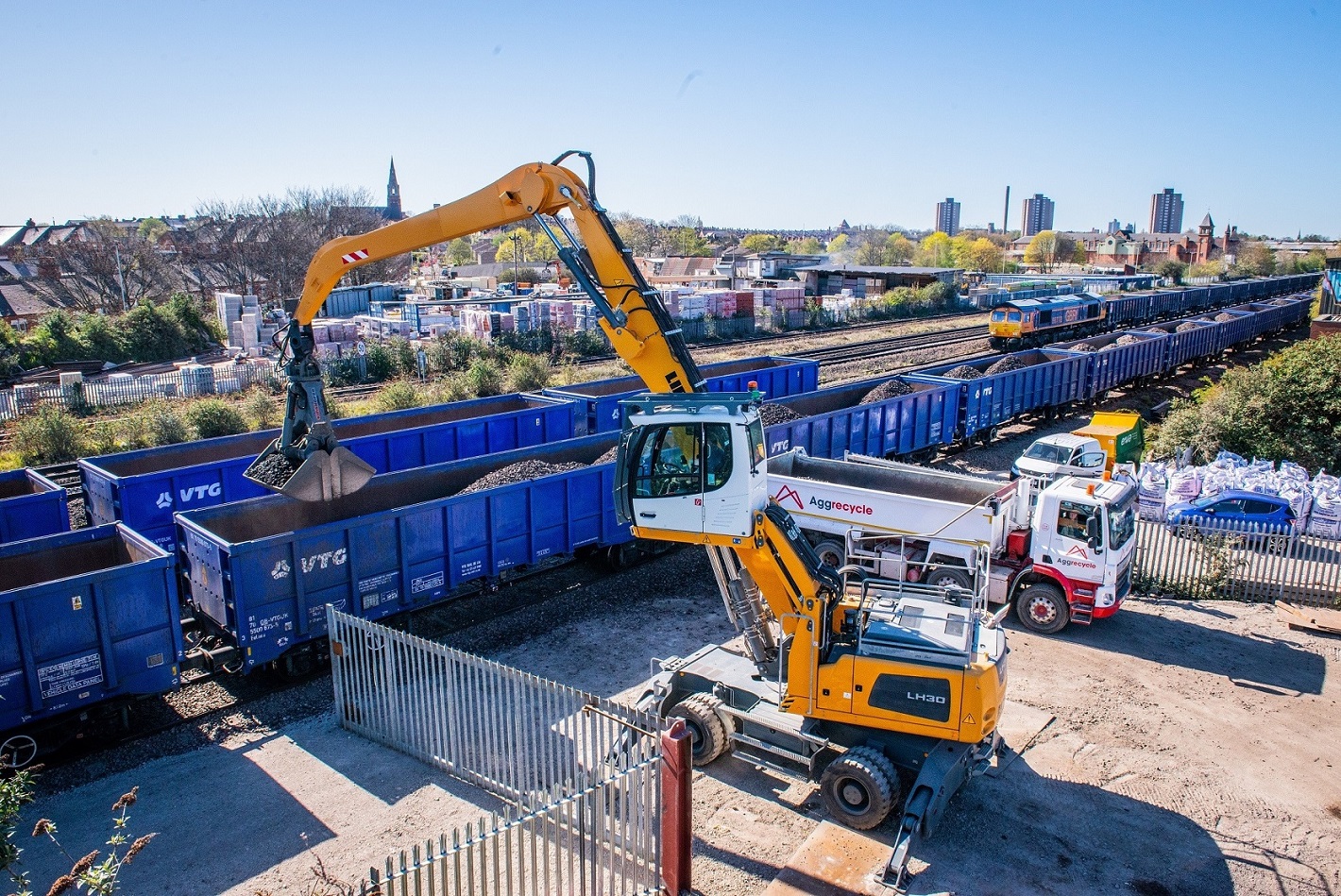
The company will work with private rail operator DC Rail to freight thousands of tonnes of spent aggregates each year to its recycling site on Syston St East in the city centre.
With each rail delivery bringing the equivalent of 81 lorry loads of material, the move will result in significant emissions savings as well as enhancing productivity at the quarry. The company's directors hope to see turnover at Aggrecycle rising by up to 60 per cent thanks to the new arrangement.
Darren Thompson, site manager at Aggrecycle, expects the site to become a hub for collecting aggregates arising from demolition projects – waste such as brick, concrete and asphalt – with deliveries arriving from all over the UK and then being used on construction sites around Leicester.
Initially, the rail service will use existing infrastructure adjacent to the Aggrecycle site. Subject to the project's success, Thompson said new rail infrastructure could be installed on-site within the next 12 to 18 months.
"This is a development which has been eight years in the making," he said, "and now that infrastructure projects are proceeding at pace around the UK, the time is right for us to make this new arrangement with DC Rail.
"We are one of the very few urban recycling quarries in the country which has a rail feed, so it's an exciting move. The Government is keen for more transport to be done by rail, rather than road, so we're excellently placed to benefit.
"Leicester is positioned at the heart of the country so we can take deliveries from anywhere and send our high quality recycled product back out to any location, particularly locally. The cost savings and reduction in carbon footprint are significant, so we'd certainly encourage construction companies to consider the benefits that the use of recycled aggregates can bring."
In 2019, Aggrecycle announced continued investment in the future of its business with £800,000 of cutting-edge machinery – two pieces of kit from German manufacturer Kleemann: an MR 110 Z EVO 2 impact crusher and an MS 953 EVO screening plant.
Energy and fuel-efficient, the new plant has improved site productivity and continues to enhance Aggrecycle's economy and safety performance.
Thompson's brother, Andrew, who co-founded the business in 2010, said he was keen to further develop a business with sustainability at the forefront, not only in terms of plant performance but also to promote a genuinely circular economy in the local construction industry.
"We believe a relatively small contractor can become a beacon of operational and environmental standards," he said. "We understand we have a valuable role to play in providing recycled materials to fulfil the demand for aggregates as the UK looks to invest in developing its infrastructure and housing stock.
"That's why we're keen to develop relationships with a variety of local businesses – large and small – to provide aggregates which have a minimal environmental impact and can help serve the community in which we're based.
"Our mission is to effectively eliminate, reuse, reduce and recycle all possible elements of construction, utility, and demolition arisings."