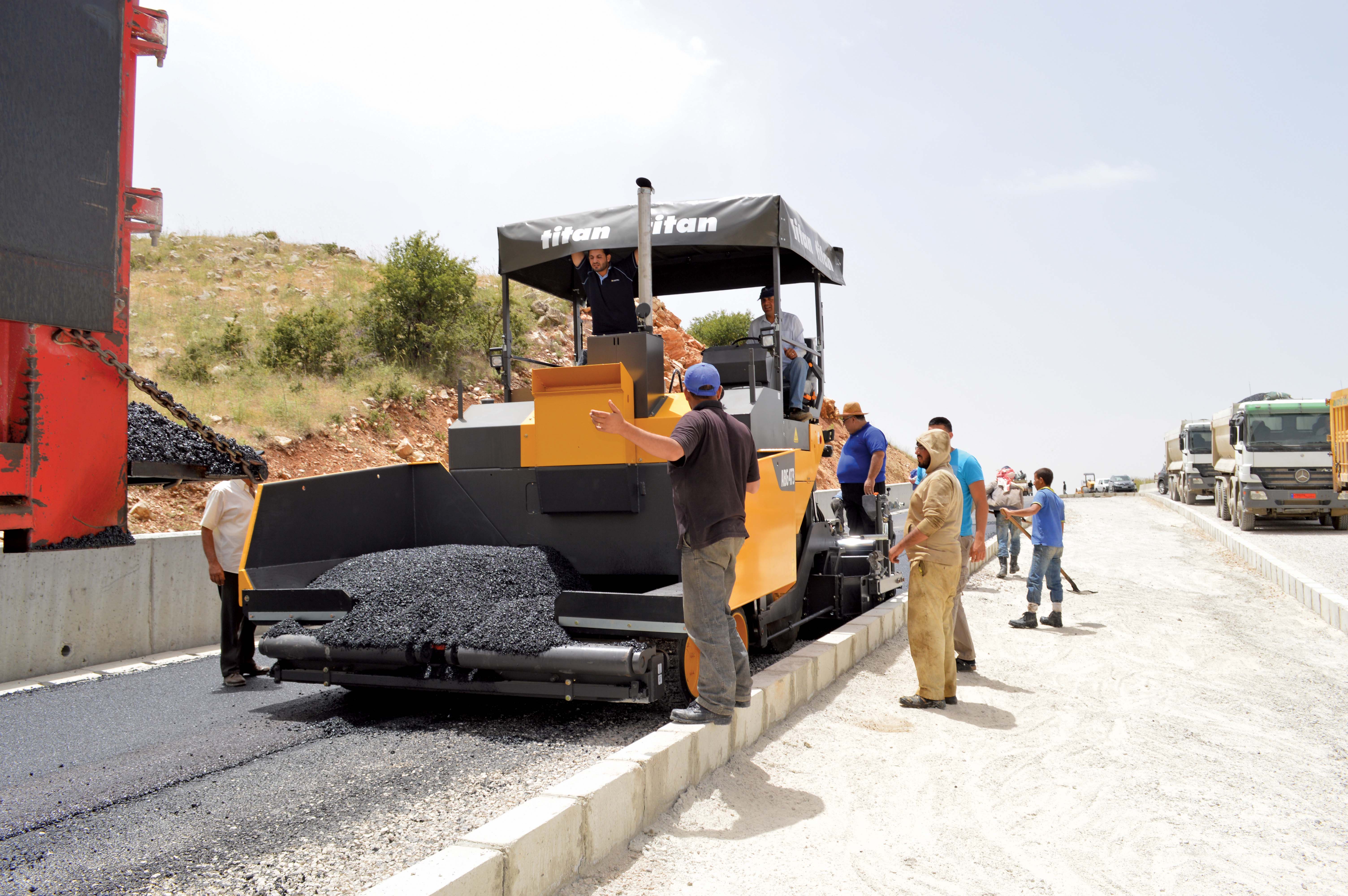
Despite increases in alternative methods of transport, road construction worldwide is seen as essential and is taking on a new urgency.
Many countries in Africa, Asia and parts of the Middle East as well as Eastern Europe, still have under-developed road networks, and it is here that a majority of the work is being carried out, often to improve the transport of essential goods for export or indeed import.
However, many routes are also in need of repair or rebuilding such as in Lebanon, which is rebuilding its infrastructure and connecting the mountains with the seaside and cities to encourage foreign investment and show the ambition and determination of a strong nation.
While many of these routes will be constructed using materials produced in the conventional way, there appears to be an increasing move towards technologies that offer reduced carbon emissions and energy costs.
For example, in the UK new government investment in the local and strategic road network comes with a condition: industry change. Clients, network operators and contractors must all adapt and the collective response must be underpinned by better supply chain partnership, early engagement and innovation, says Paul Fleetham, managing director of
“Construction 2025, the government’s industrial strategy, sets out ambitious targets for everyone involved in the construction sector. The industry must cut the cost of construction and whole-life maintenance of assets by 33%, as well as deliver a 50% decrease in the overall time to deliver new build projects or refurbish existing assets.
The principles of this landmark strategy are already driving greater change across the highways industry on both the strategic and local road networks, and the pace of this change is only set to increase,” says Fleetham.
“This means that greater cost efficiencies and accelerated delivery are expected for the strategic road network. From 2015, a newly remodelled public/private Highways Agency will require year-on-year savings of 4% on its new £5 billion (€6 billion/US$8.4 billion) Collaborative Delivery Framework. The HA has made it clear that it is looking for change and for supply chain partners with the necessary capacity and capability to drive quicker delivery and harness innovation.
“On local roads, it is evident from the Department for Transport’s (DfT) recently published Gearing up for Efficient Highways study, that government also expects greater efficiency from councils and, by extension, their maintenance providers.”
Indeed, Lafarge Tarmac and the
The project has lifted market barriers for the use of lower temperature asphalt used in road construction, which reduces energy costs, as well as cutting carbon emissions by up to 39%. The conventional road material, commonly used across the UK, is made by bonding aggregates and bitumen into asphalt by heating them to temperatures of 1800C–1900C. This project “successfully trialled” the use of a Low Temperature Asphalt (LTA) material, which allows mixing and working at lower temperatures. It is said to bond road materials as effectively as the conventional method, but using much lower temperatures and less energy.
The trial has enabled the project team to develop specifications for use, which will help accelerate the production and adoption of LTAs.
“Roads are the lifeblood of economic prosperity: they connect people to jobs and business to markets. There is tremendous potential for this project, given the scheduled improvements to major roads and motorways. This programme is an example of how by establishing new models of working, we can unblock demand-supply stand-offs, to help the UK to deliver the infrastructure of the future, at a lower cost for taxpayers and the climate,” says Al-Karim Govindji, technology acceleration manager, the Carbon Trust.
“This project with the Carbon Trust will help unlock barriers to bring lower temperature asphalt into wider use, cutting energy use, reducing CO2 emissions and enabling us to deliver projects more quickly for clients,” says Martin Riley, managing director for Lafarge Tarmac’s Asphalt and Aggregates business.
“It will take time for these materials to become available, but as producers follow our lead and adopt this technology, there will be a growing movement to embrace LTAs as direct replacements for conventional hot asphalts.”
If the new specification is adopted and the LTA market achieves 21% of the total UK asphalt market over the next decade, it could save around 260,000 tonnes of CO2 during the manufacturing of these.
Other project partners include
“Nynas has been developing low temperature technologies with its customers in Europe for over 20 years. We are proud to have continued our tradition by working with Lafarge Tarmac on this very successful and pioneering project,” says Jim Christie, business area director at Nynas UK.
Following on from this, the latest survey of recycled materials and warm-mix asphalt usage by the US asphalt pavement industry showed that nearly a quarter of all asphalt mixtures produced in the 2012 construction season were produced using warm-mix asphalt (WMA) technologies.
The survey, conducted by the
Because WMA is produced at a lower temperature than traditional asphalt mixes, it uses less energy to produce, reduces emissions, improves worker safety, and offers construction benefits.
US Secretary of Transportation Anthony Foxx says that the use of WMA is expected to save $3.6 billion (€2.6 billion) in energy costs alone by 2020.
Meanwhile, countries such as Lebanon are keen to press on with highway development. Lying on the eastern Mediterranean coast bordered by Syria to the north and Israel to the south, the country remains active in terms of development even though its northern neighbour is experiencing instabilities.
The country has experienced fast growth over the last 20 years, especially in its private sector, with a strong aggregate demand and a flourishing banking sector.
NAH Trading & Contracting is undertaking two extensive infrastructure projects, tendered by Lebanon’s Council for Development and Reconstruction, in Mount Lebanon Province using Volvo Construction Equipment (
The US$29 million (€21 million) Bir Hayth-Kartaba road, which also serves the local population, is 15.6km long and 10m wide. It begins 45km from the capital Beirut and finishes in Kartaba at an altitude of 1,250m, replacing a narrow road built 40 years ago, which is used by up to 2,000 cars/day. The project is due for completion early next year.
NAH’s fleet of Volvo CE machines on site includes one L150F-Series wheeled loader; three L120E-Series wheeled loaders; one SD100DC single drum compactor; four EC290BLC excavators; four A25C-series articulated haulers and the first factory overhauled Volvo ABG Titan 473-2 paver in Lebanon. NAH is supported by sub-contractor Fahim Saliba, which has two Volvo CE EC240BLC and two EC330BLC excavators.
NAH’s dealership in Lebanon, AMTRAC, provides onsite services to troubleshoot problems and conduct repairs.
The other NAH highway project runs parallel with the Bir Hayth project. The 10km, US$20 million (€15 million) Biklia-Sannine development uses the same Volvo fleet.
The stretch of highway, scheduled for completion in August 2014, runs near a popular ski resort, and includes the rehabilitation and expansion of an existing 3km road and the construction of a new 7km, 11m wide road, which will be paved with two layers of asphalt for a tough finish that will withstand winter conditions and high traffic levels.
“The Volvo ABG Titan 473-2 paver has been rotating from one project to the other, allowing fast paving cycles and reliable, accurate paving with synchronised movement of the screed, according to the soil conditions,” says Nassim, owner of NAH.
“The soil is naturally very fine and weak, which caused a road to collapse and increases the risk of slipping. The machines have fast cycle times and are reliable in these difficult conditions.”
German company
Ensuring an uninterrupted supply of asphalt mix to the paver required perfect job site logistics and optimum material management, and the solution was a non-stop supply of mix with a material feeder.
The contract consortium Arge A2 Zöbern-Pinggau (comprising construction companies Bauunternehmung
The PowerFeeder received the mix from trucks and continuously transferred it to the paver without physical contact, while the trucks navigated the job site.
The paver operator and screed operator were able to concentrate on paving work while one truck after another drove in reverse for up to 1km to dump mix into the feeder’s receiving hopper.
Equipped with an AB 500 TV Extending Screed, the Super 1900-2 placed two layers of asphaltic concrete (7cm and 7.5cm thick) for the binder course followed by a 3.5cm surface course of stone mastic asphalt. The pave width varied from 4.75m-6m.
“We achieved an outstanding degree of evenness thanks to the material feeder. We were easily able to meet the client’s strict quality requirements,” says Harald Zippe, the site manager from Granit.