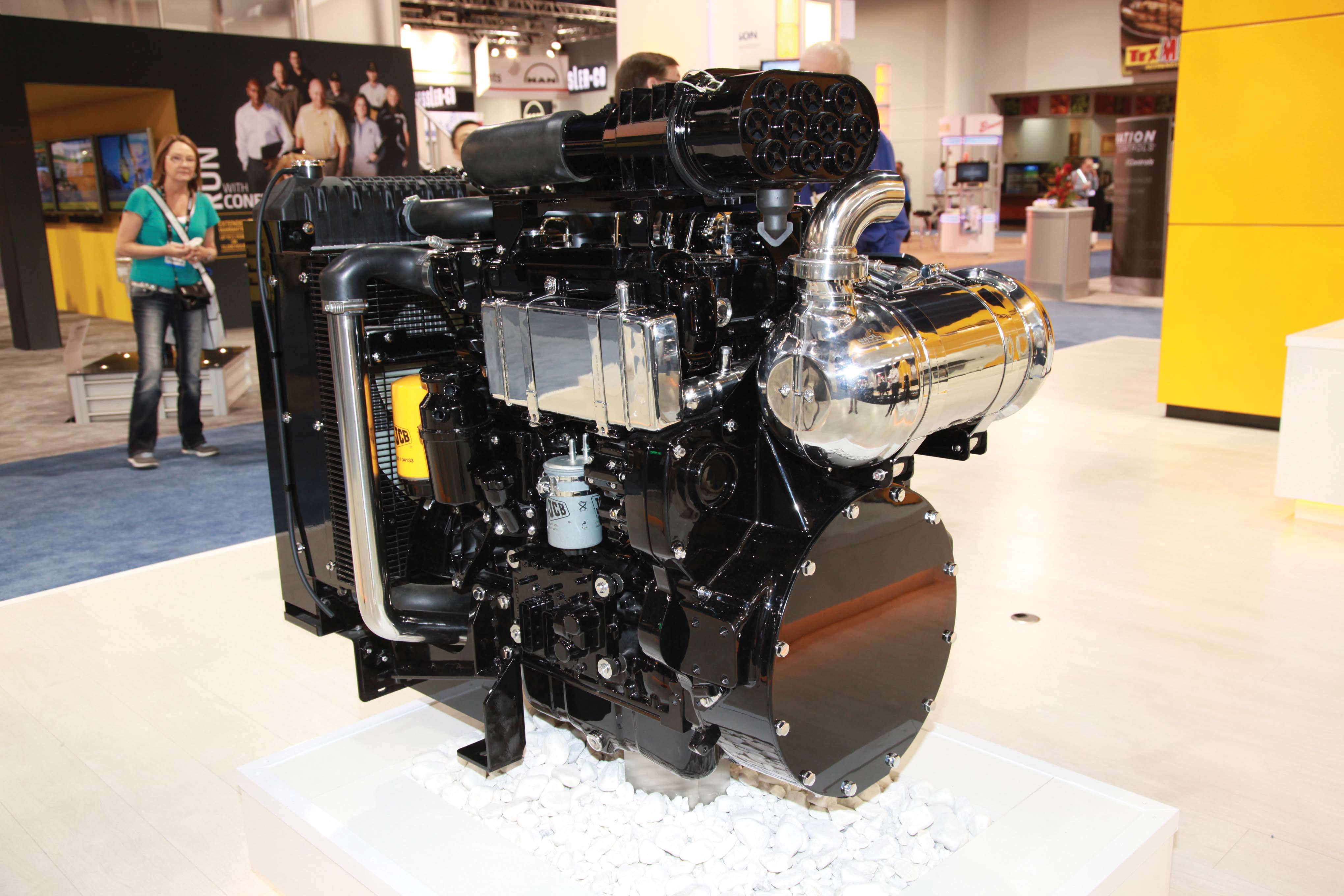
Solutions for Tier 4 Final emissions regulations have been coming thick and fast, with many companies showing off their engine options of DOC, DPF and SCR aftertreatments.
Some companies, including
Meanwhile, with the Stage IV/Tier 4 Final legislation now in force,
“Drawing on the research strength of the Volvo Group, the Volvo CE Stage IV/Tier 4 Final-compliant D4, D6, D8, D11, D13 and D16 diesel engines meet the stringent new EU and US emissions legislation, while also improving fuel efficiency by up to 5% over previous models and reducing running costs overall,” says the company.
“The V-ACT (Volvo Advanced Combustion Technology) engines feature advanced fuel injection, a more effective air handling system and enhanced engine management.
Comprehensively tested in punishing conditions, the Stage IV/Tier 4 Final engines have been validated in bench and multi-application field testing to reduce nitrogen oxide (NOx) levels from Stage IIIB/Tier 4 Interim levels of 2.0g/kWh to just 0.4g/kWh (an 80% decrease) and in observance with the demands of the new legislation, which came into effect in January 2014.”
To meet these new requirements without dramatically changing the base engine, the majority of Volvo Stage IV/Tier 4 Final engines now incorporate Selective catalytic reduction (SCR), a technology that has already been comprehensively tested in more than one million SCR-equipped Volvo trucks since the system was introduced in 2005.
SCR uses an injection of a reagent liquid (a 32.5% solution of urea in deionised water) into the exhaust gas flow to convert NOx to nitrogen and water, both of which are found naturally in the air. The reagent liquid is called AdBlue in Europe and DEF (diesel exhaust fluid) in the US. The system reduces NOx emissions by as much as 95%.
Along with SCR, the cooled external exhaust gas recirculation (cEGR) system also works to lower NOx by diluting the air in the combustion chamber, which in turn lowers combustion peak temperatures.
“The fully automatic diesel particulate filter (DPF) system reduces harmful particulate matter without interrupting machine operation or lowering productivity or performance,” says Volvo CE.
“The Volvo CE Stage IV/Tier 4 Final engines have benefited from more than 80,000 hours of testing in articulated haulers, wheeled loaders and excavators, as well as on engine test benches. Prototype testing has also been done in sub-zero temperatures, extreme heat and at high altitudes.”
Innovative emissions control technology is a key feature of the latest diesel from
The company has continued developing its Integrated Emissions Control system to meet the emissions targets, with the technology including various combinations of aftertreatment and emissions-reduction components.
The system configurations have been tailored to meet regulations and customer needs in each power range, and John Deere is offering three Integrated Emissions Control system configurations for the Tier 4 Final/Stage IV requirements. For the 36-55kW power range, the company is offering engine models using an exhaust filter that contains a diesel oxidation catalyst/diesel particulate filter (DOC/DPF) without cooled EGR or SCR. For the 56-104kW range, the PowerTech PWL 4.5L engine is equipped with cooled EGR and an Integrated Emissions Control system configured with SCR and a DOC. Engines delivering 93kW or more feature an Integrated Emissions Control system comprising cooled EGR, a DOC/DPF and SCR. All John Deere Integrated Emissions Control system configurations are designed to meet the demands of off-highway applications.
Using a dual SCR system, the water-cooled 90º V6 and V8 engines with power outputs from 390-520kW, do not need to use cooled EGR, DOC or DPF technologies. Compared to a similar engine using cooled EGR, Deutz said its V6 and V8 engines can be installed with a cooling package that is around 20-25% smaller, improving packaging for OEMs.
Deutz’s SCR package uses a combined DOC/SCR catalyst as the first phase of exhaust treatment, followed by a ‘clean-up’ catalyst.
Despite increased fluid consumption for aftertreatment, the Deutz V6 and V8 engines are said to offer up to 8% more performance with average fuel consumption reduced by around 5% compared to the previous Tier 4 Interim versions.
The six-cylinder, 12litre engine is purpose-designed to meet US EPA Tier 4 Final near-zero emissions regulations with a more compact envelope and over 30% higher power-to-weight ratio than the class average for engines with a similar power range.
Importantly, the QSG12 brings a major advantage for Tier 4 Final equipment installations by restoring the envelope size of its QSM11 predecessor, which was used for Tier 3 applications. Higher efficiency air handling and advanced combustion enable the QSG12 to return to the simplicity of a wastegated turbo-charger and achieve near-zero emissions without the need for a cooled EGR system.
As a result, internal loads on the QSG12 are reduced, says Cummins, to free up extra power potential, while heat rejection is lowered by over 40% compared with engines using cooled EGR.
Liebeherr Component Technologies is a new division set up by the German manufacturer to promote the sale and distribution of its components to external customers.
For Tier 4 Final, the company’s latest generation of engines operate with SCR-only technology, avoiding the need for a particulate filter, oxidation catalyst or exhaust gas recirculation. But the company offers much more than the latest emissions-compliant engine packages: it also offers basic engine packages with standardised interfaces for Tier 3 compliance. This means a compact EGR system for the Tier 3 version, which can be removed for less regulated markets requiring basic engines.
The
Enter the Dieselmax 672, JCB Power Systems’ new six-cylinder engine platform. Unveiled in the UK towards the end of 2013, the company introduced the 7.2litre capacity six-cylinder to a US audience to showcase its capabilities.
Launched in mid-2013 as a Tier 2-compliant power unit for less regulated markets, the Dieselmax 672 now gains an external EGR system to meet Tier 3 emissions levels.
With specific fuel consumption said to be as low as 189g/kWh, the six-cylinder engine delivers power outputs from 140kW to 212kW. It is anticipated that this latest JCB engine development will soon adopt a similar Tier 4 Final emissions solution to that used on the company’s smaller four-cylinder Ecomax engine range.
The Ecomax engine uses highly efficient combustion technology for the 4.4litre and 4.8litre versions, allowing them to meet the required standards without the use of a DPF.
A compact SCR solution will be used on engines above 55kW and the SCR catalyst is incorporated into a single exhaust silencer, in most cases replacing the existing exhaust box, to provide a ‘one-can’ solution.
It is recognised as a compact solution that remains straightforward to install in a wide variety of machines without incurring costly modifications to bodywork.
A high-sulphur fuel capability has been announced by
MTU’s sulphur tolerance solution will be available in mid-2014 for Tier 4 Interim 900, 500 and 460 series engines. This will be followed by the company’s complete line up of Tier 4 Final certified engines in the 1000-1500 series in the future.
The solution involves recalibration of the engine ECU to isolate the aftertreatment system. Once disabled, the SCR catalyst does not need to be removed, says the company.
MTU said this new capability should simplify design, ordering and installation processes for OEMs and repower customers around the world.
The company has tested the engines in applications such as excavators, wheeled loaders, crushers and dump trucks.
Scania’s technology to minimise emissions includes key features as extra-high-pressure injection (Scania XPI), EGR and SCR. A sophisticated control system optimises a large number of engine parameters, with different modes that combine the amount of fuel, injection timing and settings of the variable geometry turbo-charger. This controller ensures that the mix of air and recirculated exhaust is combined with the correct amount of AdBlue.