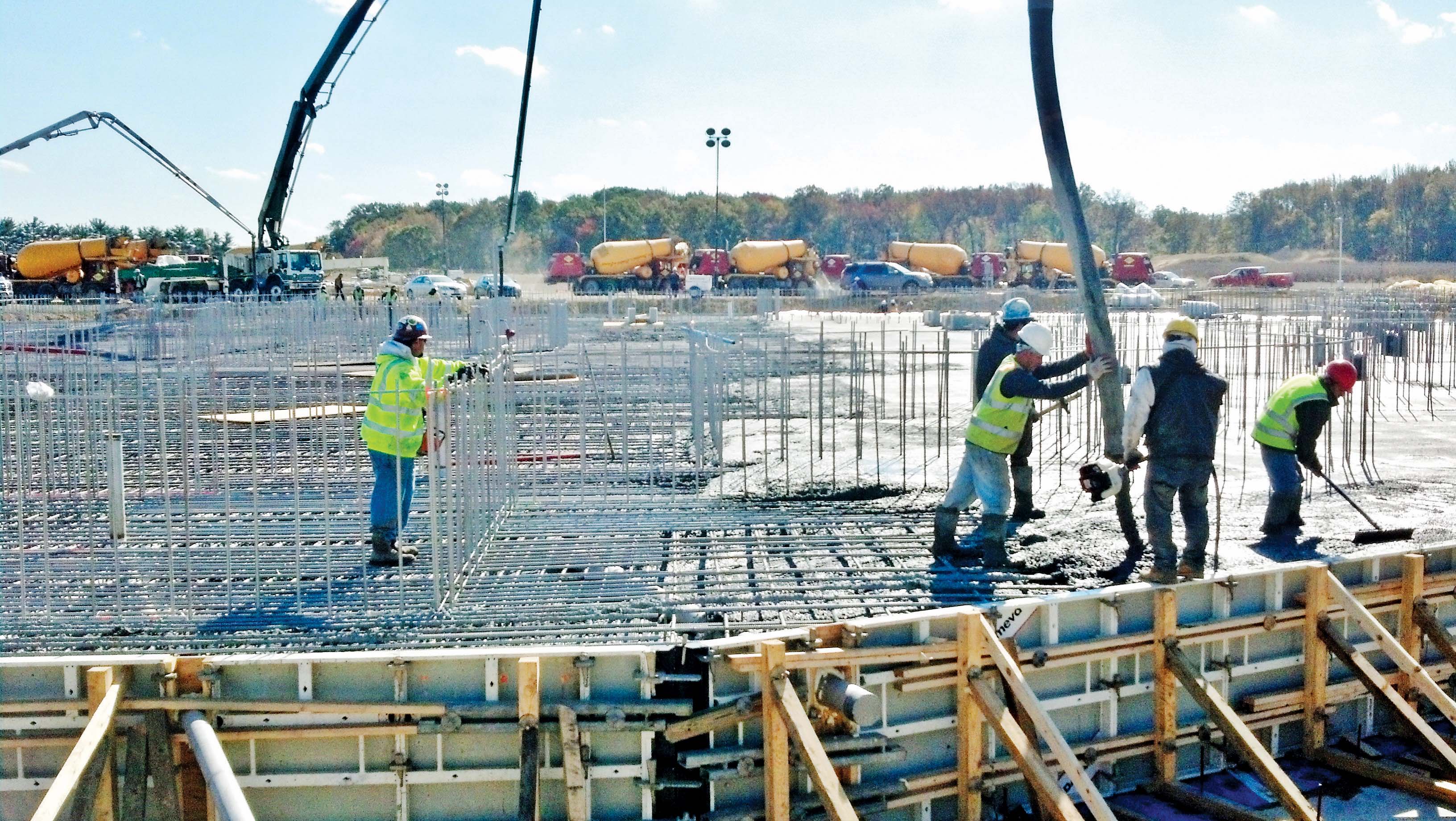
The daunting challenge of laying a 4,550m² monolithic concrete foundation within a record-setting 12 hours, was no easy task for ready-mix manufacturer Silvi Concrete.
The foundation was vital for the placement of a new monument for the worldwide Hindu Organisation (known as BAPS) for its recently completed 6,500m² recreational and teaching facility, and ornate temple in Robbinsville, New Jersey, US. The 52m-high monument is now part of one of the largest and most ornate Hindu mega worship centres in the world.
In addition to over the concrete, the project contained 145,000tonnes of stainless steel rebar.
In an effort to streamline this race-against-time logistical challenge, Silvi, of Pennsylvania, leveraged its association with GivenHansco of Columbus, Ohio, a developer of producer-driven software for the ready-mix construction industry, and its integrated Keystone suite of advanced accounting, batch control, dispatch, and GPS vehicle software solutions.
The goal was to deliver over 540m³ of ready-mix concrete/hour over a 12-hour period, continuously implementing 106 trucks from three central ready-mix concrete plants to the foundation site.
The BAPS project represented the largest continuous concrete pour in Silvi’s history, requiring a perfectly executed timetable and plan of attack: the slightest error in judgement and planning could represent the potential for failure.
Silvi’s automated, high-capacity plants, trucks, and experienced personnel were able to manage and facilitate emptying a full truck of concrete every 60 seconds within the time limit with assistance from GivenHansco’s Keystone products, working seamlessly in the background.
Silvi implemented a full complement of the integrated Keystone suite of software products to streamline logistical power, efficiency, and flexibility for the BAPS project, including Keystone Accounting, Keystone Dispatch and Keystone GPS.
For example, Keystone Dispatch tracked all 106 trucks on one screen with continuous fleet management, order status, and updates throughout the 12 hours while Keystone GPS tracked 700 truckloads of concrete with radio GPS throughout project’s critical product delivery.
Hours of advanced meetings were required to discuss the possible problems that might occur and to formulate solutions to those challenges, and Silvi assigned 20 additional employees on site to assist in quality control, traffic management, and truck placement.
“Given the short timeframe, staging the traffic patterns for the trucks was a must and the ticketing of 700 truckloads of material was key for success,” says Jeff Davis, Silvi’s director of dispatch.
Pushing the 106 trucks through faster was critical, as the drivers were only legally allowed to work 12 hours/day.
At 5.45am on the day of the placement, 40 trucks started rolling on to the site. On arrival, after a Hindu priest’s ceremonial blessing at the project’s start, they began feeding five pump trucks strategically staged around the foundation.
Efficiency of the material supply chain is critical to batch concrete with on-time deliveries to the plant, while moving a lot of material in a short amount of time, as was the case with the BAPS project.
Silvi’s automated, high-capacity plants, trucks, and personnel were able to manage and facilitate emptying a full truck of concrete every 60 seconds.
The integrated Keystone suite of software products helped to streamline logistical power, efficiency, and flexibility.
For example, Keystone Accounting facilitated centralised reporting for the project’s multi-plant operations; customised full financial and ready-mix specific accounting requirements of the producers involved, and managed tickets, material usage costs, and job management data throughout the project’s process.
Keystone Dispatch provided straightforward truck scheduling with an easy to use colour-coded interface, tracking the 106 trucks on one screen with continuous fleet management, order status, and updates throughout the delivery timeline while Keystone GPS tracked the 700 truckloads of concrete with radio GPS throughout the project’s critical product delivery; provided easy-to-recognise icons that changed colour based on a driver’s current vehicle status, and quickly identified a truck that was blocking the entrance to the BAPS site for retrieval.
“It allowed us to maximise every last drop of efficiency out of whatever resources we had in action on the project. There were no lags in tickets, no waits from plants, as well as approved mixes, immediate driver tracking, centralised reporting, and cost control analysis. Most importantly, GivenHansco’s customer service was impeccable: if there was any problem they were right there at the make of a call,” says Davis.
Currently, Silvi is using GivenHansco’s Keystone products for all nine of its operating plants; including three new ones which were integrated easily into its system.