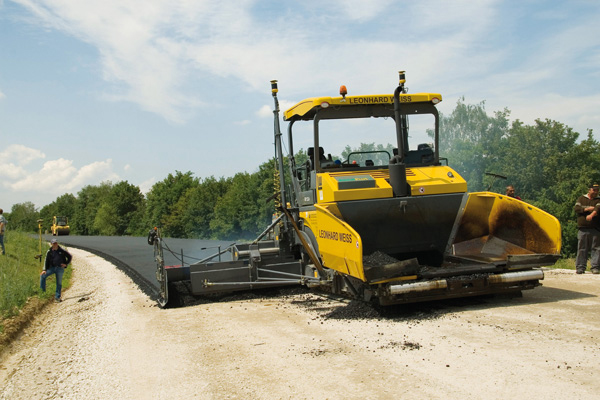
Developments in asphalt mix design are now being matched by hi-tech innovations in paving technology. ABE takes a look at one of these in action on site in Germany
Advances in asphalt mix design have helped to create road surfacing around Europe that reduce spray in heavy rain, create less noise and offer better skid resistance. All these attributes have been achieved by careful laboratory analysis to revise the aggregates used, the material size and shape and high performance bitumen binders.
However, despite this innovative asphalt mix design, the smoothness of the finished surface has always depended on the equipment and processes used on site. But paving technology has also advanced and means that even smaller surfacing contracts can benefit from improved surface smoothness.
One road that has just received the advanced treatment is the L546 near Heidelberg in Germany, which was surfaced using a
The new 1.2km €3.5million link was built by main contractor Leonhard Weiss to take the heavy traffic away from the village of St Leon-Rot, which is home to 12,000 people. Construction of the new road will also provide better connections to the Im Schiff industrial area and remove trucks from passing by a nearby high school. The road construction on the L546 is the last phase of work to improve traffic flow around the village, which lies close to both the A5 and A6 motorways.
But despite the short length of the new road, the project involved surfacing several tight curves and managing several changes in transverse profile.
According to the contractor's site team, the full automation of the paver eased the work on site by allowing them to stand back and monitor the work as it progressed and concentrate on coordination of the delivery of asphalt to the paver.
The design data for the by-pass, which included several 400m radius bends and transverse slopes of up to 8%, was available from the client in digital form. This allowed the data to be imported straight into Vogele 3D system. As a result, there was no need to carry out time consuming surveying and preparation of the job site as would be necessary for grade and slope control with tensioned wires.
According to Vogele, the paving team opened the interface of the 3D system by connecting to a millimetre GPS system from positioning specialist
The Topcon unit is designed to receive satellite signals from both the US GPS system and the Russian-owned Glonass network. Using both systems means that the 3D system has access to the maximum number of visible satellites at any one time and minimises the potential of downtime due to being out of range.
However, satellite based positioning systems cannot offer the level of accuracy needed for surfacing, so the Topcon system combine the satellite signals with a locally sited laser receiver to provide the extra elevation information needed to give millimetre accuracy.
Vögele's Navtronic 3D system continually compares the actual position information with the design position and changes the paver's screed and direction accordingly.
Minor deviations in terms of screed position are corrected by way of the screed's extending units. In the event of major deviations or the turning of radii, Navtronic intervenes in the paver's steering, moving both tractor and screed into the course of the route.
Vogele claims that it is the fully automatic control of both the screed's position and the paver's direction of motion that makes the system stand out from others available on the market.
Addition of GPS positioning technology has been available for pavers for some time, but most systems do not provide the vertical control necessary to guarantee a smooth road surface.
The width of the new L456 bypass varied from 7.7 to 7.8m. The Super 1900-2 paver used for the project was fitted with an AB 600 extending screed in TV version, which meant that Leonhard Weiss could surface the full width of the road in one pass. However, due to the large width, a receiver was fitted to each of the screed's arms to ensure maximum positional accuracy, particularly on the grade and slopes.
The contractor used the paver to lay the bitumen bound base course, formed using 0 to 32mm aggregate, to a thickness of 120 to 160mm, depending on the location. The automation on the paver meant that the thickness was controlled by the 3D system. According to the contractor, the tight bends and varying crossfall would normally have been a significant challenge but use of the 3D system helped to reduce work on site and the project went very smoothly. The automation of the paver also meant that the work on site proceeded much faster than might have been possible without 3D control.
Vögele has said that on a straightforward project the Super 1900-2 paver can lay up to 25m per minute but the rate is usually much slower on complex projects such as the work on the L546. Nonetheless, the automation of the surfacing allowed the work at St Leon-Rot to be fast tracked without compromising the final finish.
The project was Leonhard Weiss's first use of the paver fitted with the 3D control, so the contractor carefully checked the base course before continuing with the project. But accuracy of laying on the base course was so high that Leonhard Weiss's site team did not have to use the 3D control for application of the binder and wearing course.
Work on landscaping the new road is now underway and the local authority is now planning to further develop the Im Schiff area to bring new business to the area.RSS