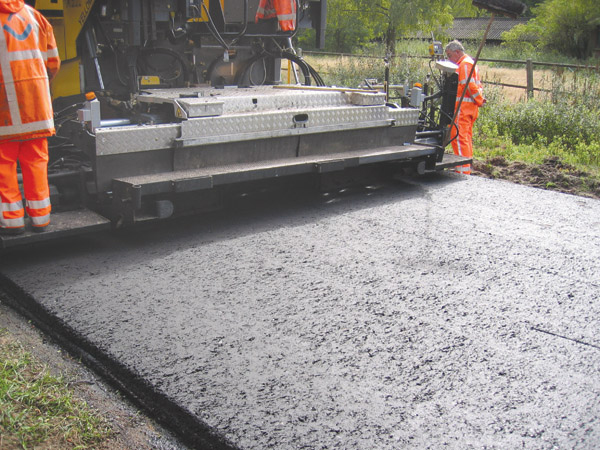
Reducing the temperature that asphalt is produced and laid at has significant benefits for the environment but achieving lower temperatures needs to be balanced with quality and durability
While increasing use of sustainable transport is frequently under the spotlight, few can argue against the social and economic need for roads in modern society. But the materials used for their construction and maintenance and the vehicles that use them all impact upon the environment.
Nonetheless, reducing the temperature that the asphalt mix is produced and applied at is one area of development intended to lessen the impact. According to
"New products and processes are constantly being brought to market seeking to ameliorate the environmental impact of roads," said Renaudeau. "Referring specifically to road construction and maintenance, the increased use of recycled asphalt planings (RAP) and other recycled materials together with new materials from renewable resources are all significant contributors to the overall objective of a "green" industry.
"In many circumstances bitumen emulsion technologies such as surface dressings and microsurfacing are cost-efficient, fit for purpose and of low environmental impact. Lately, however, the industry focus seems to be on the reduction of asphalt mix production and application temperatures."
Hot history
Hot mix asphalt (HMA) production and application typically requires materials to be heated to between 135°C and 180°C. The temperature is dictated by the viscosity of the bitumen binder and is needed to ensure a homogeneous and thorough coating of aggregates by the bitumen.
Such constraints must be borne in mind when considering the possibilities of reducing production and application temperatures. There is also the demand to guarantee mechanical properties for the new pavement immediately following completion of the surfacing, to minimise risk of compromising durability and traffic disruption. The key lies in the diffusion of the binder through the mineral skeleton of the aggregates. Several options have been introduced to achieve such goals at significantly reduced temperatures to deliver three different categories of reduced temperature asphalt - cold mixes, semi-warm mixes and warm mix asphalt.
"Cold mixes are generally produced at temperature between 25°C and 60°C" explained Renaudeau. "These bitumen emulsion cold mixes - where aggregates are coated at low temperatures in an emulsion of bitumen in water - are a more recent development but no novelty. The material can be used for binder layers, overlays and even wearing courses for anything but the heaviest trafficked roads. These products have until now had to be manufactured in specific cold mix plants and undermined their commercial development.
"Yet all this could change. Typically, only about 0.1litre of fuel is required to produce 1tonne of cold mixed asphalt, compared with between 10 and 14litres of fuel per tonne of hot mix, representing substantial cuts in energy bills and CO2 emissions.
"Emulsion-based cold mixes also allow a far higher proportion of recycled material to be incorporated into the mix than is possible with hot mixes. A cold mix binder layer can successfully be made using RAP for the entire aggregate content and emulsions can also coat planings that are contaminated with tar." The next group is semi-warm mixes, which classifies materials produced at between 60°C and 100°C. Several products and processes are now being developed to produce emulsion-based semi-warm mixes in conventional hot mix asphalt plants. The production and application temperatures of these mixes can be reduced from standard conditions by 50°C to 75°C without compromising the durability of the paving material.
Yet the most ambitious processes for temperature reduction make use of the foaming properties of bitumen when in contact with air and moisture under pressure. As the bitumen volume expands dramatically, binder viscosity decreases and a thorough coating of the aggregates is made possible. The target here is to maximize the energy savings and emission reduction by taking advantage of some of the moisture in the aggregates; if all the aggregates are not fully dried, up to 40% or 45% of the energy usually required can be saved.
"Various processes using this technique have been developed and successfully trialled," said Renaudeau. "Benefits go beyond reduced energy use and lower emissions to the environment, such as CO2, volatile organic compounds and dust. They include the reduced risk of burns for operators, an increased flexibility by extending working time for transport and application (the materials do not cool as fast as standard hot mix asphalt) and reduced ageing of the binder during the production." Warm-mix asphalts (WMA) - produced at between 100°C -135°C - tend to be classified by their working temperature range. Reducing the temperature requirement of WMA while maintaining or improving its end performance characteristics requires a technology that reduces the viscosity of the binder during the mixing and laying phases without having a negative effect at in-service temperatures.
Water vapour or organic additives can be used to modify the viscosity of a 'hot-mix' binder so that it can be successfully handled at the lower WMA temperature range.
The water vapour method uses the violent reaction between water and a very hot substance at atmospheric pressure to create a foaming effect if used with bitumen. Introducing small quantities of water to hot bitumen causes the bitumen to foam which reduces its viscosity and increases its surface area to ease mixing, coating surfacing at reduced temperatures.
Water can be introduced into the asphalt via damp aggregates (coarse and /or fine), water injection nozzles and zeolites (powered, hydro-thermally crystalline, hydrophilic materials), which have a high moisture content that is released slowly during the mixing and compaction process.
The organic additives approach uses specially selected long-chain waxes and fatty amides to reduce bitumen viscosity. Both of these material groups are classed as viscosity modifiers, both have melt points that allow viscosity reduction at production and surfacing temperatures, allowing up to a 40°C reduction.
The additives disperse as discrete micro particles within the bitumen; as the asphalt cools the additives gradually return to their naturally solid state. The type of additive and the base binder dictate the impact on in-service performance; typically the wax-based additives will solidify above the softening point of the bitumen, improving resistance to rutting and allowing early opening to traffic.
"These developments mean that it is now possible to produce and lay asphalt mixes at temperatures ranging from 60°C to 130°C instead of the traditional 135°C - 180°C," said Renaudeau. "Emissions can be cut by 25% to 45% but to assess the benefit for the environment the overall energy consumption of road transportation (including road construction and vehicle consumption) and CO2 and SO2 emissions need to be considered."
Construction, maintenance and operation of roads only account for 2% to 5% of the overall energy consumption of road transportation. However, a 2004
"Consequently, reducing greenhouse gas emissions during the production of the materials used in road construction and maintenance is a very relevant contribution to reducing the environmental impact of roads," said Renaudeau.