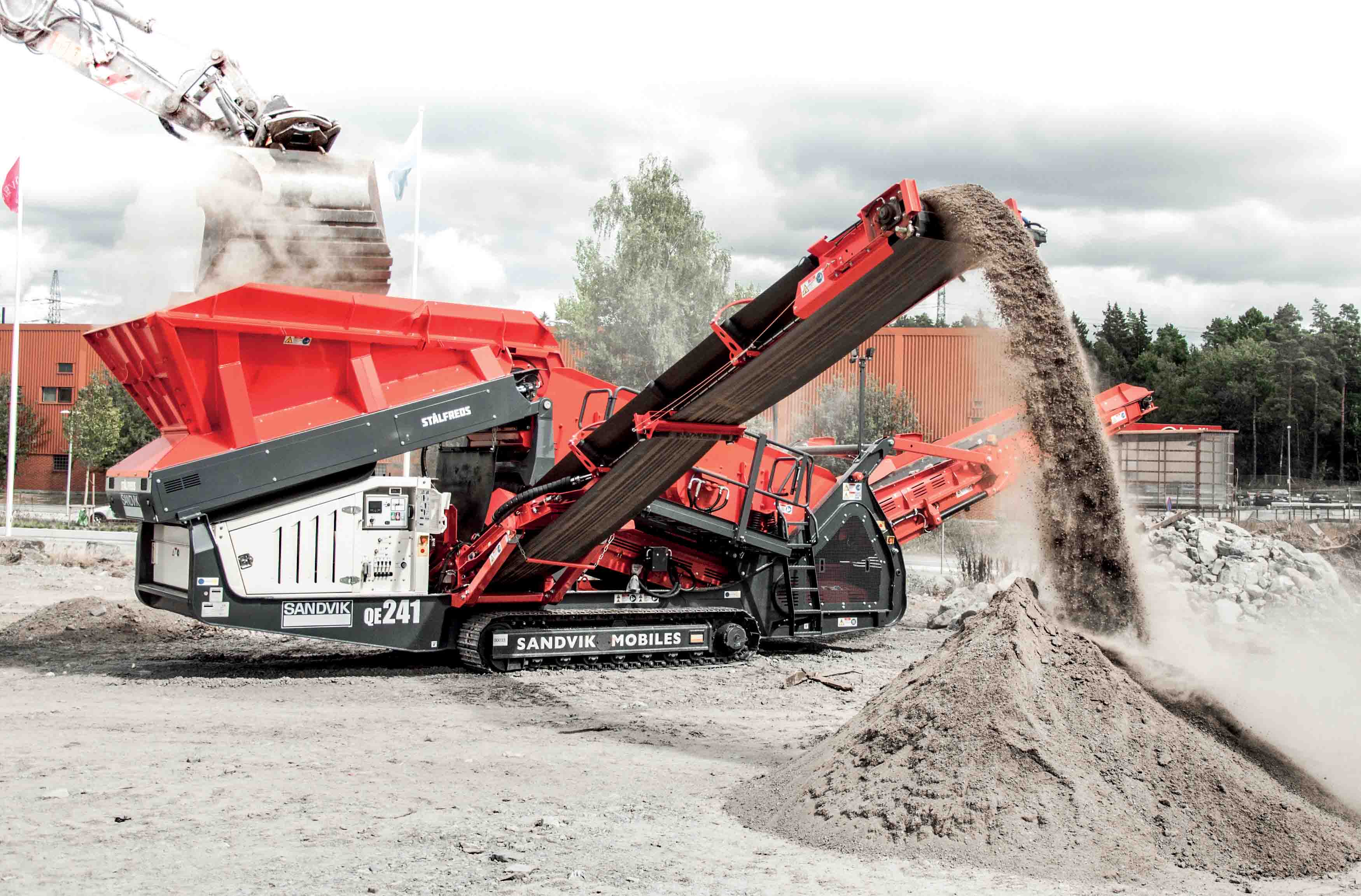
Innovative crushing and screening solutions have recently been highlighted by manufacturers. Patrick Smith reports.
The company says the RM 120GO! is the result of 25 years of experience and paves the way for the future of RM. It weighs 35tonnes and has a capacity of up to 350tonnes/hour.
“One of the main goals in the development of the RM 120GO! was the flexible range of use of the mobile RM crusher in both recycling and the processing of natural stone,” says Gerald Hanisch, Rubble Master founder and CEO.
With RM crushers and screens processing a wide variety of materials with a vast range of requirements and purposes, the company developed Spec2App to ensure the optimum recycling of natural stone, construction and demolition waste, basalt or ceramic tiles with a single crusher.
Another innovation, RM GO! SMART, a new form of smart machine communication, will be available in a basic version from the beginning of 2017.
It enables the monitoring of the performance and status of the key machine parameters using commercially available smartphones and tablets. The presentation of the Plus and Premium versions gave customers and dealers an insight into the future.
“We started 25 years ago as a pilot project and today our exports are accounting for over 95% of business in 2016,” says Hanisch.
Meanwhile, MD Recycling of Ceredigion, a Mid-Wales waste management company, says it has ramped up the quality and speed of its recycled products after investing in a new
Marc Davies, director of MD Recycling, has since reported a significant improvement in the standard of soil and aggregate products processed by the machine, and a much-faster production rate.
“The Terex Finlay 883+ has replaced an 883 screener and not only have we noticed a real difference since it arrived, but our clients have commented on it too,” says Davies.
“The hourly production rate of the machine is considerably better and its ability to cope with wet conditions is amazing.”
The screener processes green, mixed inert, builders’ waste, and construction and demolition material taken to the site by local authorities and building companies from across Wales. After being processed through the 883+, the soil and aggregates produced are sold on to farmers and construction companies.
Designed to work after a primary crusher or on its own as a frontline tracked mobile screening machine, the Terex Finlay 883+ boasts an aggressive screen box which features both a 4.8m x 1.5m top and bottom deck.
“The versatility of the plant means it can work with applications including sand, gravel, coal and aggregates as well as demolition debris, topsoil and quarrying,” says Gareth Johnson, managing director of Finlay Plant SW.
Meanwhile, brothers David and Gösta who run Swedish company, Stahl-Fredh, recently acquired a
The company, whose activities are diverse, operates an extensive plant fleet, but this is the first screener it has bought, and the first QE241 model in Sweden. It will complement activities by adding to the operational performance of the business.
“The scalper is used to separate the processed material into three different stockpiles,” says David.
“Everything over 60mm in one stockpile, then we have a 0-8mm fines fraction and a pile of rubble.
The QE241 comes fitted with a screen box jack-up facility and modular deck frames, which enable easy access for maintenance and quick change-over of screen media. Another feature that has impressed the Ståhl-Fredh brothers is that one conveyor can be moved from one side to the other so that both conveyors are positioned on the same side, a benefit in tight, confined spaces.
When McGirr Bros. of County Tyrone, Northern Ireland, decided to upgrade from its
It went for a
These, its says, include the lower fuel consumption, the bigger capacity, and the ease at which it can change the close side settings (CSS) on the jaw chamber, which are now done hydraulically.
“Four- wheeled versions and particularly the tracked models, D5 and D6, guarantee a high operational versatility on changing sites or on large-scale depots with varying materials,” says Keestrack.
Since last year Keestrack has cooperated in development and production with a European specialist in wheeled drum screen solutions, and as a result four trailer versions, with transport weights from 11-24tonnes, were introduced into the Keestrack programme.
At
As well as the smaller D5 (15.6tonnes; 4,700mm; 1.8m Ø), the 19tonne D6 with 5,500mm drum screen is said to offer trouble-free low bed transports (width 2,920mm), quick set-up times and is easy deployable on site.
Haver & Boecker says its new, portable F-Class vibrating screen offers increased mobility to maximise flexibility and return on investment (ROI) for aggregate and mining operations, with a base frame that easily attaches to a custom-built chassis.
The plant includes a hydraulic system that positions the vibrating screen at the optimal angle from 15-25º, features that allow producers to move and set it up in less than 30 minutes in nearly any location.
“With the fast pace of the industry and the underlying need to increase screening efficiency and profitability, it was the right time to launch the portable F-Class,” says Karen Thompson, Haver & Boecker Canada president.
The F-Class is said to be ideal for tough applications, such as scalping and classifying ores, minerals, stones, sand and gravel.
Additionally,
Other companies showing off new equipment are
Johnson Crushers International’s Kodiak K500+ is a remote-adjust cone crusher that is part of the Kodiak Plus cone crusher family, which consists of three other models, the K200+, K300+ and K400+.
The K500+ model fills the demand for larger secondary and tertiary cone crushers that are used by high production aggregate producers and mining companies, according to Ian Pendergrass, JCI product development manager.
“The Kodiak Plus product line includes a hybrid cast/fabricated base frame design; an automated control system; a patented liner retention system; patented thread locking ring; anti-spin cone brake, and other additional evolutionary refinements,” says Pendergrass.
Kolberg-Pioneer has expanded its jaw crusher product line with the new 3365 Pioneer.
“This crusher has up to 20% more capacity than the next size in its width class in both hard rock and recycled applications,” says Tim Harms, product manager for Kolberg-Pioneer.
“The 3365 features an automatic adjust, for both the wedge style and tramp iron release systems. It also offers the advantages as standard on Pioneer crushers, including replaceable jaw die seats, barrel protector plate, as well as an aggressive 1.5inch [38mm] stroke.”