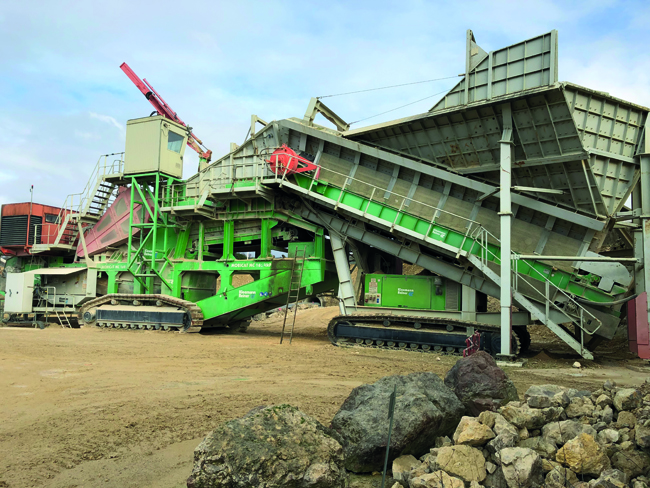
The massive
The Prasville limestone quarry near Berchères-les-Pierres in France has a machine that makes it almost unique.
The quarry site, which is close to Chartres and one of three in the vicinity operated by construction company SMBP (Société Matériaux Berchères Les Pierres), is home to a giant Kleemann Mobicat MC 162 RRP mobile crushing and screening machine that can process 1,000 tonnes of material per hour. Only two such machines have been deployed, with the other operating at a quarry in Chile.
The Mobicat MC162 RRP at Prasville, which was purpose-built for the quarry, features a 1.62m jaw crusher that produces rock in varying sizes up to 300mm at the end of the crushing and screening process. The machine has been in operation since 2000 and has racked up 20,000 hours of production.
In addition to Prasville, SMBP operates two other quarry sites near Berchères-les-Pierres - Viabon and Moulin de Pierre. Prasville produced 300,000 tonnes of material in 2018 while the other two sites produce 500,000 tonnes each.
The three quarries cover a total area of 150 hectares. All three sites produce limestone that is used to make cement and aggregates for road and transport construction in the Paris area. This includes supplying the giant Grand Paris Express (GPE) project which is designed to meet the growing city’s needs for an improved transport infrastructure and prepare Paris for the 2024 Olympic Games.
The sites operate a three-stage process to quarry the limestone, which involves crushing twice with a jaw crusher and once with an impactor. All the aggregates are then washed and screened for final grain size.
SMBP also operates one other Kleemann machine at the Viabon site, a 160-tonne Mobicat MC 125 RR crushing and screening machine. The single-jaw crushing unit is capable of processing feed material of up to 1,250mm x 1,000mm in size, and of achieving production rates of up to 700 tonnes/hour depending on the feed material to be processed.
The Mobicat MC 125 RR mobile crusher is equipped with a wobbler feeder for thorough pre-screening of adhesive feed material. The machine has operated at the quarry since summer 2016 in the preliminary crushing stage. The limestone with a size of 0-900 mm is fed to the elliptical rollers in the first stage of the wobbler feeder. At the same time, contamination and dust are removed from the stones.
The material is levelled and then conveyed to the second stage of the wobbler feeder for further cleaning and better material distribution. The fines with a size of 0-80 mm fall through the rollers onto a conveyor belt and leave the process via the side discharge conveyor, which reduces jaw crusher wear. A total output of 600 tonnes an hour is achieved. The oversize grain is crushed to 0-300 mm and then further processed by a stationary plant for concrete production.
Kleemann offers its mobile crushers and screeners with diesel-electric power that run from the grid or with diesel-hydraulic electric power. “Customers choose electricity as it is cheaper than diesel fuel and they don’t have to do any maintenance,” says Vincent Levesque, area sales manager Kleemann for the Paris area at
Levesque says that the market for large mobile crushers and screeners that can process huge amounts of material is likely to remain a niche one. “You need a very big quarry to operate these machines,” he adds. He adds that there is a lot of demand in France for Kleemann’s smallest machine, the 39.5-tonne Mobicat MC110 Z EVO mobile jaw crusher and primary screener, as it is easy to move around different job sites.
In addition to the mobile crushing and screening machines, there are more than thirty wheeled haulers, excavators and loaders at the three sites, with the vast majority being
Prasville operates three Caterpillar 771 haulers, which can each carry loads of up to 45 tonnes, in addition to a Cat 980 wheeled loader.
Apart from the Cat vehicles, two
Prasville quarry manager Franck Désiré-Laye said that SMBP is in discussions with Kleemann about another large mobile crushing and screening machine, the MC 160 RR, which would be deployed by 2025.
“We have had a lot of contracts to supply large quantities of materials,” he added. “In the future we will have two machines each producing 1,000 tonnes per hour, which will meet our production needs."
While the three sites sold a total of 1.3m tonnes of material in 2018, they have government authorisation to produce up to 3.4m tonnes per year.
SMBP is a family company, which originally started as an earthmoving business in 1978 before moving into quarrying around 30 years ago. It has four competitors within a 20km radius who also operate limestone quarries.
“Limestone quarry customers want crushers and screeners together,” says Levesque. “There is a lot of sand in limestone, and they have to remove the sand with the screener and then crush the rock. For granite quarries it’s different. There is no sand so you don’t have to screen it and only need a crusher.
SMBP is planning to build a static installation at Viabon for crushing and screening. The machine will involve an investment of around €25m and is due to come into operation by 2024.
“We have our own mechanics and do a lot of preventative maintenance on the machines,” says Désiré-Laye. “We analyse the motor oil all the time. For tyres and oil we order a large amount at a time to get a lower price.”
When asked what specific things he looks for from a quarrying vehicle supplier, he responds: “The design of the machine is important, the after-market service, the parts department, and the cost per hour of production.”
In terms of future plans for the Berchères-les-Pierres quarry sites, Désiré-Laye says he would like to see an increased use of telematics.
“We already have telematics on our Caterpillar vehicles,” he says. “This gives us information on fuel costs and hours of use of the engines. At the moment we don’t have telematics on our crushers and screeners as the lack of wi-fi communications at the quarries makes this difficult.”