The document highlights that, while practices such as increased hygiene and social distancing may make aspects of a maintenance routine difficult, the legal obligation to ensure a safe working environment remains unchanged.
In the case of cement storage silos, these new complications come on top of several pre-existing safety management concerns. However, as well as addressing problems that arise in regular day-to-day use, a comprehensive, testable pressure safety system can also help to reduce the need for external visitors and extra site staff.
CAUSES AND RISKS
Regardless of how much has changed this year, the basics of cement industry operations remain the same. Powdered product is still transported to sites in road tankers and blown under pressure into silos. This action risks the over-pressurisation of the silo, either due to excessive input pressures from the tanker or due to the neglect and poor maintenance of essential equipment such as pressure sensors, filters and pressure relief valves.
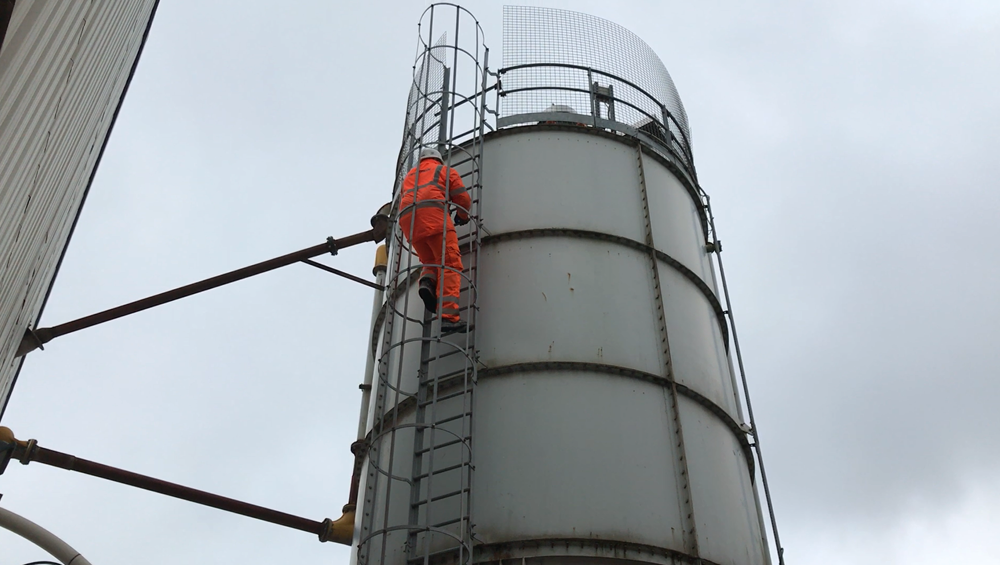
Over-pressurisation is the root cause of numerous on-site hazards, ranging from powder leakage to buckling silos. It can even cause filter units (frequently weighing more than 80 kg) to blow off the silo roof, leading to potentially fatal injuries. Silo over-pressurisation has been a significant but often unaddressed problem worldwide for many years, and, despite the reduced level of cement production during the current pandemic, it remains a direct threat to staff health and safety. It may only take a single uncontrolled tanker discharge to cause a staff fatality.
To prevent such a disaster, and to control the pressure during the delivery and alert users if anything goes wrong, a silo protection system is needed. The purpose and functionality of such systems have been discussed at length elsewhere, but we will recap them in brief.
A silo protection system (commonly abbreviated to SPS) is an integrated safety system for controlling and monitoring both the pressure and level in a vessel. Its primary functions are to test essential silo safety equipment such as the pressure sensor and emergency relief valve, to monitor the pressure levels during a tanker delivery, and to automatically take steps to prevent damage to the vessel if that pressure becomes dangerous.
WHO ARE YOU LETTING ONTO YOUR SITE?
The new HSE guidance states that “thorough examination and testing continues to be a legal requirement” to maintain continued safe operation. A silo protection system, like any piece of safety equipment, is only as reliable as the last time it was tested.
Many sites engage third-party engineering companies to undertake their testing and maintenance. Unfortunately, this means having additional external personnel on-site, which, in the current circumstances, many sites are trying to avoid. Testing vital safety equipment is a necessity, but one that may impinge on social distancing requirements.
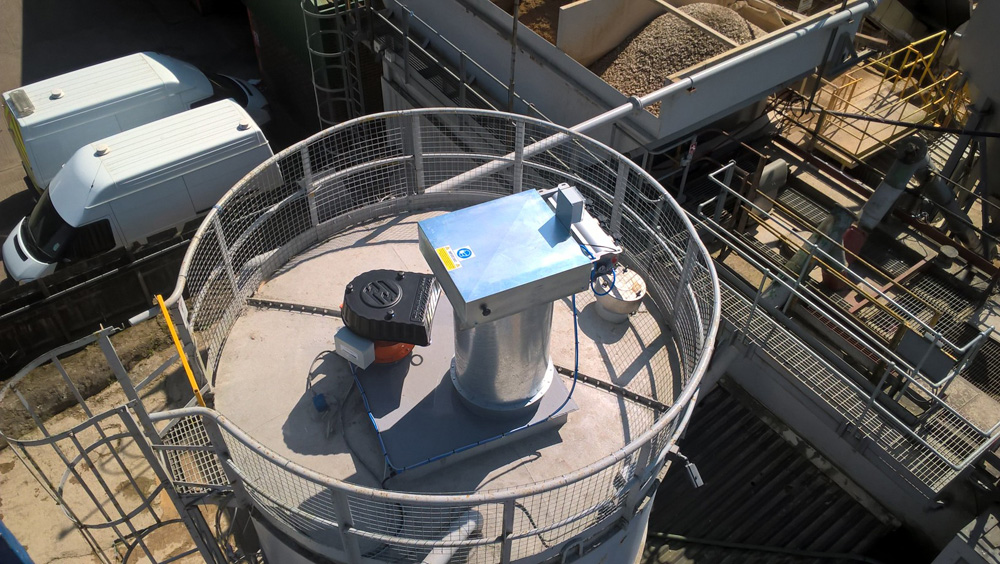
Worse, most third-party servicing companies lack expertise in silo pressure safety equipment. They are only cleaning the safety equipment to fulfil a checklist rather than properly testing its functionality – meaning their visits are pointless! These facts will be a serious concern for those looking to minimise the risk of coronavirus exposure for their workforce and having to justify third parties visiting a site. Not only is the risk of infection increased, but the risk of over-pressurisation leading to a vessel rupture or filter ejection remains the same.
TESTING IN ISOLATION
Under the current circumstances, the ideal number of staff required to undertake most tasks is just one. What is needed is a simple method for site staff to test safety equipment on their own, without having to endanger themselves by climbing a silo or bringing in extra personnel.
One proven method of achieving this is through the use of GLT (Ground Level Test) technology. Hycontrol silo protection systems are designed around this core concept. As the name implies, this facility enables a single plant operative to test all the safety and monitoring equipment on a silo with both feet safely on the ground.
A good SPS should be easy to use, with the minimum of training required. With the Hycontrol system, one key turn before the commencement of a delivery cleans and tests the pressure sensor, cycles the pressure relief valve open and closed, checks the level sensor is working and confirms the airflow to the filter unit’s cleaning jets. Once all critical components pass the GLT (the whole routine takes less than six seconds), the inlet valve will open for the delivery, and the system will continue to monitor the pressure.
Silo protection systems with automated Ground Level Test facilities check all essential safety components before every delivery. Testing every time means equipment servicing can be kept to a minimum, helping to minimise the number of external contractors on your site, as well as reducing working at height and costs of maintenance. Together, these benefits help to promote site safety and make solo working easier.
CONCLUSION
We are in an unprecedented situation that is changing rapidly – doubtless, things will be different when you read this article from how they were when it was written in June 2020.
But: many more things will remain the same. Cement will still be an essential commodity. It will still be transported by truck and stored in silos. These silos will still be at risk of over-pressurisation, and there will still be a legal and moral requirement to ensure site safety through proper testing and enforcement of best practice.
Silo protection systems that any single member of site staff can efficiently operate are already available; equipment that keeps them safe from pressurisation dangers and prevents them from having to climb the silo to test it. It also cuts the need for additional personnel to visit the site while fulfilling HSE obligations. Using a safety system that does all of this was a good idea before the pandemic began, and it will remain a good idea after it is over – hopefully, sooner rather than later!