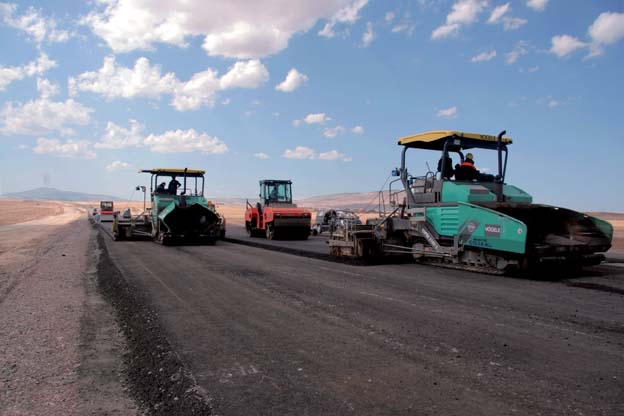
When completed, the 3200km Autoroute Transmaghrébine highway will connect North Africa together. ABE takes a look at the equipment and materials working on the Algerian part of the project
Morocco, Algeria, Tunisia and Libya form the United Arab Maghréb and the countries will soon be joined together by something more physical than their name. Work is currently underway to construct a 3200km three-lane highway between the four countries and forms the largest ever African road building project and is currently also the world's largest.
When completed, the Autoroute Transmaghrébine will link 55 cities in North Africa with a total population of more than 50 million together in a single high speed route. The motorway's 190 bridges and five tunnels will help to cut the travel time from the Tunisia-Libyan border to Morocco down to 10 hours.
The longest section of the new route passes through Algeria and work on the construction there started in March 2007 with completion expected later this year. The 1200km Algerian section is being constructed by three separate consortia.
The eastern section running from the Algerian city of Bordj-Bou-Arreridj to the border with Tunisia is being built by the Japanese consortium COJAAL. A subsection around Algiers is executed by Algerian contractors ALTRO and
A high volume of traffic is anticipated on North Africa's new "life line" and a strong emphasis is being placed on quality of both the materials and construction methods. The road construction has been designed to minimise deformation and all three road contractors have invested in new paving equipment with high compaction screeds from
Construction of the pavement has been standardised right across the whole 1200km length in Algeria. The base course is formed by a cement-treated gravel rich sand that is being placed in a thickness of 200mm followed by a 140mm bituminous bound base. This base layer is then covered with a 60 to 80mm thick asphalt wearing course formed using a 0-14mm nominal sized aggregate.
The Japanese COJAAL consortium is on schedule with its 365km section of the scheme. The contractor is using a fleet of 16 Vögele pavers - 12 Super 2100-2 pavers with AB 600-2 TP2 extending screeds and four Super 1900-2 pavers with AB 500-2 TP2 extending screeds to complete the work in echelon and paving hot-on-hot over a 6.25m width.
The China-based CITIC-CRCC is using its fleet of 13 Super 2100-2 pavers to pave the full 12.5m carriageway width in one pass. The pavers are fitted with SB 250 fixed-width screeds in TP1 version for high compaction. The supplementary construction work along the motorway, such as hard shoulders, is being handled by three Super 1300-2 pavers.
The Algerian contractors moved to the job site around the capital city of Algiers with two Super 1800-2 and two Super 1800-1 pavers, all fitted with high compaction screeds. The teams working on this section are paving for up to 14hours per day in order to finish the surfacing work on time.
According to the National Road Agency in Algeria, which is coordinating the project, the logistics of getting the work onto site and keeping the pavers supplied with asphalt has been a challenge. Nonetheless, quarries along the route have helped meet this demand for high quality materials and the work is on schedule for completion later this year.