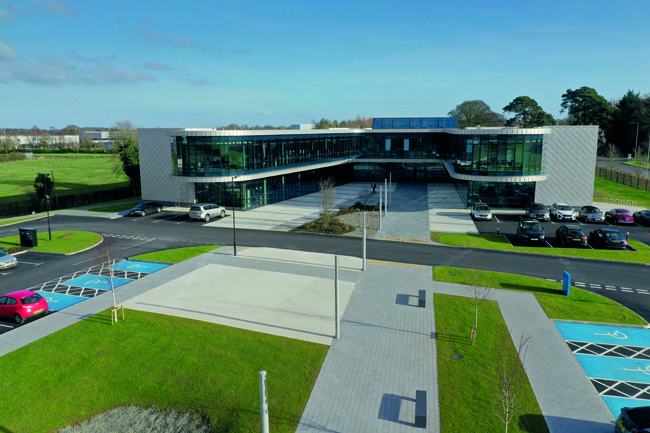
CDE says its new global base can develop the company’s position in the aggressively competitive wet processing sector. Liam McLoughlin reports.
Wet processing equipment provider
Having grown its team by 65% over the last two years the Northern Irish company, with 2,000 projects around the world, plans to create an additional 150 new jobs by 2020, bringing the total employed globally to almost 800. The new facility can accommodate over 400 people and CDE claims it houses the world’s largest engineering team dedicated to wet processing technologies.
CDE group managing director Brendan McGurgan and chief operating officer Sean Kerr sat down with Aggregates Business to discuss the impact the new facility will have on the company’s business.
“The new base brings everything together under one roof,” said McGurgan. “Over the last 10 years we have grown out of the existing offices in Cookstown, Northern Ireland. Our new HQ is a very open-plan building to encourage increased collaboration and ensure a one team culture to create the best solutions for customers.”
Kerr agreed: “Everything we do is a bespoke solution for our customers which is quite unique for the industry. The open-plan of the new HQ and collaboration between all departments is critical for our solutions to be world class. That rapid communication, ability to be very agile and do things quickly is greatly enhanced by the environment here.”
As part of its five-year strategic plan, CDE has embarked on a strategy to deal with the end customer directly rather than sell through a distributor network. To that end CDE acquired the extensive
“We are passionate about maintaining our USP which is about creating bespoke, customised solutions and a partner for life aftercare service,” said McGurgan. “That too is where our new HQ is important. We need the best environment to attract the best talent.
“A strong connection with third level educational institutions such as Queen’s University and the University of Ulster provides CDE a great pipeline of that new talent.”
Once the talent is attracted CDE seems able to keep it, with McGurgan pointing out that the company’s staff retention rate is extremely high. “Almost half our global board of directors is made up of people who joined the business as a graduate,” he added.
He added that another major benefit of the new HQ is the facilitation of customer visits, and that it is an ideal venue to showcase an innovation ethos. On average, one foreign delegation is present at the new HQ each week with recent visits including groups from Canada, Israel and Argentina.
McGurgan said that, because of the customisable nature of CDE’s equipment, the company innovates in every single project it is involved with - both in terms of product and process. CDE’s innovation ethos appears to be reaping dividends. “Thirty per cent of our revenue, on average, comes from new products released in the last 36 months,” he said.
CDE, which claims to hold more patents than anyone else in the sector, has a specific number of its R&D staff now completely dedicated to ‘blue-sky thinking’ and new product development rather than refinement of existing products. That future thinking team is active in a diversity of areas including alternative materials, 3D printing, technology and software. “This industry is aggressively competitive which is why we focus heavily on new product development, coupled with a strategy of protecting our design rights and IP [intellectual property] through patents.” McGurgan also shared that the company had a large pipeline of new products with a significant number of patents pending.
“The main objective of this R&D is to enhance the customer experience and change the direction of the industry with these new and novel ideas, and that’s why we have the reputation as being the industry innovator,” Kerr added.
The internet of things is also set to be an interesting development for the industry as CDE incorporates its smart technology around the operation of plants. “We are moving to a new generation of quarry owners and managers who are brought up with considerable technological skills and therefore expect a certain level of tech sophistication in operating their plants,” McGurgan said. “This is something we have been working on and we will be launching a new innovation at bauma which will change traditional thinking and the manual way plants are typically run.”
This drive for continuous innovation to solve customer challenges means that CDE has plans for expansion beyond its new HQ, with an innovation hub scheduled to open on the same site within the next 12 months.
The new hub will feature a state-of-the-art laboratory. “As we develop further into our regions and sectors, customers’ feed materials become increasingly varied,” Kerr said. “There are more surgical requirements on the separation side in terms of size fraction and removing impurities, chemicals and various other things, and this can turn what was typically waste into a valuable product. The new laboratory will enable us to continue to extract the maximum value from our customers’ feed material streams.”
McGurgan said that recycling is fast becoming a necessity the industry needs to explore and increasingly presents both incredible business opportunities and environmentally sound practice.
“Virgin natural sand is the most used natural resource after water,” he said. “We need to preserve that and ensure we process in a responsible manner as the reserves of natural sand are depleting. We are looking towards material streams that would historically be perceived as waste - such as highly contaminated soils, earth and excavation waste, over-burden and crusher dust on the sand and aggregates side - and have developed solutions that divert those materials from landfill and bring them back into mainstream construction as an alternative to virgin sand and aggregate.”
Therefore, one key area of CDE’s focus is the construction and demolition waste recycling sector, in which the company has played a central role in the UK over the last two decades. As a relatively small and densely populated island, natural sand availability in the UK was continuously going down. In addition, landfills were becoming filled with construction and demolition waste to the point where they were running out of space.
“People weren’t able to handle this waste or do anything with it,” said Kerr. “But through our R&D at the time we were able to recover up to 90% of the waste into recycled sand and aggregates which was used directly back into the construction trade. As that developed the rest of the regions started following suit and we have quite a number of recycling plants in Europe now, and our first project in Australia.”
In terms of factors that have driven recycling in the UK he highlights the Aggregates Levy, which is a £2 per tonne tax for extracting natural sand and aggregate. “This really drove the demand towards alternatives,” he added. In addition, the government-supported agency WRAP subsidised the investment in technologies to enable the recycling of construction and demolition waste.
Kerr added that technologies such as CDE’s mean that recycled product is sold for 80-90% of the value that it had in its original, natural state.
“The UK is a global leader in this type of recycling, and on the back of the UK’s success and our experience in this area we have done the first projects of this kind to reclaim from landfill in India, Australia, and North and South America,” he added.
McGurgan believes that there is an increasing need globally to find alternatives to the finite resources used in the construction industry. For example, in the Middle East, Qatar relies on importing natural sand and aggregate for construction purposes. The Gulf state has huge levels of construction and demolition waste, and McGurgan said that ultimately there was potential for technologies such as CDE’s to address a need in such markets.
“There are benefits in recycling across the board,” he said. “In the Middle East water is more expensive than oil and we have the ability to recycle 98% of the water that’s used within the wet processing process. It’s the circular economy in action.” CDE has created what it says is the largest sand washing plant in the world at The Qatar Sands Treatment Plant.
McGurgan added that in some markets, such as Switzerland, the cost of landfill is significantly high which was also driving demand for recycling services.
He concluded: “On top of all that, many countries are facing a shortage of processing capability and raw material resources while at the same time experiencing increasing demand for infrastructure, housing and civil works. Therefore, it is becoming essential for them to explore ways to maximise value from construction, demolition, excavation and various contaminated waste and re-use that valuable resource to meet supply and demand in the face of declining natural resources.”
US-based washing, crushing and screening equipment provider Superior Industries is another company that is heavily involved in sustainable technologies. Its Aggredry Dewatering Washer, a sand washing solution that supports sustainable aggregates processing, has been deployed by Wissota Sand & Gravel, an aggregate supplier based in Wisconsin.
“Our greatest resource is our water,” says Wissota Sand & Gravel president Christopher Larson. As its third-generation owner, Larson is keenly focused on sustainability initiatives, the latest being the installation of new sand washing technology that allows cost-efficient fines recovery and the conservation of valuable water resources. The operation utilises an innovative system that combines a fines material washer and a dewatering screen in a single machine. “Its advantages are far-reaching. Importantly, we’re realising these benefits at a fraction of the typical costs per tonnes in this application,” said Larson.
When using their prior sand screws, Larson said that the sand was coming out at about 25% moisture content. “Per my calculations, we were losing about 91m3 per hour – and the water was going to a part of the operation where it could not be recovered,” he added. “Replacing that water would require pumping it from a deep well or finding some surface water within the operation that could be recovered.”
It was the latter costly challenge, he stresses, that led to the acquisition of the Aggredry Dewatering Washer. Larson describes the new system as “making a lot of sense in its unique combination of two tried-and-true technologies – sand screws and high-frequency screens.”
The Aggredry Washer at Wissota features twin 1,524mm fines material screws (500 tonnes) combined with twin-high-frequency dewatering screens. “Our sand is coming off the two screens at 8% moisture content and requires no drying time,” said Larson. “Plus, we’re saving about 80m3 per hour.”
In the past, Larson said that his company had to be very selective on what could be run through the wash plant. “If we hit a dirty spot in the pit, we weren’t able to get enough fines out of the sand,” said Larson. “With our new system, we can process dirtier material and still manage the fines on the wash end of the plant. This gives us more throughput without having to be so particular about the material coming from the primary circuit. That’s a big advantage as the face of the pit is always changing.” He added that his operation crushes 1.8-million tonnes per year, with about 90% going through the wash plant.
Terex Washing Systems (TWS) will be presenting live washing demos of its AggWash 60 during the bauma 2019 construction industry show (8-14 April). The AggWash 60 wash plant incorporates screening, scrubbing, sizing and recovery of sand on one modular chassis and produces up to six grades of saleable sand.
The AggWash is intended to address requirements for recycling customers and quarry owners, particularly in the construction, demolition and excavation waste recycling market. It is designed to maximise yields from feed materials with efficiently designed system processes that keep running costs at a minimum. TWS says the plant’s portable format makes it particularly suitable for green-field applications, contractor use and temporary planning permission sites. The company adds that operators more used to static installations will still appreciate the small footprint and minimal site preparations required.
TWS engineer Paul McWilliams commented on the design: “In all cases, installation time is significantly less than conventional builds thanks to the high level of factory pre-fitting and connections. The no-compromise design ethos ensures maximum serviceability and performance despite numerous innovative features, including easily removed pumps, ready access to screening media and intuitive controls.”
Also at April’s bauma show, McCloskey Washing Systems will present the CSP120 plant. The company says it is designed to deliver superior separation efficiency, produces the driest, drip-free final washed sand product in its class, and produces up to two in-specification sands, to desired grade, at up to 120 (total) tonnes/hour.
The plant has been designed with the machine operator in mind. In addition to the highest level of quality and performance, significant benefits include simple and fast assembly times, ease of operation, low maintenance and an overall reduced footprint.
The CSP range can be tailored to suit any sand application, regardless of desired tonnage, ranging from 40-300tonnes/hour.
McLanahan will be exhibiting its new UltraWASH modular wash plant at bauma, the first time it will have been displayed at a trade show. It can produce up to three aggregate products and two sand products. It features a single process water feed point and a single effluent discharge point.
McLanahan says that, thanks to its recent acquisition of Anaconda Equipment, the UltraWASH feed hopper and conveyor can be upgraded to come with tracks for easier conveyor maintenance.