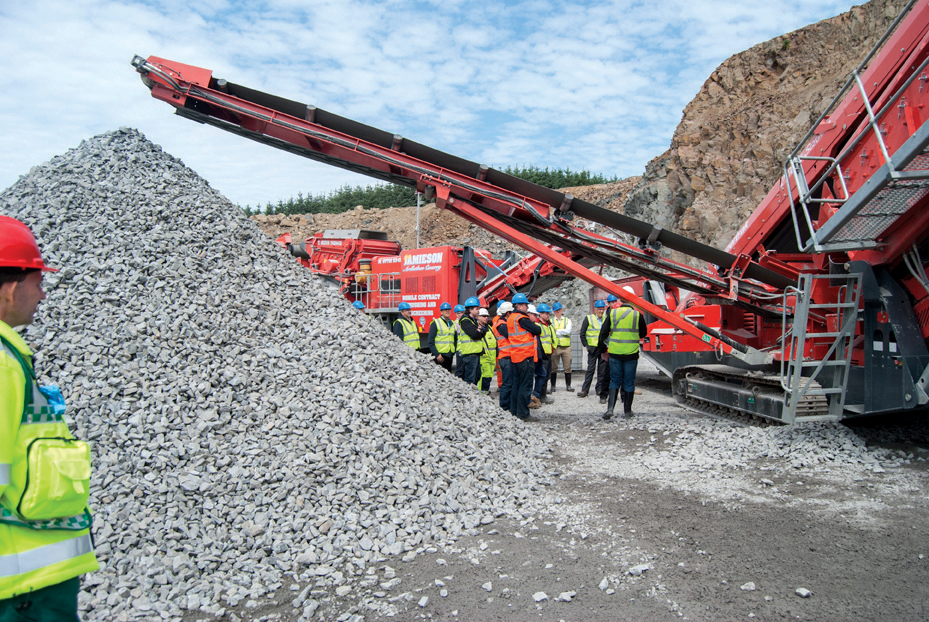
About 25km north of the city of Aberdeen on Scotland’s east coast is the town of Ellon. Driving through the city on the way to James Jamieson’s Ardlethen Quarry just outside Ellon, it is not difficult to see how it got its nickname, writes Patrick Smith. Best known as the Granite City, it is also called the Grey City after the material that was quarried nearby, and of which much of it is built. Another nickname, the Silver City with the Golden Sands, is from a 1950s guide book, when post-war visitors were happy with a trip to the beach.
At the Ardlethen Quarry a weathered granite rock is quarried in an operation that has been described by experts as “meticulous” at a quarry site that has been described as “perfect.”
Indeed, Nigel Irvine,
“We do a lot of prototype testing of our equipment here.”
Ardlethen Quarry is operated by director Jim Jamieson who has been a leading figure in the quarrying, construction, civil engineering, waste handling and recycling industries across the Grampian and County Aberdeenshire regions for 40 years.
The family-orientated and operated business is headquartered at Ellon, Aberdeenshire and has grown and diversified under the guidance of Jamieson, who started out as an apprentice bricklayer.
Jamieson’s entrepreneurial spirit, vision and direct workmanlike approach progressed to developing his own business, and today he leads a group of companies that continues to grow steadily, and which employs over 60 people.
In 2000, Jamieson bought a landfill site outside Aberdeen and under his control it became the first double-lined landfill site in the Aberdeenshire area.
He sold this business in 2004 to focus on his construction and civil engineering businesses, and this led to the acquisition of Ardlethen Quarry in 2005 to service the Grampian and Aberdeenshire regions, and support his construction focused-businesses.
He decided to sell the quarry in 2008 to concentrate his efforts in further developing his commercial construction business.
The Ardlethen Quarry was then repurchased during 2010 and he immediately set about the process of developing the quarry and taking it to the next level.
This was followed by the acquisition and development of additional local quarry locations in Whitecairns and more recently in Newmacher, Aberdeenshire, to produce crusher run, quarry dust, sand, gravel and various sized aggregates ranging from 0-150mm, Type 1, and railway ballast as well as tight specification aggregate products to meet client requests.
Today the company’s client base boasts some of the most prominent regional players and includes local councils.
To produce such a range of products the James Jamieson company exclusively operates tracked mobile crushing and screening equipment across the company’s three quarries.
Jamieson’s first experience of mobile quarrying equipment was over 25 years ago when he rented a Finlay mobile screen from Tom McNeill at Finlay Scotland. This led to a long-lasting partnership between the two companies.
Today Jamieson operates a range of Terex Finlay jaw and cone crushers as well as heavy-duty and inclined screens. To work alongside the crushing and screening equipment is a range of excavators and shovels from
The latest additions to the fleet include a J-1480 jaw crusher; a C-1550 cone crusher and a 694+ inclined screen, which are among the machines that are said to be key to production at the three quarries, and also the contract crushing and screening services that the company operates throughout Scotland.
The versatility of his fleet means that Jamieson can also employ his crushing and screening equipment on-site to support his and son James's civil engineering activities when required.
Jamieson’s business motto is Service Set In Stone, and this rings true with the meticulous approach that he adopts in every aspect in each of his businesses, which he runs with the support of his wife Moira, and son and daughters.
At present Ardlethen Quarry covers some 70 acres (28 hectares), and the rock is won by blasting, which is carried out as required but usually at least once every two months, when some 40,000-50,000tonnes of material is produced.
This can be loaded directly into the crushers using a variety of hydraulic excavators owned by Jamieson including a Caterpillar 336D; Liebherr 954; Volvo EC250DL and a Volvo EC290CL.
These are also used at the other quarries as required as is the crushing and screening equipment, which is also used for contract crushing.
“There is land available for expansion here and we have got planning permission for this,” says Jamieson.
“I estimate that we have between 4-5 million tonnes of material that can be excavated: at present we produce about 140,000 tonnes a year.
“We also have prepared land that can be used as storage or in the future as a concrete plant. This is a realistic proposal.
“While we blast and then crush and screen, we also keep stockpiles of material at the quarry and we have a fleet of wheeled loaders to keep these topped up.”
The fleet includes a Caterpillar 972H; Caterpillar 966H and two new Caterpillar 966K models, one bought last year and the other just recently.
“We also have a fleet of 14 tippers here, mainly
Jamieson’s Terex Finlay crushing and screening equipment is set up in a train and the company’s plant includes the new J-1480 primary jaw crusher and two J-1175 jaw crushers along with the C-1550 cone crusher, which is generally used as a secondary crusher.
Screens at Ardlethen include a Terex Finlay 694+ three-deck inclined screen and a Terex Finlay 883, which is designed to work as a primary screen in a variety of operations including quarry, sand and gravel and aggregates. It can also be used as a secondary screen fed from a crusher.
Open Event
Indeed, Ardlethen Quarry was the site of Terex Finlay’s largest ever Customer Open Event when it highlighted all its new models for quarrying and recycling applications to over 300 end users and dealers from China, Australasia, Russia and CIS states, Africa, the Middle East, Europe and the Americas.
The highlight of the demonstration was a single plant configuration consisting of eight different models, says Nigel Irvine.
This featured products introduced to date in 2013 and a number of new models to be launched later in the year.
In Jim Jamieson’s main quarry new models presented included the J-1480 with direct drive jaw crusher; 893 heavy-duty screener; 684 two-deck inclined screener and new 694+ Optidrive inclined screener, a diesel/electric dual power alternative to the three-way split screen.
Other models featuring as part of the train included the C-1550 cone crusher; J-1175 jaw crusher and the I-130RS impact crusher. The line-up was completed with the incorporation of the Terex Finlay C-1540 cone crusher.
The model on display featured the new onboard side conveyor configuration that is said to afford operators the opportunity to remove pre-screened fine material from the plant.
The Terex Finlay J-1480 jaw crusher which operates at Ardlethen incorporates a Terex Jaques single toggle jaw crusher, and has a throughput capacity up to 750tonnes/hour, depending on application and material, while the 893 screen has a forward-facing inclined modular configuration screenbox with a 6.1m x 1.8m top deck and a 5.5m x 1.8m bottom deck. It is being launched in the first quarter of 2014.
Excavators
1 x Caterpillar 336D
1 x Liebherr 954
1 x Volvo EC250DL
1 x Volvo EC290CL
WHEELED LOADERS
1 x Caterpillar 972H
1x Caterpillar 966H
2 x Caterpillar 966K
MOBILE CRUSHERS
1 x Terex Finlay J-1480 jaw crusher
2 x Terex Finlay J-1175 jaw crushers
1 x Terex Finlay C-1550 cone crusher
SCREENING
1 x Terex Finlay 883
1 x Terex Finlay 694The Terex Finlay J-1175 tracked mobile jaw crusher, of which Jamieson operates two, incorporates the Terex JW42 jaw crusher, and the chamber is hydrostatically driven, offering operators reversible operation for clearing blockages or bridged material.
The I-130RS is based on the Terex Finlay I-130, and machine features a 4,270mm x 1,520mm single deck screen for sizing and recirculating oversize material back to the crushing chamber, while the Terex Finlay 694+ Optidrive is the latest variant of this inclined screen, offering the 6.1m x 1.52m triple-deck inclined screen. It was launched at the open event.
The Terex Finlay C-1550, also operated by Jamieson, incorporates the Terex 1300 cone crusher driven by direct drive, and features a pre-screen module with a single deck 2.45m x 1.52m screen for removal of fines from the feed material.
The 684 two-deck inclined screen features two 4.3m x 1.7m inclined decks, while the 684 three-deck inclined screen features three 4.3m x 1.7m inclined decks. All three discharge conveyors hydraulically fold for transport
In the quarry recycling area, the Terex Finlay J-1170 crusher with a Terex 1,100mm x 700mm jaw crusher is also available with an optional hydraulic release, and the I-100RS direct drive 860mm x 860mm horizontal impact crusher with variable speed is based on the Terex Finlay I-100. Featuring a 2.44m x 1.2m single-deck screen for sizing and recirculating oversize material back to the crushing chamber, it is to be launched soon.
The mobile Terex Finlay 883 with Spaleck screen, launched at bauma 2013, has at its heart the two-deck German-designed
and constructed high performance screenbox. The stepped top deck design is combined with state-of-the-art flip flow technology on the bottom deck.