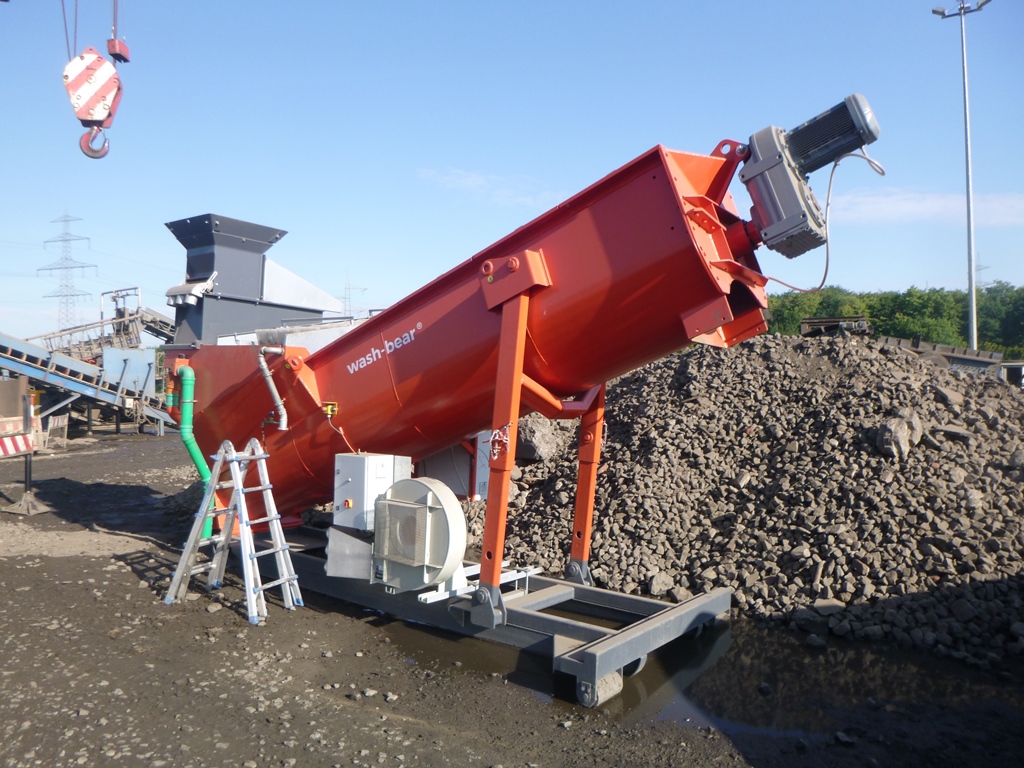
The mobile wash-bear system is purpose developed for the separation of light materials from heavier particles such as building rubble, and London-based Orba Group says it has proved to be an effective solution in quarrying, recycling, demolition and general construction applications.
The wash-bear works according to the floating-sinking principle and is designed to reliably and cleanly separate light materials such as wood, artificial and insulating materials from the minerals. Orba Group says that all mineral substances can be cleaned, but most of all, RCL building materials.
The closed system consumes whatever water adheres to the discharged mineral, meaning that in a 10 hour shift 4-8 m3 is used in practice, whereby the inlet is controlled automatically by floats. Orba Group says this technique avoids the build-up of chemicals in the eluate.
The water used is absorbed into the basic moisture of the RC material. What comes out with regard to the chemical composition, at most, is what was discarded by the rubble in the system. The energy expenditure is at around 8-15kW/h during operation, which is claimed to be significantly lower than an air sieve with a similar performance.
The wash-bear can be integrated into the overall process chain even on narrow construction sites. By using (the optional) ‘clean extension’, t can be used as a wet-processing system for the removal of fine fractions,for example when washing track ballast.
The current generation of systems is available as wash-bear 2.0 in three models, which are designated as ‘S, L, XL’ depending on size. Their hourly throughput rates range between 100 t/h and 190 t/h depending on the input. All types are designed with a mobile lift hook for easy transport.