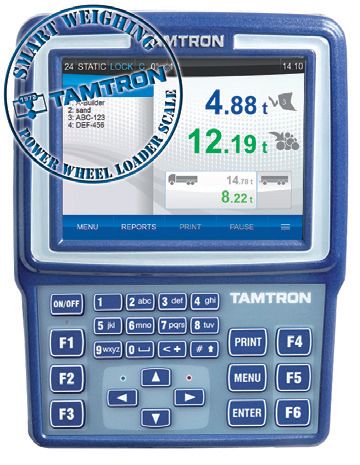
Accurate payload monitoring over time can save huge sums for a quarry business, with leading weighing solution manufacturers constantly bringing new products to the market. Guy Woodford looks at what’s new for 2015.
For accurate payload monitoring within quarry operations,
InsightHQ is also said to be ideal for other industries using loaders, excavators or conveyors, including cement or asphalt production, mining, and earthmoving.
Johan Smet, Trimble Loadrite general manager, said: “InsightHQ gives users the information they need to know about how their operation is performing, making it easy for them to closely manage the main profit drivers of their business. In addition to providing live data to take action, InsightHQ also generates easyto- use reporting that enables managers to optimise their day-to-day processes and tracks the effectiveness of operational changes.”
InsightHQ allows access to its performance data from a web browser on a smartphone, tablet or PC and Smet added: “Customer feedback shows quarry managers are checking the status of the quarry remotely, helping to reduce productivity loss from downtime issues. In addition, email reports provide a regular summary right into their inbox.”
Plant snapshot through InsightHQ allows site managers to spot issues quickly to ensure delivery on their daily targets. A delay in reacting to issues, in the load-out area for example, could mean the customer delivery expectation for the day is not met, losing goodwill or an entire sale.
Reports provide information to optimise plant and loading performance and asset utilisation to increase productivity. Trimble Loadrite also says that InsightHQ is a fraction of the cost of PLC (programmable logic controllers) or SCADA (supervisory control and data acquisition) based reporting systems, but is more flexible and provides key performance indicator (KPI) data in an easy to interpret format. The first European company to introduce the onboard weighing concept for dump trucks application, with more than 15,000 of its systems installed and working around Europe, Italian weighing solutions firm
Within Europe, Outset is looking to create a German subsidiary, given its status as the continent’s biggest producer of aggregates, and national quarry operators need of accurate, cutting-edge weighing technology.
After doing this, the firm will focus on setting up a US subsidiary. Among Sandrigo, Vicenzabased Outset’s large range of products is the VISION EVOLUTION system of onboard weighing for earthmoving and logistics. It is described by Outset as the ultimate innovation in onboard weighing systems, with its large colour graphics display, a user-friendly icon menu and navigation wheel system for browsing through menus. Connection to an external camera is said to be a crucial aid during excavator, wheeled loader or articulated dump truck manoeuvring, guaranteeing more safety with the advantage of using a lone display.
A new weighing concept developed with years of experience on the field, VISION EVOLUTION is said to be ideal in every type of excavation as it automatically checks the load in both deep and ground level excavations. Without pausing, it registers and displays dynamic weighing during all lifting operations. The system also automatically adjusts weighing height when necessary.
Now upgraded with new weighing software and sensors and certified with Class approval MID Y (b) and OIML R51, VISION EVOLUTION allows the user to eliminate the use and the costs related to the weighbridge by certifying the material loaded and invoicing directly to a customer from the wheeled loader, optimising working time.
Part of Outset’s LANX solution range and ideal for use in quarry dump trucks, the LANX HD system comes with a control unit that can be directly installed in the driver’s cab and displays weight loaded on board in real time. Furthermore, it allows for the management of moved materials, and to select the operators or the destination.
LANX HD uses ES160 and ES400 digital pressure sensors positioned on the vehicle’s suspension and shows all data on a clear display, without having to press any keys. All round trips are automatically memorised without the need for operator intervention.
The internal database allows for display reports of each round trip, including material, operator or destination, date, time and weight data, as well as daily, weekly or monthly reports with individual and overall totals for all loads transported. All weighing data and individual reports can be transmitted via GPRS or printed out on a specially designed printer installed in the cab. The USB reader connects with the LANX HD system allowing for recorded weights to be saved through a USB Flash Drive device.
Outset says that the system pays for itself immediately, as knowing the load weight when you travel means optimising transport times and economic yield in greater safety.
Cement giant
From the outset of this high profile project Lafarge commissioned leading weighing specialist Precia Molen to design and install a fully automated loading and weighing system, including interfacing with Lafarge’s Quartz back office business system.
Situated south-east of the Sainte Baume mountains, 47km from Marseille, Signes Quarry occupies 73hectares, of which 33 hectares are exclusively dedicated to the extraction of limestone deposit which is processed to produce sand for either concrete batching plants or road products. Prior to the installation of the new loading system the trucks were loaded manually using loading shovels and were required to return to the out weighbridge to collect their documentation. However, at peak times this created traffic congestion resulting in long queues and reduced truck throughput.
The new weighing and driver self-loading system had to meet Lafarge’s four key criteria: minimal staffing levels for vehicle control, weighing and loading operations; full integration with the Lafarge Quartz business system; a robust and resilient system designed to ensure 24/7 operation; replace the normal out-loading procedures using a loading shovel.
Drivers arrive at the incoming weighbridge Precia Molen BI400 driver console and via a dialogue display they are asked to present their RFID card. The system validates whether the vehicle is an authorised user of the site, confirms the product to be loaded, directs the driver to one of the seven loading points and calculates the correct net weight to load from measured tare and authorised maximum gross weight (PTAC).
When the truck arrives at the self-loading driver console the driver is prompted to present the RFID card to confirm that the truck is at the correct loading point. Once loading commences, real-time integration is initiated between the Precia Molen BT conveyor scale and the plant PLC control to ensure safety interlocks are observed. The truck must drive slowly forward as the target weight is reached as indicated on the remote weight display.
Once the loading cycle is complete and the truck has reached the target net weight, final documentation is printed and the driver is directed to exit the site without the need to return to the exit weighbridge.
The installation of the Precia Molen BT weighing conveyors within the site is said to have provided significant benefits for Lafarge, as the loading stations represent a substantial saving on labour costs, eliminating the need for seven weighbridges in excess of 24m in length.
The BT weighing conveyor comprises a fully weighed conveyor connected to the chassis by two articulations placed along the centre line supported at the opposite end by one or two load cells. These instruments are for accuracy class 0.5 +/- 0.25% commercial use and perform the same bulk management functions as a weighbridge or hopper scale.
The BT is available with a 40cm wide belt, 120cm in length, or in sizes up to a 180cm wide belt, 500cm in length. The weighing conveyor is capable of dealing with a material flow of up to 1,000tonnes/hour.
By using the automatic system, the whole cycle is said to be completed in only ten minutes compared to more than 40 minutes with manual loading. Since commissioning, nearly 90% of drivers now choose this mode of loading which reduces time on site and improves productivity. Another important benefit in terms of quality of service is that the certified weighing also delivers the expected quantity, avoiding the risk of overloading or underloading.
“This diminishes rejected results dramatically, saves drivers time and improves the productivity of customer’s operations.” The company claims that Smart Weighing improves many daily operations such as, for example, load control. Overloading of the truck is prohibited by law, but underloading is also a problem as it will sacrifice operational efficiency and profitability.
“Smart Weighing technology allows faster and more intuitive tip-off function as the boom does not need to lower unnecessarily anymore. That saves time, fuel and nerves from both operator and owner as there are no extra lifts required anymore in the work cycle,” says Tamtron.
“In addition, when heavy material, for example large rocks, are weighed, the weighing can happen closer to the ground, saving time, fuel and the loader, but also increasing safety at worksite.”
Tamtron’s Smart Weighing scale is said by the firm to have been thoroughly tested in reallife work in various challenging conditions, and the company says it is easy to install, with the machines back at work in one day with all installations, calibration and verification having been completed.
“The Smart Weighing scale is available for all different types of loaders and machines and the installing requires minimal mechanical modifications on the machine,” says Tamtron.
Intercomp’s MS450 has rugged appeal
Available in various configurations for over a decade, the rugged platform scales are said by the US firm to provide a durable, high-capacity weighing system to increase on-site efficiency, prevent premature wear on vehicles, conduct on-site weight studies, and help operators maximise payloads. It can also be used as a way to verify onboard weighing systems, becoming more and more common on modern vehicles.
The versatile platform scales are made to fit quarry operational needs and are available as above-ground, portable scales with ramps, or as semi-permanent inground systems, with both styles featuring temperature compensated sealed load cells to stand up to harsh environments and weather conditions. Fully integrated RFX Wireless Communication enables a cable-free connection with a variety of devices including weight management software, portable indicators, printers, displays, and many more. It is said to bring peace of mind to quarry operators no longer having to worry about severed cables and wires.
MS450 scales provide further operational convenience by weighing vehicles statically or dynamically with accuracies of 0.5% static and 1-3% dynamic.