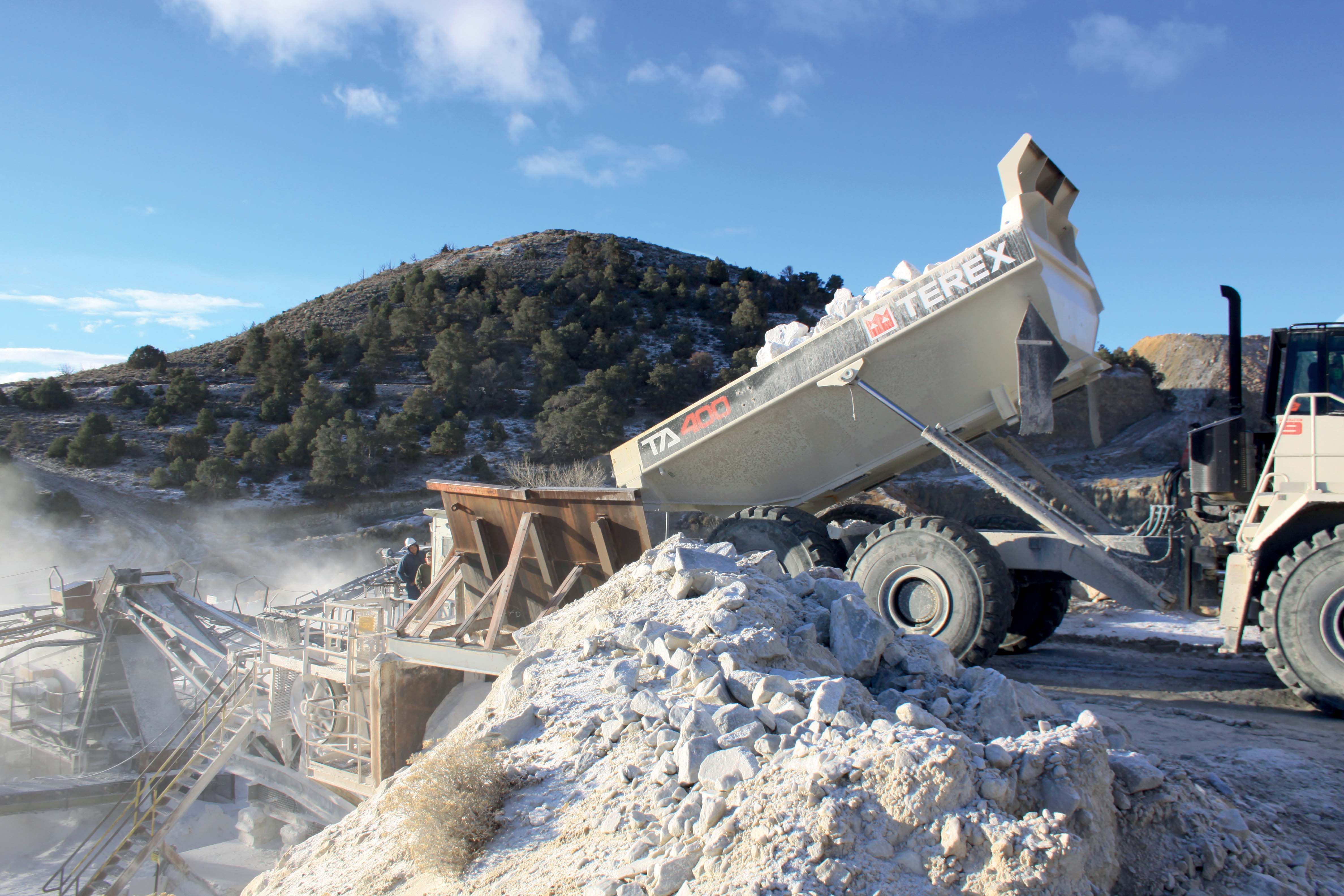
Well-suited to extreme weather conditions and packed with features to ensure smoother on-site operation, the latest haulers being manufactured by leading sector OEMs are proving a big hit on both sides of the Atlantic, as Guy Woodford reports.
After a comprehensive evaluation of its fleet, family-run mining business Art Wilson Company, recently bought four
This successful company has been producing limestone for cement rock, and gypsum for the agriculture and turf markets, for almost 50 years. The anhydride produced from the Adams Claim Mine is a form of gypsum said to be of a higher purity than most gypsum produced in the region. It is in high demand.
The trucks operating at Adams Claim Mine are required to make a 1.2km haul cycle from the bottom of the pit and haul material up the 10% grade. Art Wilson Company has historically operated 45tonne capacity rigid dump trucks at the Mine before the need for a strategy change was identified.
Nevada-based Terex Trucks dealer, Shafer Equipment Co., provided Art Wilson Company with a TA400 articulated dump truck for a thorough evaluation.
“There were a number of elements that had to be considered in the selection of new trucks, including the limited road size, the incline of the haul roads, and ability to handle bad weather in winter,” explained Paul Wilson, mine manager for the Art Wilson Company. “The Terex Trucks TA400 passed all the tests. We went with the 38 tonne-capacity truck as it is close to the capacity of the rigid trucks we were using.”
The original rigid trucks required substantial roads and struggled to pull on the high grade in the slippery underfoot conditions experienced during bad weather.
“During winter, even a light layer of snow in the mine would make it difficult for the previous trucks to navigate the slope,” said Jay Shafer, president of Shafer Equipment.
The TA400’s ability to climb and – more importantly – descend the 10% grade proved to be one of the critical factors in the decision-making.
“The retarder system in the TA400 really stood out to us,” said Wilson. “We also tested a truck with a single retarder system and wet disc brakes, which overheated on the downhill when trying to keep up with the TA400.”
Truck operator, Ty Vanroy, was most impressed by the TA400’s ability to handle the downhill slope smoothly. “I loved the exhaust brake in the TA400,” he said. “I didn’t need to use the brakes when going down even steep hills, which makes the brakes last longer.”
The TA400 has a dual retarder system, where a modulating transmission retarder is coupled with an efficient exhaust brake and fully-enclosed oil-cooled multidisc brake.
Having excelled in all performance tests, four Terex Trucks TA400s were purchased, and are currently operating at the Adams Claim Mine. The TA400s have two primary responsibilities at the mine: hauling material from the pit to the crushing circuit and removing overburden from areas being prepared for blasting. The company blasts 22,680tonnes of material two to three times per month in order to maintain supply.
Steady and consistent is the motto at the Adams Claim Mine, according to Wilson. “We don’t run fast; we run steady,” he said. “We run at about 10 mph (16.1 kmph) and are more concerned about getting material out of the pit consistently, rather than speedily.”
“You could say that dump trucks are the heart and soul of the operation,” said Robert Franklin, regional sales manager for Terex Trucks. “Carrying overburden and the muckpile to the crushing circuit is vital in order to keep the operation moving.”
The TA400’s 330kW
“I typically keep the truck in low range on the grade, but I can easily switch between low and high gear with the toggle switch inside the cab,” explained VanRoy.
Wilson is also expecting a significant cost saving with the new fleet of Terex Trucks, thanks to increased fuel efficiency. The TA400 will, on average claims Terex Trucks, reduce fuel consumed by an half in comparison to the previous trucks.
County Dyfed, Wales-based Gravelle Plant Ltd has expanded its use of articulated dump trucks (ADTs) from
The company has experienced a recent surge in orders, with fleet expansion required to accommodate supply to construction and excavation projects from Scotland to Cornwall, Southwest England. As such, the call for ADTs with the power to perform has increased substantially, as managing director Peter Gravelle explains: “Our latest purchases with Bell could not have come at a better time. We’ve kept our eyes on the manufacturer over the years, as we’ve had some exceptional machines from them in the past, each of which has proven itself throughout its working lifetime.
“With our recent need to expand, it made sense to look closer at what Bell had to offer, particularly with regard to brake engineering.”
Gravelle says the varying conditions his machines perform within can have a harsh effect on the brake systems of the ADTs within his fleet, and their mechanics. Taking the opportunity to consider improved design options, he looked seriously at the Bell B30E ADT before purchasing an additional four machines with twin-board brake systems.
“The design of the Bell B30E includes a hydraulic transmission retarder, which is powerful enough to significantly reduce ‘brake use’. This in effect can extend the pad life by up to five-fold. The machines also feature wet disc brakes as standard, which can also lower vehicular running costs.”
Gravelle says he has confidence in Bell, having purchased a number of 40 tonne machines in the past, all of which have exceeded his expectations.
Volvo Trucks claims to be the first truck manufacturer in the world to offer automatic engagement of all wheel drive on construction trucks. The Automatic Traction Control function activates the front wheel drive when the rear wheels lose traction on slippery or soft ground.
“Many drivers connect front-wheel drive or differential lock in good time before a difficult section of terrain in order to avoid getting stuck. Volvo Automatic Traction Control engages the front wheel drive when in motion, and only for the short time that it is really needed,” says Jonas Odermalm, construction segment manager at Volvo Trucks.
Volvo Automatic Traction Control, which has now become standard in the Volvo FMX with driven front axle, is already used by Volvo Construction Equipment in their articulated haulers.
The solution consists of software connected to the wheel speed sensors which detect and control wheel drive. When a rear wheel starts to slip, the power moves automatically to the front wheels without the truck losing torque or speed. A dog clutch activates the front-wheel drive in just half a second. The clutch is said to be lighter and has fewer moving parts than a traditional solution with permanent all-wheel drive. If the driver encounters particularly rough ground, then it is possible to manually lock the other differentials at both front and rear.
The drive on the front axle prevents standstills on slippery surfaces. At the same time, the function is often only required for a very small part of the total driving time. With Automatic Traction Control, the front tyres’ grip is concentrated on the steering right up until any critical situation. Thus, the driver can take advantage of the better manoeuvrability for as long as possible.
The driver also avoids extra fuel consumption and wear on the driveline and tyres, factors that are the usual result of constant front-wheel drive use. Automatic Traction Control is said to ensure that the optimal drive combination is always enabled and removes the decision from the driver.