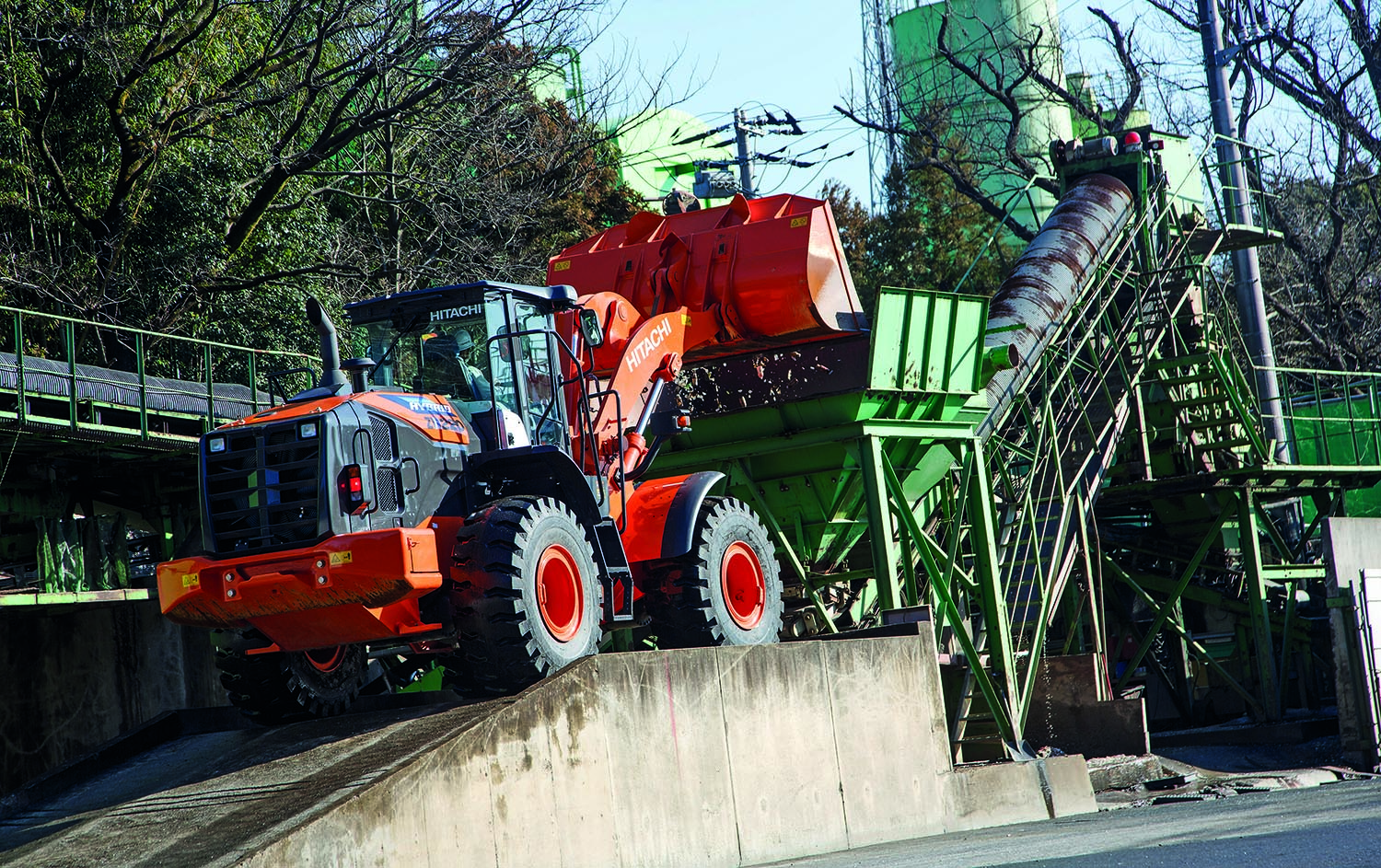
As fuel prices yo-yo, quarry operators and contractors, and therefore manufacturers, are constantly looking at ways of making machines even more efficient. Patrick Smith reports.
Construction machines of today have improved greatly from 10-20 years ago as tough emissions regulations have brought about major engine developments that in turn have seen research and development focussing, among other things, on improving fuel efficiency.
All the major manufacturers are now seeing their machines doing more work with less fuel, and are also developing hybrid and dual fuel equipment that it is claimed can offer even more savings.
“Even though magazines are full of articles talking about multiple propulsion systems as if they were the latest invention, they most plainly are not: the idea is as old as the engine itself,” says
“For a combination of reasons, the major nations of the world are now keen to develop new types of engines and work on adjustments to new fuels. The oil/combustion engine partnership has been dominant for over 100 years but its critics are getting louder. The fact that the supply of oil will eventually run out, that it is increasingly expensive and that demand for oil is projected to soon exceed supply are all helping to bring the date when the world is no longer dependent on the ‘black stuff’ nearer.
“There are also concerns about burnt oil-based fuels’ CO2 emissions contributing to global warming and their impact on health. These diverse factors have now come into alignment, creating a situation whereby manufacturers are keen to develop vehicles, including construction equipment that use less fuel and are more efficient and cleaner in their emissions.” Volvo Group says it, like other companies, is investing heavily in research on alternative power sources and alternative fuels, as well as in the constant refining of existing combustion technology. The work Volvo is doing on its diesel-electric hybrid called for a decision on how the two engines should work together: series or parallel.
Volvo says it has focused much of its research efforts on parallel systems, which connect both the electric motor and the diesel engine to the mechanical transmission, so that they work together to operate the vehicle. The company says a key component is the I-SAM (or Integrated Starter, Alternator Motor), which is basically a powerful starter motor with enough strength to propel even heavy construction vehicles from stand-still up to a good speed for the diesel engine to take over.
“The biggest fuel savings from diesel-electric hybrids in the construction industry are likely to come from those machines where there are frequent starts and stops. This is because the diesel engine will be dormant for much of the time. Machines such as wheeled loaders will see big fuel savings. But all construction machinery should see benefits from this technology,” says Volvo.
Meanwhile, Bullet Train (Shinkansen) technology was used in one of the highlights of the
The new ZW220HYB-5 hybrid, designed and constructed at HCM’s wheeled loader factory at Ryugasaki, Japan, is part of HCM’s quest to manufacture an eco-friendly product that will use significantly less fuel than it did in 2010. This is in response to the world’s focus on protecting the environment and as a result of increasingly strict emission regulations.
The ZW220HYB-5, initially being introduced in Japan, incorporates 100% proven Hitachi group technology from the Shinkansen and EH-series dump trucks, specially developed for the hybrid wheeled loader.
The ZW220HYB-5’s four-cylinder engine powers a generator, which produces energy to drive two electric travel motors. When the machine is rolling or braking, it continues to store electricity in a capacitor. Under acceleration, it uses energy by the generator and the capacitor, and so less revs are required when it reaches normal travel speed.
The control units are the key to the electrical power process and engine operation. For example, when lifting and loading automatically the engine rpms increase in regards of the load, and there is no need to use the accelerator pedal.
HCM says there are four main benefits of the hybrid system: reduced fuel consumption; enhanced reliability and safety; less noise; and easy operation. It is claimed that the ZW220HYB-5’s hybrid system will improve fuel efficiency by up to 26% compared to the previous conventional ZW220 wheeled loader.
The lifetime cost of the hybrid wheeled loader is also reduced, requiring less maintenance for the generator, travel motors and service brakes. Safety has been enhanced by the auto-braking system that enables the machine to travel downhill at a constant speed.
The loader has been tested extensively by HCM’s customers at quarrying and waste handling sites in Japan, and the feedback has been “extremely positive.”
The new hybrid is said to deliver estimated fuel savings of up to 20% (compared with standard 336F L/LN) and up to 25% (compared to the previous standard 336E L/LN) with no compromise in performance nor added maintenance costs.
Rated at 235kW and designed to operate efficiently on bio-diesel blends up to B20, the engine uses a diesel particulate filter (DPF) along with an exhaust after-treatment that does not interrupt work cycles or require operator intervention.
“The key to the hybrid’s efficient performance is the Cat Swing Energy Recovery (SER) valve, which captures kinetic energy during swing deceleration by storing normally wasted hydraulic flow from the swing motor in high-pressure accumulators, then releasing this stored energy to assist swing acceleration. The result is reduced load on the hydraulic pumps and a subsequent, significant reduction in fuel consumption,” says the company.
“Ample hydraulic flow in the 336F L/LN XE’s implement circuits and a high main relief pressure generate the power to handle a range of buckets and work tools, including shears, multiprocessors, hydraulic breakers, and rippers.”
The HB215LC-2 sees the company’s components harness free kinetic energy through the machine’s swing and braking and convert it to electricity, allowing significant fuel savings to be achieved, along with lowering an excavator’s carbon footprint.
Keiko Fujiwara, chief executive officer of Komatsu Europe International, said that the 22-23tonne operating weight HB215LC-2 had delivered a 5% reduction in fuel consumption compared to its predecessor, the HB215LC-1; a 30% cut in fuel consumption compared to Komatsu’s PC210LC-8 hydraulic excavator, and a 20% fuel consumption saving compared to the PC210LC-10 hydraulic excavator.
Dual powered equipment is finding favour among crushing/ screening operators, with recent launches including dual powered variants of Terex Finlay’s J-1175 jaw crusher and C-1540 cone crusher, which have joined the
“The dual powered crushers are electrically driven allowing users to run from electrical supply with the aim of giving significant savings on energy costs. These machines are also fitted with an onboard genset allowing the operator to move and use the machine where there is no electric supply, giving the flexibility and versatility of current standard models.
“In applications where a full train is powered by the onboard genset configuration the crushers generate sufficient energy to enable the operator to run the Terex Finlay 694+ dual power inclined screen for free when used in conjunction with the J-1175 dual power jaw crusher. “Either power option presents operators with significant power, servicing and maintenance cost savings in direct comparison to a diesel/hydraulic powered plant.”
The C-1540 also offers operators the flexibility to power the plant either by mains electric connection or the onboard genset power pack configuration.
Dual power screens are fitted with an electric/hydraulic drive system that can be connected to an external electricity supply once the machine has been set-up on site, and applications include situations where only electricity is permitted, for example underground; where electricity is freely available, generated on site or cheaper than diesel; where complete crushing spreads are run using a stationary genset, and where environmental, legislative and/or noise constraints are present.