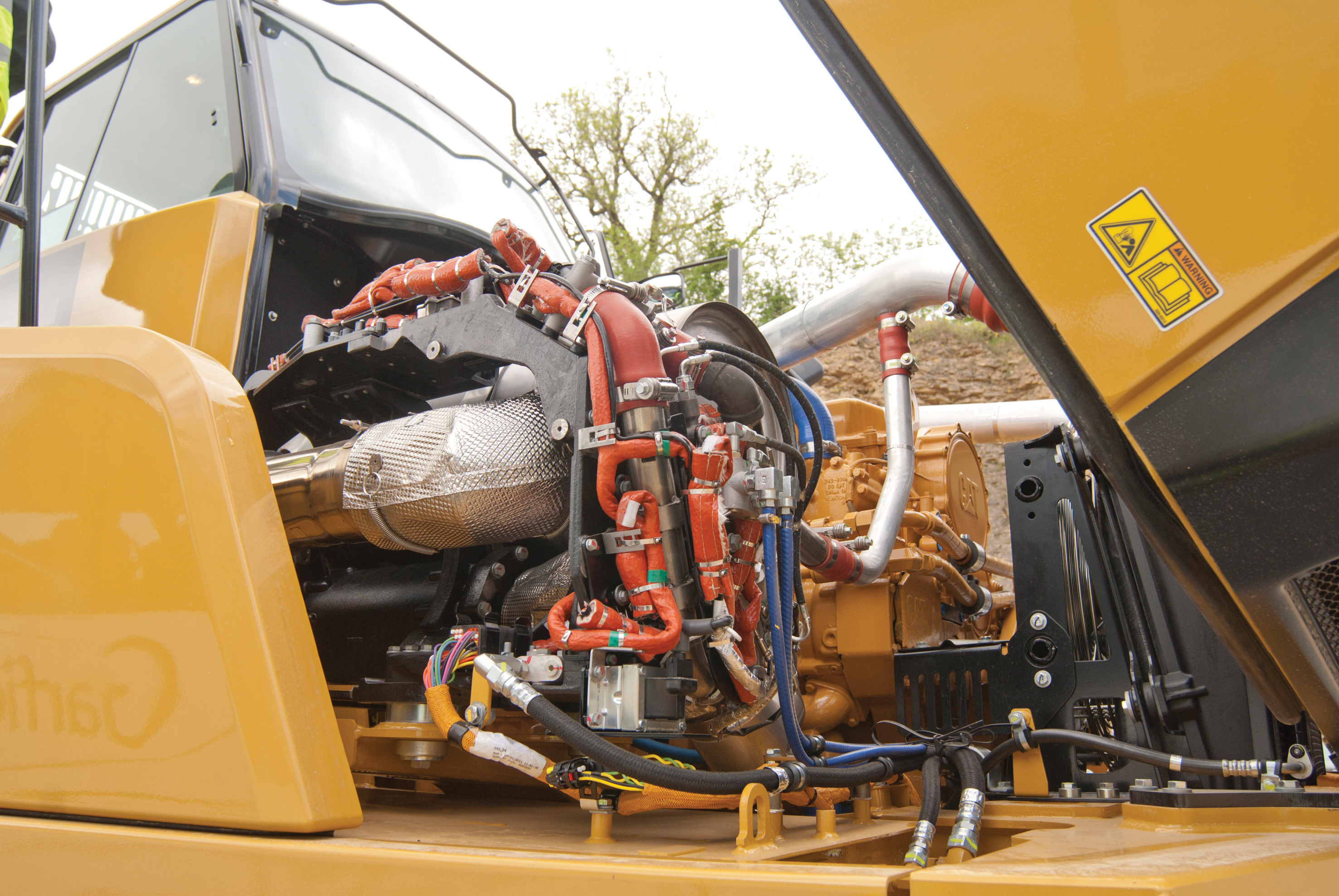
Dan Gilkes looks at emissions regulations and how engine manufacturers have and are meeting standards
On-highway truck manufacturers in Europe have started to take the wraps off their Euro 6 engine solutions, introducing a range of trucks capable of dealing with ever more stringent emissions control.
Why should we in the off-highway market care, you might ask? Our regulations are different to the on-highway market after all.
However, while on-highway regulations don’t include quarry equipment, they will certainly have an effect on those quarry owners that also run a fleet of delivery trucks.
More importantly, what happens on the road today eventually follows in the off-highway market. Yes, it may take a few years but you can be sure that the same measures will be implemented in the plant sector in the next few years.
Of course, we have just been through a round of emissions regulation, with EU Stage IIIB/US Tier 4 Interim standards now in force across much of the industry. Surely, time to take a step back and get used to diesel particulate filters, diesel oxidation catalysts and putting AdBlue into the right tank then?
Not quite. EU Stage IV/US Tier 4 Final standards are already just around the corner and will start coming into effect in 2014. So can we expect to see manufacturers going through the whole process all over again throughout the next two years in preparation?
Stage IIIB/Tier 4 Interim standards call for a major reduction in particulate matter (PM) and a significant fall in oxides of nitrogen (NOx). In terms of engines in the most popular 130-560kW power range, that meant a cut of 90% in PM and a 45% reduction in NOx.
There is a similar drop in PM for engines in the 56-74kW range, though the cut in NOx is less severe than for larger motors. Tier 4 Interim standards also began in the US and Canada in 2011 for engines over 560kW, but these are not yet applicable in Europe or Japan. The NOx levels are also set much lower for engines used in portable power generation.
However, in January 2014, when EU Stage IV and the US Tier 4 Final standards come into play, there will be a further 45% drop in NOx emissions for engines above 129kW. Similar NOx levels will also be expected from engines above 55kW.
At this point both NOx and PM emissions will in effect be at near-zero levels, bringing off-highway engines virtually in-line with on-highway trucks.
To meet these regulations engine manufacturers have followed a number of routes, employing electronic controls, high pressure fuel injection systems and generally optimising combustion. In some cases they have also employed variable geometry turbochargers; cooled exhaust gas recirculation (CEGR); catalysed diesel particulate filters (DPF); diesel oxidation catalysts (DOC); selective catalytic reduction (SCR), and exhaust additives such as AdBlue.
Not all manufacturers have gone down the after-treatment route to meet Stage IIIB.
As we have seen in many of the latest equipment launches, emissions compliance has resulted in larger cooling systems to cope with the additional heat created by cooled EGR and by SCR systems. This in turn has led to larger engine canopies and in some cases, heavily revised bodywork on machines.
For equipment with SCR, it has also led to the installation of an additional tank on the machine for the AdBlue exhaust additive.
The good news at Stage IV is that with just three years between emissions standards, most equipment manufacturers will have made the necessary changes at Stage IIIB to cope with what is coming. That means that many of the new machines that we are seeing this year will require little visible change externally to meet the coming standards. Certainly we shouldn’t see a need for even larger engine canopies and increased cooling pack dimensions.
Further good news coming from the on-highway market is that ever more stringent emissions legislation can in many cases lead to improved combustion efficiency and reduced fuel consumption, despite increases in power and torque outputs.
We have seen similar results with Stage IIIB engines, which for many plant companies are now offering higher outputs with a 5-10% reduction in fuel consumption.
The downside of course is that technology is not cheap, so customers are seeing initial purchase prices rising, and service and maintenance costs too, as additional filters and low ash engine oils come into play.
The cost has not been cheap for the engine builders either, both in terms of development or manufacturing, as particulate filters and catalysts incorporate high value metals and other materials.
Indeed in the last couple of months we have seen further evidence of engine and machinery manufacturers working together on future development and production.
Engine giant
“The formation of the HCEC joint venture takes Cummins working relationship with Hyundai to a much closer level, where we can share our respective expertise and better position both parent companies for growth in markets around the world,” says Cummins vice president Rich Freeland.
Production will start in 2014 and the new facility has a capacity of up to 50,000 engines per year.
For
Volvo already uses Deutz engines in some of its smaller wheeled loaders and other models, so further cooperation in terms of development is a sensible move.
Earlier this year the two companies signed a memorandum of understanding aimed at jointly developing a range of medium duty diesel engines for industrial applications. They are also looking at establishing a joint venture in China to support the Volvo Group’s expansion plans in the Asian markets.
So engines and the machines that are powered by them are going to get increasingly expensive, both to produce and to buy.
However, the manufacturers tell us that the efficiency and fuel consumption benefits will in part outweigh this initial on-cost.
At the recent MINExpo show in Las Vegas, USA,
It says the new generation of MTU Series 2000 engines for construction and industrial and mining applications complies with EPA Tier 4i and Tier 4f emission limits without the use of any exhaust gas after-treatment.
The Series 2000 engines are powering applications such as excavators, haul trucks, wheeled loaders, heavy drilling units as well as dockside cranes and mobile cranes.
MTU says that for compliance with Tier 4 limits without any external after-treatment, it has implemented a combination of four key engine technologies: cooled high-pressure exhaust gas recirculation (EGR); regulated two-stage turbocharging; common rail fuel injection and an advanced diesel engine controller (ADEC).
But what about when the time comes to move the machine on? It has been well documented that Stage IIIB/Tier 4 Interim engines must be run on ultra-low sulphur diesel, which is not a problem in Europe or the USA. However, in many developing countries, the main buyers of used plant and equipment, low sulphur diesel can be harder to find.
To date, JCB has been one of the only engine suppliers to offer a de-rating service, to take a Stage IIIB engine out of the emissions tier system. This is achieved by reducing the common rail injection pressures and disabling the EGR system. Any JCB dealer worldwide can provide this service using standard service tools and this will allow the engine to run on higher sulphur content fuels.
For other engine manufacturers things are still not so clear. While this may not pose much of a problem to a company that runs its equipment full life, for those who prefer to move machinery on after a set period there may be concerns. This issue could also affect leasing costs as leasing companies and manufacturers will have to factor second life values into the original working rate. It is certainly something to consider when funding new machines.
So there are cost implications now and more to come at a later date. For many though the biggest concern currently will be the running of machinery on site today. In many cases that will mean setting up clean storage and distribution for AdBlue, considering additional service concerns for regular maintenance schedules and pre-planning downtime in the future for particulate filter and catalyst changing and reconditioning.
Emissions legislation is not a major concern as long as you understand the cost and service implications and plan your equipment operation accordingly. That may also include adjusting your operation to make the most of the increased performance available from the latest equipment on the market.