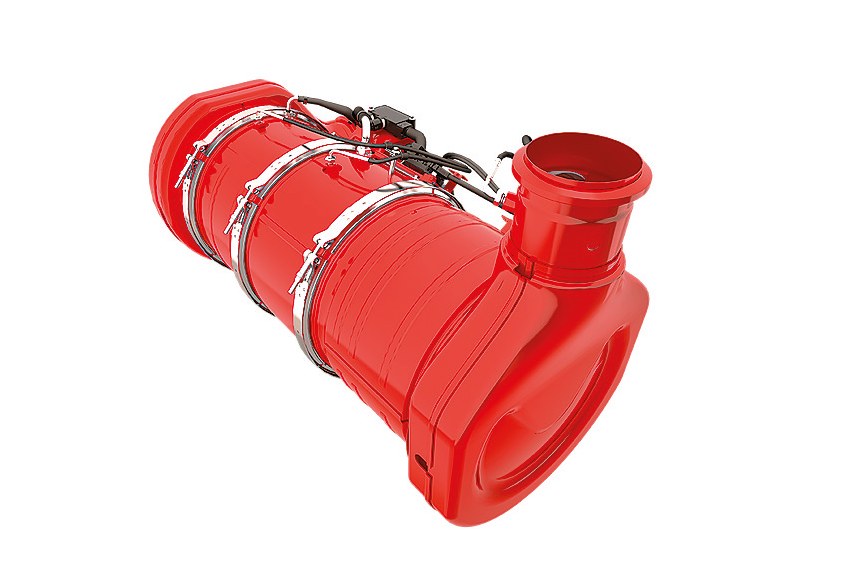
A wide variety of new Tier 4 Final/Stage IV emissions standard engines and other engine performance-enhancing technologies for quarrying and heavy civil construction machines have hit the market, with more than one leading engine manufacturer already turning its attention to the next emission stage requirements. Guy Woodford reports.
The world’s leading construction equipment engine manufacturers worked tirelessly to meet Tier 4 Final/Stage IV emissions standards, but they are already focused on the new show coming to town – Tier 5/Stage V emissions standard engines.
“We could achieve Stage V with our current DPF-SCR system, however Stage V is an opportunity to take this technology further,” said Richard Payne, Cummins’ off-highway regulatory affairs director.
While the current proposal for Stage V emissions is just that, a proposal that can still be amended before implementation in 2019 and 2020, Cummins believes that every engine manufacturer will have to use a Diesel Particulate Filter (DPF) as part of its emissions solution to meet the required levels of Particulate Matter (PM).
“Cummins has over a decade of experience in DPF and after-treatment technology with more than 590,000 DPF-SCR modules in use already,” said Jane Beaman, off-highway commercial leader at Cummins Emission Solutions. “It is a concept at present but we’re exploring it for our entire range.”
Advancements in catalyst technologies and efficiency improvements, plus Cummins’ investment in DPFs with higher ash capacities, are said to allow for longer cleaning intervals in the filter. The SCR catalysts, coupled with the EcoFit UL2 liquid-only urea dosing system, offer enhanced NOx reduction with minimised fuel and AdBlue use.
By making the DPF-SCR module smaller and lighter, Cummins says it will make it easier for equipment manufacturers to package the engine in their machinery.
“Over the last few years we have seen continued demand for smaller, lighter high-quality components to drive diesel engine efficiency improvements,” said Cummins sales and marketing director Suzanne Wells.
“The latest technological enhancements enable us to meet these demands as well as offer greater versatility, which allows the development of tailored customer solutions.” Meanwhile, at the recent
The Series 900 has been designed to meet the diverse duty cycles of this engine range. The technologies offered by the complete range are suitable for applications from 294-4,707kW.
“We tailor our development process to create solutions that complement our customers’ business strategies and give the optimum level of confidence in the robustness and flexibility of our products, which is vital in minimising downtime,” says Jonathan Wood, executive director, Cummins Turbo Technologies research and engineering.
“The advances of the Series 900 will be applied across the already robust and flexible product range, Series 800 and Series 1000, thanks to our world-class research and development facility, to create the most efficient and diverse turbochargers we have ever produced for the 16 litre and above engine range.” Cummins Turbo Technologies has also unveiled plans for investment in future technology solutions for the range to improve fuel efficiency.
Volvo Penta has two newly-redesigned 5litre and 8litre engines and a complete range of common-platform units spanning all emission levels.
At INTERMAT 2015, the company’s Stage IV/Tier 4 Final D11 engine was seen for the first time with the new Stage IV/ Tier 4 Final-compliant 5litre and 8litre engines.
Developed in coordination with the
All
The range also shares a common electronics platform that allows them to communicate using the same protocol, regardless of emission level. The company says that displacement has also been increased, compared to previous versions, offering improved engine block stiffness, as well as higher torque at low speed, but “despite a larger displacement, fuel consumption is reduced by as much as 2.5%.”
Volvo Penta also showed off at INTERMAT 2015 its Tier 4 Final/Stage IV after-treatment system, selective catalytic reduction (SCR), for the D5 and D8. It says it is a simple and straightforward way of lowering nitrogen oxide (NOx) levels. With SCR technology, AdBlue is injected into the exhaust line and reacts with NOx in the catalytic converter to turn the harmful compound into nitrogen and water.
Engine manufacturer
6R1300 was unveiled at INTERMAT 2015 in Bell’s 50 tonne B50E articulated dump truck, where it offers 390kW. Bell also uses the 6R1000 in its smaller B30E truck.
“By offering proven technology and flexibility as regards when to implement it, our aim is to provide our customers with the best possible product planning support and to help them upgrade their products to meet Stage V,” says Michael Wellenzohn, a DEUTZ board member with responsibility for sales/service and marketing.
DEUTZ says that on the basis of the EU Commission’s Stage V proposals, published on 25 September 2014, its diesel particulate filter (DPF)-equipped engines in the 2.9-7.8litre range already meet the limits envisaged for 2019. The definitive regulation is expected at the beginning of 2016.
In anticipation of the fourth emissions standard (EU Stage IV/US EPA Tier 4), introduced in 2014, DEUTZ had already redesigned substantial parts of its engine range from scratch and had implemented the latest exhaust after-treatment technology. In conjunction with a sealed DPF, these engines already conform to Stage V.
“We’ve struck some major deals with manufacturers,” said JCB Power Systems’ OEM engine sales and development manager Robert Payne. “Our OEM business is five times the size it was in 2009 and we saw 63% growth in OEM sales volumes from 2013 to 2014.”
As well as the compact SCR-only design, which allows manufacturers to maintain low engine canopies for improved operator visibility, he said that the firm’s frugal fuel consumption figures have proven increasingly popular, giving equipment firms an added sales point for their machinery.
Sister division JCB Drivetrain Systems is also reporting a big surge in demand, with regular sales to more than 115 OEMs.
The most recent additions to the firm’s line-up include a locking drive axle first seen on JCB’s Fastrac range and the 760
power-shift lock-up transmission, which offers lock-up in all gears for improved hill climbing and reduced fuel consumption.
FPT Industrial’s Cursor 16
Powertrain manufacturer
FPT, a brand of
The Cursor 16 is the company’s biggest solution for the world of construction and is compliant to Tier 4B/ Stage IV emissions standards thanks to the patented HI-eSCR system. It is the first FPT Industrial engine to adopt a Compact Graphite Iron (CGI) cylinder head, a high performance material providing high thermal and mechanical resistance, and the engine features a third generation common rail system of up to 2,200bar under cover.
The engine delivers power outputs of up to 570kW with maximum torque of 3,320Nm at 1,500rpm in its single stage version and up to 630kW with maximum torque of 3,500Nm at 1,400 rpm when available in its double stage version.
The Cursor 16 is specifically suitable for large construction and material handling equipment, such as wheeled loaders, excavators, cranes and dumpers.