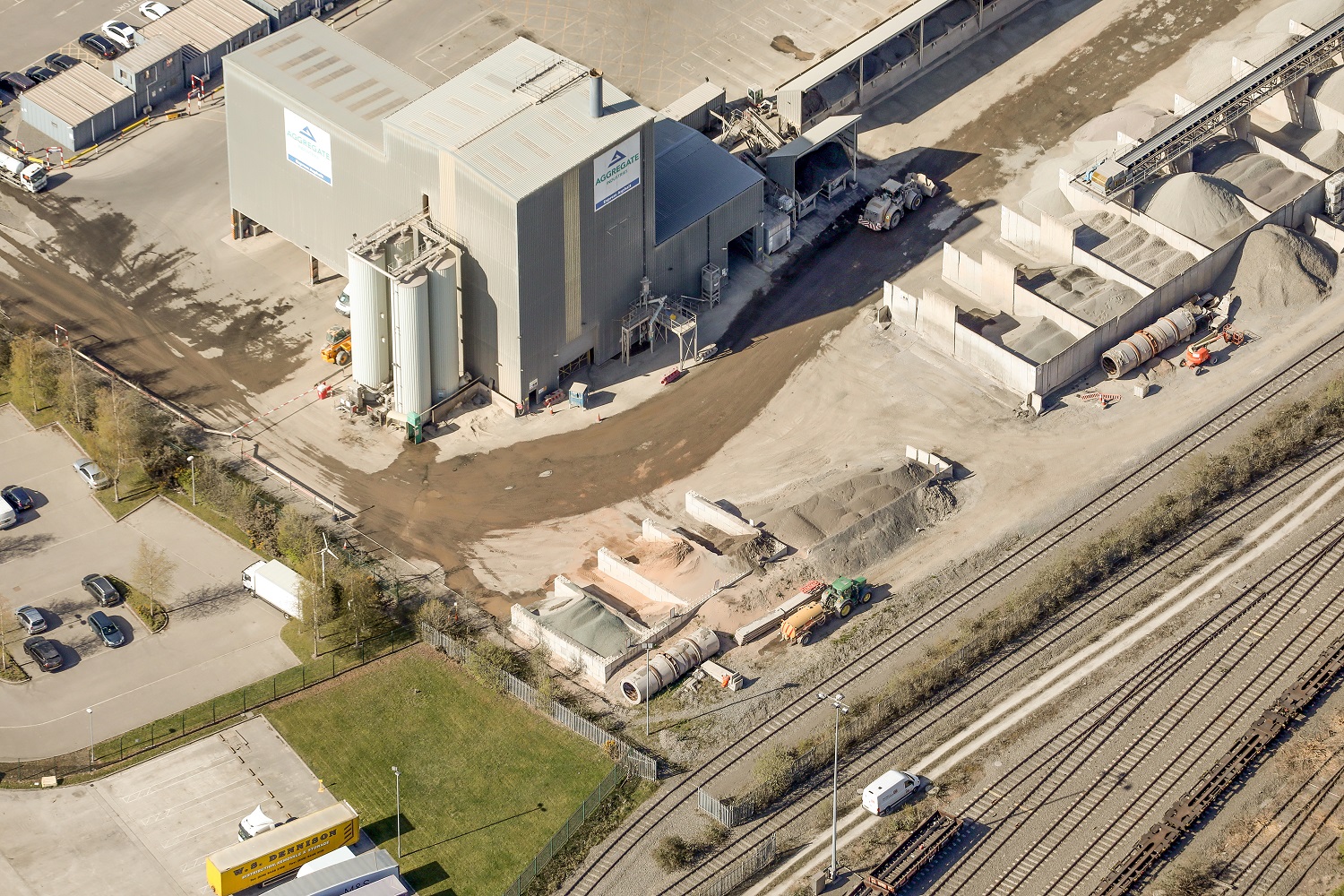
The BEIS (Department for Business, Energy & Industrial Strategy) grant, managed by Innovate UK, is part of support funding for major industries to meet the UK's net-zero targets. The grant allows Aggregate Industries to utilise Coomtech's innovative kinetic drying technology and the reclamation of pulverised fuel ash (PFA) from landfill to develop this new cement product.
Using managed turbulent air, Coomtech's kinetic dryers remove surface moisture by shearing the water from particle surfaces, keeping the air and moisture separate from the dried particles, which go to storage, transport, or directly into processing.
Aggregate Industries is using this technology to remove moisture from recycled PFA, as it seeks to decarbonise its processes and implement a circular economy business model.
In its new sustainability strategy Building Progress for a Sustainable Future, Aggregate Industries has made a commitment to increase its use of recycled materials from 1.5 million tonnes to 3 million tonnes by 2025 and to reduce waste to landfill to zero. The use of reclaimed PFA supports this transition.
Chris Every, chief commercial officer and a founder of Coomtech, said: "We're delighted to have the support of Aggregate Industries in this grant project. Coomtech is especially pleased to have the business' ongoing technical and commercial input to the project operation and analysis of performance.
"The added benefit of our new drying technology is its flexibility – providing the potential to dry a wide range of materials being considered to aid the greening of the cement industry, including limestone, ground blast-furnace slag, natural pozzolans, and other crushed and milled minerals that can offer an activated character to combine in cement and concrete mixes."
Barry Mellor, cementitious materials manager at Aggregate Industries, commented: "The partnership with Coomtech allows us to move towards the sustainable targets we've committed to as a business. Their innovative kinetic drying technology enables us to create a new cement product using reclaimed PFA, which would otherwise sit in landfill.
"Traditional methods of drying PFA would use a high amount of energy; thus recycling this material, combined with a low-energy drying process, results in a product which offers an overall reduction in energy, CO2, and carbon footprint.
"As we seek to move towards a circular economy, utilising products such as PFA, which would otherwise sit in landfill, is a really ground-breaking move forward for our business and the industry."