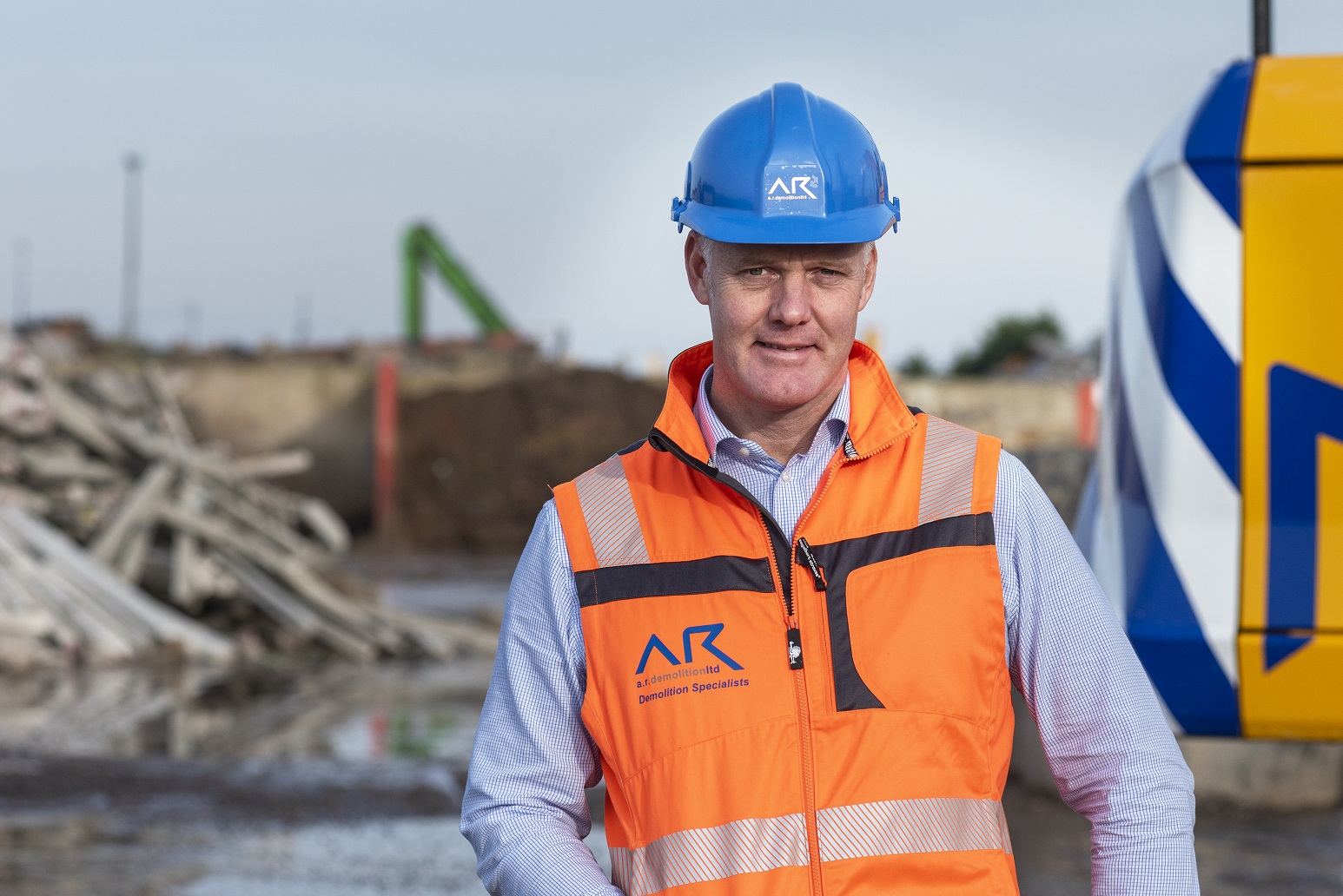
What is the importance of recycled aggregates for major infrastructure projects such as the HS2 rail initiative?
For the Birmingham HS2 alone, the target for recycling is over 90% wherever possible, according to the HS2 in Birmingham website.
The construction and demolition industry create huge amounts of waste materials that need to be recycled and reused as recycled aggregates (RAs) for partial or total replacement of natural aggregate products. This aggregate recycling approach, as demonstrated at AR Aggregates, reduces waste and reduces energy consumption and helps to ensure a more sustainable approach to deconstruction. This in turn cascades down to our clients in the wider construction/infrastructure industry.
Benefits include reduction in the extraction and use of natural products; substantially reduced transport movements reducing carbon emissions and cost; and promoting Cradle to Cradle techniques, extending the life of the building and embracing the circular economy.
The definition of the Circular Economy (CE) is described by the Waste and Resources Action Programme (WRAP, 2018) ‘an alternative to a traditional linear economy (make, use, dispose) in which we keep resources in use for as long as possible, extract the maximum value from them whilst in use, then recover and regenerate products and materials at the end of each service life.’
Design for deconstruction is the ideal going forward into the future.
The demolition industry is viewed as the built environment’s dustbin men – it is important to realise the value of waste and how it can be streamed, segregated and reused. In the demolition industry waste reuse, recycling and up-cycling is common practice. Aggregate arisings such as brick, concrete etc. are segregated, crushed and graded for reuse. Reprocessed aggregates arising have a variety of uses they can be used on site, such as: a sub-base for buildings; roads; and backfill for voids. If not needed on the demolition site, aggregates arising can be taken to a repossessing facility for recycling and sold back out into the construction or civil engineering community for other construction or infrastructure projects. Likewise, metals, glass, wood and vegetation can all be segregated, streamed and recycled.
Most demolition projects can recycle over 90% of waste arisings as currently most buildings demolished are old and old building techniques and materials were used for construction such as bricks, concrete, wood, tiles and glass.
In 2018 AR Aggregates sister company AR Demolition recycled 93.98% of all demolition waste arisings, 179,706.82 tonnes of which was aggregate arisings and reused on construction, infrastructure and civil engineering projects.
Recycling and repurposing of materials has never been higher on the social and political agenda. In the current climate it is essential that all industries look at how they can make a real impact in the area of recycling and reducing their carbon emissions.
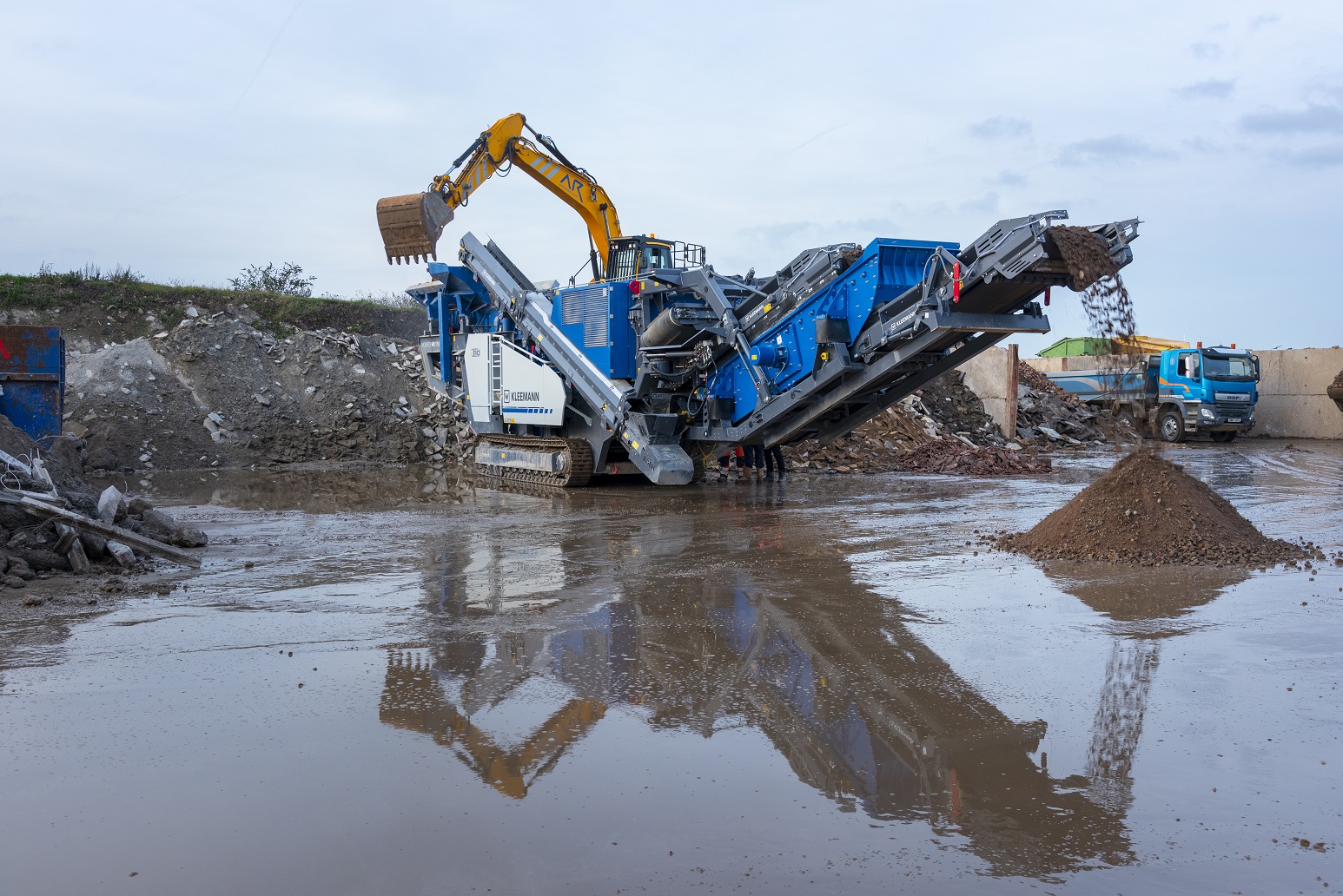
How will AR Aggregates newly-acquired Kleemann MR 110 Z EVO 2 impact crusher and Kleemann MS 953 EVO screening plant help with the recycling issue?
The new Kleemann MR 110 2 impact crusher has evolved to include additional benefits in terms of economy and operational safety. It is universally adaptable and suited to processing natural stone, asphalt and demolition waste. Although it is a relatively small crusher and can be easily transported to site, it can achieve outputs that up to now have only been achievable with larger crushing plants.
Compared with the old jaw crushers they are 30% more efficient, with maximum input capacities of 120 – 180 t/h easily attained. For classified end product, the plant can be fitted with the high-performance secondary screening unit. The new crusher Averages 18 litres per hour on fuel, approx. saving of 15% over the old machines. The safety features include emergency stop facility; remote control; and guard rails and safety walk around stair balcony.
The Kleemann MS 953 EVO screening plant has excellent transport properties, quick setup times and is efficient operationally. It has performance values of screening up to 500 t/h and will screen both recycled and natural stone. The metering flap installed at the outfeed end of the hopper ensures a continuous of flow of materials this will impact on the efficiency of the recycling process.
Products produced include Type 1 (Recycled), Utility Mix, Hybrid Utility Mix, 20mm Ballast, 40mm Down (Recycled), Type 1 (Recycled Asphalt), 6F5 (Recycled), Fill Sand (Recycled), 10mm Clean (Recycled), 20mm Clean (Recycled), 50mm Clean (Recycled), and 75-40mm (Recycled 6C).
What is the latest data on trends in the use of recycled aggregates in construction, and their importance in this area?
As reported Mineral Products (Products, 2019): ‘In 2017, a total of 176 million tonnes of primary aggregates were produced by the industry in Great Britain, which, together with an estimated 72 million tonnes from recycled and secondary sources, supplied demand. Recycled and secondary materials accounted for 29% of the total aggregates supply, which has put Great Britain in a leading position internationally in the use of recycled and secondary aggregates for many years, well ahead of the European average.
What sustainability initiatives are AR Aggregates and AR Demolition undertaking?
We have made a significant investment in the latest technology for controlling the environmental impacts at our aggregate recycling yard and demolition projects. From managing dust generation to maximising the recycling potential of our clients’ waste materials, we offer a state-of-the-art range of equipment and techniques which manage and monitor on-site environmental aspects.
The environmental management strategy of AR Aggregates Ltd and AR Demolition Ltd sets out our approach to waste management. Its focus is to assure that no arisings from any project are sent to landfill. Through our robust environmental processes for pre-planning and on-site control, including site waste management plans, we can effectively eliminate, reuse, reduce and recycle all possible elements of construction, utility, and demolition arisings.
What are the major sustainability issues and environmental regulations that will impact construction/quarrying equipment and the AR Aggregates business in future?
The Environment Agency’s work on guidance for LCRM (Land Contamination Risk Management) is now nearing completion. A six month consultation will be held and the policy will and procedures will replace the archived CLR11. It’s a significant step forward and will ensure the highest level of competency while making sustainability an integral part of the process.
A conclusion of research by WRAP (WRAP, 2019) says it ‘would require the resources of nearly three earth-sized planets for future populations to consume at the rate we currently do in Europe.’ The construction industry has to change the way it in which waste is recycled, repurposed and reused.
Waste and recycling facilities are regulated and the use of crushing and screening equipment subject daily, weekly and annual maintenance checks with certificates of thorough examinations in place available at all times for inspection. All operators should be suitably qualified to CPCS level requirements.
All crushing and screening operations must comply with the relevant environmental permitting and waste management legislation.
All operations must be undertaken in full compliance with the site including due care and attention made to requirements such as noise and dust generation. Management staff are Waste Management Industry Training & Advisory Board trained (WAMITAB).