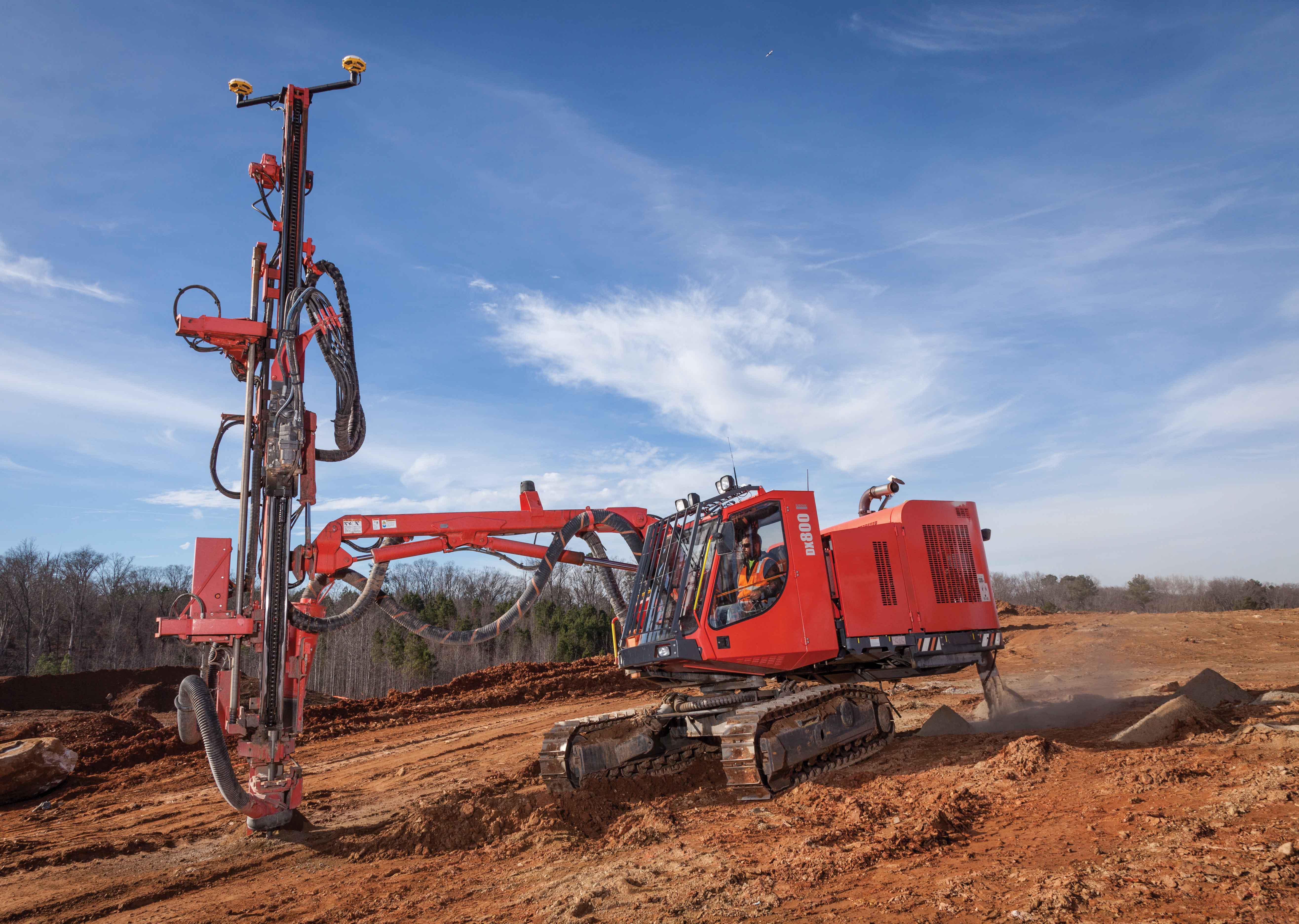
Anyone with experience working in quarries knows that drilling with precision requires a certain amount of guesswork. So says Kevin Garcia, business area manager for paving and specialty construction within Trimble’s Civil Engineering and Construction Division.
“From spray-painted markers to working on uneven surfaces, hitting an exact point from a location, depth and inclination perspective comes with its share of challenges,” says Garcia. He points to what he says is one solution, the
The aftermarket, land-based 3D system relies on positioning technology to guide operators to correct locations with centimetre level precision.
“With the Trimble DPS900 system, drill plans can be created in either office or field software and sent wirelessly to a Trimble Site Tablet, located in the cab at the operator’s fingertips. All metrics are displayed using large icons on an easy-to-read touchscreen,” says Garcia.
“Using two GNSS receivers and machine sensors, the system improves quality by guiding the operator to the precise location and angle of each hole resulting in evenly spaced holes and correct bench slopes.”
The system uses elevation, not depth, and this is said to eliminate all uncertainly around drilling to the correct bench height, regardless of uneven terrain, and it offers an auto-stop feature to ensure all holes will end on the same plane, leaving the operator with a level bench.
“Drilling to exact elevations without over-drilling improves efficiency and helps contractors reduce consumables, wear and tear, and ultimately, cost. Overdrilling, even a little bit every time, adds up to substantial wear and tear to the machine as well as extra costs associated with the additional explosives,” says Garcia.
“The system also increases job site productivity by eliminating the need to layout hole locations. Putting the drill plan at the operator’s fingertips enables workers to go from drill plan creation to production immediately.
“Getting surveyors off the bench and allowing operators to position over hole locations without assistance increases worker safety significantly. In addition to keeping workers out of the way of drilling machines, the Trimble DPS900 system includes an avoidance zone feature that will warn an operator who is approaching unsafe work areas.”
In Korea, the first
GMC Corporation uses the rigs for mining limestone, and from its mine in Baekwoon (Korea’s largest limestone producer), some 2 million tonnes of limestone/year is removed and transported to Jincheon for further processing.
“The Tiger DG series has been developed to give excellent rates of penetration with high performing Sandvik rock drills. Blasting results are also enhanced due to the advanced Rock Pilot drilling control system that guarantees smooth collaring thereby delivering better hole quality,” says Sandvik, which has been customer field-testing a dedicated accessory to the Dino DC400Ri drill rig, a remote screen and app to enhance remote control working.
In Norway, drill rig operator Andreas Gundersen was one of the first to see this latest technology when his employer, Vestfold Fjellboring, bought its first Dino DC400Ri rig for site clearance work among the rocky outcrops at a building project.
Working with the Dino and the remote screen, Gundersen found new ways to better perform many of the tasks required on site, realising that many tasks could be done in parallel. This included such activities as marking-up the next drill holes and planning and grinding bits, all while the Dino was drilling.
These were accomplished as Gundersen used the remote small screen to safely monitor the rig’s performance as he continuously moved around, resulting in overall productivity being improved with safety being further enhanced.
The Sandvik app, installed on an Android phone, is clicked into place on a mobile grip, itself locked to the operation console hanging from the shoulder.
Simply tap the app and the remote screen is ready to go, and whether near or far from the Dino DC400Ri, the operator gets the same key drilling data to read on the phone screen. Information and data comes over a secure wireless link from a small transmitter added on to the Dino.
Vestfold Fjellboring was the first company to receive the remote screen as part of a beta test programme, and following this Sandvik aims to have the remote screen available in 2016 as an optional extra for the Dino DC400Ri.
Such is the technology in this field that TEI, a US supplier of drills and attachments, is now seeking to open up new applications for its DrillAll, which was originally developed for the US military. It has turned to the crossindustry
Meanwhile, among
SmartROC D60, a down-thehole (DTH) rig, is designed for drilling 110–178mm holes., and its hole navigation (HNS) and auto-positioning systems ensure that the rig will locate the exact position of each hole and then accurately collar and drill them to precisely the required depth and inclination, giving a better fragmentation and improving loadability and crushability.
The standard feed carrying 5m tubes features built-in sensors in the rod handling cylinders and carousel motor, eliminating the need for inductive sensors. The rig also has Auto Rod Handling as a standard feature to automatically add and then extract the rods when the desired depth is reached.
At worksites where bench stability may be in doubt, the SmartROC D60 can be used together with Atlas Copco’s BenchREMOTE operator station that enables it to be operated at a distance of up to 100m. Another newcomer is the Atlas Copco SpeedROC 2F, specially designed for the dimension stone industry. The radio remote-controlled rig offers a 360° coverage area; long boom reach; flexible drilling capacity; fast positioning, and high tramming stability.
In the Ukraine,
Knauf’s plans to increase production in the Ukraine meant it required two more breakers: a new Rammer 4099, installed on a
The hydraulic breakers in the Rammer Large Range, of which the 3288 and 4099 are two, include such customer focused features as the Ramlube II automatic greasing system and Ramdata II service indicator.
These protect the equipment from unwanted breakdowns, with the 3288 and 4099 models also being equipped with VIDAT tie rods, idle blow protection and stroke selector.
At Rockmore International a new line of drill tools is conceived to be a “major breakthrough in improving performance and service life of extension drill tools in surface and underground percussive drilling applications.”
Company engineers have developed XT, a new thread design for the Vector Rod System that incorporates “revolutionary new guided cylindrical contact zones between the male and female thread joints.” These guided surface features are located in the nose and rear of the thread connections and are said to serve various benefits and improvements over traditional threads.
The XT thread profile is based on the traditional trapezoidal T thread design and is compatible with industry standard thread types such as T38, T45, and T51.
Rockmore says in underground mining long-hole and production applications, where up to 30 rod connections are common, hole deviation can be reduced substantially by using Vector Rods, which are offered in multiple configurations of button bits, MF rods, and shank adapters, and these drill string components are available in XT38, XT45, XT51, and XT60 thread types.