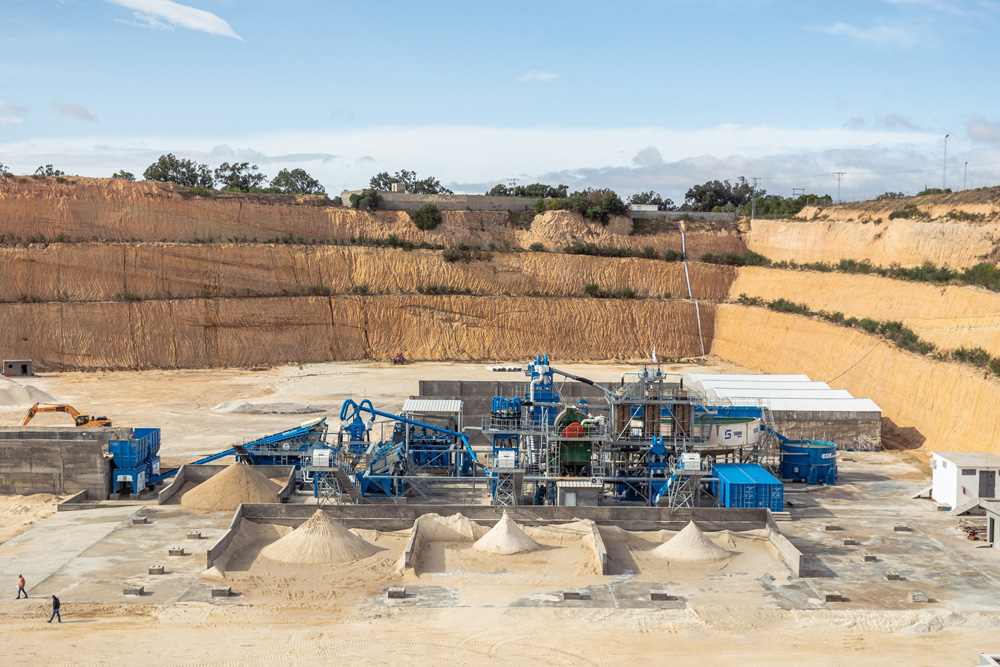
Tunisian quarry operator SOMEVAM has announced plans for its second wet processing solution from Northern Ireland-based CDE. The new plant will produce high-specification silica sand products.
SOMEVAM is a subsidiary of the Tunisian Sebri Group, which has interests in quarrying, agriculture, and food processing. Sebri Group will work with its wet processing partner CDE to design and engineer the new plant at one of SOMEVAM’s quarries in Oueslatia.
The sand and aggregate materials from Sebri Group’s Oueslatia sand quarries have been supplied to the national construction market for the past two decades.
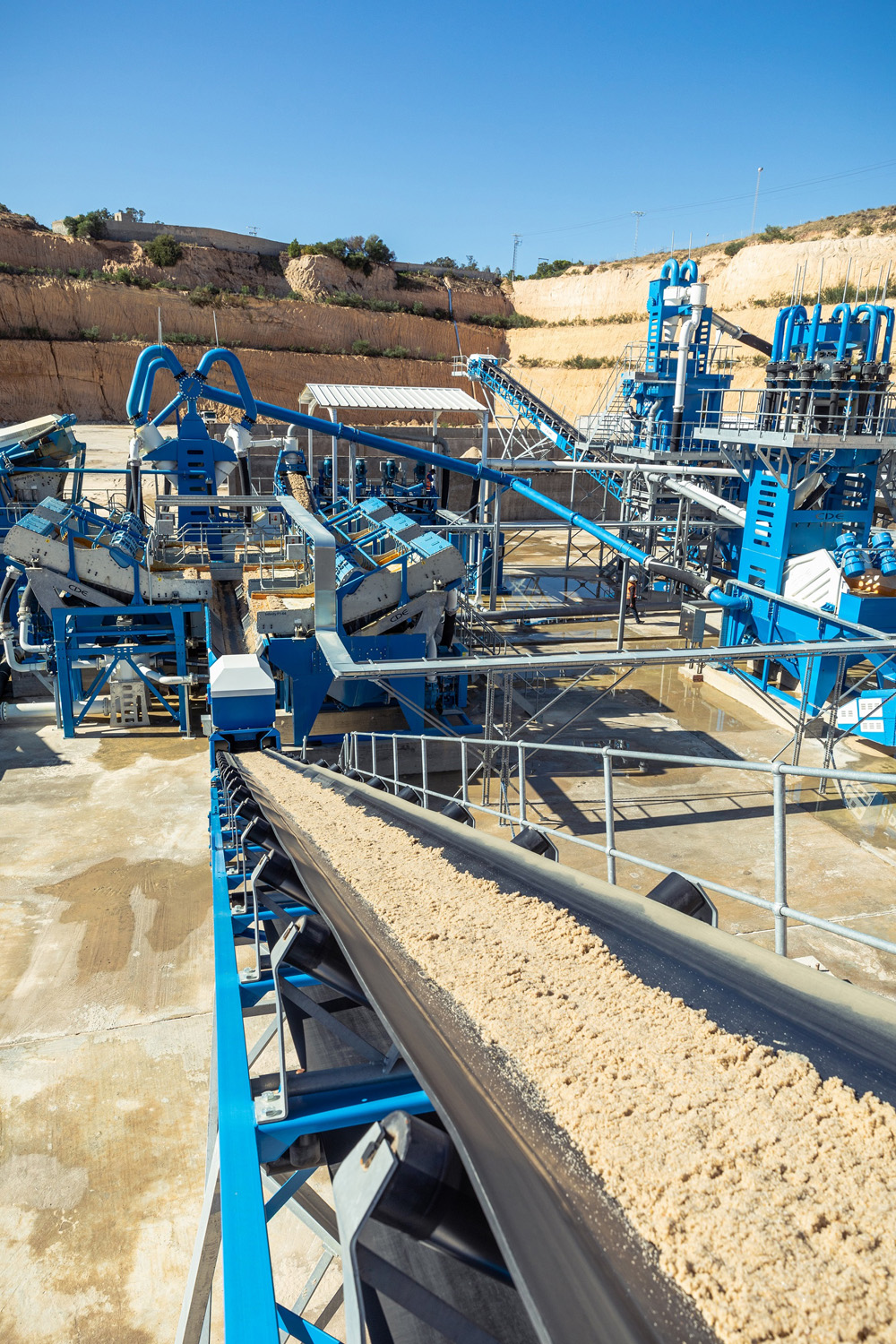
Its management team identified an opportunity to further diversify the business by expanding into the glass sands market to strengthen its commercial proposition in the region, and in 2019 commissioned its first CDE solution at the site.
The state-of-the-art silica sand wash plant can treat up to 200 tonnes per hour of sand, producing 100 tonnes per hour of silica glass sand for the glass industry, as well as a range of secondary products including fine silica sand for silica flour production, foundry sand, concrete sand and road base.
Investment in a second silica sand wash plant comes as SOMEVAM says it is recording significant interest in its future production output. The plant will produce silica sand, which has applications in paints, coatings and inks, adhesives and sealants, pharmaceuticals, lighting and more, and silica for flat glass applications such as windows, mirrors and flat glazing.
The glass industry accounts for more than a third of the total market for silica sand based on end use. The market analysis projects a growth rate of 7.12% in the silica market over the forecast period 2019–2026, reaching US$3bn by 2026. While North America has the largest market share, the Asia-Pacific region is anticipated to display the highest growth rate, according to a report from Bizwit Research & Intelligence.
Commenting on the announcement, CDE’s senior project manager Bassem Idriss said: “We’re very pleased to once again partner with Sebri Group on this exciting project announcement that will significantly expand SOMEVAM’s silica sand processing and production capacity. Its previous investment in CDE technology exemplifies our commitment to engineering excellence and is one of the most advanced plants of its kind.”
Ruchin Garg, CDE regional manager, MEA (Middle East & Africa), added: “At CDE, every customer is a customer for life. SOMEVAM’s existing silica sand plant, which was commissioned in 2019, receives expert proactive and preventative maintenance and support. It’s this commitment to our customers, one that ensures their CDE solution is running at optimum efficiency to maximise product throughput, yield and profitability while minimising their environmental footprint, that has formed the foundation from which we can continue to build upon our positive relationship with Sebri Group through this latest announcement.”
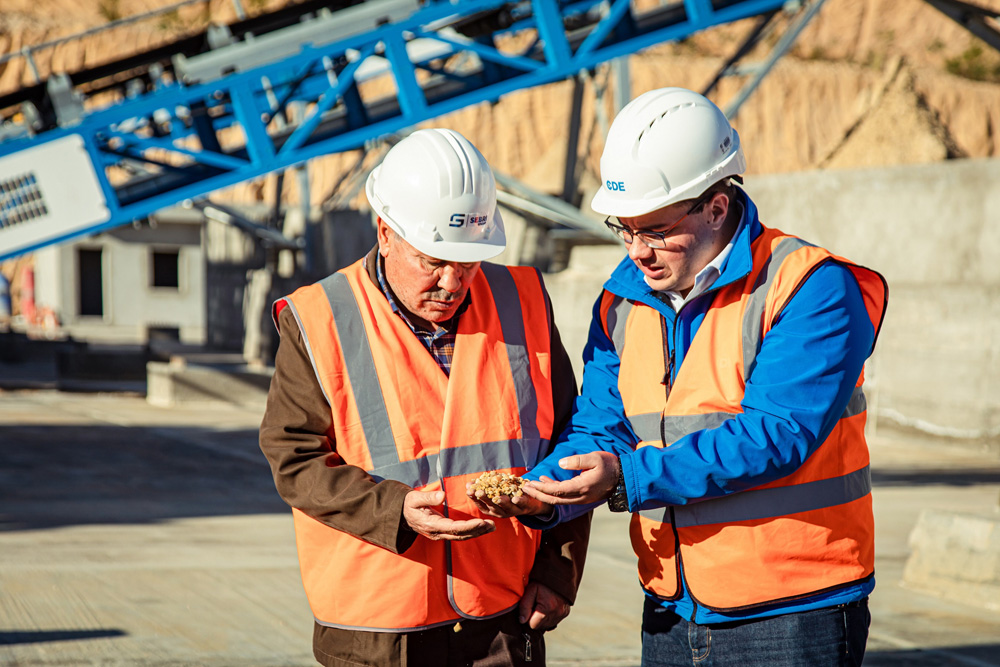
Habib Sebri, owner and chairman of Sebri Group, said: “Following a hugely successful venture into the glass sand industry with our first CDE plant, we sought an additional plant to meet the growing demand for our products. We are excited to partner with CDE once again on this new project to maintain the quality and consistency of our offering, and we thank all of those partners who helped secure funding and provided their expertise and resources to help make this ambitious project a reality.”
CDE and Sebri Group said they would share more details about developing the new SOMEVAM silica sand wet processing solution in the Oueslatia region over the coming months.
With authorisation from the Central Bank of Tunisia, funding for the new investment was secured with the support of UK Export Finance, AF Capital, Apple Bank, and supported by the British Embassy Tunis.
Tri-Parish Sand and Gravel is a dry mining operation located in Walker, Louisiana, USA. The company produces C-33 concrete sand, pea gravel and #57 concrete gravel for use in their ready-mixed concrete operation, Parish Ready Mix.
James Nolan, who owns Tri-Parish Sand and Gravel with his wife, Gail, has always been concerned about the cleanliness of the products they use in their ready-mixed facility. They strive to deliver quality products on the concrete side of their business, which starts with the material used to make those products.
To better control the quality of their concrete products as well as lower their production costs so they could pass those savings onto their customers, the Nolans purchased land for dry mining their own sand and gravel. They looked at a few wash plants in different parts of the country for processing the feed and separating it into the various products needed at their ready-mixed facility.
In 2020, Tri-Parish purchased the McLanahan UltraWASH 6206 modular wash plant that debuted at CONEXPO/CON-AGG 2020 in Las Vegas. Availability was a key factor in the purchasing decision. Tri-Parish needed a wash plant quickly, and the McLanahan UltraWASH offered an entire wet processing plant in one compact, modular unit that was ready to run.
“We bought the plant, and we’re very, very pleased with it,” said James Nolan. “It definitely does way more than they said it would do.”
The UltraWASH features a McLanahan inclined vibratory screen for sizing up to three aggregate products (the oversize, the pea gravel and the #57 gravel in Tri-Parish’s operation). It also features a sump, two McLanahan Pumps, two McLanahan Hydrocyclones and a McLanahan Dewatering Screen for washing, classifying and drying the sand product. This particular UltraWASH model is a double wash system, which processes the sand twice before discharge for a cleaner end product.
A modular plant, the UltraWASH arrived at Tri-Parish in several partially pre-assembled and pre-wired pieces.
“It went together very easily,” said operations manager Danny Graham. “You could almost do it by pictures alone.”
Graham added that the modularity of the UltraWASH would be beneficial if they need to move the plant closer to the area in which they are mining in the future.
“It could be somewhat portable. You can take it and move it in a matter of a day or two,” he said.
Besides availability, one of the aspects that attracted the Nolans to the UltraWASH was the rated tonnage of the machine, but this exceeded their expectations in the field.
“It’s delivering way more than we’ve ever dreamed, so I’m really happy with it,” James Nolan said.
“We’re actually outrunning our guys who are stockpiling raw material,” Graham added. “Production-wise, it’s better than expected. We’re keeping up very easily with this product; it hasn’t been a problem. The UltraWASH is doing a great job.”
Since they started operating the plant, James Nolan said the biggest benefit of the UltraWASH is how quiet it is. The Tri-Parish property borders a housing development, and the neighbours can’t hear the plant when it is running.
Graham likes that the UltraWASH is easy to operate.
“I really like that it’s one central unit,” Graham explained. “Everything’s maintained in one electrical panel. It’s easy to work with; the PLC and everything make it very user-friendly. It’s automated stop/start, so there’s no guesswork and there’s no manually starting different components. You start it, it runs; you stop it, it stops. You can’t beat that.”
In addition to the UltraWASH’s performance, James Nolan is also pleased with the cleanliness of the product coming off the end of the machine.
“I guess I’m bragging on it, but it needs to be bragged on. It turns out a real good material. It’s clean. I’m proud of it,” James Nolan said. “Even the guys at the plant, they realize the change in the material because we have started running out of here now and it’s a whole lot different. We don’t have to be looking for mud balls and sticks and stuff like that because we send out a good product. We’re not going to send it out dirty, but this plant definitely helps us with a lot.”
The UltraWASH allows Tri-Parish to supply the concrete side of their business with a clean, high-quality product.
“Our goal and business is quality, and we’ve achieved it at this point,” James Nolan said.
The Tri-Parish team was also pleased with the support it received from everyone at McLanahan, from sales to project management to field service.
“My experience with McLanahan has been wonderful,” Graham said.
“They were all great in helping us facilitate getting the plant off the ground,” Gail Nolan shared. “They never left us behind. Any time we called them, they were always there and giving us an answer in a timely manner.”
“The machine is a good machine, but without service, it’s nothing,” James Nolan said. “The McLanahan team helped us out a lot. Without them, we couldn’t have made it.”
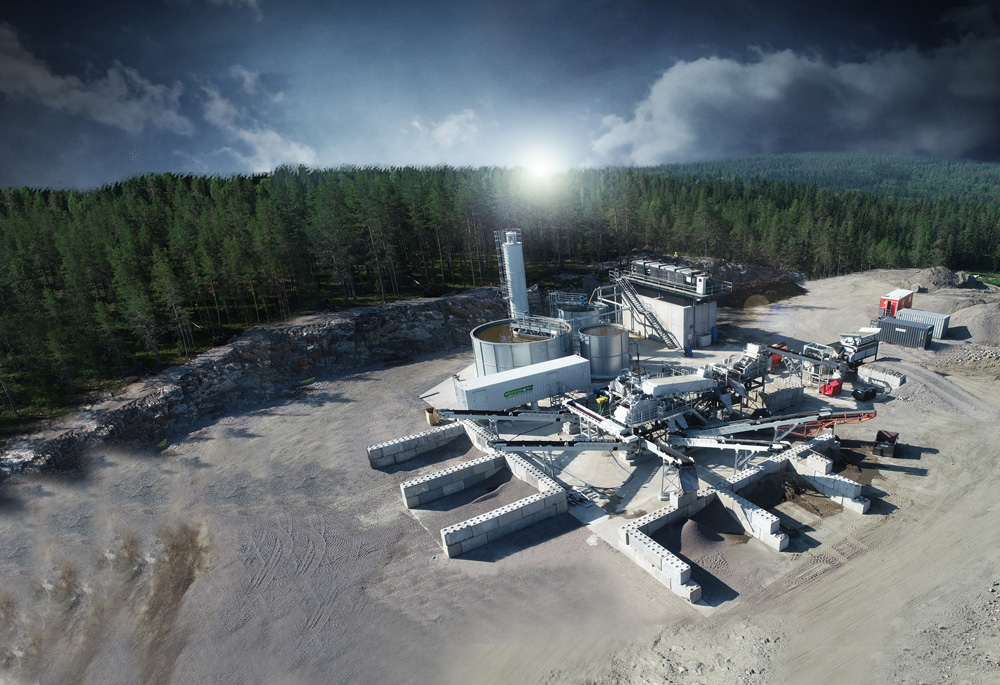
With more than half a century of washing experience already under its belt and a proactive research and development team (R&D) that never stands still, Terex Washing Systems (TWS) has a proud and rich history. A division of Terex, TWS was established in 2012, and in this time, it has continued to commit time and resource in developing and investing in R&D and the latest technologies and systems in the wet processing world.
TWS’s product portfolio now offers ‘end to end’ washing solutions, including the more recently introduced AquaClear Water Management Solutions and GreenLine Engineered Recycling Solutions. However, all these solutions’ beginnings can be traced right back to before 1960 within the Finlay and Powerscreen product lines.
The mid-1960s saw the development of the very first washing plants, and the following decade saw the launch of the MK1 and MK11 Rinser range. It wasn’t long before Powerscreen and Finlay realised the crucial need and potential opening in the market. They knew that the natural sand and gravel supply would soon be exhausted and foresaw stricter building and construction specifications being written for aggregates usage.
As technology started to advance in the late 1970s, the Sand Saver Dewaterers were soon phased out. They were replaced by the more sophisticated and modernised Screw Recovery Dewaterers, later to be called the Trident range.
The 1990s saw the establishment of a dedicated washing department, set up by Finlay and Powerscreen. By the 2000s the demand for washing was expansive, so TWS was established in 2012 as the sole provider of washing solutions within Terex.
While its roots are firmly established locally in County Tyrone, Northern Ireland, TWS now enjoys a global reach. The business is supported by an over 70-strong global dealer network. While TWS continues to navigate through these unprecedented times, now more than ever, this global dealer network has been fundamental in providing local and regional on-the-ground support to customers worldwide.
Furthermore, the business has significant support from local Terex footprints globally, such as Jacques in Melbourne, Australia, and Louisville in Kentucky, USA. The local support backbone has become increasingly important in allowing TWS customers to continue their operations. It has also allowed the continuation of plant installations, start-ups, and commissioning. While also being supported remotely from TWS’s County Tyrone HQ via digital technology, local support is something that TWS says sets them apart from many of its competitors.
To go further, TWS has spent many years developing its portfolio of accompanying AquaClear water management solutions and products. The business has always had a relentless goal to be a single-source partner for complete solutions, perfectly balanced to match the needs of front-end equipment globally.
TWS’s recent launch of GreenLine Engineered Recycling Solutions (Greenline) puts together many years of expertise in easy-to-understand, tailored, packaged solutions designed to deal with varied recycling segment materials, muck-away, trommel fines, and C&D waste across differing capacity levels and at different levels of investment.
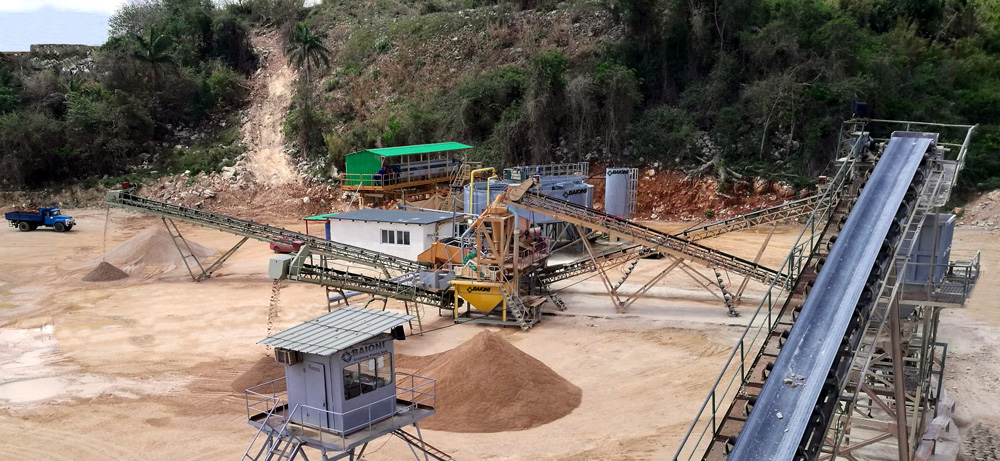
Greenline couples TWS’s front-end processing products with the business’s back-end AquaClear Water Management Solutions. Several new TWS-patented specialist units will further enhance the Greenline offer, delivering an easily adaptable and potentially bespoke out-of-the-box approach to processing diverse material at a rate of 60-300 tonnes per hour.
Italian washing plant specialist Baioni has a new four-business division set-up as part of a major strategy and rebranding process, focusing on design, people, and the environment.
The new business divisions – Baioni Crushing, Baioni Environment, Baioni Equipment and Baioni Service – have their own goals and features.
Baioni Crushing focuses on Baioni’s ability to design and build large-sized processing plants. Baioni Equipment incorporates the Italian firm’s comprehensive range of equipment for processing aggregates. Baioni Service handles increasingly important aftersales business, and Baioni Environment is responsible for designing and producing plants to treat contaminated soils and sediments. The business division also offers plants for the treatment of road-sweeping waste and incineration slag.
A Baioni spokesperson said: “In the last few years, the requirement to wash mineral, aggregate and soil has become more frequent as operators tackle more difficult materials. With this upward trend set to continue, Baioni have an important part to play in developing products and solutions that can meet the evolving demands.
“For 2021, our approach in response to the coronavirus challenges is to offer equipment when there is clay or contaminated particles present in the material or high levels of -63 micron material that can ensure production of the highest quality washed sand and aggregates.”