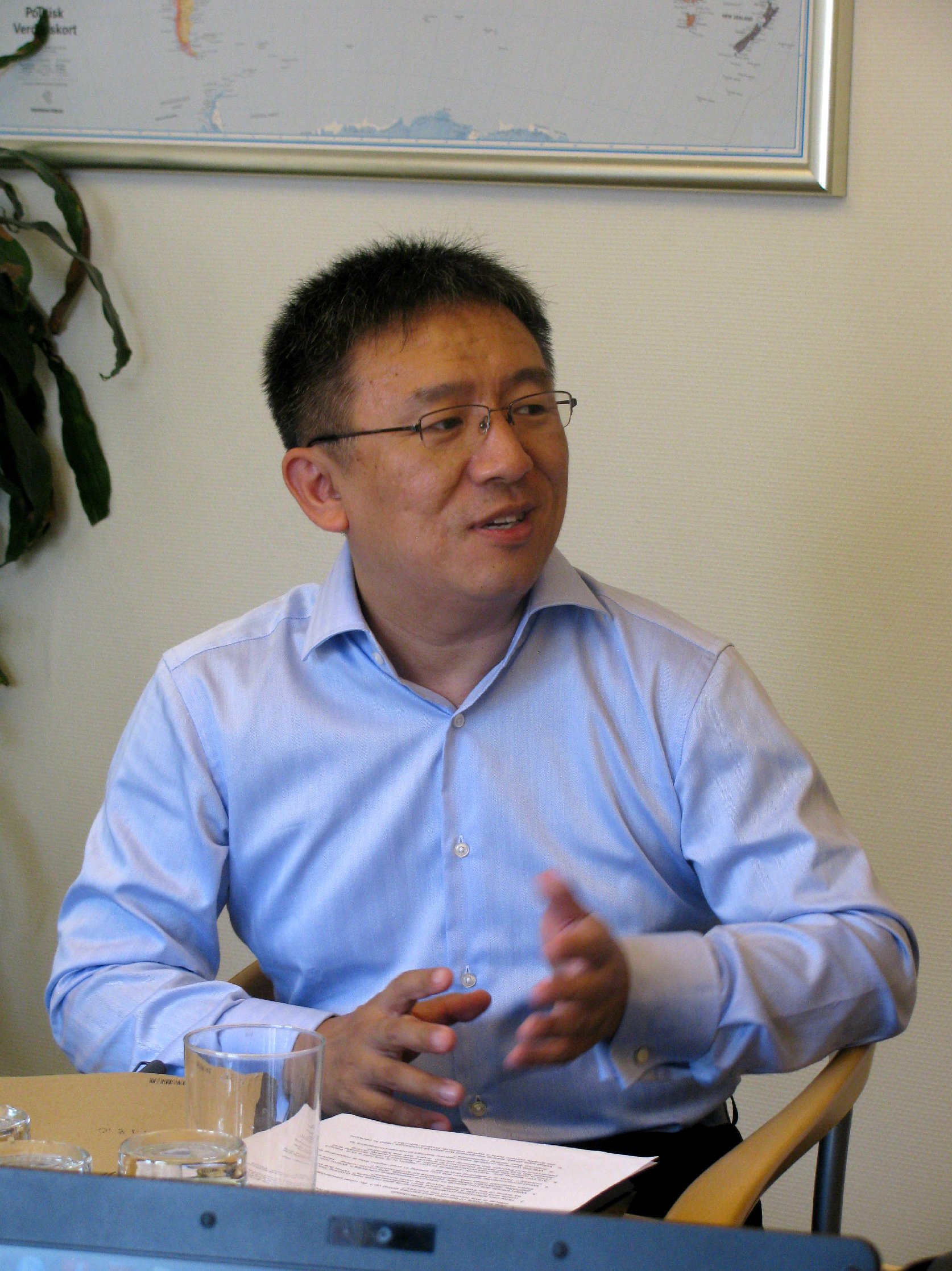
Empty environmental commitments from governments, falling bitumen quality and the impact of the economic crisis led DenimoTech to ask its global distributors about the challenges of today’s markets. Kristina Smith reports.
These are challenging times for
Looking to the future, DenimoTech brought together ¬five of its 14 distributors at its headquarters in Arslev, Denmark, to brief them on new product developments and to ¬find out what is happening on the front line. Covering regions including South East Asia, North Africa, China, Western and Eastern Europe, these firms supply equipment, chemicals and technical know-how to asphalt suppliers and contractors.
Against the backdrop of the economic crisis, these firms are battling to open minds and budgets to the wider range of applications that are possible with bitumen emulsions. As a potential cold technology, which could save energy and the environment, bitumen emulsions should be gaining in popularity. However, it seems that governments’ rhetoric on cutting carbon emissions has remained just that, with capital cost now the overriding concern.
“In 1998 we had the Iberian Congress in Spain. Everybody came from the conference thinking that we had lots of projects with green solutions on their way. Up until now, we never saw one,” said Hugo Guimarães, CEO of WeedsWest which is based in Portugal but also works in countries including Mozambique, Angola and Equatorial Guinea.
For contractors to consider new technologies, cash savings must be on the table, says Zoran Krusic, deputy managing director of Coning-PPI of Serbia. “I would not motivate my customers by telling them that they will save on carbon emissions,” he said. “We should talk about savings in fuel first, and this will lead to cutting carbon emissions.”
In Ukraine, Prologue has taken a proactive stance in the downturn, opening a laboratory and running training sessions in bitumen emulsion technology.
“When conditions change and road enterprises start to think about buying something for emulsions, they will come to us,” said Anatoliy Baback, head of the firm’s technical department.
However Michael Tan, managing director of T-Pave International from Singapore, highlighted a looming issue for the industry - the diminishing quality of bitumen. “The cost of bitumen is rising. And the performance of bitumen is getting worse and worse,” said Tan.
“One day bitumen will be very dif¬ficult to work with. Sometime in the future, there will be competition to see who can find bitumen substitutes.”
This process has already begun though, said Tan, with one Korean firm looking at replacing 20% of bitumen with Carbon Black and a Chinese supplier working with Coal Tar Pitch.
“Eventually there will be a lack of bitumen,” agreed Krusic. “I think we should focus our efforts on technologies such as rejuvenating old binders to slow down consumption.”
In China, Nico Zhang Yi, vice general manager of Hotlink, faces fierce competition from Chinese manufacturers supplying plants at a fraction of the price of suppliers such as DenimoTech. Some European contractors are also buying Chinese kit, says Guimarães, but for most customers, reliability and after-sales care are more important considerations. “Sometimes, that’s worth more than money,” said Guimarães.
Around the table, all agreed on the dif¬ficulty of introducing new technologies. Several had accounts of new surfacing techniques beginning to gain ground, only to be stopped in their tracks at the first sign of failure. “Governments won’t take the risk,” said Guimarães. “Until they are able to take the risk, we are not able to supply them with what they don’t want.”
“Cold recycling started very strongly in the Balkans,” said Krusic. “And micro surfacing also made a good start. But at the first failure, it stopped for a long time. Sometimes it feels like everybody is waiting for the mistakes, rather than supporting new technology.”
Tan explained the growth of microsurfacing in China, introduced in 1990 but stalled for a decade due to early teething problems. Then in 2000 MeadWestvaco arrived and took a new approach, controlling every element of the process from the aggregate supplier to the logistics and the quality management, and microsurfacing took off.
Tan’s conclusion is this: “If you want to do a demonstration trial project onsite for a new emulsion technology, you need to take control of the whole project from A to Z, including lab testing, mix design, emulsion production, onsite operation. Otherwise it will have a greater risk of failure, slowing down development of new techniques.”