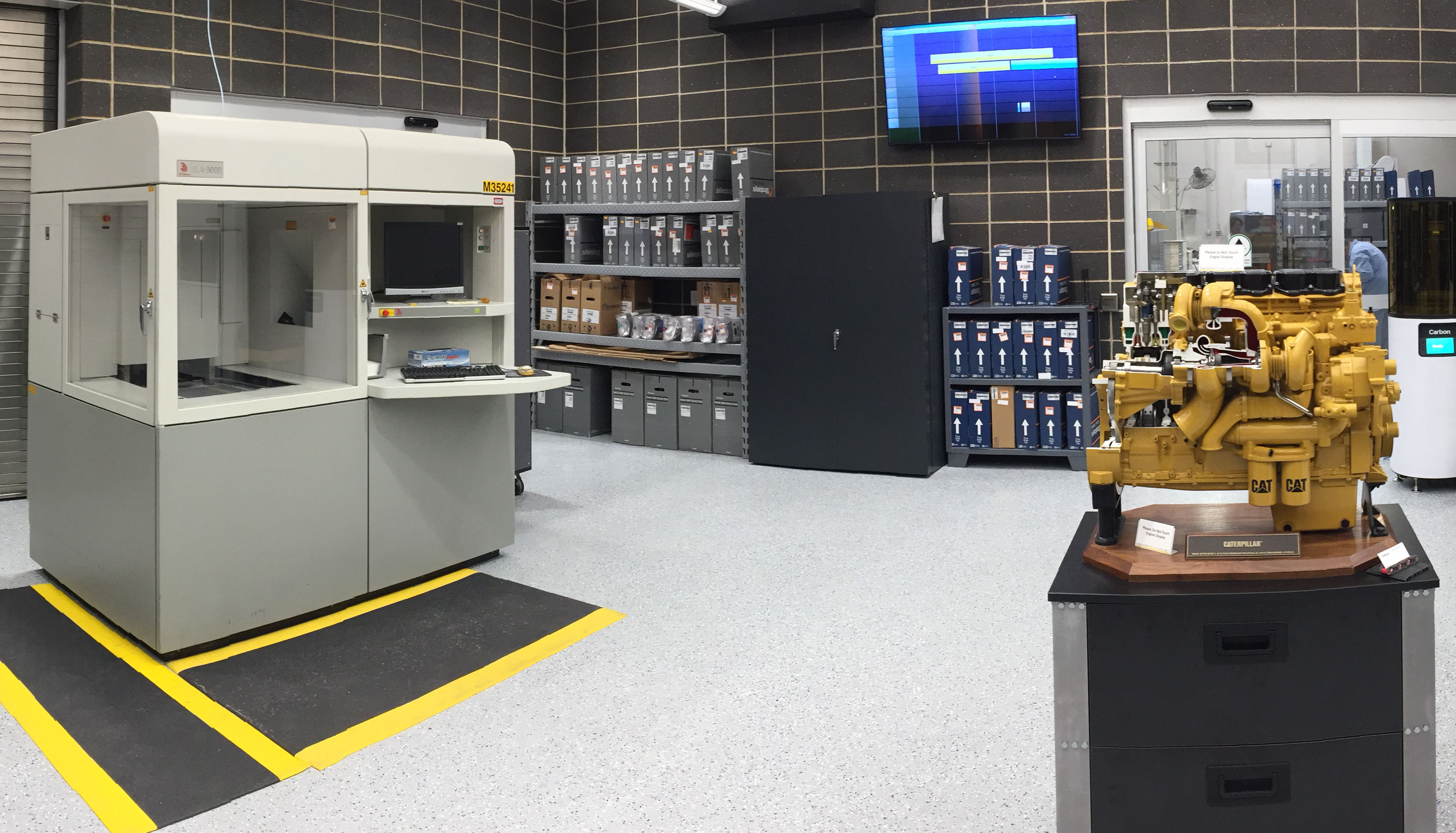
Caterpillar is investing heavily in developing its 3D machine parts printing capabilities, a move that could result in huge aftermarket gains for customers, while significantly reducing parts production costs for the U.S. quarrying and construction equipment sector giant.
Guy Woodford spoke to Don Jones, Caterpillar’s general manager of global parts strategy, to find out more about the company’s work in this innovative area of the industry.
As Don Jones states, 3D parts printing is not new to
The real excitement for Caterpillar and other leading OEMs is in working towards being able to produce spare parts close to customers. This would not only reduce lead times for customers ordering replacement machine parts, but also greatly reduce parts’ transport costs and the associated carbon footprint.
“Up until the recent past, 3D printing was used primarily for parts prototyping. An engineer would do a new design and want to see what it looks like and whether it works, before taking it for production tooling. The second area it has been heavily used in is jigs and tools for the assembly line, primarily using plastics, but we also have used 3D metal printers.
“What’s exciting now is the recent development of new printing technology for both plastics and metals. Our solar subsidiary [Solar Turbines in San Diego, U.S.] makes very large gas turbine engines and they have a fuel [injector] swirler that’s 3D-printed out of metal. That fuel swirler can’t be created with traditional manufacturing. It was designed for 3D printing. They are producing those for full production use on their gas turbine engines. This shows that technology is moving to being able to produce very complex parts in one piece using 3D printing. If you try to make complex parts in one piece using traditional manufacturing methods, you can’t afford to given the type of machines required. But 3D printers are faster and use less material. Complexity doesn’t cost anything when you can just print a part!”
Jones stresses that Caterpillar is focused on training its engineers about how they can use “honeycomb/organic structuring” to reduce the amount of materials and parts traditionally used to make quarrying and construction machines, without compromising on their strength and durability. “Organic structuring is very big in the aerospace sector,” he explains. “It’s like a bird’s bones, which are strong but very light because they are honeycombed.
“If we can design our machines with less materials and parts, the customer would still have a strong machine, but one carrying less weight, making it more efficient. We may also have one part instead of four that has to be serviced.”
Jones says he is excited about new developments in carbon fibre, Kevlar and 3D-printed plastics, the latter having the same strength as metal, while also being lighter, easily 3D-printed and made of composites that don’t rust. If these materials are successfully used in time in the manufacturing of construction and quarrying machines, Jones believes this could lead to big efficiency gains for customers.
Caterpillar has a number of different vendor suppliers that it uses in its ongoing 3D-printed parts R&D. “We have about 85 3D parts printers from a number of different vendor suppliers. We also have a strategic alliance with FIT, a German company. We are working with them on some [3D printing] metal technologies. We’re trying to reach out with some new partners as well, and keep up with the innovation. The difficulty is there are so many vendors entering the market. There have been roughly around 100 new 3D printing vendors coming onto the market in the last year; then you have big companies like Hewlett-Packard, Stratasys and GE, who are introducing new products all the time. It’s a very exciting space.”
Jones says that Caterpillar’s large array of 3D parts printers includes new sand printers that can print moulds for machine tool castings. “This means we can print with sand and not have to make machine tools. It lets us do needed assembly line production parts as well as prototyping, while also assisting with our aftermarket service. There are hundreds of parts that we’re now printing with sand moulded casts.”
Focusing on Caterpillar’s current and future aftermarket use of 3D-printed parts, Jones says: “We have about 80 3D-printed parts that we sell to our aftermarket customers. They are all composites and plastics and include some grommets, some holders, some fixtures that hold hoses, and insertion tools for oil rings.
“Caterpillar’s business model is about providing very long-life machines, all over the globe. The machines use a lot of wear parts over time, and are rebuilt several times over their lifetime. Because of that and our product breadth, we have 21 distribution centres that hold parts and support our dealers in repairing customer machines. There’s a lot of slow-moving material because of how long the machines need to be serviced, coupled with our broad product line. We and our dealers need to stock a lot of inventory to cover servicing needs.
“What we see as the real advantage of 3D printing is around providing parts globally, without having to stock the inventory. This means we can respond on demand, getting the parts to customers quicker as we don’t have to fly parts all over the planet, thus increasing their machine uptime and profitability. The big focus is on quality 3D-printed metal and plastic parts that can be with the dealer much quicker, or, potentially, even be printed locally at the dealership. The carbon footprint reduction due to reduced transportation of spare parts is also a nice sustainability win.”
Jones is not predicting a time when the localised 3D spare parts distribution model will become the norm, but he emphasises the efforts being made towards that goal. “We’re investigating this now. We want to be sure that the supply chains for the parts’ materials and the printers are functional globally, and are doing some testing around that.
“I think some of the initial, easier parts to do around a more localised 3D parts distribution model would be those where you don’t have to worry so much about metallurgy; such as brackets, fasteners and plates. You need to really look at the quality of the 3D parts printer before you get into using it on safety-related parts. High wear material and metal parts would need a lot of work before we could consider offering things like 3D-printed ground engagement tools.
“It’s fair to say, though, that the general cost of 3D printing parts has come down a great deal, which increases the ability to do higher volume.”
In keeping with the CONEXPO-CON/AGG 2017 theme ‘Imagine What’s Next’, attendees at the Las Vegas, U.S. showcase for the global construction and quarrying equipment sector held in March this year saw a demonstration of the world’s first 3D-printed excavator, known as Project AME (Additive Manufactured Excavator).
Project AME was developed at the Oak Ridge National Laboratory’s Manufacturing Demonstration Facility in Knoxville, Tennessee, to create and assemble three components: the cab where the operator sits, the boom (a large hydraulically articulated arm) and a heat exchanger.
A consortium of research teams that are part of the Center for Compact and Efficient Fluid Power (CCEFP) contributed additional design and engineering work for the project.
The idea for the excavator came about when CCEFP members toured the Oak Ridge Laboratories in 2014, and saw a 3D-printed car on display that had been produced for another industry trade show. CCEFP members brainstormed how they could make a similar splash for the fluid power and mobile equipment industry, which led to the excavator.
Jones has been following the work of Project AME, but he believes that given the complexity of metallurgy and other materials involved in constructing construction and quarrying machines, the industry is “some way off” seeing a significant portion of a machine being 3D-printed.
Jones does, however, think that if more 3D-printed parts are used in the future on a typical construction and quarrying machine, new machines will be launched onto the market quicker, giving customers earlier access to an even greater choice of models to add to their fleets.
“There is a definite benefit to the customer in manufacturers such as ourselves being able to develop prototype and then full production machines quicker with 3D printing.”