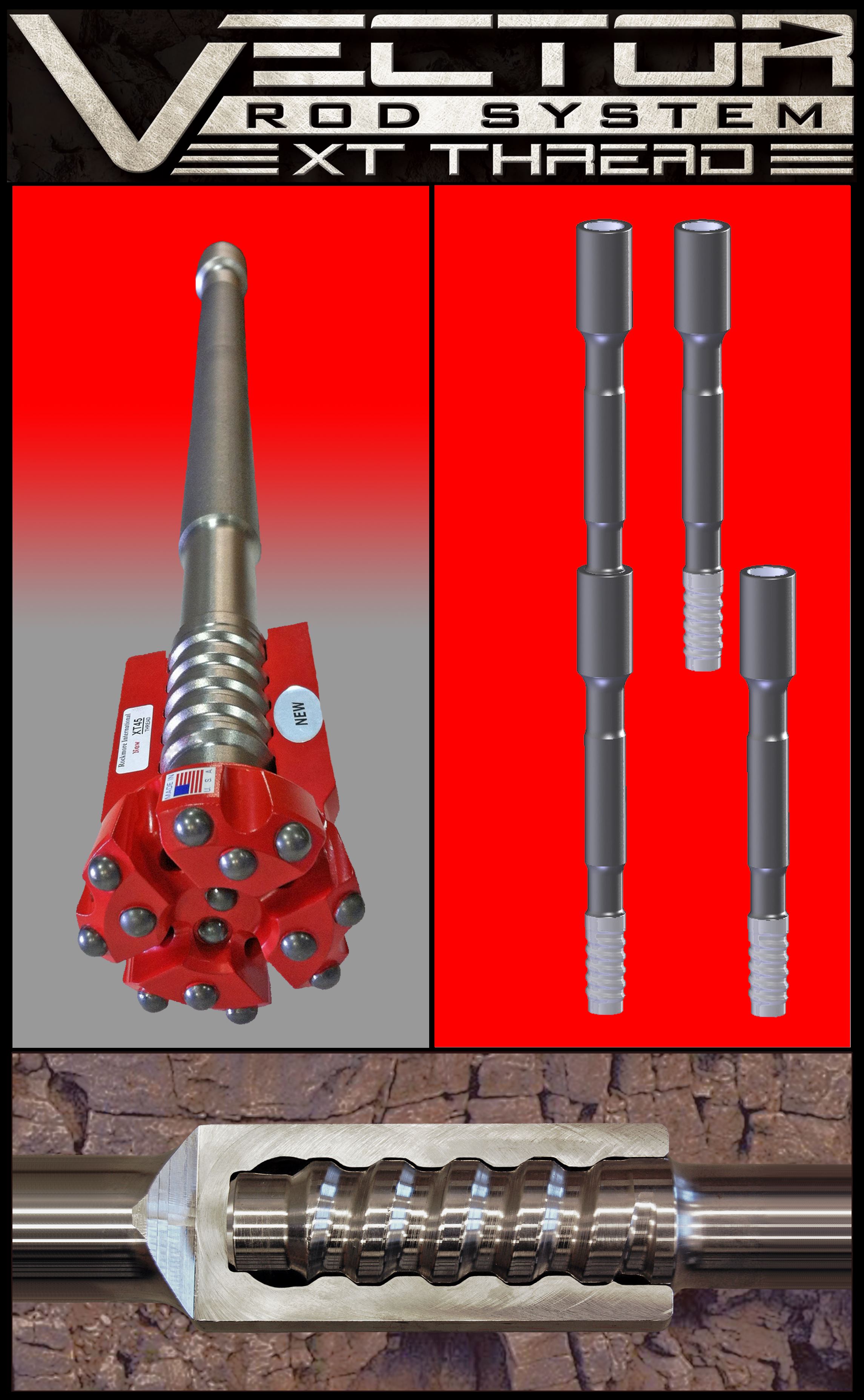
Claimed by the U.S. manufacturer to be a major breakthrough in improving performance and service life of extension drill tools in surface and underground percussive drilling applications, Rockmore International’s (Rockmore) new line of drill tools are said to offer tremendous advantages in productivity and reliability.
After several years of intense research and development followed up with monitored field tests in various ground conditions, Rockmore engineers developed a new thread design, XT, for the Vector Rod System. The new XT design incorporates revolutionary new guided cylindrical contact zones between the male and female thread joints. These guided surface features are located in the nose and rear of the thread connections and serve various benefits and improvements over traditional threads.
The XT thread profile is based on the traditional trapezoidal “T” thread design and is therefore compatible with industry standard thread types such as T38, T45, and T51. Thus, one can interchange and connect standard “T” style threaded components with the new XT thread, although the guiding advantages aforementioned would be neglected. For example, a T45 threaded bit or shank adapter can be connected to a XT45 threaded rod with full compatibility.
“We specifically targeted to increase thread service life while enhancing drilling performance in extension drilling applications,” says Pejman Eghdami, Rockmore’s executive vice president, in explaining the goal of developing the Vector Rod System. The dual cylindrical contact zones in the nose and rear of the XT threads significantly increase the lateral support between thread joints and stabilise the connections with more rigidity to provide better energy transfer. The enhanced thread support and geometry extends thread life and increases the overall component service life of the shank adapters, rods, and bits with XT threads that comprise the Vector Rod System.
Because the XT thread guide feature improves thread alignment, the impact duration when “rattling” rods, as required in uncoupling connections, is minimised. This leads to lower wasted energy transmission, cooler couplings on rods, and ultimately to longer rod life. Thread grease is also better retained on the thread pitches resulting from the new XT geometry, further increasing thread life in all XT components.
Another claimed key advantage of this rod system over traditional threaded components is providing straighter holes and minimising its deviation, so inherently critical in modern drill and blast techniques. The guided XT thread feature increases the rigidity and stability of the connections between the shank adapters, rods, and bits so significantly that overall rod bending is minimised and hole straightness improved. In fact, this improvement allows for larger and deeper blast holes to be achieved using existing rod diameters, but only by converting to XT threaded components. In underground mining long-hole and production applications where up to 30 rod connections are common, hole deviation can be reduced substantially by using Vector Rods.
Eghdami continues: “As a major breakthrough for extension drilling systems, we have significantly improved drilling productivity and increased drill string lifetime by introducing new design features in the XT thread configuration. And just as important, the new XT design is fully reverse compatible with industry standard “T” style threads, enabling the Vector Rod System to be truly remarkable, yet a practical choice for premium drilling tools.”
The Vector Rod System is offered in multiple configurations of button bits, MF rods, and shank adapters. These drill string components are available in XT38, XT45, XT51, and XT60 thread types, designed to improve drilling productivity and reduce extension drilling operating costs in surface and underground percussive drilling.