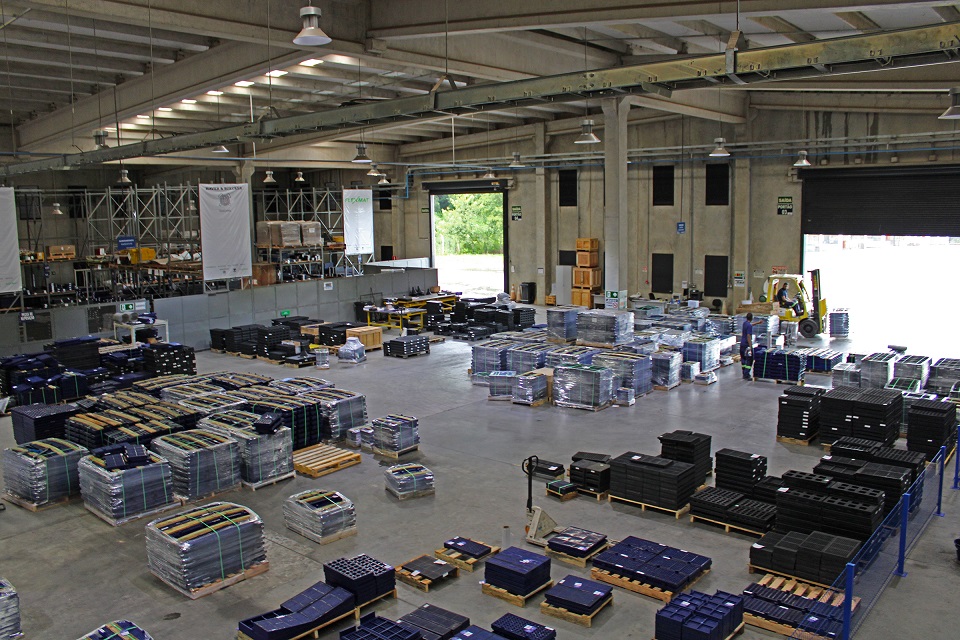
The screen media company says the building expansion allows it to produce 8,000 parts per month at a rate of 320 parts per day. It adds that it can now also move its rubber production 100% in-house, allowing for an increased production capacity of its signature Ty-Dura screen media and premium rubber liners by 60% while offering unrivaled quality control.
“As Haver & Boecker Niagara’s global presence has grown, so has an interest in our innovative mineral processing products. It’s an exciting position to be in,” said Laís Andrade, sales manager at Haver & Boecker Niagara. “Part of the decision to expand our Pedro Leopoldo facility was the need to move our rubber production in-house to best meet our customers’ requirements. In addition, it allowed us to expand our R&D laboratory and testing center. The expansion helps us to better support mineral processing operations worldwide.”
The 48,438-square-foot (4,500 square-meter) facility allows the Haver & Boecker Niagara team to increase their screen media and parts production capacity by 15%. Additionally, the facility’s laboratory tests samples of the company’s rubber and polyurethane materials, which it says offers unprecedented quality control for their materials. The laboratory’s services range from abrasion and hardness testing to stretch, tear, cut testing and more.
“By bringing our rubber production 100% in-house, we are able to significantly increase the product quality,” said Luís Henrique Bastos, production coordinator at Haver & Boecker Niagara’s Brazilian facility. “Our mineral processing specialists recognize that there isn’t a one-size-fits-all solution when it comes to screen media selection. That is why we work closely with each customer to understand their operation’s requirements and conduct thorough testing and analysis in our R&D center to ensure proper selection. This attention to detail helps increase our customer’s productivity and production.”
The updated manufacturing facility also features a range of efficiency- and safety-enhancing manufacturing equipment. One such update is the sandblasting cabin, which aids in tool cleaning. The cabin offers a 40% cut in equipment cleaning costs and substantially decreases cleaning times from 24 hours to 15 minutes.
Another equipment adjustment is the sandblasting machine for metal frames. The machine decreases manufacturing costs by 79% while reducing production time by two days. The facility is also equipped with an upgraded paint shop which cuts processing times by 75% and features a powerful exhaust system to support the health and safety of Haver & Boecker Niagara technicians.