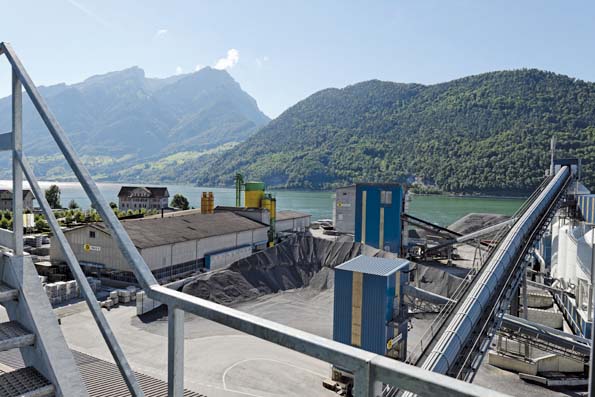
Plant automation has taken off in a big way in quarrying and aggregate processing facilities. Guy Woodford looks at some of the latest solutions.
The Swiss Müller-Steinag Group has constructed a hard rock processing plant at its Rozloch facility on Lake Lucerne to produce aggregates from siliceous limestone for use in concrete production. The company is using the
Within the Siemens TIA Portal, three ET 200M I/O modules are connected via Profibus to the central Simatic CPU 317-2 PN/ DP for the hard rock processing plant. These are used to control the Sinamics frequency converters for the crushers, conveyor belts and screen drives. Other controllers are used to monitor water treatment and the grit chamber. Operation of the plant takes place at two PC stations equipped with the Simatic WinCC Scada system. One PC operator station is located in the treatment plant, the other – connected by a 300m-long fibre optic Ethernet cable – is located in the control room of the gravel crushing and sorting plant.
The fully automatic loading station is also linked to the central CPU. For rounding the rock in the crusher, a Sinamics drive is used with a nominal output of 132 kilowatts, whose speed is adjusted to different process requirements using a frequency inverter. This means that fewer on and off switching cycles are required, and contributes to a more energy-saving operation overall.
The Müller-Steinag Group, one of Switzerland’s biggest suppliers of natural building materials and concrete products, uses the coarser components to produce ballast and aggregates for pavings in its gravel crushing and sorting plant in Rozloch.
Although to date the company has sold its finer grades with grain sizes below 22mm for use as levelling material, in actual fact this high-grade siliceous limestone hard rock product was wasted on this application. Müller-Steinag consequently decided to develop a process which would allow rounded and washed hard rock products to be manufactured from these finer components.
What emerged was a highly valuable aggregate for concrete, which not only improves the flow properties of the concrete but also increases its durability and resistance.
The Müller-Steinag Group may be counted among the pioneers of the wet processing method. The stone components screened from the raw material with a grain size lower than 22mm are first washed, then rounded and graded. Washing out the fine dust takes place in a closed water circuit with minimal loss of water. The rock mix is rounded by a crushing process in a horizontal
crusher and then graded in screening machines.
The rounded end products, crusher dust and hard rock are stored in four size grades in silos and can be purchased from a self-service place provided at fully automated truck loading bays.
The CS-2000 crushing and screening control system comprises a control PC with full colour graphic display, either located in a control room or in many instances now in a main office such as a weighbridge office sited well away from the plant.
A major benefit is that the whole operation is controlled remotely, removing the need for a manned control room close to the plant. This allows scope for a single operator to monitor and control two plants from one central room, or to double up plant control with other functions such as weighbridge operation. Essentially the CS-2000 largely runs itself, and usually only requires the operator’s attention when it detects a plant problem.
The system can also integrate facilities to control primary rock breakers remotely, removing operators from dust, noise and vibration conditions often found in the vicinity of the primary intake. One particular case has allowed an operator originally stationed in a local control room alongside the primary inlet to move into a clean weighbridge office, in line with the operating company’s drive for a healthy working environment and higher efficiency.
Full process information is displayed to the operator on an animated colour graphics mimic screen showing which plant items are running, material moving through the plant, the rate at which material is being processed, plus motor currents, levels in bins/surge hoppers etc.
The CS-2000 system provides full automatic start/stop of all plant items in the preferred sequence. Once started the system continuously monitors plant performance, for example, by reading the rate of passage of material through sections of the plant using beltweighers, or measuring the current drawn by crushers and screens, or using level sensors to monitor the contents of surge hoppers or even final storage bins. Not only is this information continuously provided to the operator but crucially the system then adjusts the process automatically, typically controlling the rate of delivery into the plant by changing the speed or extent of vibration of an incoming feeder, to keep these measured flow rates, currents and/or levels at or close to their required settings.
This ensures that the plant is automatically kept at its optimum performance, maintaining high plant throughput whilst reducing the risk of overloading, which in turn reduces the risk of blockages or spillages which can otherwise result from overfeeding or from sudden changes in the composition of the raw product being fed into the plant.
The CS-2000 also ensures good product quality by keeping the feed rate over screens as consistent as possible, or in the case of sand/gravel processing by continuously monitoring the density of the sand/water in the washing plant and adjusting the flow of water in and sand out from the plant to optimise the quality of the sand produced.
Furthermore details of the production process are continuously recorded on a disk on the main control PC, allowing records of production rates, running times of motors and other key performance indicators to be examined by the technical or management teams at a later stage whenever that information is required. This is a key benefit in allowing bottlenecks to be seen
and maintenance requirements and/or potential improvements to the plant to be identified. This information can also be available in other locations well away from the quarry itself, for example regional offices or head offices, over broadband connections.
The system offers several key benefits to improve throughput and bottom line return. As the process is essentially automatic, there is far less dependence on expert skills and knowledge of a particular operator, translating into greater flexibility of staffing. This means that different people can run the plant, for example, during holidays or when the usual operator is on leave. In many instances, the same person can multitask, monitoring the CS-2000 while primarily concentrating on another task, such as issuing weighbridge tickets.
The CS-2000 also detects if no material has passed over the incoming beltweigher for a time, ie that the plant is not being fed, and switches off the incoming feeder and shuts down the plant in a controlled sequence. This can result in reduced energy costs and unnecessary wear and tear on the plant, as it is not left running for extended times without producing.
Additionally, related items of the system such as the wireless graphics display for installation in dump trucks mean that dumper drivers can monitor the levels in a set of final bins and thus only take material from them as they become full, leaving them free to conduct other tasks around the quarry much of the time, rather than being essentially tied to the one area of plant.
Moreover, this same wireless unit allows the dumper driver to initiate loading of material from the bins from within his/her cab, avoiding the need to get in and out and thus reducing the risk of slips/falls or (worse) injury from other heavy vehicles.
Insight HQ not only allows operators to view scale data from their equipment, but also uses the Cloud to consolidate information from scales on each machine within a company fleet. By doing this, operators and project managers at different locations are able to access the information and determine the progress of equipment at specific job sites