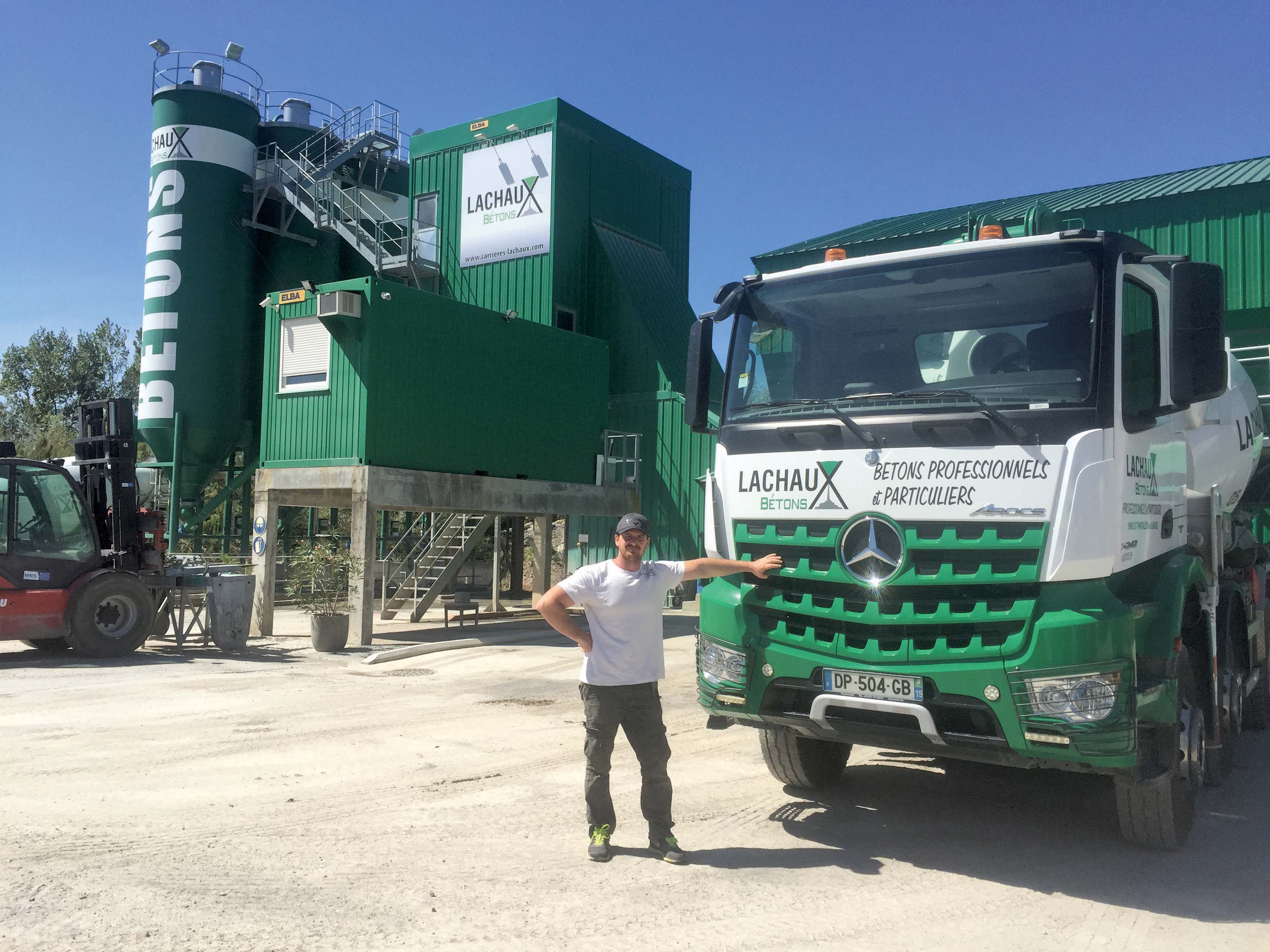
Depending on what it is used for, the material, with its basic ingredients of aggregates, cement and water, can be blended into any amount of mixes with a variety of strengths and different densities.
As the use of concrete has developed so too has the equipment used in its production, which has become more sophisticated, and capable of producing vast quantities of what is one of the world’s most flexible building materials.
Carrières Lachaux, a family company located in Vinevialle, near Brive, south-western France, dates back to 1948, when its business focused on aggregates. Pressure in this segment caused demand to drop and in 2011 the company decided to diversify into the ready-mix concrete market by establishing Lachaux Bétons.
“We have always been renowned for the quality of our products and our service,” says Vincent Lachaux, the company’s general manager for concrete and aggregates.
Continuing to foster this philosophy was a key factor. Lachaux Bétons knew that a high-quality, dependable plant was essential to fulfilling its promises to customers.
This commitment to customer satisfaction also led the company to make deliveries with its own fleet, comprising four truck mixers and two mixer pumps, a service that ensures deliveries reach customers on time.
Achieving maximum success in the new business called for a plant that would meet Lachaux Bétons’ needs perfectly, and that meant turning to a plant manufacturer with a range that could meet every challenge, one factor that prompted Lachaux Bétons to explore working with
“This company offers a vast range of products and options, so we were certain of finding a solution that would meet our needs,” says Vincent Lachaux.
“We wanted to purchase a turnkey solution, including several items of special equipment. For instance, we wanted a stairway that would enable our technicians to access the tops of the silos with maximum safety. We also wanted to cover the linear bin so as to prevent dust and maximise our environmental effort.”
Opting for a single supplier is much easier than brokering the purchase of each individual component, and “Ammann Elba met all our expectations.”
The Lachaux Bétons team was interested in Ammann Elba products, so it visited a number of plants to see them operating in real conditions under day-to-day pressures.
Once all the factors were considered, Lachaux Bétons chose the Ammann Elba EMAD 105 with a 2m3 mixer and four cement silos: access to the filters is easy thanks to the stairway.
The 5 x 35m3 linear bin for aggregates is enclosed and covered. There is a lateral appendix, used as a technical equipment room, with a retention zone for additive storage. The EMAD 105 is a fully-covered green plant that meets all environmental requirements.
Since the plant began operating, it has guaranteed the flexibility needed to deliver concrete of all types to the area’s diverse customer base. It also meets the required quality and productivity goals.
“We had no problems whatsoever in delivering 6,000m3 of concrete for the new aquatic centre in Brive,” says M. Lachaux.
Today the Lachaux Bétons team is happy with its decision to enter the ready-mix market and to opt for an Ammann Elba EMAD 105 plant.
Environmental protection; reduced energy consumption; the use of recycled materials, and reduced emissions are the main ecological objectives of Swerock, one of Sweden’s largest groups specialised in the production, transportation, and installation of concrete for the construction industry.
The issues were the underlying theme of a meeting held at the Swerock head offices in Rosersberg, Stockholm County, following the purchase of two
The group, which employs some 900 people, has various concrete and aggregate production plants throughout Sweden, and a considerable fleet of mixer trucks and vehicle-mounted pumps.
Hans Orest, manager in charge of Swerock’s vehicle-mounted pumps and mixers department, says that the recent purchases, and 2015’s purchase of two new truck-mounted pumps (a CIFA K31 and K45 Carbotech), show how Swerock group is attentive to the innovative and technological aspects of its machinery.
One Energya unit is being employed in the Stockholm area, and the other in the south of Sweden, where the concrete market is growing in both the public and private sectors.
The Energya units are also said to represent a combination of green technological innovations, and are mounted on
Among the many attendees at the Swedish event were Carl Fredrik and Måns Sjödahl, respectively the owner and sales representative of Modern Betong, a CIFA dealer in Sweden that played an important role in the sale of the two machines.
A high-performance mobile concrete mixing plant from Austrian company
On the upper course of the River Inn a prestigious hydro-electric power plant is being constructed at record speed, with major construction companies hoping an annual 400gigawatt hours of electricity can be gained from domestic hydro-power starting from 2018.
One section of the project is a 23.2km-long headrace tunnel with a diameter of 5.8m. Truck transports of about 1 million m³ of excavated material are kept to a minimum as the material suitable to produce concrete is processed directly on site for environmental reasons.
Construction company Hilti & Jehle, responsible for this part of the project, has been operating its SBM LINEMIX 3000 to produce the required concrete since June 2015.
“Only such a powerful and reliable plant can produce a total of 120,000m³ high performance concrete for 50,000 tubbings in time in year-round 24-hour-operation,” says Jürgen Steinhauser, responsible project manager of Hilti & SBM.
The LINEMIX 3000 can produce 420m³/day of special concrete, meaning that up to 180 reinforced concrete tubbings, each weighing 5,000kg, can be produced each day in the specially-built field factory. The high-precision fit tubbings are assembled into rings.
In summer and in winter operation (up to -25°C), SBM says the plant assures the necessary fresh concrete temperature of 28°C at a maximum temperature deviation of only +- 2°C. This is possible due to a material deposit with insulated container hopper allowing for adjustment of the temperature by heating or cooling. Controlling the temperatures of all additives such as rock, cement or water assures optimum consistency of the special concrete.
Another development comes from
Trakmix is a track-mounted, totally mobile and self-contained, fully-weighed, high volume mixing plant, which Rapid says was designed in response to the growing demand for a mobile continuous mixing plant which provides “easy, cost-effective transportation and eliminates the need for special transportation permits.”
Customer demand also indicated a need for a machine providing more options on outputs on a different platform, offering flexibility for a wide range of site types and applications, says Rapid International.
The company says Trakmix features a number of innovative, patent-pending features, including a controls system that weighs all materials and double hopper cement weighing system.
Trakmix offers outputs of up to 250tonnes/hour via a continuous Rapid Twin Shaft mixer and 12m³ aggregate hopper, which includes a division plate for two different types of aggregates.
An integral 600litre water tank and provision for admixtures is also included.
In the Cambodian capital Phnom Penh three
The HB37A pumps, with pumping capacities of 138m³/hour, were mounted and an