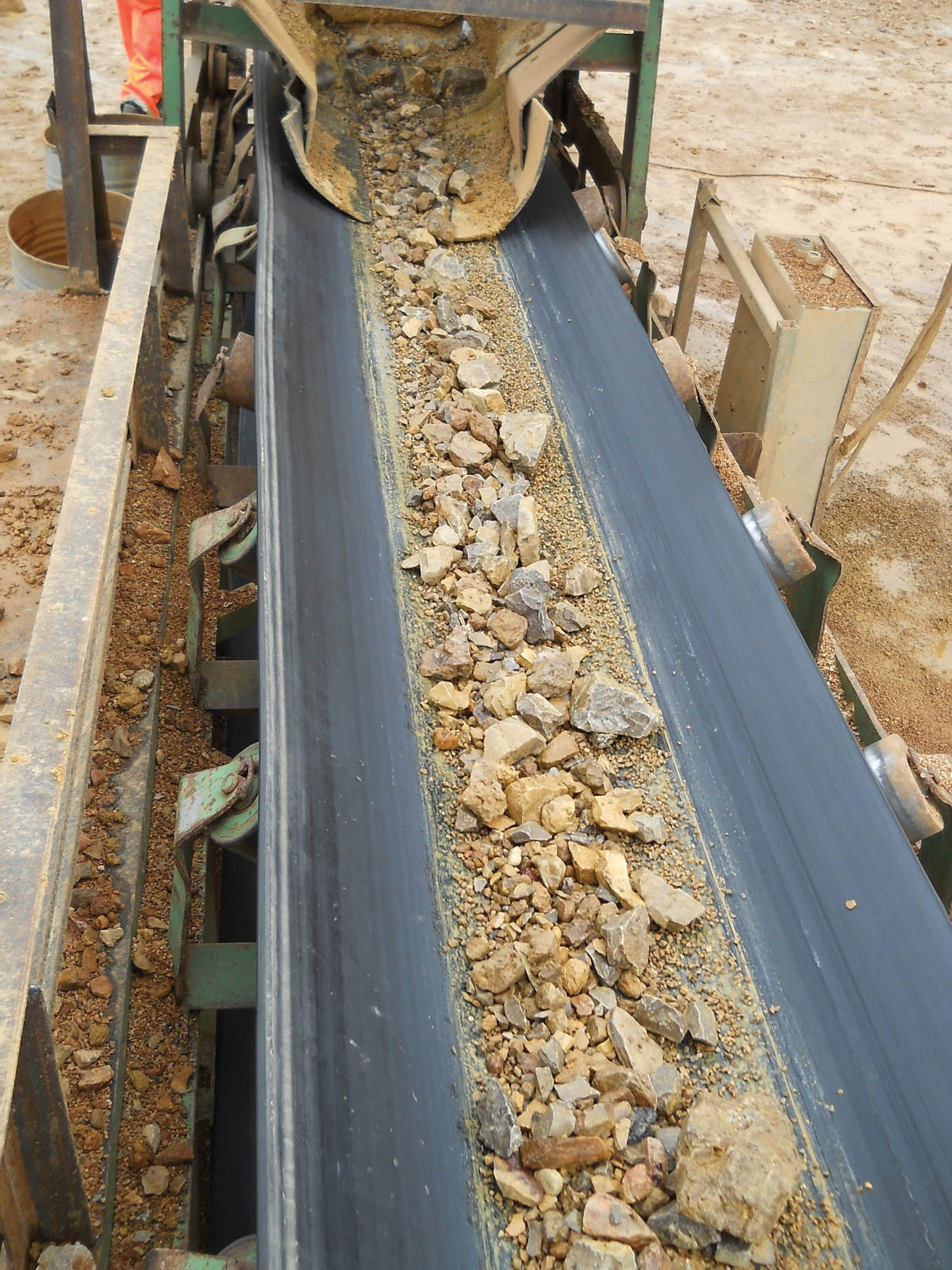
Specially designed equipment is helping minerals operations to produce clean, high quality products. Patrick Smith reports
In recent times the requirement to wash mineral reserves has become more frequent as operators tackle more difficult materials.
With this upward trend set to continue, equipment manufacturers have an important part to play in developing products which meet the evolving demands of the global industry.
Peter Craven outlines the approach taken by
“There has always been a requirement to process difficult materials. The geology of a region plays a large part in influencing the processing system that is chosen and it is for this obvious reason that washing equipment has found its place in the market. When there is clay present in the material or high levels of -63 micron material a washing plant offers the best solution to ensure production of the highest quality sand and aggregates,” he says.
When operators are faced with reserves which have variations in material quality they will obviously process the easiest material first: the ‘low hanging fruit.’
The selection of the appropriate system will be selected according to the nature of the material to be processed and the final products that are required to satisfy customer demands.
“As we have moved through the decades and quantities of this low hanging fruit have diminished the challenge for equipment manufacturers has been to continually develop and improve systems to ensure the more challenging materials can be efficiently processed.
“One of the key developments of recent years has been the move to mobile equipment within the global construction materials sector. This began with the development of mobile crushing and dry screening systems which operators can easily move between different processing locations and also move around a single site in order to minimise the transport movements of other vehicles.
“The unique requirements of washing plants made this move to mobile a more challenging concept. Logic tells us that washing plants are restricted in their mobility due to the requirement for connection to an external water supply. The early attempts at mobile washing provided evidence of this and these plants were moved rarely, if at all.”
Another shortcoming in the development of the first washing plants described as mobile was the inability to successfully integrate the sand washing element with the washing screen, says Craven.
“This required operators to purchase two separate items of equipment to deliver on the sand and aggregate production requirements.
“The result of these shortcomings was that the uptake of these systems was limited and the perception in the industry was that mobile washing plants had a problem: they weren’t mobile. Simply putting hydraulic tracks onto what was essentially a dry screen with the addition of a few spray bars was not a satisfactory solution.”
The term ‘mobile washing’ had reached a point where it had become the “evil that will not be spoken of” due to flaws in existing systems. These systems did not fail because of limited demand or lack of promotion. They failed because of an assumption that the same design principles that apply to dry processing equipment can simply be copied when developing a mobile washing plant.
“This provided the motivation for the development of the M2500.
“Central to the creation of the M2500 [from CDE Global] was the integration of the sand washing element with the rinsing screen. The aim was to produce a mobile washing plant which offered feeding, aggregate washing, sand washing and stockpiling on a single chassis.
“Another key issue was ensuring that the rinsing screen was suitable for the application and would stand up to the rigours of an aggregate screening process. The issue with [many] previous mobile washing screens was that more often than not the spray bars were bolted to the screen box. This meant they were subject to extremely high stress levels which would ultimately result in failure.”
According to Craven the M2500 eliminates this risk by offering a spray bar assembly which is completely independent of the screen box thus removing this risk of failure and ensuring it is designed for long term reliability and performance.
“By successfully integrating the Prograde rinsing screen and the Evowash sand washing plant onto the M2500 mobile washing has gained new momentum in recent years.”
The M2500 equipment is in use in a variety of industry sectors and has been employed on the processing of sand and gravel, crushed rock, dust washing, scalpings and construction and demolition waste recycling. In addition to this there are specific models available for mining applications.
“The success enjoyed by the M2500 since its introduction to the global market is evidence that with the correct design ethos, existing processing systems can be substantially improved to offer the industry more efficient processing systems which help to improve product quality, reduce waste and meet the requirements of a fast changing industry,” adds Craven.
TWS launched
“Our customers are looking for a more cohesive solution to their washing needs so we have created TWS to focus solely on providing solutions to the minerals washing industry,” says Kieran Hegarty, Terex Materials Processing president.
“This business line will be the single provider of washing equipment within Terex and will replace products previously offered by our
He says that changing market dynamics call for stricter specification compliance; an increasing demand to recover useable product and the need to minimise waste.
TWS says it offers a broad product portfolio, including sand wash and fines recovery plants; log washers; hoppers; feeders; conveyors; dewatering and static screens, and mobile, static and modular rinsers.
“With the addition of combination plants and water management systems, the range will provide the potential to work in many applications,” says TWS.
“Utilisation of proven Terex washing technologies and a strong focus on R&D will drive our new product development programme,” says Sean Loughran, global product line director for TWS.
“Supported by a dedicated engineering, sales and application team, TWS will quickly become one of the global leaders in mineral washing equipment.”
All washing products will be manufactured at Terex Corporation’s Dungannon facility in Northern Ireland and distributed through a global dealer network. Technical Support and Parts will also be managed from the Dungannon facility.
In another move,
Norstone, part of the
The new Hewitt Robins 2QV-14, 3m wide x 9.6m long triple-deck washing screen allows Norstone to do this. The heavy-duty screen was installed by Agdermaskin (Hewitt Robins’ partner in Norway) who also designed and installed the stand-alone washing plant next to Tau’s ship loading facility in order to be able to rinse the railroad aggregates or other products before being transferred into the ship loading system.
The screen handles 1,500tonnes/hour of railway ballast plus over 10,000litres of water/minute in the feed and from the sprays.
The screen is required to wash the material prior to being loaded onto the ship and also take out -20mm waste. The top deck separates at 45mm; 20mm middle deck and 4mm bottom deck using Tema Isenmann WS85 heavy duty modules.
“The new stand-alone washing plant allows us to increase our production at Tau and supply a higher quality product,” says Bjørn Ingvalstad, technical manager, Norstone.
Haver Screening Group’s (HSG) Hydro-Clean washing technology is being used by a gold producer who wants to increase production, reduce water consumption and minimise wear.
HSG worked closely with the producer to set up the unit and rinse screen as a separate test operation to prove it could successfully wash the operation’s three distinct products better than the current test equipment.
“Each product has varying degrees of impurities, ranging from easy-to-wash to sticky material that is nearly impossible to clean with the current washing system,” says HSG. “Since installing this combination, the operation has increased production from 5tonnes/hour to 25tonnes/hour, reduced its water consumption by up to 70% and saved up to 30% energy for every tonne of material.
“In preparation for a large mine upgrade project, these positive results have led the operation to put the Hydro-Clean in its plans for all future mineral washing.”
Said to be ideal for use in clay-heavy material deposits, the Hydro-Clean employs high-pressure nozzles, rotating at 90rpm, to spray up to 90% recycled water on the material with pressures up to 200bars to remove silt and clay particles as small as 63microns from mineral mixtures.