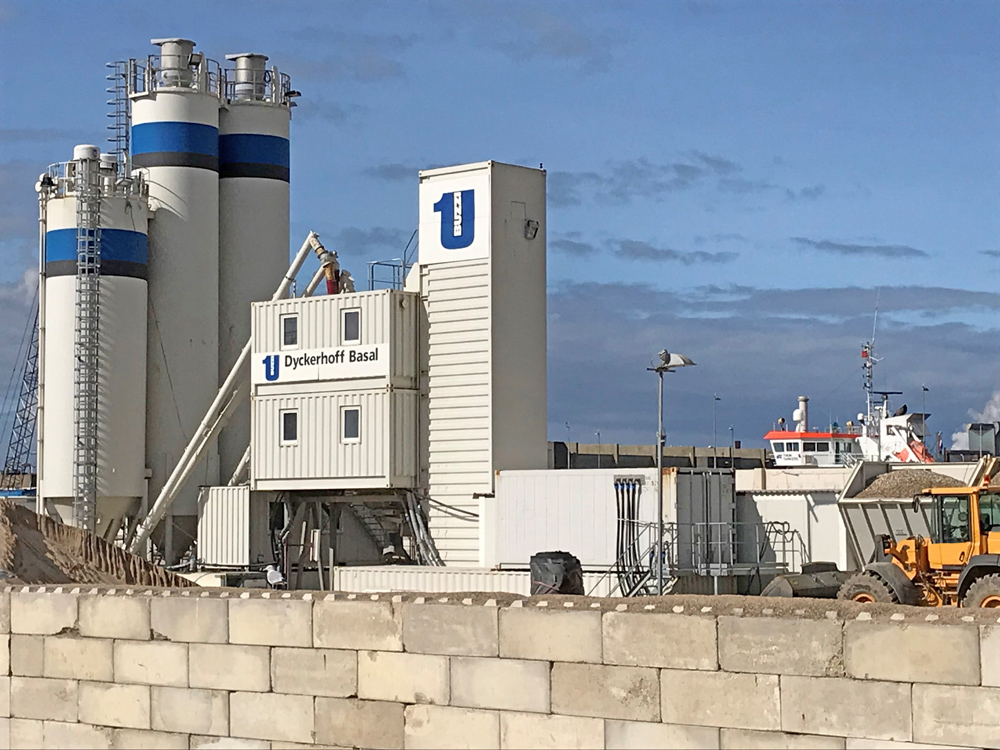
A highly mobile concrete mixing plant has been proving its capabilities in the Netherlands.
Dyckerhoff Basal is the Dutch subsidiary of cement manufacturer Dyckerhoff and is a major supplier of ready-mix concrete and cement in the Netherlands.
In order to make the port of Amsterdam accessible for the new generations of ships with even larger dimensions, what is claimed to be the largest lock in the world will be built in IJmuiden. The port city of IJmuiden is located at the south of the 27km-long North Sea Canal, which connects Amsterdam with the sea.
The construction project comprises an investment volume of around €700m and is expected to take around seven years. The new lock is to be opened for shipping at the beginning of 2022 and requires around 300,000m³ of concrete.
For Dyckerhoff Basal, the most important criterion in selecting the concrete mixing plant was a rapid start of operation and the possibility of a rapid change of location in the future in order to be able to start concrete production at short notice for construction projects with limited time. In addition, a theoretical output capacity of up to 150m³/h was an essential requirement for the mixing plant in order to reliably cover delivery peaks throughout the day.
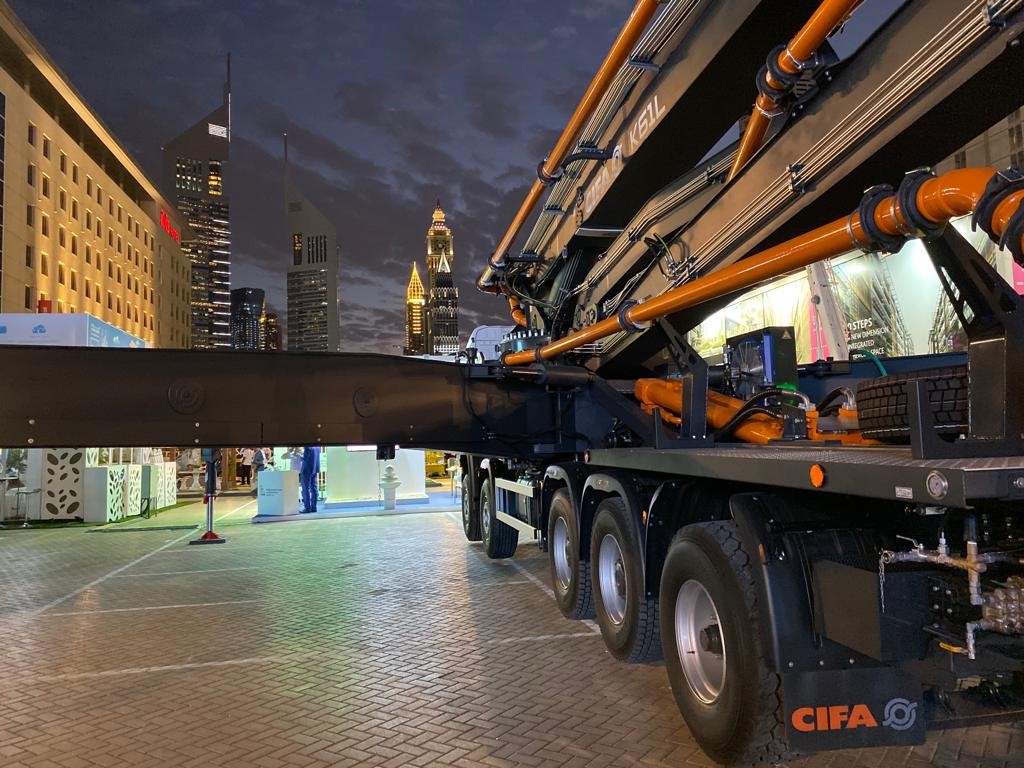
Dyckerhoff Basal has selected the Liebherr Mobilmix 3.5-C in container design with CSC (Concrete Sustainability Council) approval for cost-effective and worldwide ship transport. The container design and installation on steel foundations are aimed at making the Mobilmix 3.5-C suitable for quick installation and relocation in temporary construction projects.
The plant can be relocated within four days. Thanks to the already integrated insulation, the Mobilmix 3.5-C is also equipped for winter operation. The mobile mixer is equipped with a Liebherr DW 3.5 twin-shaft mixer, which is designed to enable optimum concrete homogeneity thanks to the three-dimensional mixing principle. In addition, the mixer is suitable for short-term recipe changes.
With the Mobilmix 3.5-C, up to 150m³ of concrete can be produced per hour, and as a double plant even up to 300 m³. The plant is operated intuitively via Liebherr‘s own Litronic-MPS mixing plant control system at a PC workstation. All components are accessible for maintenance work via steps and platforms and are designed to offer sufficient space for tools and working equipment.
Italy-based concrete machinery design and manufacturing company CIFA has inaugurated its branch office in North America. The CIFA North America facility which is located in Yorkville, Wisconsin, will work as an industrial machinery assembly plant as well as the customer service centre. CIFA says the local hub will provide service in terms of sales, parts supply, technical support, service support and training with high quality and efficiency for customers in the US and Canada.
Marco Polastri, sales, after-sales & marketing director of CIFA, commented: “North America is of great strategic interest for CIFA, and we aim to increase our market presence in the United States and Canada. Being in the area with a stronger local presence is of the utmost importance in order to provide quality products and service to satisfy the needs of our customers.”
CIFA has also been promoting its presence in the Gulf region, which it says is a strategic market for the company with the potential to increase in the forthcoming years. It adds that the Gulf is an advanced market with very well-organised groups, dealers and end users that will keep pushing towards the latest technologies and high-standard products.
CIFA is a main sponsor of the Big 5 building and construction show that was staged in Dubai from November 25 to 28. The company also exhibited at the event, where it presented for the first time the new K61L truck pump, which is suitable for markets requiring long, tough truck pumps with high performance. It features a pumping unit with 25.4cm S valve and 260mm concrete cylinders that are designed to provide lower cycles per minute, low wear and low noise level during operations. The K61L features CIFA’s Smartronic Silver machine management: LCD monitor, user-friendly interface with counters, pumping unit management and advanced diagnostics.
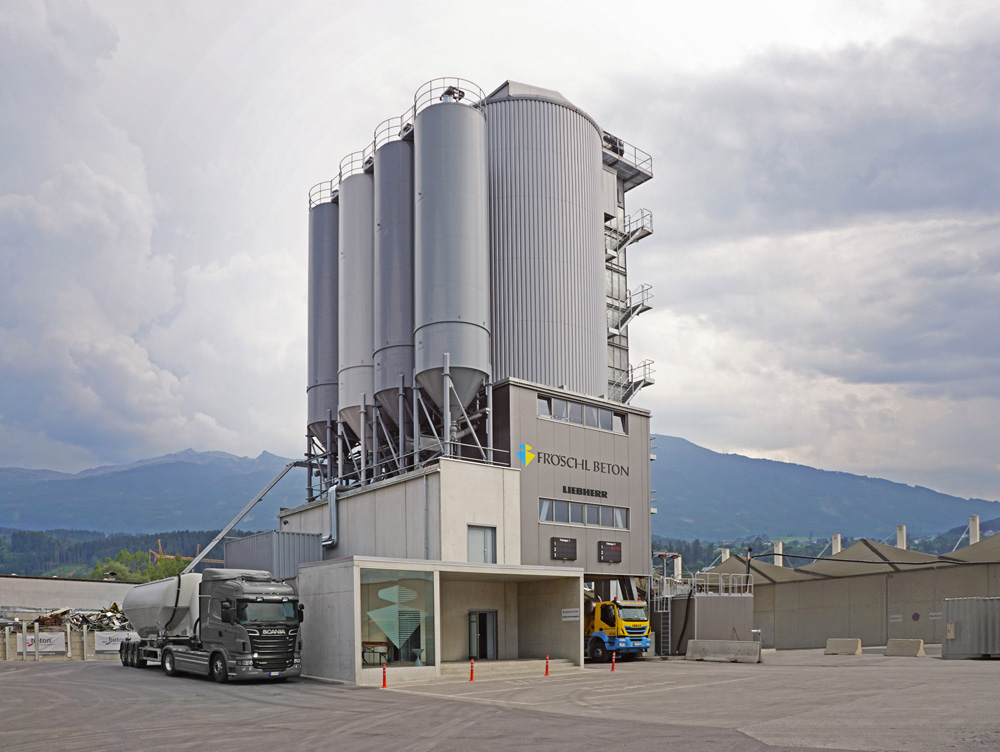
In Austria, the Fröschl Beton company has been supplying construction sites in the Innsbruck area (Austria) with ready-mixed concrete for many years. Its 45-year-old mixing plant was technically obsolete and no longer met current standards. The company wanted to replace it with a set-up that covered the entire concrete logistics chain and delivered flawless concrete efficiently and flexibly.
After an extensive planning phase, the Betomat concept from Liebherr was chosen. It enables the operation of two completely separate mixing plants within one mixing tower, and incorporates a compact design of the two weighing and mixing lines.
The Betomat holds up to 600m³ of stone in nine silo chambers. The mixing tower is fed with aggregates via two charging hoppers and a powerful bucket elevator with an hourly output of 200m³/h. The plant has seven silos for a binder supply of around 840 tonnes.
The new mixing plant is equipped with two mixer systems: a ring-pan mixer with agitator system and a double-shaft mixer. Liebherr says this means that normal standard concretes as well as high-performance and special concretes can be produced very efficiently. When in operation with both mixer systems, the plant achieves a possible output of around 160m³ of compacted fresh concrete per hour. The tower is equipped with two lanes, and the separate weighing lines mean that two vehicles can be loaded simultaneously with different types of concrete.
Northern Ireland-based Rapid International has re-entered the concrete truck mixer market with the launch of its sister company Rapid Tumbler which supplies premium lightweight truck mixers.
Rapid Tumbler’s first product to market is the RTM89 8m3 capacity truck mixer. The mixer’s 8m3 mixing drum is manufactured using long-life, high-strength Arcelor Mittal steel. The truck mixers feature premium components from Bosch Rexroth, Arcelor Mittal and ZF Germany. Rapid says the range is set to be expanded in 2020 to include other size options. The official launch of Rapid Tumbler took place in December 2019 at an open morning at Rapid’s headquarters in Tandragee, County Armagh. The event was attended by many local and national readymix concrete companies, as well as members of the Mineral Products Association Northern Ireland (MPANI).
Rapid International MD Mark Lappin expressed his delight that the company was re-entering the truck mixer market with the launch of Rapid Tumbler. “Having celebrated our 50th anniversary last year, it seems fitting to re-introduce one of Rapid’s original iconic products,” he added.
Garten Richter, a German company involved in construction work and concrete projects, has acquired a Carmix 3.5 TT concrete mixer truck for the production of eco-friendly blocks from recycled materials that are in the shape of LEGO bricks.
The LEGO blocks the machine produces have enabled Garten Richter to easily build compartments for different aggregates, while at the same time optimising site management and material organisation.
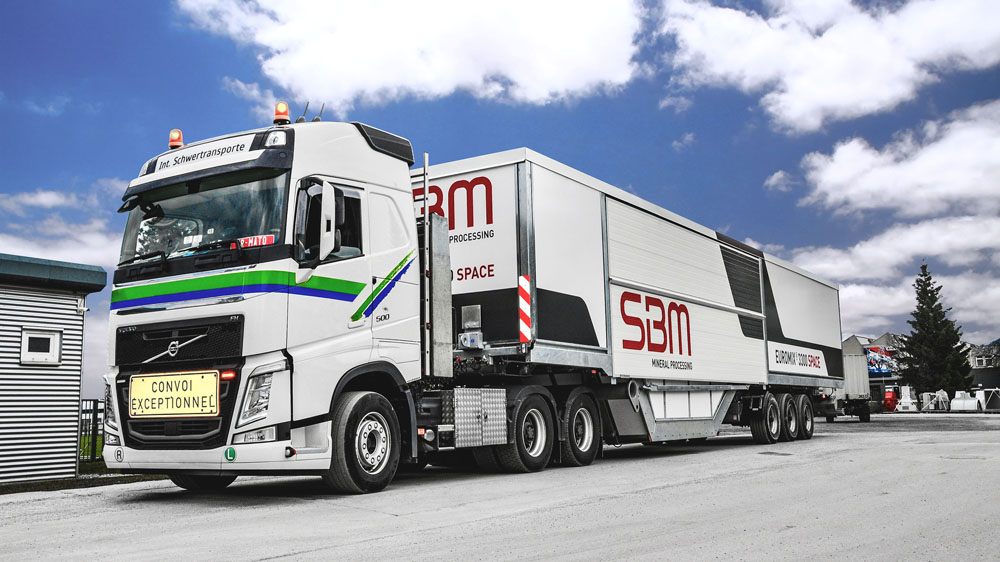
Carmix claims its machines reduce concrete costs compared with existing mixing methods, have a greater capacity than screw mixers combined with tractors or other mini-loader machines, and also simplify the mixing and unloading phases for more efficiency. In one working cycle, the Carmix 3.5 TT concrete batching plant chosen by Garten Richter produces concrete for five cement blocks, whose mixture is composed of 5,580kg of recycled material sized 1 to 12mm, 410l of water and 920kg of cement, to a final concrete resistance of C25/3 kp.
SBM Mineral Processing presented its EUROMIX 3300 SPACE mobile mixing plant for the first time at bauma 2019. Stephan Godel, MD and founder of German concrete producer GODEL-BETON, purchased one of the plants after seeing it at the construction and quarrying equipment event in Munich last April.
A few days later the machine was in operation at the GODEL location in Gelsenkirchen, Germany, and has since then been producing up to 1,000 m³ concrete per day.
Zacharias Funk, head of systems engineering at GODEL, set up the plant with his team in less than two days. “I think that under optimum conditions it is possible to produce concrete in only three days after the first transport,” said Funk.
The EUROMIX 3300 SPACE is provided with an insulated cladding as standard to ensure better production and operating conditions.