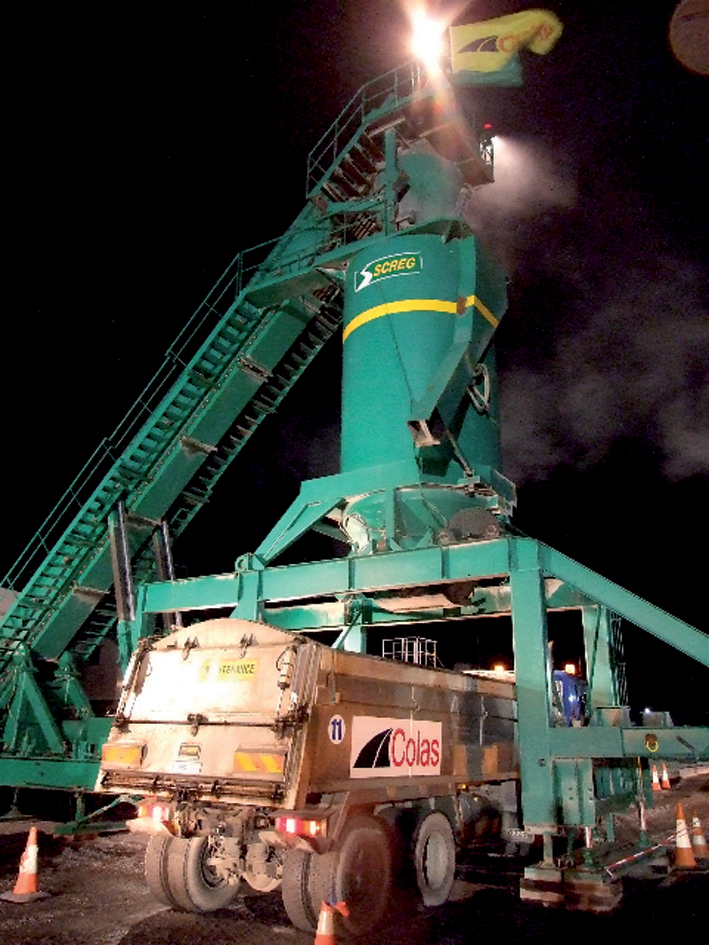
Introduction of better performing and more cost effective asphalt materials is gathering momentum in UK airport surfacing - and building a bank of invaluable knowledge within Colas. Jon Masters reports on its application at Jersey Airport
Airfield surfacing is a particular specialism within the paving sector and one in which
The latest project to be completed is on Jersey in the Channel Islands where a partnership of contractors
This is vital and very valuable data because the BBA spec is largely performance based. In comparison to materials specified to a recipe approach, including the Marshall Asphalt most commonly used on UK runways, BBA allows more opportunity to innovate and use modern polymer modified binders - providing mixes meet specified performance criteria. Every BBA mix has to be individually developed and tested with the exact constituents to be used on the project, which Colas has been doing at the company's research facility in Paris.
"For every job using BBA asphalt, we have to identify suitable sources of aggregate and carry out considerable mix development and testing up front, but the results are worth the effort," said Colas airfields business manager Carl Fergusson. "While our French colleagues have a vast amount of historic data on suitable aggregates, we have to build a similar database for the UK market. BBA materials and French pavement technology are generating a lot of interest from airport operators and consultants alike."
Delegations from other airport authorities and their consultants to a number of Colas' projects have been impressed with the results and in a recent revision of its paving standards the UK
For the Jersey project, a new asphalt pavement was needed to replace the existing 'porous friction course' and to smooth out the runway's longitudinal profile to the Code 4C standard. David Tisdale of the airport's project manager Capita Symonds CI said, "The porous friction surface had performed well but was nearing the end of its useful life.
"The design team and client spoke to contractors about various options including the possibility of pursuing a Marshall Asphalt surface, but we needed to build up the runway's geometric profile in layers. BBA asphalt can be laid in thicker layers and gives better friction and drainage characteristics. The BBA option also presented a more economic solution due to its lesser aggregate requirement." The Jersey runway's effective length could not be shortened over the duration of the project, so the team needed a material that could be used for take off and landings while in a temporary - before overlaid - state. "BBA gives very good friction values when laid in a temporary state and in the long term. On site it has proven easier to use all round, which, with the temporary state friction characteristic, has been very good for project programming." Tisdale said.
According to Carl Fergusson, BBA asphalt is generally an easier material to manufacture due to its aggregate grading and is more workable in laying, usually from the addition of a polymer modified binder. The results are more productive mixing and construction outputs in a given time.
Colas initially introduced BBA asphalt to the UK in 2006 at Sumburgh Airport in the Shetland Islands for maximising surfacing outputs in limited runway possessions as pressures were mounting on operators to maximise runway availability time. Success at Sumburgh for Highlands & Islands Airports Ltd (HIAL) led to further work and use of BBA materials on Tiree in the Inner Hebrides (also for HIAL) and at Ronaldsway
Airport on the Isle of Man where Colas is due to return later in 2009 to carry out the second of two major phases of surfacing work.
"For the Jersey contract we joined forces with Fitzpatrick in the bidding because of a natural synergy between the two companies," Fergusson said. Both have a lot of experience in the airfields sector; Fitzpatrick having carried out at least three previous contracts on Jersey.
Colas' runway resurfacing projects have been getting bigger. The Isle of Man scheme involves 158,000m2 of pavement construction, but with 40,000tonnes of BBA binder course, Jersey represents the greatest UK development in BBA asphalt to date.
Other aspects are similar to those at Sumburgh, on Tiree and the Isle of Man: detailed planning of movements of resources and deliveries of materials is essential for such relatively remote locations.
Aggregates were supplied from a combination of hardstone quarries in northern France via the port of St Malo and a local Jersey quarry. The bitumen binder, including Colas' own Colflex binder, came from Britain via Portsmouth in two or three road tanker deliveries each day on the daily ferry from Portsmouth, while plant and equipment was supplied from Colas UK's own airfield division and from France by the Colas SA subsidiary Screg Grands Travaux.
"We had a very extensive supply chain and complex organisation of materials and resources to manage," explained Fergusson. This included Screg's very large mobile asphalt plant of 350tonnes per hour output and the company's big
Every tonne of the asphalt laid at Jersey went down at night. The existing 25mm porous friction surface was planed off in sections and new BBA binder course laid in various regulating thicknesses followed by a 50mm BBA surface course, which was subsequently grooved - all during runway possessions lasting from 9.00pm to 5.30am between the end of October and mid December 2008.
"We generally had to be finished and cleared from the runway with fresh white lines down and grooves on the surface by 4.30 each morning, which gives an idea of how critical each night's planing and paving is in terms of getting it right first time," Fergusson said. "Everybody on the team is always fully briefed before each shift and reminded of the importance of good workmanship." The grooving applied to Jersey's new runway surface was not entirely necessary, Fergusson said. BBA asphalt is not grooved in France due to its higher friction value and macrotexture. If not applied, surfacing programmes could be shortened further. "Our French colleagues think we're mad grooving the material," he added.
The debate continues though, partly because UK standards state runways have to be grooved, so threatening non compliance if runways are not grooved whatever the material. Colas is hoping that in time this can be reversed.
David Tisdale said, "Pilots' JAR Ops standard gives guidance on the condition of UK runways based on either a porous or grooved surface, which is very different from BBA surfaces, so we were stuck with the possibility of non compliance and forced down the route of grooving. Grooving does, however, aid the dissipation of water in wet conditions giving added safety to landing aircraft.