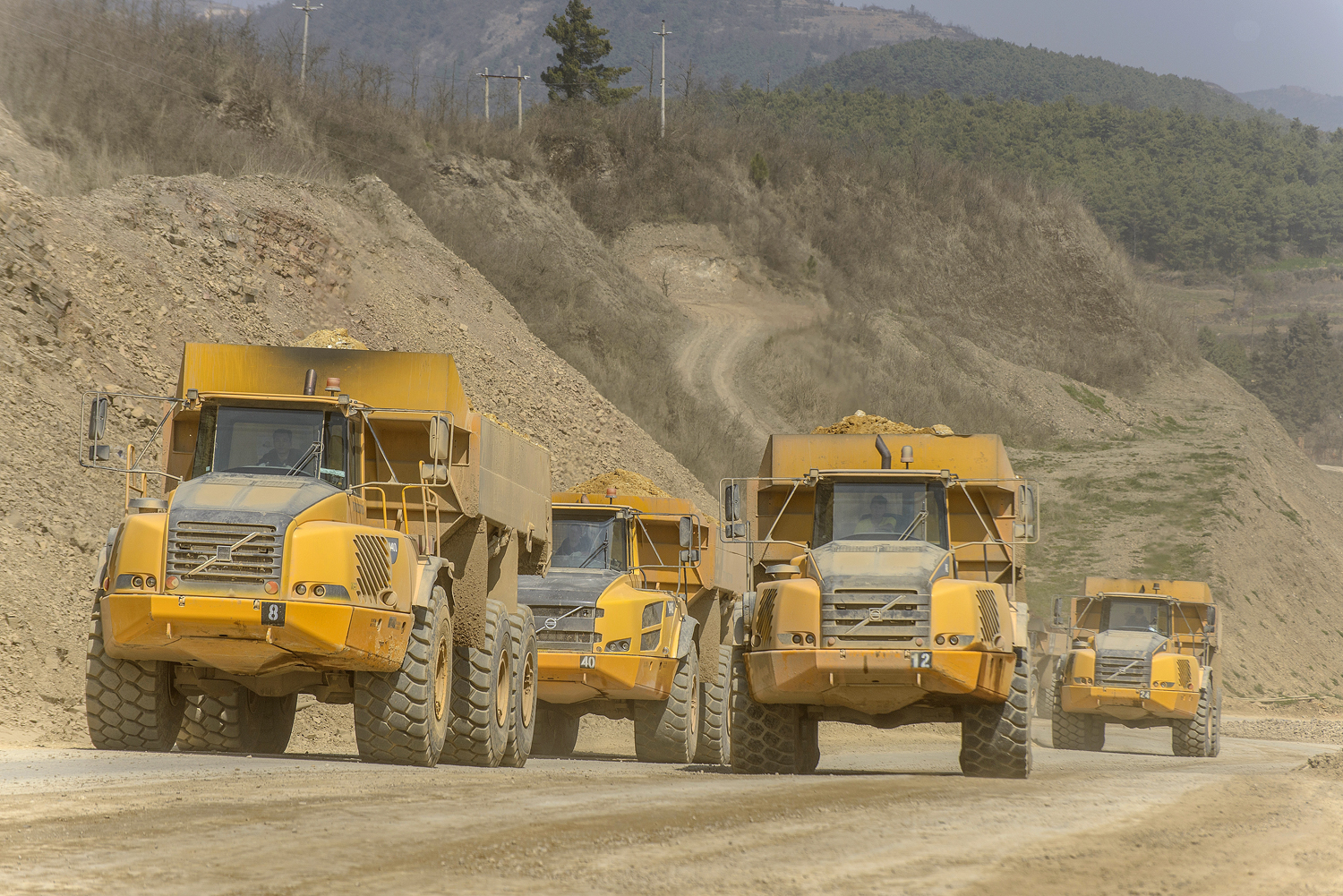
China’s largest modern open-pit phosphorus mining operation is relying on a fleet of 40
The pace is fast and furious at the Jinning phosphate mine. A procession of Volvo articulated haulers powers up the dusty hill towards the mine entrance. Located near Kunming, Yunnan, the mine nestles amidst the beautiful mountainous region in south-western China. Everywhere, the earth is a deep red hue. At its highest point, the mine reaches an altitude of 2,450m, but the turbocharged engines powering the army of Volvo A40 articulated haulers are said to not falter in their performance.
Phosphate is a pillar of modern agricultural practices. Most of the global production of phosphate is used in fertilizer, which is essential for sustainable agricultural production, particularly in developing countries. While Morocco is home to 85% of global phosphate reserves, China and India – with teeming populations to feed – are becoming important players in both mining and consuming it. China’s state-owned Yunnan Yuntianhua Company was established in 1965 in response to the growing need.
The Jinning mine is one of four open-pit mines owned by the Yunnan Phosphate Chemical Group Company, a subsidiary of Yunnan Yuntianhua. Together, these four mines make up China’s largest modern open-pit phosphorus mining operation. With a fleet of 40 Volvo A40 machines – a combination of D, E and F-Series – the operators are moving huge quantities of earth, although, with a production of about six million m³/year, this is still considered to be a ‘medium-sized’ operation.
Production is relatively simple. First, explosives break up the terrain, and then the haulers take the dislodged material to a collection site where it is crushed by a crusher. Finally, a 13km conveyor belt delivers the matieral to a refining site.
On the ground, the entire mining operation relies on a large fleet of articulated haulers, that work in tandem with excavators. Purchasing decisions are made by Yunnan Yuntianhua with input from operators working at the mine. They all agree: “We choose Volvo – for efficiency and safety.”
In the past, the company invested in other local brands but says this resulted in numerous maintenance issues, which put the safety of operators at risk. A tendency for those machines to tip over was blamed for accidents, which have on occasion proved fatal at this and similar mines. One of the main challenges for drivers is manoeuvring around the tight uphill and downhill bends. It’s not hard to imagine the consequences of fully-loaded haulers working in close proximity on the wind-blown, steep gravel road leading to the top of the mine.
The number of serious accidents drastically diminished when the Volvo articulated haulers arrived on the scene. To ensure jobsite safety, operators were trained by the Volvo CE dealer Beijing Century Development Technology Inc Co Ltd (Centec).
The dealership has a newly built maintenance center situated between the mine and the city, which contributes to a rapid turnaround of maintenance parts. Centec president Stiven Duan says that although the Volvo machines come with a higher price tag than some other brands, they end up saving their owners money.
“These haulers will pay for themselves relatively quickly because they consume less fuel and have less down time and fewer breakages than the machines they were using before,” he explains.
Li Yao Ji, Yunnan Phosphate Chemical Group Company general manager, agrees: “In the past 10 years, since we started to use Volvo equipment and training, the gain in efficiency has been around 20-30%,” he says.
There are usually around 25 haulers operating on any given day. Nevertheless, the haulers run for 18 hours a day, spread over three shifts, which means that on average each hauler covers 270km each day, 365 days a year. With an average of 2.5km between collection sites, the machines rack up the mileage very quickly.
Naturally, the figures fall significantly during the wet season, between June and October, as does productivity at the mine. Outside the office perched on top of the hill, a gigantic mound of slippery mud on the plateau illustrates why this is considered to be the harshest of Jinning’s mines.
The company has also acquired three Volvo EC700BL excavators to explore the bottom of the pit. The aim is to determine whether or not the vein of phosphate is present at that depth.
“The demand for most raw materials has plummeted in the past few months due to the slowdown in the economy,” explains Duan. “But demand in this sector remains stable because of the ongoing need for phosphate in agriculture.”