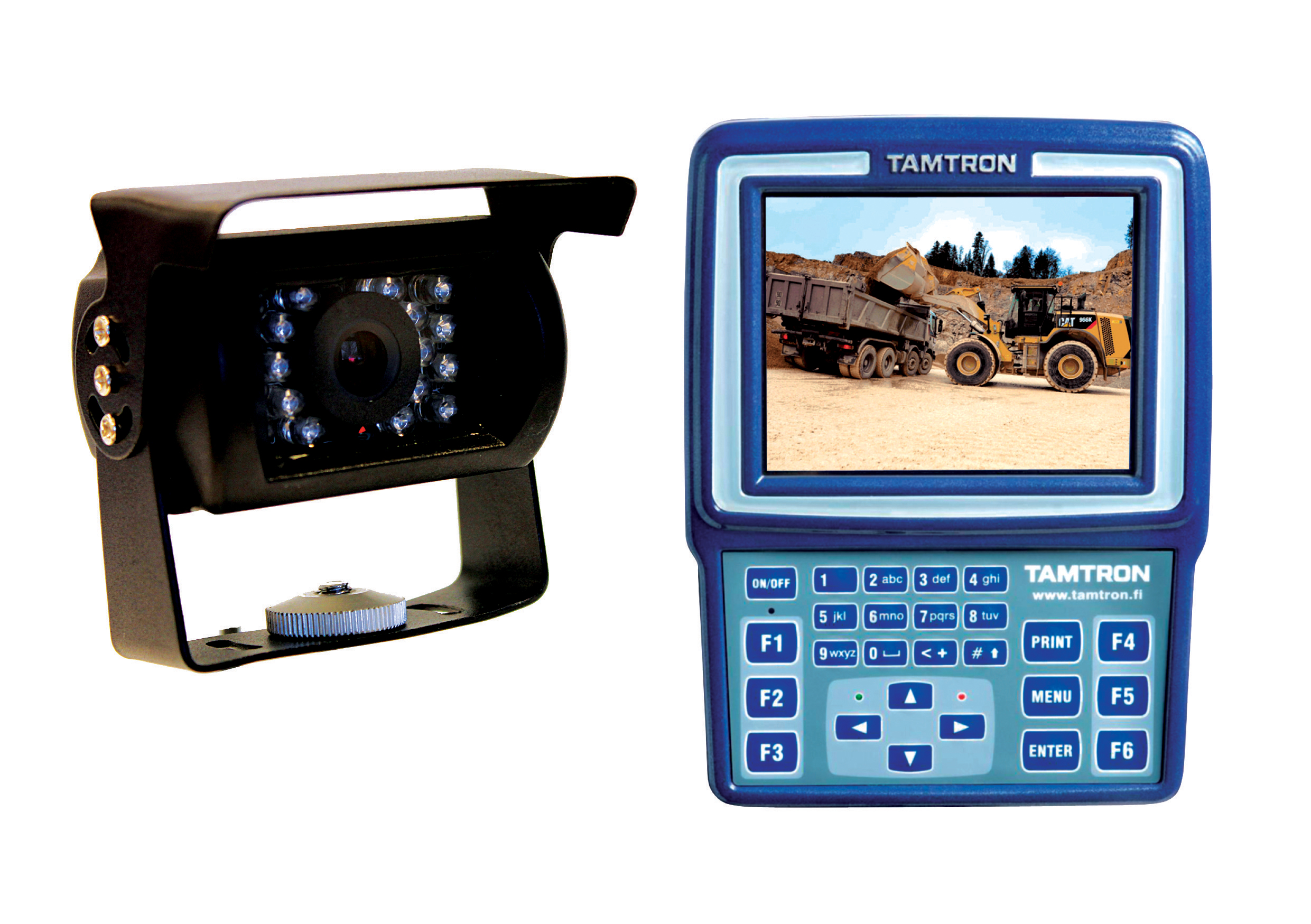
Most quarries use static or dynamic weighing systems to manage the quality of the products they produce. These are used to measure the quantity of material or finished products such as aggregates that are delivered to customers.
Established equipment is regularly joined by new state-of-the-art products that make the weighing job easier, quicker and more effective.
For example, Finnish company
The company, which says it is as easy to use as a smart phone, claims the new Power is the first full-colour touchscreen in a wheeled loader scale.
“The Power scale has over ten key features other scale brands do not have,” says Tamtron, which has some 40 years of experience and expertise in scale manufacture, the Tamtron Power scale being protected with international patents and trademarks.
Tamtron says the scale offers three weighing modes in one scale: a standard scale for basic weighing; memo weighing for professional users, and stock control weighing.
It also says that weighing can be carried out while lowering the boom.
“Repetitive, time-wasting last bucket weighing is a thing of the past: no more weigh and subtract lifts,” says Tamtron.
“Zeroing is only once an hour, not after every load or during loading. Zeroing with an empty bucket unnecessarily wastes time and resources.”
Tamtron’s Power scale is said to offer a loading speed of over 500tonnes/hour because of the touchscreen, certified weighing downwards and the long time between zeroings.
“It is legal for trade in the temperature range from -25°C to +40°C temperatures, and the automatic tilt error compensation guarantees fast and accurate weighing even on uneven loading ground.”
Online automation means that weighing data transfers easily to invoicing and integrates into ERP (enterprise resource planning) systems with the 300i scale and the WNexus server services.
Tamtron’s optional GPS locationing maximises stock control, while worksite safety improvements include options such as automatic rear-view camera integrated in the scale display and immobiliser to prevent unauthorised use of the loader.
Volvo Construction Equipment’s award-winning On Board Weighing (OBW) system is being offered on
“Fully automatic OBW logs all transported loads and the ensuing data is then shown on the operator’s display. The information can also be accessed remotely, thanks to Volvo’s advanced CareTrack telematics system,” says Volvo CE.
“This allows complete payload management, giving access to data such as total transported load in tonnes; tonnes transported per litre of fuel, and number of cycles.”
OBW-equipped haulers are fitted with a load indicator light, mounted outside the machine and clearly visible to the operator of the wheeled loader or excavator that is loading the hauler (a yellow light comes on when at part load, which changes to a green light at nominal load, finally turning red when overloaded).
“This simple tool helps prevent overloading and the machine wear, tyre damage and excess fuel consumption that go with it. The nominal load can be preset to suit material and site requirements,” says Volvo CE.
According to the company, the OBW system also offers the ability to unlock a wealth of previously inaccessible information, such as the weight of carry-back left in the haul body after tipping.
“OBW helps show the true productivity of the machine, combining fuel efficiency with tonnes of mass moved. Additionally, it can help in improving operator performance.
“By measuring number of cycles, total of mass moved and load efficiency, site managers can compare and improve the productivity of its operators. The system also provides easy-to-understand daily, weekly or monthly productivity reports, which can be invaluable for site managers in assessing whether performance matches job-specific targets or assisting in calculations for the next project.”
Weighing is also a major element of a system from Italian company Ma-estro, which has been developed for the control of material and machinery movements on large road building sites and in quarries.
The Transport Q-control solution relies on the innovative technologies and systems available on the market today.
“Ma-estro has identified and developed reliable solutions that take account of the specific operational difficulties: building sites with constant movement, shift work, frequent renewal of personnel, difficult environmental conditions, geographical distances between the various sites and the use of many languages,” says the company.
While the system has been specially developed for quarries, it has been tested on building sites where the main problem has been tracing all the movements of equipment and materials entering and leaving the site, and doing this automatically, safely and accurately.
“A control system entrusted to a number of persons in continuous rotation, where external personnel pay little attention to procedures and where management is spread over a number of distant sites, considerably complicates the speedy recovery and registration of accurate information on materials bought and sold, as well as the corresponding accounting,” says Ma-estro.
“Constant monitoring, with the ability to visualise anywhere and at any time both stocks and inventory documentation, simplifies building site organisation by removing the unwelcome risk of creating emergency situations or excess production.
“In operation management and organisation, the project manager must make sure that the resources requested and/or divided between the various activities are adequate; problems that can arise here are those due to waiting to use resources during construction work. When a queue forms, there will be operations that must wait, with time lost, delays and the corresponding costs.”
Remote operation via the internet allows immediate control and optimum management, reducing lost time due to faulty communication or organisation.
“In order to be available to personnel of various nationalities and languages, the system had to be extremely simple in use and, at the same time, reliable, accurate and precise,” says Ma-estro. After analysis of these and other aspects, Ma-estro proposed the Transport Q-control system. The company says it can recognise vehicles automatically, allowing management and tracing of materials entering and leaving sites, and determine the exact quantities loaded and unloaded and the real empty weight of the vehicles.
“The system also informs the operator as to the loading/unloading site and the type of material, limiting human error and hence offering considerable time savings as well as an increase in site productivity and efficiency.
“The Transport Q-control system allows in-depth customisation to satisfy the needs of the end user without being invasive, with data that can be exported to any accounting software for invoicing and with the possible automatic emission of shipping documents.”
In some cases, special video cameras have been supplied allowing automatic recognition of vehicles in transit, and following integration with site weighbridges, the system can acquire a variety of information.
This includes vehicle registration number and owner data; date and time of entry and exit; empty and loaded weights of the vehicle; photograph of the material loaded/unloaded; photograph of the vehicle; destination and final customer data; destination distance for the material, and type of material.
“Thanks to the information acquired autonomously by the system, the shipping document can be printed automatically, avoiding any personnel errors and also accelerating accounting operations when invoicing,” says Ma-estro.
Meanwhile,
“The L2150 provides certainty that trucks will be loaded to the optimal weight, first time,” says the company, which also highlights its X2350 excavator scales designed specifically for bucket excavators and its conveyor scales.
Among RDS Technology’s latest offerings is the Loadmaster a100 onboard weighing system, an all-new CAN-based system combining cutting-edge sensor technology and signal processing techniques providing precise and consistent weight information.
“With the ever increasing focus on productivity, Loadmaster a100 has been designed to operate within the fastest loading environments and toughest of conditions compensating for uneven, sloping ground and restricted loading areas reducing cycle times and maximising tonnes per hour performance,” says
“Loading correctly first time eradicates return trips to the stockpile reducing vehicle movement, fuel usage and machine and tyre wear.”
The new system is said to be suitable for use with up to ten different attachments including buckets or forks, and it can be retrofitted onto wheeled, telescopic and tractor type loaders.
By continually measuring hydraulic pressure using up to four sensors, the pressure signals are captured and filtered through a weighing ‘arc’ provided by inclination sensors measuring the angle of the main boom. An additional sensor compensates for oil temperature.
“All signals are processed in the RDS Smart Box and the resultant weight calculation is sent to the terminal mounted in the cabin,” says RDS Technology, whose products were supplied recently to Kelston Sparkes, the long established plant hire and sales based in Stanton Drew near the city of Bristol, south-west England.
Two Loadmaster 8000iX systems are fitted onto Volvo L110G wheeled loaders that will join a fleet of 20 loaders and be put to work within the crushing and screening division deployed on a wide variety of sites including one of the company’s specialist areas, serving the south- west quarrying industry particularly in the Mendip Hills.
The recently launched 8000iX model is said to benefit from additional standard features. These include temperature compensation which enhances system performance, particularly on loaders with a wide variation in operating temperature and angle compensation, providing an additional level of precision beneficial on most sites and not only those with obvious slopes.
The Loadmaster 8000iX has an integral SD card port for the transfer of data between loader and weighbridge or office PC, and it enables pre-registered customer reference data to be uploaded directly to the instrument.
“Loadmaster is an integral part of the ‘load out’ process. Trucks are accurately loaded at the face eliminating return trips from the weighbridge and therefore maximising productivity,” says Alan Sparkes, Kelston Sparkes’ managing director said.
Vishay Precision Group’s VPG onboard weighing product group has partnered with VUE, a supplier of vehicle CCTV, tracking and telematics solutions, to enhance its 1300 BulkWeigh and 1300 WasteWeigh systems.
The new PM 1300 360-VUE systems is said to offer enhanced health and safety and security features through new video data recording capabilities and support for up to eight cameras, including near side, far side, front, rear, and load.
The BulkWeigh and WasteWeigh onboard weighing systems that use the new PM 1300 360-VUE indicator can come equipped with three cameras and provide support for an additional five cameras to provide drivers with a 360º view.
For increased safety, when the vehicle slows below 15mph (24km/hour) and the left turn indicator is on, the systems will automatically default to the near-side camera. This gives the driver a clear view of the blind spot, helping to avoid accidents with pedestrians and cyclists when turning left.
The reverse camera also features new technology that corrects the fish eye effect, providing drivers with a clear, undistorted rear view.
Offering a 500GB hard drive and recorder, the new PM 1300 360-VUE systems record vehicle speeds, G-forces, and the use of brakes and indicators for insurance purposes.
Providing fully controlled loading and unloading recording, the systems record GPS position, date/time, vehicle load weight, and video of the load platform for any planned load or unload, which can be included on digital photographs and stills. This same information is also recorded any time the vehicle load changes by half a ton, ensuring that no unauthorised unloading of goods occurs.
The systems record load weights as text over video, and can store 30 days of data.
The new PM 1300 360-VUE BulkWeigh and WasteWeigh systems are available now, and the enhanced features are also available as an upgrade to PM’s existing 1300 systems.RSS