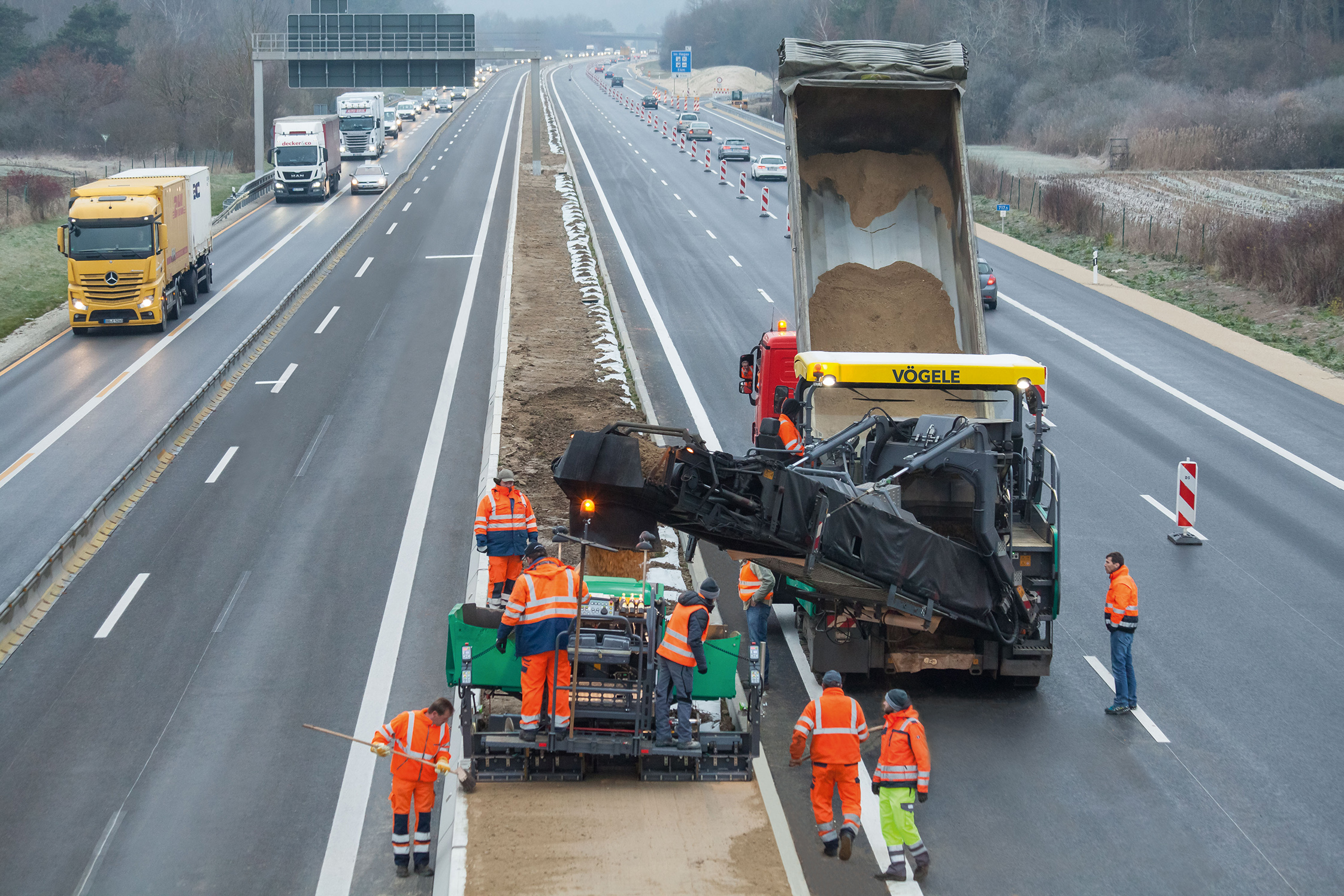
Traffic areas are permanently subject to heavy and fluctuating loads, and allowance must therefore be made, in the base course design, for the particularities of each application.
Geossynthetics have offered a tried-and-tested base course reinforcement solution for many years, performing a key function by increasing bearing capacity and improving traffickability, says Huesker.
“Further benefits include their high resistance to mechanical loads, straightforward installation, cost-effectiveness and eco-efficiency compared to conventional construction methods,” says the company, which is introducing Basetrac as the new brand for base reinforcement.
“As a result, the use of geosynthetics reduces the base course thickness and increases service life while significantly reducing maintenance intervals and costs.”
The company’s established products, including Fortrac (biaxial), Fornit, Base, Duogrid, Comtrac, Sefitec and HaTe, have been brought together to form the Basetrac product family.
“Huesker thereby simplifies product selection and provides construction companies and transport engineers with single-source solutions for all application areas. All Basetrac products are used as base reinforcement for permanent and temporary traffic areas, working platforms and railway applications.”
As well as simplifying the structure of its product portfolio, Huesker has also developed an entirely new base course concept with the aim of reducing the complexity of base course design.
“Using the newly-developed and specially tailored BaseCalculator web application, with just a few clicks the client can calculate the base course thickness and select the most suitable product to match the condition of the soil and application type. The BaseCalculator is available for free online use at: basecalculator.huesker.com,” says Huesker.
Meanwhile,
“For these reasons, material feeders are being specified for an increasing number of construction projects in many countries,” says Vögele. With the two material feeder models in its PowerFeeder series, Vögele says it is spearheading technological advancements in this machine segment.
Its proportionally-controlled pivoting conveyor, the MT 3000-2i Offset PowerFeeder, which offers flexibility to paving teams, “opens up completely new applications to construction companies,” and this was demonstrated by a job on the A81 Black Forest motorway, Germany, in which the machine fed a Super 800-3i Mini Class paver from the side.
“By these means, it was possible to fill a cavity between two safety barriers on the median strip of the motorway continuously. At the A 81 job site, the PowerFeeder’s pivoting conveyor was also able to also handle mineral aggregate.
“It was an unusual sight on the motorway job site: the largest and smallest Vögele machines joined forces to work as a team.”
This, says Huesker, yielded a number of advantages. Since the paver was supplied with material from the side, it was possible to safely maintain the flow of traffic.
The alternative, filling the cavity with an excavator or wheeled loader, requires an additional slewing and manoeuvring area. This means the trucks have to tip the material onto the traffic lane, and work cannot proceed uninterrupted.
“Working on a motorway has seldom been so relaxed. Traffic simply passed us by without affecting the construction work at all. The trucks with the mineral aggregate simply merge in front of the Vögele material feeder and transfer the material with no further ado,” says Ralf Wagner, foreman at J. Friedrich Storz Verkehrswegebau, describing his experience working with the MT 3000-2i Offset PowerFeeder.
Additional compaction was also unnecessary when placing the mineral aggregate with the Super 800-3i and the AB 220 TV extending screed.
As a result, the new concrete safety barriers, which form a 7km-long structural separation of the traffic lanes, were quickly and safely filled.