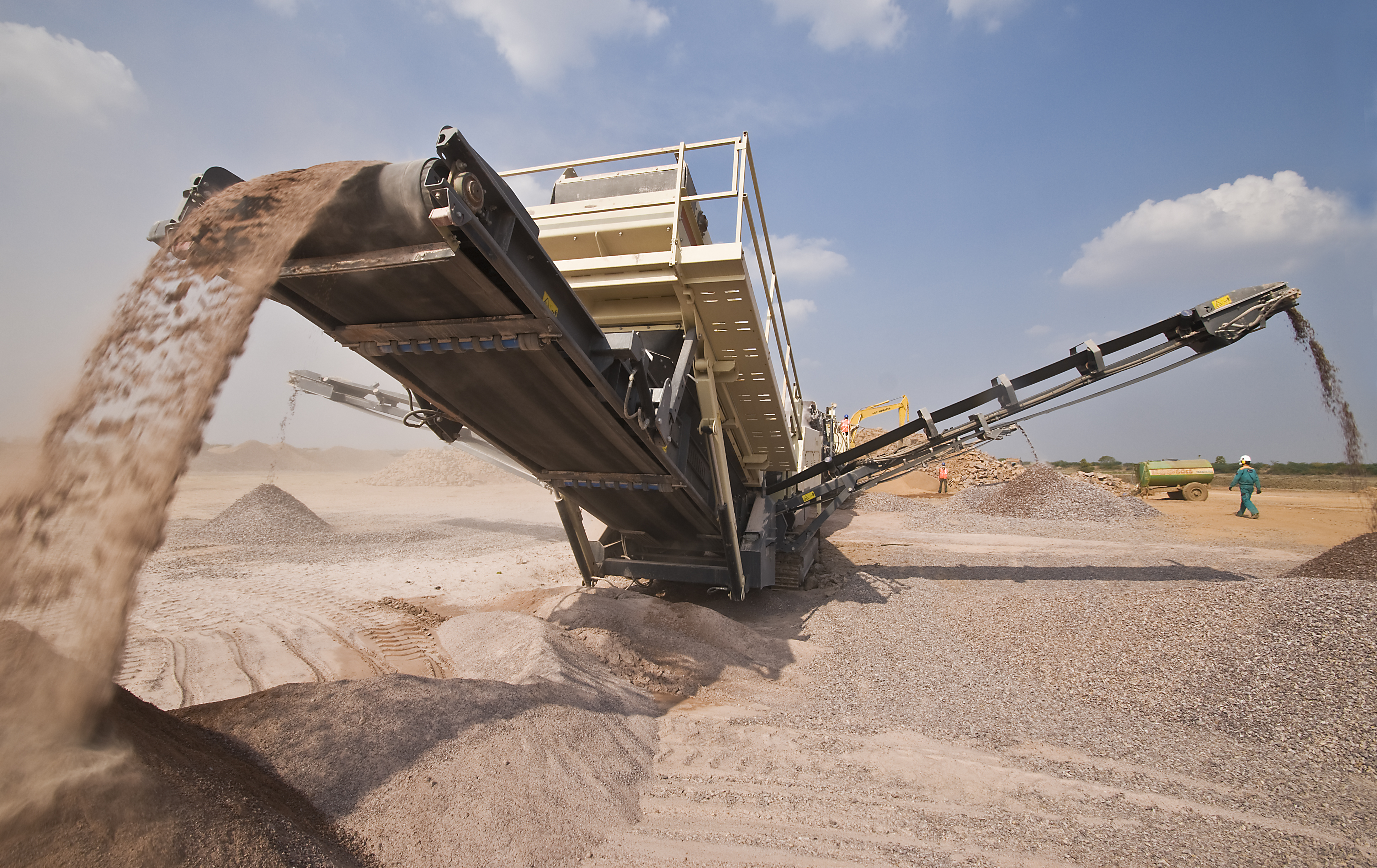
“Compared to our previous range of Lokotrack equipment, this is actually 20% more efficient so making more effective use of energy. We consider it as green through improving the efficienct use of the equipment,’’ says Mike Djan-Sampson, customer service senior manager of Metso Ghana.
There is the absence of redundancy with regard to the equipment.
“It is pure manual, hydraulics, without solenoids, electronics, it a very simple design fit for purpose that increases energy efficiency,’’ says Djan-Sampson, pointing out that the previous Lokotrack series was designed for use in the European market.
“The Lokotrack 1000 series we made it easy for people in Africa and developing areas to operate: basic hydraulics, basic electrics, and relatively cheaper, which guarantees comfort to the customer and that will be fit for purpose and the environment. It is more of cost effective solution for the environment.”
The Lokotrack 1000 employs a combination of hard-core engineering and components from brands such as
The crushing and screening plants offer a quick set-up time “which makes it a ready-to-go, non-stop machine.”
When the machine was delivered all that was done was to commission it, says Djan-Sampson.
“There is no excavation or civil work to be done, the equipment arrives on site, gets placed at the correct location and then rock feeding starts.
“If we wanted to make final products we drive up the secondary unit, which is also another LTG1000 secondary to the end, so straight away it arrives and starts producing aggregates.”
The Lokotrack 1000 series has three models: the C1000 jaw crusher, the G1000 cone crusher with or without on-board screen and the S1000 screen.