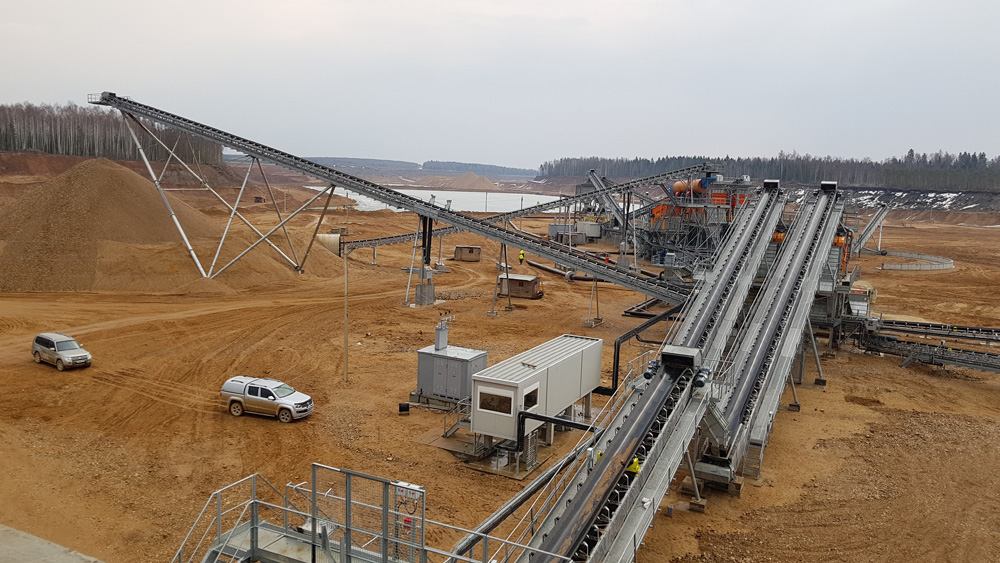
One of Russia’s largest aggregates processing companies, Bogaevsky Karyer JSC (Bogaevsky) was founded in the Moscow region in 1997. At the heart of the business is its Oreshkinskoye-based deposit of sand and gravel used to produce aggregate building materials, including Class II crushed stone, gravel, and sand. The vast site allows Bogaevsky to produce around 5.5 million m³ of finished GOST-compliant products annually.
Increasing demand nationally for finished products such as Class I and II sand, washed 5-20mm and 20-40mm crushed stone, and 3-10mm washed gravel made Bogaevsky keen to improve the firm’s production volumes and efficiency, while simultaneously lowering product price while enhancing its quality. Company management turned to Metso and a strong partnership between Bogaevsky and the Finnish crushing and screening plant giant was born.
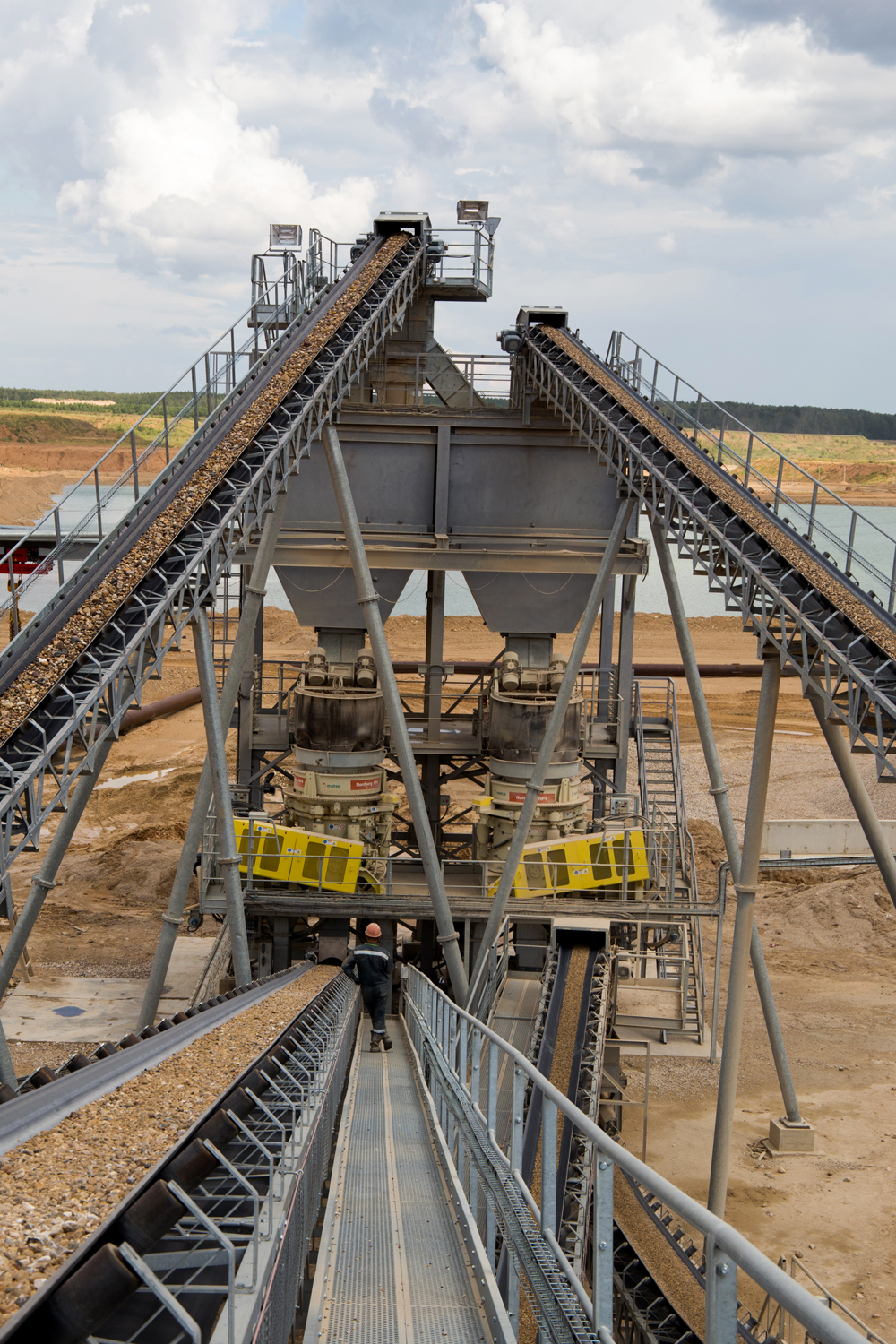
To increase the capacity of production plants while, at the same time, reducing the number of personnel, and loaders, shovels and other machines involved in daily operations, Bogaevsky management decided to agree to a Metso proposal to replace three crushing and screening plants (DSF-1, DSF-2 and DSF-3) and one mobile washing and screening facility with a single advanced crushing and screening plant capable of processing high production volumes over the remaining 25 years of the Oreshkinskoye open pit’s working life.
Metso’s work, in close consultation with Bogaevsky management, on designing the new single plant began in 2017, and, in March 2019, the plant was put into operation.
The new plant consists of a C116 jaw crusher, two HP4 cone crushers, a VG540-3V scalper, five SF-2975 sand traps (sand washers), conveyors, and key support structures and chutes, all supplied by Metso. Bogaevsky sourced their own screens and a washing barrel to work with the new plant.
“It was critical for the customer to complete all construction and installation works during the winter period to be able to reach the design capacity in early spring 2019. It was possible to meet the tight deadline due to close cooperation between Metso installation supervision personnel and the customer’s team,” stresses Alexander Soldatov, Metso project manager.
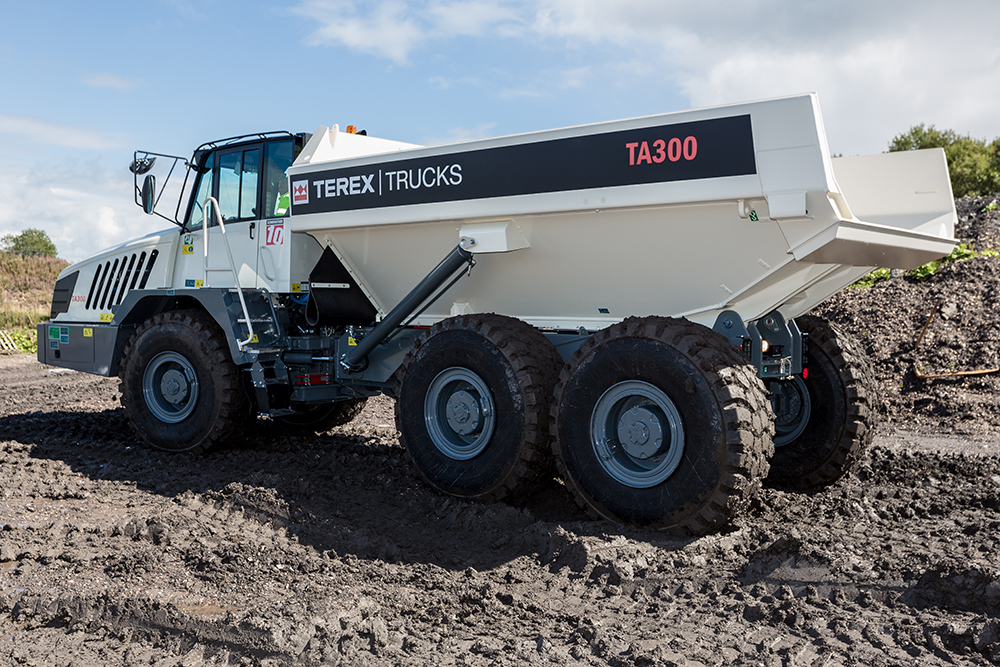
Metso developed the new crushing and screening facility, including its cutting-edge conveyor system to transfer the material from one handling stage to another and the automatic process control system, and completed its construction, installation and pre-commissioning works within the agreed period.
Since it began processing material, Bogaevksy says its state-of-the-art plant has been demonstrating high performance and gaining recognition from its product consumers.
The Bogaevsky crushing and screening plant is fully automatic, which enables mitigating the risks related to human factors and reducing downtime for maintenance. For example, Metso experts provided an automatic calibration feature for cone crushers, performed by the control circuit based on the extent of wear of cone crusher linings, which helps saving time for equipment maintenance and adjustment.
In order to ensure smooth and proper operation of the new equipment, a team of engineering and technical specialists was created at the Bogaevsky open pit and trained by Metso experts to efficiently operate the facility.
Maintenance of the plant equipment now requires only one hour per shift. Bogaevsky is also able to utilise the expertise of engineers from Metso’s Russia-based team. “It is critical that we fulfil our obligations and carefully maintain the equipment entrusted to us. This is why the efficiency of all our equipment is very high,” said Igor Gorbunov, general director of Bogaevsky Karyer JSC.
“Moreover, all the spare parts we use are supplied by Metso. It is like in that saying, ‘We are not rich enough to buy cheap materials.’ We understand that it is better to pay more for an expensive spare part today and be sure that tomorrow it will operate properly and will not fail.”
The spare parts delivery to Bogaevsky’s Oreshkinskoye open pit from the Metso warehouse in St. Petersburg takes no more than eight hours.
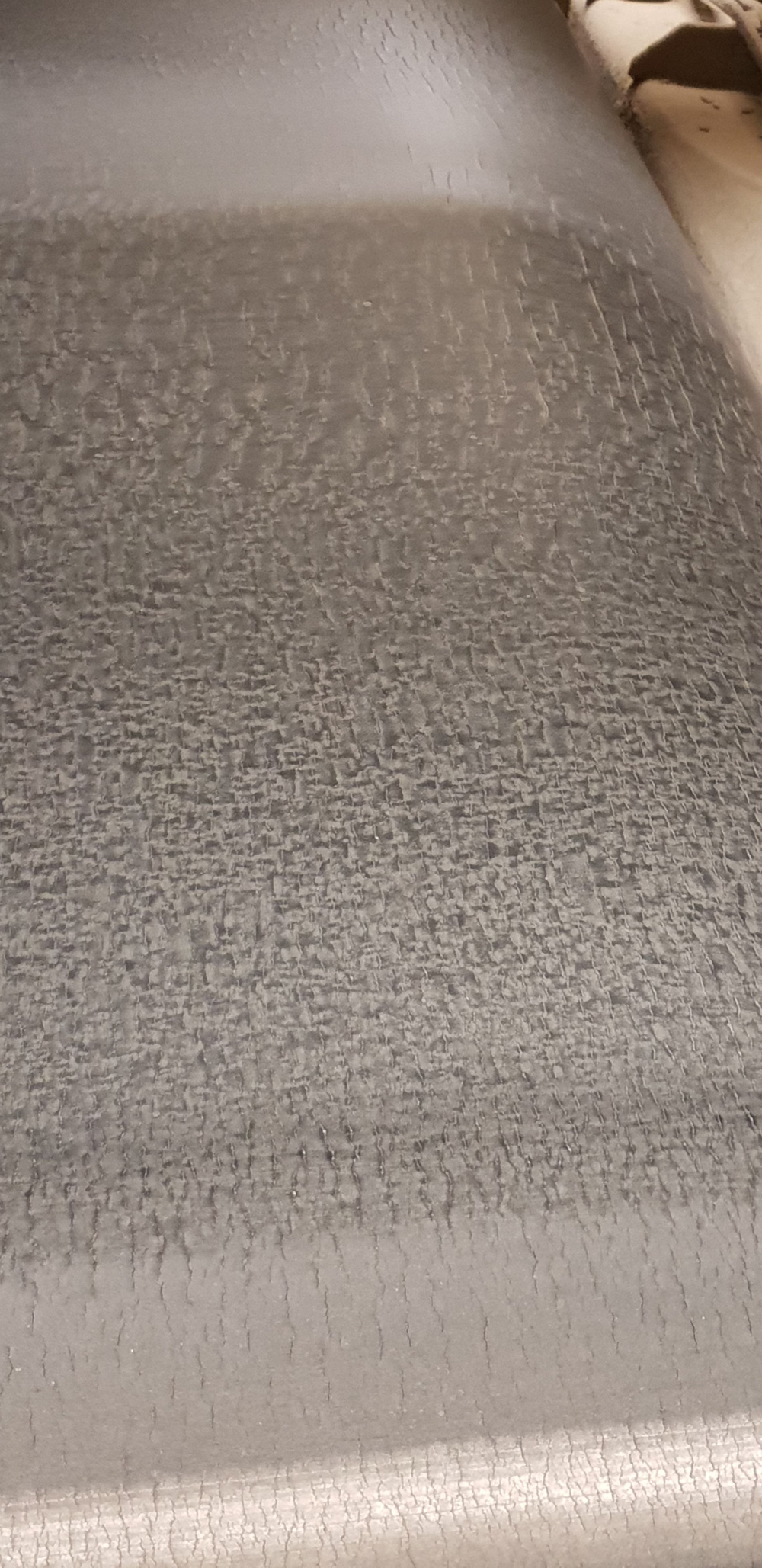
By building the new crushing and screening plant, Bogaevsky managed to successfully achieve its two goals: improve productivity while increasing production efficiency. This resulted in a reduced equipment fleet and service manpower requirement.
“Let the numbers speak for themselves. The cost of production has become lower, the production volumes have tripled, and the capacity is now higher,” said Gorbunov. “We currently produce 5,500m³ of finished products per shift. Before the reorganisation, we used to handle 8,000m³ of sand and gravel mixture daily, today we handle about 11,500m³. The average volume of products we ship today is 25,000m³ per day.
“In the past, the crushed stone flakiness was 25–28, now it is 12-15; the crushing ratio didn’t exceed 65%, now it is 85–90%. We achieved the desired production capacity in just two months of operating the new [plant] process flow.”
Gorbunov concluded by saying that Bogaevsky’s crushing and screening plant built in partnership with the Metso team is a “tight-knit, unique and exciting” project brought to life through large-scale investments.