems. Demands are mounting for ever more sophisticated washing and water recovery plant, but just as virtually every site has its own unique requirements, the make-up of demands driving equipment development is complex.
Trends can be seen in current plant installations for a variety of reasons, but in all likelihood, it will be suppliers' work with each new bespoke installation that pushes the technology forward
UK-based
Mobile solutions
"From a planning perspective, the tighter regulations that our customers are facing in many locations are causing a shift away from long term static facilities toward mobile installations that can easily be removed from site once the project is complete," he said. "This is driving increasing demand for lighter and more compact technology which is nonetheless robust and easy to maintain
"We are seeing a lot of demand for complete systems - including pumps, cyclones, dewatering cyclones or classifiers - that are either mounted on skids or trailers and can be delivered to site, run for the requisite period of time and then easily removed." Secondly, said Cook, Weir's customers are reporting the majority of easily extracted pure natural aggregates to have already been exploited from many of Europe's major sand deposits. Clients are increasingly faced with less pure sources
"This has resulted in a growing requirement for more sophisticated separation and classification equipment at a greater number of sites in order to ensure the same quality of end product is delivered. To go with the classifiers we have seen increasing demand for control systems to allow the separation of the detritus to be adjusted in response to variations in the feed to the plant," Cook said
For environmental and cost reasons, Weir's customers are also facing a growing imperative to reclaim as much water as possible from slurry mixtures. This is compounding the need for more advanced equipment across the board. Cook said, "We are now frequently faced with briefs that demand just 12% to 15% water remaining in the dewatered product, where traditionally 20% to 25% was considered acceptable with natural drying. Greater reduction of water content is driving demand for dewatering cyclones and dewatering screens at an increasing number of sites." Manufactured sands created from crushed rock are now being discussed more meaningfully as a serious proposition by aggregate producers, Cook added, as they look for new revenue streams and face up to depleted stocks of sand. "If this is borne out, it will further increase the industry's appetite for advanced separation systems, as manufactured sands typically feature much greater variation in particle size than natural sources," he said
"As more stages are introduced to the process, the pressure will be on equipment suppliers to deliver an increasing range of tough yet easily controlled separation systems that are also highly cost effective. This could be a major arena for innovation in the coming years." Italian equipment supplier Fraccaroli & Balzan manufactures a full range of water filtration and recovery plant from its Verona site for various international quarrying and construction sectors
According to its area manager for North America, northern Europe, the Middle East and India, Andrea Giglioli, the market for this equipment in aggregates sectors continues to grow. Environmental legislation is still the principal driver of demand, particularly in Europe where recently joined members of the
For the initial main settlement stage
of water treatment, Fraccaroli offers traditional vertical clarifiers, typically of 5m diameter and 10m in height, and radial decanters of 9m to 12m in diameter but only up to 4m in height. While flow rate dictates the necessary size of unit, criteria for selection of vertical or radial plant is a balance of meeting height restrictions of planning or environmental constraints against cost - greater foundations are needed for the radial silos
Whichever option is chosen, combination with the latest filter press plant to extract more water from the settled slurry sludge in a closed loop system, allows 95% water recovery. Some of Fraccaroli's clients are doing this on a grand scale, treating flow rates up to 200m3 per hour with big filter presses with up to 150 2m plates (supporting filter screens), or installations with multiple settlement tanks and presses. One such system, at the Nordkalk hard stone quarry in Poland, contains two decanters and three presses of 100 plates, with another filter press expected to be installed soon
"Customers are demanding bigger and bigger machines, with no limit it seems," said Giglioli. Fraccaroli's clients are also requesting mobility. The challenge is to build plant of high capacity with a compactness and ease of assembly for moving equipment within and between quarry sites
"Another thing we're facing is the need for plants to be more and more sophisticated," Giglioli said. "It is now taken for granted that water recovery processes are fully automated, with a robotic cleaning device for washing of filter screens, and it is becoming more important to include automatic control of flocculent in the system."
Increased technology
Remote monitoring and control of customers' equipment from Fraccaroli's Verona base is now offered as part of servicing provision. Additionally, quarry operators are asking for system connections to their mobile phones to allow them to receive information on plant performance - particularly alerts if something is wrong. Overall, a lot more sophistication and computer technology is going into water recovery systems
"Generally these plants have to be running 24 hours a day, seven days a week. Automation is vital for operations and maintenance as well. It is now normal for plants to run continuously for three to four months before any down time is needed for changing filter screens. Robotic screen cleaning keeps the plant operational in the interim. Customers will see more of this automation coming into water recovery systems," Giglioli said
For an indication of how water recovery technology is developing, look to construction and demolition (C&D) waste processing in the UK, said
While the principal driver of demand for water recovery at quarry sites is environmental legislation, C&D processing firms have for some time had this and tight restrictions on space to contend with, particularly in the urban locations these operations typically inhabit close to the source of C&D waste. As making better use of land to realise its value becomes more important within the aggregates sector, with increasing need for reducing water consumption, it is likely to follow the lead of C&D processing
Kelly said, "The UK is currently the market leader in C&D waste processing and with legislation developing it is likely the rest of Europe and worldwide countries will follow. Likewise, more producers within the aggregates sectors are likely to adopt full water treatment and recovery plants as pressures on land use build." Kelly gives a C&D waste processing site near Nantwich in Cheshire, England, as example of what is possible. The site is washing 120tonnes of C&D waste per hour, using up to 300m3 of water every hour, on a site less than three acres in size. The customer is using CDE's screening and washing equipment, plus a fully enclosed cyclical water recovery system incorporating CDE's AquaCycle thickener and GHT filter press, as well as its FlocStation flocculation and AquaStore tanks and pumps. The upshot is a processing operation being topped up with water through a 25mm pipe due to 97% water recovery, on a remarkably small site
"We believe the real driver of advances in this technology is the need for expertise, to get the most out of the system in a small area of land take," Kelly says. "We recently commissioned our own study of silt thickening and settlement. Other suppliers are offering larger plants but our study shows it's about clever use of equipment to get optimum performance. Accurate rate of flocculation and settlement rather than size of plant is important to achieve the critical cubic capacity."
Careful control
CDE also offers fully automated control of its plants, but does not recommend this, "because there is nothing better than what can be seen with the eye and manual monitoring of performance", Kelly said. "The de-sludging process of our plants is fully automatic and we recommend the flocculation make up process is automated, but the actual quantity of polymer we have seen working against the system. Automation can get this wrong
"The main variable in dewatering and water recovery is the nature of the material brought to the plant. If adjustment is needed to the flocculation polymer, we recommend the operator does this manually, to help promote a good 'feel' for the plant; this also overcomes the potential problem of overdosing the polymer." Kelly summarises the key drivers of advances in water treatment and recovery plant as demands on use of land and more cost effective processing overall, given environmental and health and safety legislation
There remains however, the critical issue of whether investment in automated water treatment plant is money well spent in comparison to maintaining well managed settlement ponds. "Our model shows a return of the investment within months, using our customers own data of capital and running costs," Kelly said.