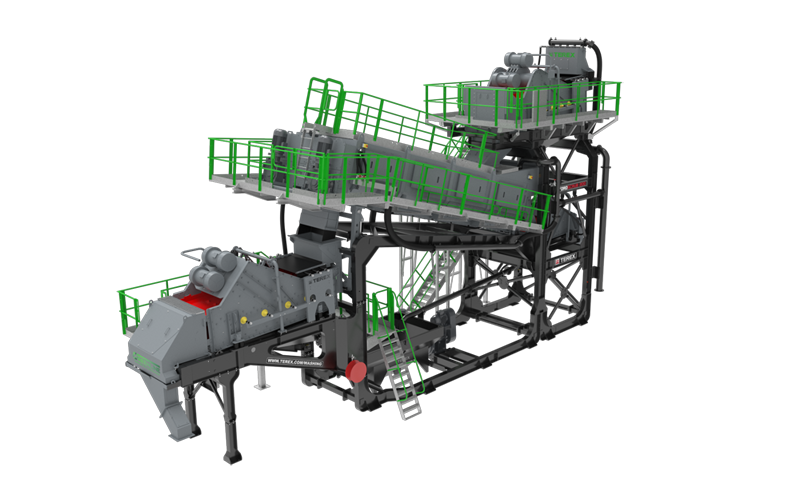
The pace of change in the aggregates wash plant market has been rapid in recent years. The latest example of this is Terex Washing Systems’ (TWS) new HydroScrub 200 — a state-of-the-art new addition to the company’s Greenline range of products specifically tailored to work in wash recycling applications.
Described as TWS’s “most versatile machine to date”, and the end result of a two-year research and development project, the HydroScrub 200 uses the core principles of a high-performance log-washer with new features that offer dynamic adjustment and control, ensuring a flexibility that enables the customer to adjust parameters to optimise performance and suit various types of feed material.
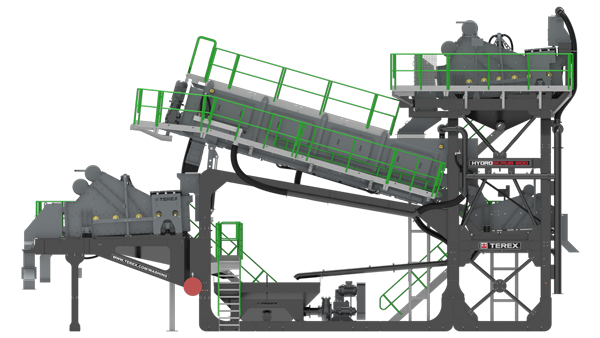
Comprising of hydro flotation water injection, integrated pre- and post-screens, a high-volume trash removal screen, and single-pass processing for various feed materials, the HydroScrub 200 is said to be ideal for wash recycling applications. These can range from construction and demolition (C&D) muck away applications—where the challenge is liberating the valuable aggregates and light organics from tough to break down fines and insoluble clay—to ‘high volume lights’ applications, where the level of attrition required to clean aggregates is lower, but high volumes demand more water to create the hydro separation required to float these off effectively.
Barry McMenamin, business line director - Terex Washing Systems, said: “We recognise that not only is there a huge growth in the wash recycling sector, but there is ever-increasing diversity in the range of materials end-users need to wash. The HydroScrub 200 offers the convenience of having one machine that can be easily adjusted to process different feed materials and provides opportunities for expansion in the range of customers you can provide a service for and expansion in terms of the volume of material they can process. It is the epitome of what we strive to offer through our Greenline range of products: balanced, end-to-end processing systems that enable our customers to wash wisely.”
The HydroScrub 200 was officially unveiled at a live launch webinar on Tuesday 17 November that took viewers through critical features of the product and how it efficiently and effectively caters for various applications, allowing you to wash more and waste less.
Independent, family-owned business Longcliffe Quarries is fast approaching its milestone centenary celebrations. To mark the occasion, it has committed to a series of ambitious sustainability targets and has partnered with CDE, a leading manufacturer of wet processing technologies, to help realise its environmental objectives and strengthen its position as a champion of sustainability in the UK’s quarrying sector.
Founded in 1927, Longcliffe Quarries is the largest independent supplier of calcium carbonates in the UK. By 2027, it hopes to achieve zero-carbon quarrying operations.
The Derbyshire, central England-based business produces over one million tonnes of high-quality calcium carbonate powders and granules every year, quarried from pure limestone deposits at its Brassington Moor quarry.
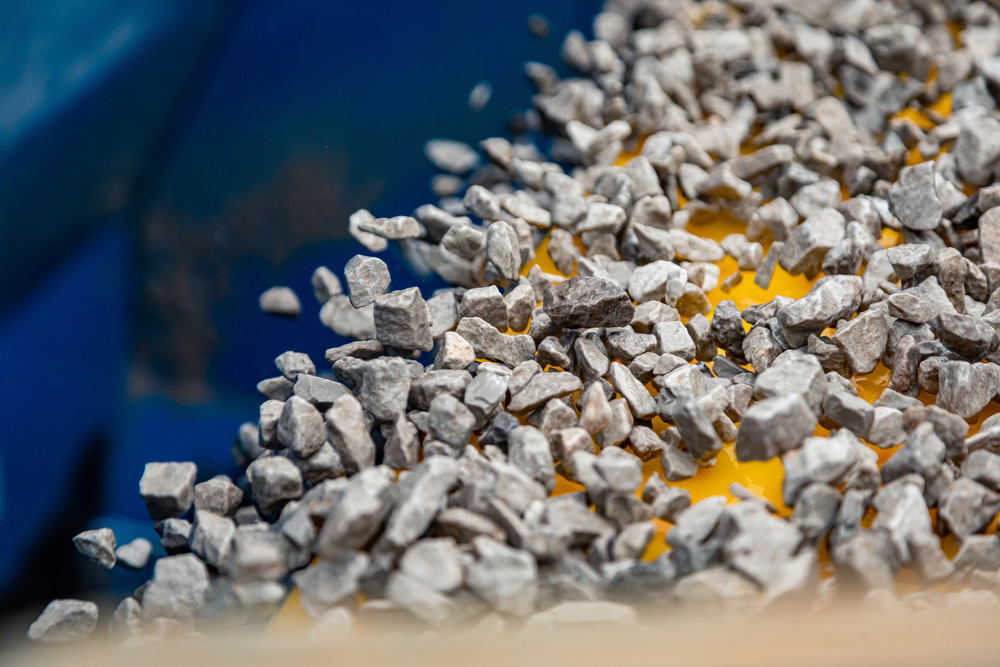
Calcium carbonate forms the basis of many everyday products. Longcliffe Quarries managing director Viv Russell says it has “many applications” and that the company produces over 100 products for a vast range of “critical industries”.
Longcliffe Quarries’ calcium carbonate products are vital components in animal feeds and pet foods. Its powders and granules are also supplied into the glass, plastics, and pharmaceutical industries and many more.
Russell also explained, proudly, that sealants – or cure activators – produced by Longcliffe Quarries are used in fluoroelastomer docking seals on the International Space Station.
“We are quite a wasteful industry,” Russell states, adding that Longcliffe Quarries generates “about 300,000 tonnes of waste per year.”
In pursuit of its environmental commitments, the business sought to address the high volumes of waste generated at Brassington Moor quarry.
The business had historically discarded its quarry by-product, material described as having a higher clay content. But feasibility studies and material testing to demonstrate market demand for products recovered from this stream highlighted the potential for Longcliffe Quarries to realise its commercial objectives without sacrificing its sustainability credentials.
David Kinloch, CDE’s regional manager in the UK and Ireland, says the partnership with Longcliffe Quarries began several years ago.
“Following intensive testing in our lab, we demonstrated through on-site plant trials how CDE wet processing technology could process Longcliffe’s by-product into a very clean and high-value revenue stream.
“It was after a procurement process through which CDE proved its technical capability that workshops were launched in partnership with Longcliffe to co-design what would eventually become its first-ever wet processing plant.”
CDE operates an innovative co-design approach which involves working closely with its customers to design customised wet processing solutions tailored to meet their specified commercial and environmental objectives.
Kinloch said this design process included integrating the plant into the existing setup at Brassington Moor quarry.
“One of the more unique aspects of this particular plant was how it integrated with Longcliffe’s existing primary crushing setup. We introduced overland belt conveyors to charter product to the CDE wet processing plant.”
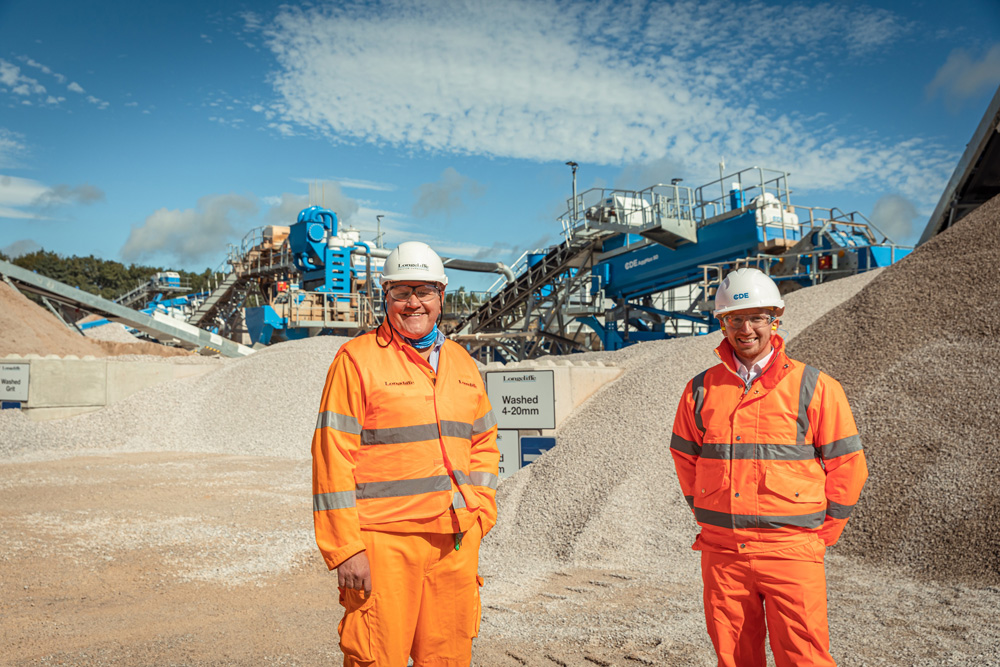
The resulting 220 tonnes per hour state-of-the-art wet processing plant represents the single largest investment Longcliffe Quarries has ever made.
Engineered to maximise product yield from heavy clay-bound feedstock, the plant features CDE’s signature AggMax modular logwasher setup for scrubbing and sizing.
It also incorporates CDE’s patented EvoWash classification and dewatering system which offers greater efficiency compared to more traditional washing methods.
Central to the system and to address the availability of clean water on site is CDE’s AquaCycle thickener which allows for up to 90% of the process water to be recycled and recirculated back into the system, offering near-total independence from fresh water supplies.
Exceptional water management means the CDE wash plant requires only a small top-up water supply resulting in a highly efficient system extending significant operational savings to Longcliffe Quarries.
Previously discarded clay-bound material is now being processed through the wet processing plant creating new, high-value revenue streams.
High-quality single-sized aggregates and sand grades are among the key products being recovered, which is maximising available reserves and supporting Longcliffe Quarries to realise its environmental targets.
It’s a win-win scenario, as Russell explains.
“We’re recovering up to six different products from heavily contaminated material. The CDE plant is producing a very, very clean product and one that we’re now able to turn into a higher value industrial material.”
This has led to a significant 12% reduction in the quarry’s load and haul fuel usage and follows an almost 70% reduction in net emissions recorded at the quarry since 2014/15.
Russell says the quality of the washed aggregates has created new commercial opportunities for Longcliffe Quarries.
“We’re now supplying into both the ready-mix and decorative markets as a direct result of the quality of material output from the plant. We’re processing high volumes of low-grade feed and turning that into saleable products.”
He adds that addressing the impact on the environment will produce a competitive advantage.
“As we move towards a more circular- driven economy, it’s vital that the industry continues to adapt. Our investments in renewable energy and this wet processing plant demonstrate our commitment to sustainability.
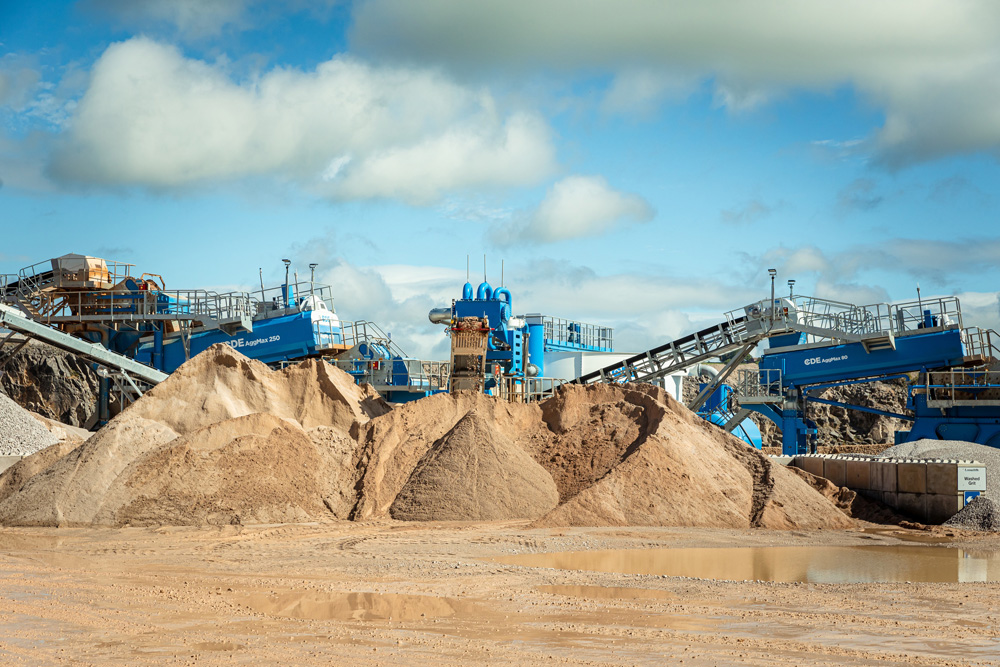
“In hard economic terms, if planning permission is to be granted, then we want to be seen as the supplier of choice. Yes, the steps we are taking now offer immediate returns, but longer-term they also position Longcliffe as a socially responsible business committed to the Derbyshire Dales.”
James Thorne, chief executive officer of the Institute of Quarrying, says technology is reshaping how the industry operates.
“There’s been a massive change in technology, and I think that’s really exciting. We’re only going to see more of that. The industry has always adapted to changes and utilised technologies coming in to its benefit to make it better and more efficient – and safer.”
He believes the Longcliffe Quarries wet processing plant will generate significant interest from across the industry.
“Projects like this are the future. It makes sense to do these kinds of things, and I think the industry will view this with real interest, particularly when you look at the big picture of the issues we’re facing as a society.”
The integration of technology and IT in the plant, Russell says, has impressed the team at Longcliffe Quarries.
“Due to the IT related to the plant, if we’ve got an unforeseen problem then CDE often knows about it before we do. That gives us the confidence and reassurance that we are working for the right team.”
It features CDE CORE, a suite of smart technology tools that offers plant operators greater control over their plant and access to real-time data on how their plant is operating to maximise plant uptime and throughput.
“We want the plant to be running and producing products and so too does CDE. This exemplifies the partnership and shared ethos of both companies.”
Kinloch concludes: “The plant, a fully optimised turnkey solution, will provide Longcliffe with the capacity to utilise available resources to their fullest potential by extracting maximum value from previously disregarded by-product material due to its high clay content. This will facilitate the company’s growth and further strengthen our shared purpose for a sustainable future.”
Luck Stone is the largest privately held, family-owned and -operated producer of crushed stone, sand and gravel in the United States. Its 28 sites across Virginia, Maryland, Georgia and the Carolinas provide consistent, quality aggregate materials that serve as the foundation of roads, bridges and buildings.
At each new site Luck Stone develops, the firm extends its core operating principles of economic development, environmentally sound practices and values-based leadership. The company is committed to being a good neighbour and providing a positive impact on the communities in which it operates.
In 2002, Luck Stone purchased its Bull Run Plant in Chantilly, Virginia., to serve the growing Northern Virginia market. Started in the 1950s, the quarry was a low-volume, eight to 10-conveyor operation when Luck Stone began expansion efforts to meet the market demands. It moved a road to access more reserves and grew the site to approximately 70 conveyors that transport trap rock from the quarry through the crushing and wet processing plants to the stockpiles.
The expansion efforts also included upgrading their asphalt sand processing plant to increase production.
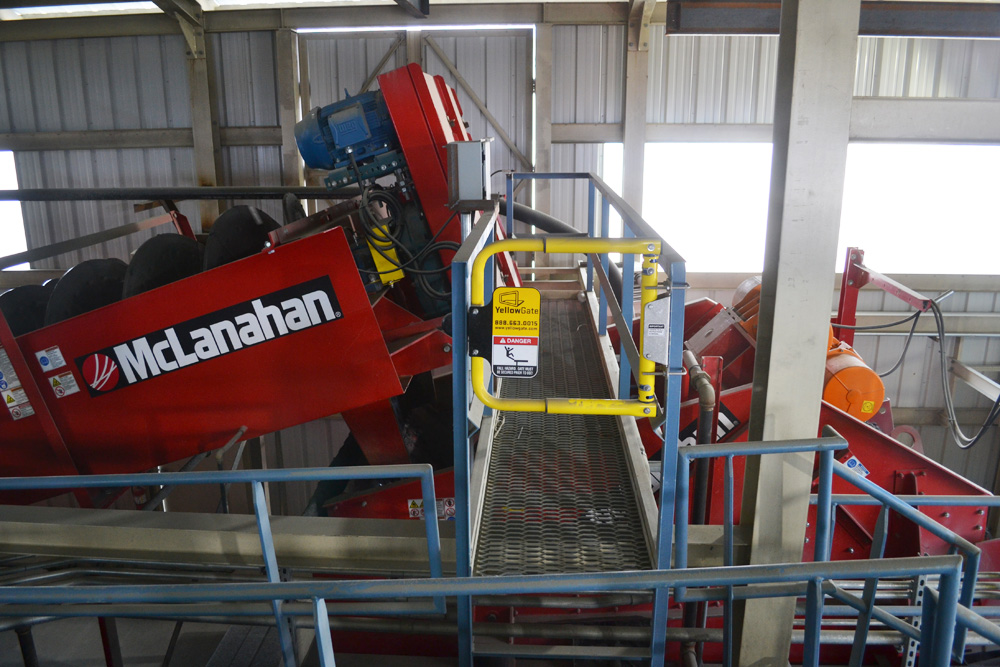
“The main driver for the expansion of the sand plant here was just the demand in the market for sand products that needed to be clean,” said Craig Wiant, assistant plant manager at the Bull Run site. “At those volumes, we can’t afford to make a pile and let it decant before we sell it, so we really needed to be able to make it on the fly, ready to ship.”
The Bull Run Plant has a lot of stock turnover, so its sand needs to be ready to ship. The company wanted a solution that would put the product on the ground as dry as possible.
“It’s really critical to us to have a lot of sand-making capacity but also to have a lot of sand on the ground that’s ready to sell,” shared Wiant.
As part of the expansion of its sand plant, Luck Stone replaced a much smaller sand screw with two McLanahan twin 44” x 33’ fine material screw washers to more effectively remove fines from its asphalt sand.
Luck Stone also wanted to include dewatering capabilities in its new wash plant, something it didn’t have in the old plant. Dewatering screens have been proven to produce final products that are at least 10% drier than fine material screw washers. When the two are used together, they provide a greater level of dewatering. Luck Stone followed each fine material screw washer with a McLanahan VD18 dewatering screen for additional moisture removal before stockpiling.
“The screw classifiers clean the material so it’s within our customer specs and above,” Wiant said. “Then, the addition of the dewatering screens allows us to produce the product at a moisture content that’s ready to ship.”
To keep valuable solids in closed circuit, the screen throughs collect in low-profile sumps underneath the dewatering screens and are pumped back to the screw feed via McLanahan slurry pumps.
The McLanahan fine material screw washers and dewatering screens help Luck Stone produce a clean, drip-free asphalt sand for its customers.
“Our customers really want to see the percent passing the 200 mesh at a two or less, especially for asphalt mixes,” said Wiant. “We can typically put it in the pile at about 1.5% passing the 200.”
Not only does the McLanahan equipment help Luck Stone meet the strict specifications required of its final product, it also allows it to produce a drier sand. The moisture content of the sand coming off the dewatering screen is as low as 7%.
“Depending on weather and setup, we usually see somewhere between 7 and 9% moisture coming off,” explained Wiant. “It allows us to sell our material much quicker, so it doesn’t have to sit in the pile and decant. It’s pretty much ready for sale as it comes off the stacker.”
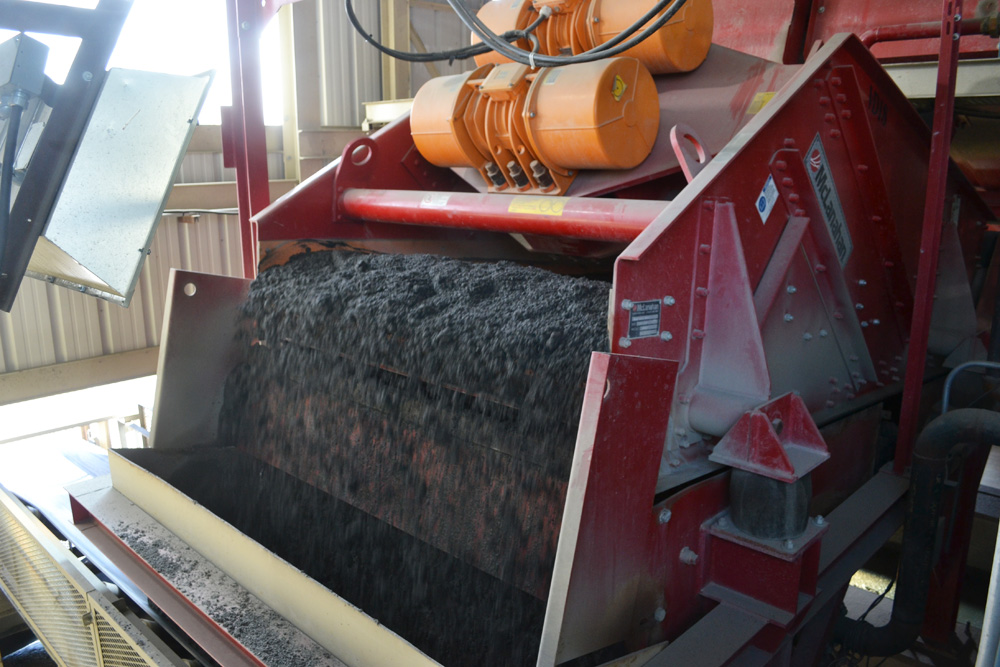
Wiant said they’ve been really happy with the McLanahan systems at the Bull Run Plant.
“The McLanahan screws and dewatering screens have been incredibly reliable,” Wiant said, “so our quality has been great. They provide a really clean product, which is what our customers demand, and they’ve been reliable since we put them in.”
With the increase in infrastructure projects in Northern Virginia, the McLanahan fine material screw washers and dewatering screens will continue to help Luck Stone meet the needs of its customers.
“Being able to provide a clean sand at low moisture to our customers allows them to build projects with the longevity to serve the surrounding community,” said Wiant.