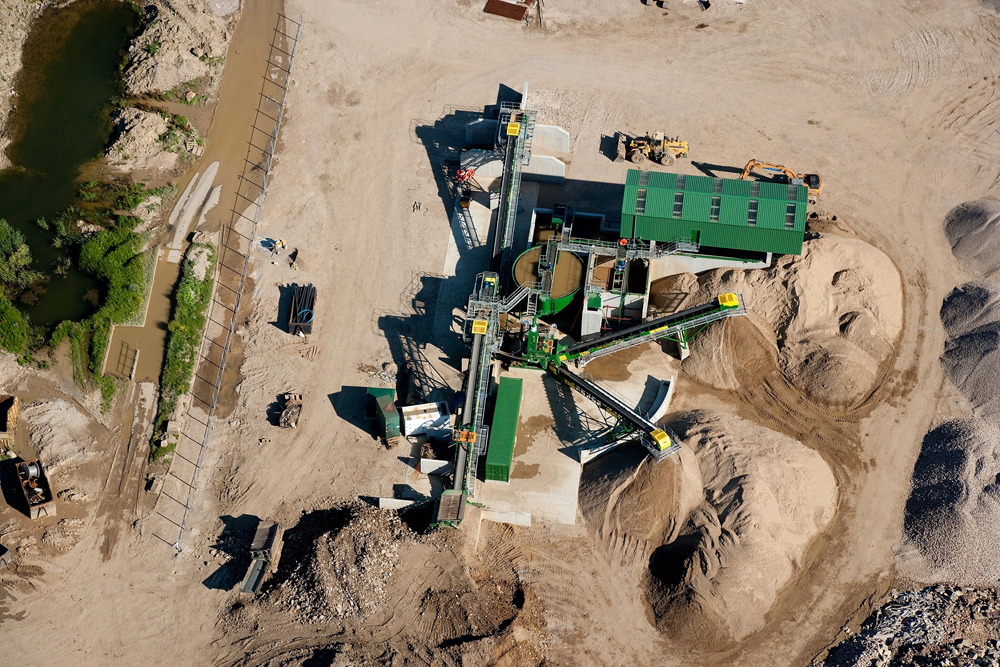
According to the latest Mineral Products Association (MPA) figures, 28% of the 250.9mn tonnes of aggregates supplied to customers in the UK in 2018 was recycled and secondary (R&S) aggregates. Within that impressive figure, 25% was recycled and 3% secondary aggregates (china & ball clay waste, colliery spoil, fly, furnace and incinerator bottom ash, iron & steel slag, slate waste, clay & shale, chalk). That UK R&S percentage of overall annual aggregates supply was the highest in Europe in 2018, with France a close second on 27% and Netherlands third on 24%.
The rise of the European and wider world recycled aggregates market complements the sustainability agenda of some of the world’s biggest building product makers. The likes of CEMEX, LafargeHolcim, HeidelbergCement and CRH have all committed to ambitious carbon emission reduction targets across their global operations.
The above quartet and other significant cement producers contribute to the Global Cement & Concrete Association (GCCA)-coordinated Innovandi Global Cement and Concrete Research Network. Innovandi has brought together 40 top scientific and academic institutions and 30 industry partners to develop new ways to aid the sectors’ lower carbon emissions goal.
The Sheehan Group, a leading British construction materials and plant hire company, has called on the UK construction industry to increase its use of recycled products following the news of another national materials shortage.
The UK Construction Leadership Council confirmed in April 2021 that cement, aggregates and plastic products had been added to the growing list of essential items in short supply, which already includes tiles, bricks, timber and steel.
The Builders Merchants Federation and Construction Products Association warned high demand for construction products combined with supply issues mean challenges will worsen in the short term. A shortage of raw materials was cited as part of the problem.
Following these warnings, the Oxford-based Sheehan Group is encouraging contractors to source local recycled products and supplies to reduce the UK’s over-reliance on global supply chains, improve the environment and support local jobs.
Tara Sheehan, finance director at the Sheehan Group, said: “This is the latest challenge the UK construction industry has been hit with due to an over-reliance on the global supply chain. It is leading to contractors struggling to obtain materials and hampering our economy at a time when the country needs to bounce back.”
She added that the Circular Driven Economy is key to long-term sustainability for the construction industry and the environment. Sheehan said that if more construction companies embraced its core principle of keeping resources in use for as long as possible, it would help make the UK market more self-sufficient, protect the environment and jobs.
“The UK is over-reliant on raw materials and imported products,” she said. “But we can take greater control by using recycled materials. We produce recycled aggregate, sand, concrete, and blocks used in construction projects and have seen the benefits first-hand.”
The Sheehan Group has a water treatment facility used to wash construction and demolition waste destined for landfill, turning it into reusable aggregate and other products. Half of the recycled material is used in its construction projects, and the rest is sold to contractors.
Quarrying equipment manufacturers see increased business from customers looking for recycling application-suited crushing, screening, and washing plants, complemented by highly productive and ultra-efficient loading and hauling machines.
A new Hyundai HL960A wheeled loader is said to be proving its worth handling a wide range of recycled aggregates at G Webb Haulage’s Little Paxton quarry site in Cambridgeshire, England.
The loader is helping meet increasing demand from developers for recycled aggregates, which can meet a specification at a fraction of the cost of virgin material.
While offering a range of recycled aggregates from Little Paxton, G Webb Haulage also operates a virgin stone quarry and a second recycled aggregates facility nearby.
The new Hyundai HL960A wheeled loader is already a firm favourite of the longstanding operator and Little Paxton site foreman Nigel Missen.
To handle the large amounts of incoming and outgoing materials, the company relies on a single, frontline wheeled loader. “We have had a number of machines over the years but have recently settled with Hyundai,” Missen explains.
Replacing an 18-month-old HL960, the new HL960A, supplied by local Hyundai dealer Willowbrook Plant, is kept extremely busy five and a half days a week.
The huge Little Paxton quarry contains a massive variety of recycled aggregates and soils ready for dispatch. Incoming aggregates are also catered for with a small processing area occupied by another Hyundai - an HX140 feeding a Sandvik crusher and McCloskey tracked three-way screener.
The arrival of the new loading shovel has seen the older HL960 machine retire to a slightly more sedentary life within G Webb Haulage’s fleet. The company runs a fleet of over 50 wheeled and articulated tippers and a small fleet of earthmoving equipment for both the quarrying activities and outside earthmoving projects the company picks up to service its local operations.
The large Little Paxton site and the variety of materials processed requires the HL960A wheeled loader to be flexible and agile. “With the amount of material we dispatch on a daily basis, having dedicated bays for each material wouldn’t be possible as we stock hundreds if not thousands of tonnes of the most popular products,” says Missen. “This means we need to be travelling from one end of the site to the other, sometimes after each truck. The Hyundai HL960A is ideal for this; it’s the right size for the site to give us the perfect combination of manoeuvrability and performance.”
With an operating weight of 19.2 tonnes, the HL960A carries a straight-edge bucket with a capacity of 3.3m³. Many heavy-duty and light material buckets are available for other applications, but G Webb Haulage feels the general-purpose unit fits their needs exactly.
The HL960A is powered by a new Stage V emission-compliant Cummins B6.7 diesel engine, delivering 168kW. The Cummins engine delivers slightly more power and has increased its torque output by 15% over the outgoing HL960 model. Meeting the Stage V regulations involves the loader using Cummins’ Single Module after-treatment system that incorporates a DPF (diesel particulate filter), SCR (selective catalytic reduction) and Urea dosing in a single unit, taking up 50% less space than the previous system. The large bonnet covering the machine’s vital components is electrically opened and gives ample room around the engine and a cooling pack for service access.
The HL960A rides on a pair of heavy-duty axles offering a ground clearance of over 400mm and, due to the short wheelbase, boasts a relatively tight 7.75m turning circle. Wide and well-spaced non-slip steps provide access to the large cab.
The Hyundai cab features large areas of glass to provide all-around visibility, in addition to a bank of switches to the operator’s right-hand side behind the main joystick. Joystick steering can be specified as an option, but Webb did not take this. “I like the steering wheel; it’s responsive and light to use,” says Missen. “I have been very impressed by the noise or lack of it in the cab.”
Willowbrook carries out servicing with remote monitoring of the machine undertaken through Hyundai’s Hi-MATE telematics system. The A model has Engine Connected Diagnostics (ECD), which reports any engine failures immediately to both the Hi-MATE system and the engine manufacturer themselves.
“The fuel consumption is good as is its AdBlue intake,” adds Missen. “If it stays as reliable as my old machine, I’ll be a very happy man.”
Rubble Master’s RM 120X mobile impact crusher, a hybrid model that can be both diesel-electric and purely electric-powered, has been in series production since autumn 2020. It is the Austrian manufacturer’s first NEXT philosophy crusher, combining enhanced safety, maximum efficiency and maximum performance.
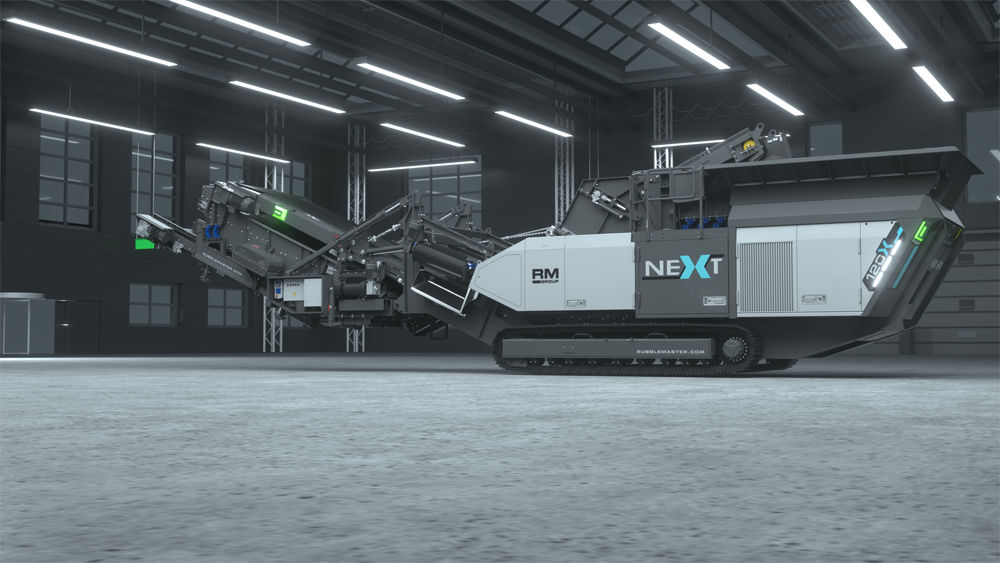
In September 2020, due to increased orders, Taha Zahir, based in Kafr Qasim, a hilltop city near Tel Aviv in Israel, decided to expand its fleet with its second RM crusher, choosing the new RM 120X. Like Taha Zahir’s early-2018-purchased RM 120GO!, the RM120X is processing construction and demolition (C&D) waste in an enclosed hall. The aggregate produced is then used as road substructure. Given that Taha Zahir’s processing takes place inside a building, the lowest possible dust and noise emissions were key concerns for the company when deciding on its new crusher.
Feed material with an edge length of up to 800mm is now processed fully electrically by the RM 120X to produce cuboid final aggregate (0-32 mm). In order to keep dust levels during the crushing process as low as possible, Taha Zahir also ordered a dust suppression system that minimises dust formation using water mist generated by a water pump and spray bar.
Every day, approximately 1,000 tonnes of C&D waste mixed with plastic, wood, and textiles are delivered to Taha Zahir. To ensure clean, high-quality final aggregate, the firm decided to install a wind sifter on both its RM impact crushers. The C&D waste is now free of unwanted light materials, leaving it able to produce a high-quality final aggregate.
The new RM120X is said to be very user-friendly, both during operation and maintenance. Rubble Master’s proven RM GO! principle - which stands for intuitive machine operation and more accessible machine components - has been further developed for the new NEXT machines.
With the innovative machine communication lights, the customer can now easily see the system’s current status. If the machine displays the green light, then everything is working perfectly. If the yellow light is on, the operator knows that a service is needed, and the red light indicates a warning.
Taha Zahir’s employees are also pleased about the new crusher’s safety features. As the first crusher in the NEXT series, the RM 120X keeps the operator well outside the danger zone during the crushing process. The radio remote control with display, RM GO! SMART (optional) as well as the machine communication lighting considerably increase the safety of the machine operator. All information relating to the crushing process is displayed in the RM GO! SMART App on a mobile device, smartphone or tablet.
Six-figure investment kick-starts aggrecycle relaunch
Aggrecycle has invested more than £100,000 in new vehicles and branding as it relaunches from its urban quarry in the heart of Leicester, central England.
The recycling firm has developed a new offering for small local operators to provide the full range of recycled, decorative, and quarried aggregates for Leicester and the wider Leicestershire county and East Midlands region building trade.
Based at its urban recycling quarry in Syston St East, the company recycled more than 150,000 tonnes of material in 2020, as AR Aggregates.
Almost half of the relaunch funding has been spent on a tipper lorry for small deliveries up to four tonnes—the rest spent on branding activity, including a new livery for Aggrecycle’s large lorries.
The latest investment comes on the back of a £900,000 investment in state-of-the-art German crushing and screening machinery in late 2019.
Andrew Thompson, Aggrecycle’s managing director, who runs the business with his brother, Darren, the company’s operations director, says there is a growing market for clean, quality recycled materials in the building trade.
“We know from our experience in construction and demolition that 99.9 per cent of spoil arising from these projects can be recycled. It’s part of our job to make that happen.
“Technology and equipment are so good now that the products we provide are indistinguishable from freshly quarried materials, so it makes sense to use them wherever possible.”
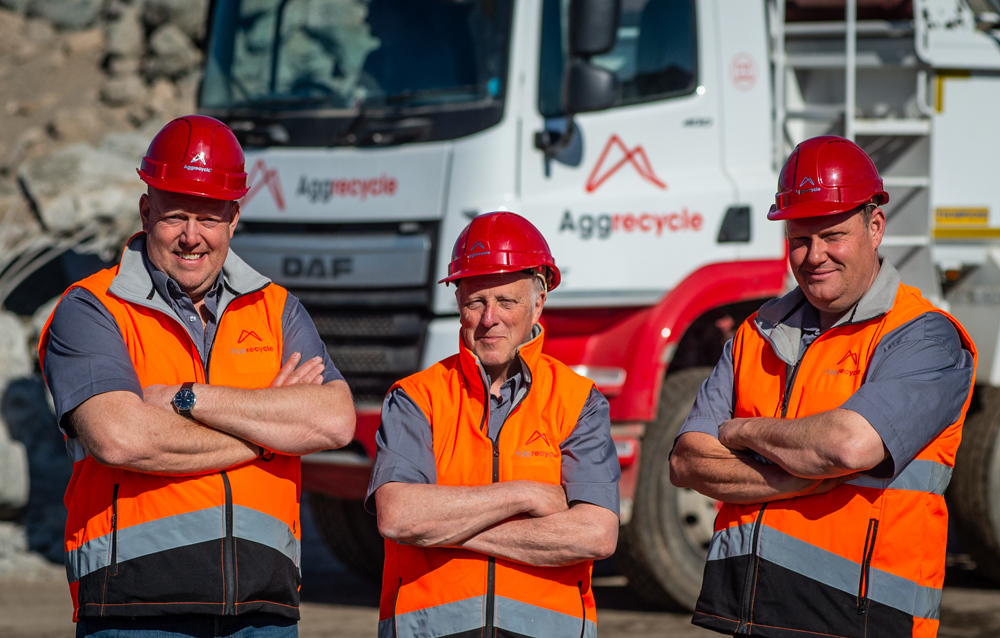
Andrew says Aggrecycle is keen to help reduce the carbon footprint of the regional construction industry by minimising landfill and keeping the supply of aggregates local to Leicestershire.
“If we can do that, by careful pre-planning and maximising the segregation of materials arising during construction processes, then there’s no reason not to either recycle every possible element or arrange for it to happen.
“People talk about the circular economy – we’re putting it into action. We’re keen to work locally if possible and help see our materials, most of which come from local projects, re-used as the basis for new construction projects.”