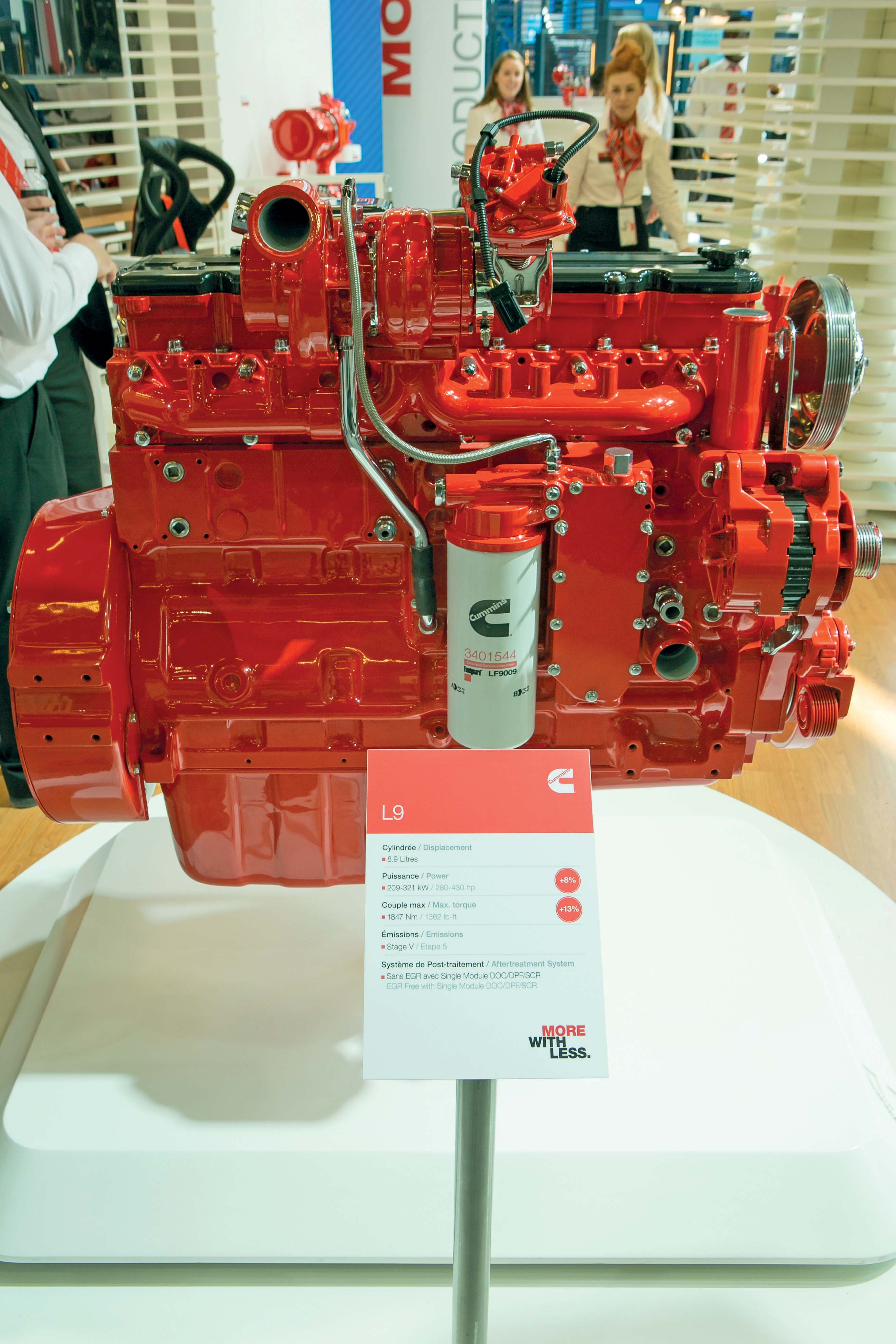
The race to be ready for the introduction of EU Stage V emissions regulations in 2019 is leading to eye-catching innovation among leading global off-highway OEMs. Geoff Ashcroft and Guy Woodford report.
As the clock ticks down on the EU Stage V emissions regulations coming into force, the global off-highway engine market is full of attention-grabbing vibrancy.
“The latest emissions-compliant specification has resulted in higher power and torque in a smaller, lighter overall package that has become cheaper to run,” said Eric Neal, executive director of Cummins’ off-highway business.
And, he added: “Cummins’ ability to tailor engine power and torque curves and make full use of our in-house equipment such as turbochargers and exhaust after-treatment packaging, is enabling OEMs to be more competitive.”
Top-rated power for the B6.7 has increased to 243kW, with a peak torque of 1375Nm representing an increase of 30% over that achieved at EU Stage IV levels. The larger L9 engine has increased from 291kW up to 321kW, together with a 13% increase in peak torque, to achieve 1846Nm.
“The higher capability of these engines is delivering down-sizing opportunities for our equipment manufacturers,” he said.
Meanwhile, meeting EU Stage V emissions requirements has resulted in Cummins’ development of a compact single module exhaust after-treatment package. Said to be 50% smaller and 30% lighter than those used for EU Stage IV systems, the single canister design has been made possible from the use of advanced catalyst technologies that deliver improved particulate matter and NOx reduction capabilities. In addition, the diesel particulate filter’s (DPF’s) passive regeneration minimises the need for preventative cleaning and maintenance, said Cummins.
Cummins has also revealed its first electrified off-highway powertrain concept, which can be used to create a range-extended electrified vehicle (REEV). It follows Cummins’ recent acquisitions of Brammo and Johnson Matthey Battery Systems.
“Cummins will be investing $300million over the next three years to continue organic and inorganic growth to develop a portfolio of alternative power units for the off-highway market including full electric vehicles, range-extended vehicles and plug-in hybrids,” said Julie Furber, executive director of Cummins’ electrified power business.
The REEV concept comprises a four-cylinder F3.8 Stage V-compliant diesel engine, a battery pack, power electronics and a high-efficiency traction motor. In principle, the battery pack provides an electrical power source for the traction motor to run a vehicle’s transmission, with battery energy replenished by the diesel engine.
Battery packs offer 35kWh of power and are modular, enabling packs to be linked according to the application.
“The REEV concept allows the battery packs to be charged as overnight, using a plug-in electricity supply, with the engine topping up as a generator during the working day,” said Furber. “A 35kWh battery pack should give two hours of 100% electric operation, and once the charge drops to 30%, the engine will automatically start and introduce a charge to keep the vehicle working.”
The REEV concept could easily replace a traditional power source that currently relies on a 9litre diesel engine, she concluded.
By optimising fuel systems and exhaust after-treatment packages, Perkins has increased the power density of its large engines as the firm heads closer to EU Stage V emissions compliance.
A key example is the firm’s 1706J-E93TA. Previously, this 9.3 litre six-cylinder was offering a power output of 300kW. As it moves towards EU Stage V certification, the power output has increased to 340kW.
“The Perkins EU Stage V engine range has more models from one manufacturer than any other, so the 9.3 litre is just the beginning,” says Oliver Lythgoe, Perkins product concept marketing manager. “The high power output of up to 340kW makes the 9.3 litre engine ideal for OEMs wanting to downsize from larger 10-13 litre engines.”
Perkins has made significant investment in its EU Stage V programme with the introduction of six new engine models to extend its power range with the 1700, 2200, 2400, 2600 and 2800 Series and the Syncro 2.8L and 3.6L. The British engine maker will have 14 different engine sizes from 0.5-18 litres and will provide tailored solutions for customers with power ratings from 6–470kW.
“Even after the emissions introduction, we will continue to release new models and add new features to our range,” said Lythgoe. “This gives our OEM customers a wide choice of power solutions that are adapted to their machines and their business models.”
Showcased at the Intermat 2018 Paris exhibition (23-28 April), Volvo Penta’s Stage V off-road engine range, including D5, D8, D11, D13 and D16, is said to have been created specifically for the rigorous requirements demanded by industries such as quarrying and mining, construction, forestry and agriculture, and lifting and hauling. A robust engine has been matched with an optimised exhaust after-treatment system (EATS), to provide a powerful complete unit that is designed to offer ease of installation, operation and maintenance.
“Our engineers have created a solution that will enable hassle-free operation and enhanced productivity with minimal servicing required,” says Johan Carlsson, chief technology officer at Volvo Penta.
“The different engines, from five to 16 litres, have been tested under many challenging conditions to ensure that they are robust, durable and ready for any job. As a complete package of engine and perfectly matched EATS, each solution offers a flexible installation – a ‘plug-and-play’ system that will make life easy for OEMs,” says Carlsson.
For each Stage V model, common rail fuel injection and a fixed geometry turbo contribute to excellent fuel efficiency. An air inlet throttle, together with uncooled exhaust gas recirculation (EGR) and the electrical exhaust pressure governor (EPG), enable the system to function without the need to inject fuel into the exhaust stream to raise the temperature. With this approach, the exhaust gas has an optimal temperature when it passes through the EATS.
The EATS includes: diesel oxidation catalyst (DOC); diesel particulate filter (DPF; for D5-D13 models); selective catalytic reduction (SCR); and ammonia slip catalyst (ASC). (The D16 model does not require a DPF.)
“The smart heat management of our engines saves fuel, thereby reducing the total cost of ownership for customers,” adds Carlsson. “The engines and EATS work together to maximise passive regeneration and eliminate stand-still regeneration. Sulfur regeneration in the SCR catalyst isn’t required, and only soot regeneration is needed to clean the DPF. Overall, prolonged ash service intervals naturally maximise uptime for operators.”
Caterpillar says it is currently developing productive, fuel-efficient, power-dense, EU Stage V-compliant engines across its industrial product line, from the two-cylinder C0.5, to the 12-cylinder, 32-litre C32. Goals for Cat Stage V engines include developing more efficient after-treatment systems, simplifying installation in OEM-customer machines, and providing added value for end users of OEM machines—through increased productivity, increased fuel efficiency, and exceptional reliability.
The Cat C9.3B engine, for example, has been awarded EU Stage V emissions certification and is now in production.
“The C9.3B’s certification is an exciting milestone for Caterpillar,” says Jeff Moore, product director, research and development for 7.2- to 18-litre engines, “and we’re confident that this engine will meet customer expectations for reliability and durability in a simpler, lighter package with more power and torque. Caterpillar has proven the merits of the C9.3B by testing the engine to its limits, both in the lab environment and in actual customer applications.”
The six-cylinder, 9.3-litre C9.3B engine builds on the core engine that has been in production since 2011, logging more than 200 million hours in real-world, off-highway operation. With a proven, reliable core engine, coupled with extensive diesel particulate filter experience, Caterpillar has focused EU Stage V engine development on simplifying design, improving performance, and reducing installation complexity.
The C9.3B combines a new high-pressure, common rail fuel system with simplified systems for air, electrical, and after-treatment to produce up to 340kW of power and 2088Nm of torque, said to result in 18% more power, 21% more torque, and 12% less weight, compared with its predecessor.
“End users will see this refinement pay off with increased performance, up to 3% less fuel consumption and exceptional starting capability in cold climates,” says Moore.
“Patented after-treatment technology provides a compact, lightweight design that is 39% smaller and 55% lighter than the EU Stage IV/Tier 4 Final configuration, and the new design provides transparent regeneration to ensure optimum machine performance and uptime.”
As with all Cat 9-18-litre engines, the C9.3B is available in various configurations, including those with factory-installed, engine-mounted after-treatment systems and radiators. In total, more than 2,000 unique configurations are available for the C9.3B.
“We understand that not all customers have the resources to design, manufacture and validate on the same scale,” says Moore. “For that reason, Caterpillar designs its products with the flexibility to accommodate various OEM requirements, resulting in lower installation costs.”
In addition to the C9.3B, the Cat large engine, EU Stage V line-up also includes the 12.5-litre C13B, incorporating similar technology to that of the C9.3B and with power ratings to 430kW.
Caterpillar is also certifying its existing C13, C15, and C18 EU Stage IV/U.S. EPA Tier 4 Final engines to meet EU Stage V emission standards. Stage V certification for these engines will be achieved, says Caterpillar, with no changes to customer interface points and with only minimal changes to the DPF, allowing customers to focus on overall improvement of their products. Cat engines and DPF solutions in this range have nearly 170 million hours of proven field performance.
Caterpillar began accepting EU Stage V orders for C13-C18 engines in May 2018 and plans to ship production engines in October. The C13B will be available in 2019.
Dual-label certification—EU Stage V/U.S. EPA Tier 4 Final (and Japan 2014/Korea Tier 4 Final)—will be offered for the C9.3B and all other Cat products in the 250-597kW power range. Caterpillar says that this flexibility allows customers to develop commonality in products, parts, and service across various regions. With products for lesser regulated countries that have similar performance and share common core engine components, machine interfaces, and control architecture, the Cat product range is suited for a global customer base, supported by the Cat dealer network.