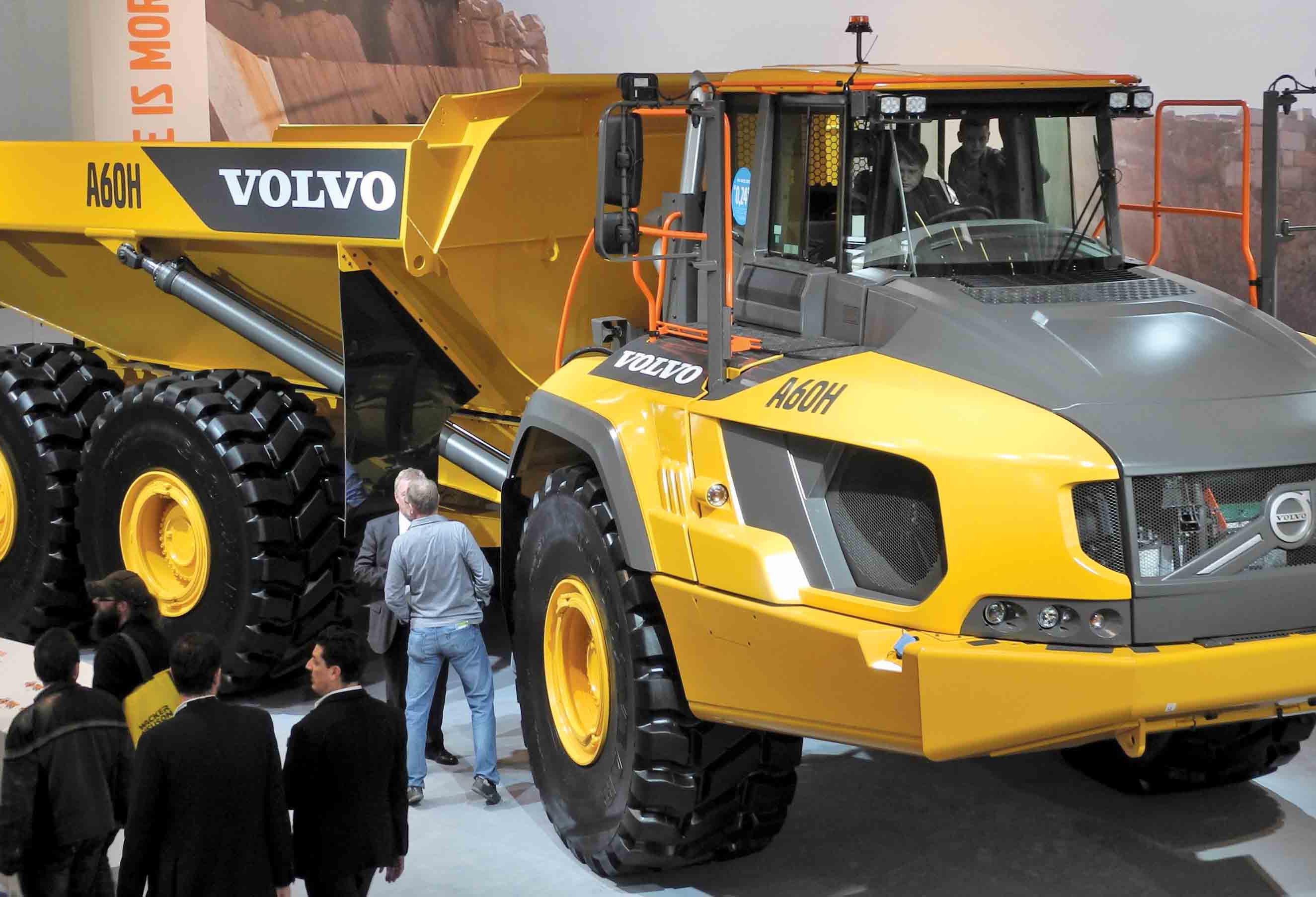
The correct tyres on quarry equipment are essential for productivity and profitability. Patrick Smith reports.
Quarries are tough places for tyres, representing a major investment for machine operators who can spend thousands on the correct product.
In Germany,
With the trucks having a gross laden weight of up to 100tonnes, Ralf Schmidt, purchasing manager at Cemex plant in Steinbrüch Piesberg, was asked what he looks for in a tyre.
“Our need is to find a tyre ensuring many advantages: high stability on rock surfaces and muddy grounds as well as a tyre life of over 2,200 hours. Indeed, the quarry of Piesberg where our dump trucks operate is quite special,” says Schmidt.
“Piesberg carbon quartzite presents huge challenges for any tyre, as around the 300-million-year-old material extracted from the quarry in Piesberg is one of the most abrasive stone of all. Good EM tyres, which easily last for 4,000 hours in other quarries, only just manage 2,000 hours in Piesberg. Given the high level of tyre wear, the choice of tyres in Piesberg also plays a role financially.”
He says that the severe operating conditions of the four Cat 775E dump trucks caused fast and irregular wear of the tyres on the rear axle.
“For this reason, we were looking for a valid alternative to reduce machine downtime and the number of tyre substitutions. We have tested Earthmax SR 45 tyres size 24.00 R 35 on our Cat 775E dump trucks for one year. At the end of the tests the results were very satisfying and exceeded our expectations. Therefore, we decided to equip the tyres on the rear axle of our dump trucks with BKT tyres.
“We started to use BKT tyres a couple of years ago under the suggestion of our tyre dealer. Before that we had no experience. Actually, it turned out to be a good suggestion.
“BKT tyres are cost effective if compared with other premium brands. They ensure a very good ratio of price and operating hours.
“Going into details our savings are more productivity, lower machine downtime, longer tyre life and fewer tyre substitutions.
“The service provided by Bohnenkamp and our tyre dealer, White of Duisberg, is excellent. We can always count on their expertise.”
Marc Preedy, commercial director for
“In the majority of cases these tyres operate in tough and hazardous conditions, such as in quarries, mines and on construction or waste sites.
“This means that more extensive care measures are essential to prevent damage than with most other tyres. For the maximum return on investment from OTR tyres it is essential to use good quality tyres and to look after them.
“It is vital to select the right tyres for a specific application in order to guarantee an optimised performance from the machine and the lowest operating costs for the operator. This means taking into account the right balance between different performance criteria such as protection against cuts and impact, traction, resistance to abrasion and resistance to heat generation.”
Preedy says loads should always be correctly positioned to ensure vehicular stability or there is the risk of damage to the tyres or even to the machine. Electronic weighing devices can be “worth their weight in gold” in preventing these situations.
“The operator can make or break the successful operation and long service life of tyres on a machine. Correct driving techniques and speed play a significant role in maximising tyre life and efficiency but it is not just the machine operator who influences the situation. Those involved in loading and maintaining the roadways also need training in the issues that can affect tyres.”
For
“The development of the new TL-4A in size 33.25R29 for Volvo’s new A60H articulated dump truck is a perfect example of innovative collaboration to achieve the common goal of satisfying customer needs in the OTR industry and helping them to reduce their operating costs,” says Octavian Velcan, managing director OTR tyres Goodyear Europe, Middle East and Africa.
Meanwhile,
The tyre is able to cover a distance of up to 10km/hour compared to the current tyre’s limit of 6km/hour (Michelin XMINE D2 SR), an increase in operating speed made possible by a new tread compound that effectively limits heat build-up within the tyre.
For rigid dump trucks in surface mines, Michelin offers its new XDR3. It claims three innovations, a revolutionary new tread pattern, four innovative rubber compounds (MB4, MB, MC4, MC), and corrosion isolating steel cables, combining to give a minimum increase in tyre life of 10% compared to the tyre’s predecessor, the XDR2.
Michelin’s R&D teams spent more than six years developing this new tyre and, during the testing process, exposed the tyres to more than 25 million kilometres of wear, the equivalent of circling the earth 625 times.
The 40.00 R 57 Michelin XDR3 is now available. The 53/80 R 63 will be available from January 2017.
The company says the EM-Master for ADTs, loaders and dozers, used for transporting large quantities of bulk or aggregate material in extreme conditions, is customised for these specific demands. The tyre is available in two versions with different tyre tread designs.
The EM-Master E3/ L3 features a normal tread depth and wide spacing between the blocks while the Continental EM-Master E4/L4 features a greater block size with less spacing between the blocks and a deeper tread depth.
The company’s RDT-Master for rigid dump trucks has a special tread design with a deep tread depth and a wide and flat tread radius, offering high loading capacity and cutting resistance.
The RDT-Master E4 is available in the sizes 18.00R33, 21.00R33 and 24.00R35.
Italian company,
Luigi Pedrini’s company has been a key partner in this market for some years, during which time the company has concentrated on precured tread strips.
“This event represented the ideal opportunity to present the Ringtread system, the only retreading process using spliceless precured tread rings,” says Marangoni.
“The advantages of the ring technology are that it enables a tyre to be retreaded to match or exceed even new products in terms of reliability and performance.”
The technology was illustrated to the Cuban industry; to the Poligom (Rovimpex’s long-time customer for retreading products) management in particular, and Comandante Ramiro Valdés, Vice President of the Government of Cuba and former Minister of the Interior.”
In an article on tyre selection, Michael Dembe, manager of product development construction for Camso (formerly Camoplast Solideal), says:” Along with improved wear life and less downtime, choosing the right tyre for the right application allows future cost savings with retreading. Whatever your plans for reducing tyre costs, the best time to start is always now.
“At the very least, keep a consistent record of every tyre, its purchase cost and its service miles at replacement. Even better, is to build a database that notes the specific machine the tyre is on, its operating hours and idle time, repairs and any downtime due to flats.
“Often this tracking can be done in partnership with a local tyre dealer.
“These tools will give your sales consultant a head start on establishing benchmarks for how your current tyres are performing on the equipment you run. That kind of knowledge is power.”