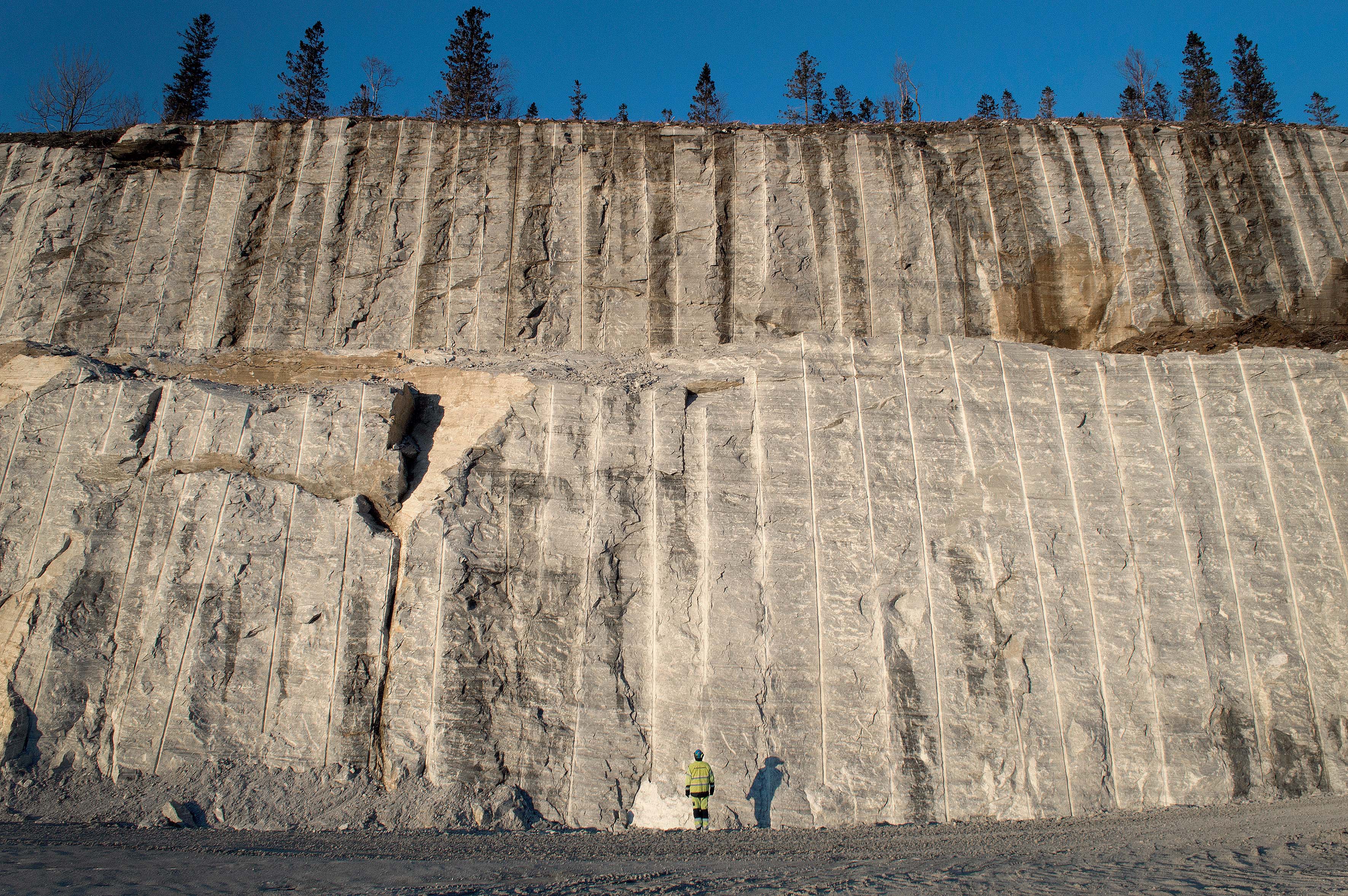
Drilling and breaking are vital parts of any quarry operation, and recent successful applications have emphasised this. Patrick Smith and Guy Woodford report
A
In another application, Brønnøy Kalk, owners of the Akselberg limestone quarry in Norway, about 400km north of Trondheim, achieved consistency and reliability in its production process using
In Kuala Lumpur, local civil engineering contractor Crescendo Infra, on behalf of a local developer, had to deal with the extremely hard granite found in the area. Plans to blast to prepare the ground works for the residential development were not to be possible due to the potential impact on surrounding residences and other buildings. It was decided to use rock breakers, and the company approached Power Ram, Malaysia’s Rammer breakers and attachments dealer.
“We brought in a Rammer 5011 breaker mounted on a 45tonne-class
The granite on the job was so hard that it required pre-drilling before work could start on breaking.
“Even so, at first our penetration rates were quite slow, but as we proceeded with the job, they started to improve. By the end, we were achieving rates of 11-16m³ every eight hours,” says Kok.
“It took us two and a half months to move around 1,040m³ of this very hard granite.”
The Rammer 5011 breaker has an operating weight of 4,750kg and is designed for carriers in the 43-80tonne-class, and its ability to vary stroke length allows it to be purpose-matched to individual applications and materials through the use of two simple working mode selectors located on the breaker itself.
The long-stroke setting of the 5011 uses a lower blow frequency for optimum breaking of hard materials, such as granite (and reinforced concrete foundations), while its short-stroke setting delivers higher blow frequency, making it ideal for softer materials, such as limestone.
At Magnus Schakt, Mikael Kauppi, was made aware by
Land used for construction projects often contributes to the problems faced by companies: it might be difficult to reach, waterlogged or just too hilly. However, when it comes to removing rock, and no matter the operating conditions, Kauppi is happy to prepare the foundations with one of his three Sandvik drill rigs.
“Most jobs are small. One exception was the Stockholm City Line project, which lasted for about four to five years. We prepared land for the new station platforms under Central Station, where we used the Sandvik DC122R,” says Kauppi.
The electrically-powered DC122R used so successfully on the Stockholm City Line project has been used by Magnus Schakt alongside two conventional surface drill rigs from the 300 series. One is being replaced by a slightly larger, new, Dino DC400Ri, the first of its kind to be delivered in Sweden.
Kauppi says it has been acquired based on three essential factors: the machine is easy to mount, dismount and transport.
The Dino DC400Ri, Sandvik’s latest addition to its fleet of surface drill rigs, was recently used by Marcus Schakt to drill blast holes needed to remove a small rocky knoll from a plot in Nävekvarn, about 25km from Nyköping, where the company Älvsbyhus is building houses.
The Dino DC400Ri is a 10tonne rig said to complement Sandvik’s range of top hammer drill rigs, and it can handle hole dimensions from 51-76mm. To accompany its new drill rig, Sandvik has also launched a brand new rock drill, the RD414, which was designed specifically for the Dino DC400Ri.
Brønnøy Kalk’s Akselberg quarry produces about 1.8 million tonnes of limestone carbonate annually, and since it was established in 1997, this 2.5km-long and 1.5km-wide pit has consistently improved its productivity in drilling and blasting.
“Everything here starts with the drilling. If we get that wrong, it has consequences for every other phase in our operation, from blasting and loading through to crushing and, ultimately, the quality of our products.
“Our vision has always been to achieve optimal utilisation of the limestone here and that requires optimising the whole excavation process. That’s why we are very happy to be getting top results with our equipment and to see the effect of this on the total efficiency of our operation,” says Raymond Langfjord, production manager at the site.
The equipment on site consists of Atlas Copco SmartROC tophammer drill rigs complete with the Hole Navigation System (HNS); AutoPos function, and ROC Manager, which creates drill plans and reports. HNS and AutoPos together are key functions that enable the operator to locate and collar the hole with accurate angles, first time every time.
There are three rigs at work in the quarry, a SmartRig ROC F9C, a SmartROC T40 and a SmartROC T45, drilling on 15m-high benches. The holes are drilled at an inclination of 10° and five rows are drilled with a burden of 2.8m and a spacing of 3.5m. After charging and firing, 20,000-80,000tonnes of rock are removed with each blast and the quarry carries out an average of ten blasts/month.
The rigs use T51 drill rods and 89mm ballistic button bits from Atlas Copco Secoroc and the rock is relatively easy to drill with penetration rates of 1.8-2.5m/minute. The bits only need to be reground every 250m and, at best, one bit can last for up to 6,000m.
Fortunately, the drillers are able to meet these tough demands using the rigs’ HNS system together with the AutoPos function. “The last row of holes, which is always at the rear of the bench, is the most important one,” continues Langfjord. “This is the master row and it has to be right. Otherwise it will negatively affect the rest.
“With HNS we can import the drill plan that has been created in ROC Manager, using a USB, and the system helps the operator to navigate the rig to the precise hole location. The rig’s AutoPos function then sets up the correct inclination on the feed, ensuring that the bit will hit the right spot on the ground at the touch of a button. The operator starts drilling and then simply switches to automatic mode and the rig drills the rest of the hole by itself.” In this way, the AutoPos function minimises the risk of human error.
After the hole has been drilled to the correct depth, log files are stored and can be viewed as status reports in ROC Manager, enabling the actual hole to be compared with the plan. If there is any deviation, adjustments can be made to correct the error before continuing.
“In that case we can either adapt the charge for that hole or drill a new hole altogether, Langfjord points out. “It makes life very easy.”
Furthermore, HNS-equipped drill rigs can also be equipped with Atlas Copco’s optional Measure While Drilling (MWD) function, gathering information such as variations in rock type, hardness, the presence of fissures, cavities and so on, which is analysed prior to blasting.
“Obviously, all of these devices are a great advantage,” Langfjord says. “They help us to achieve our prime goal which is to optimise the blasted rounds, and therefore create the conditions for making the operation as efficient as it can be.”
Correctly blasted rounds produce the required fragmentation, which in the Brønnøy quarry is maintained at an absolute maximum of 1.2m x 1.6m. Satisfactory fragmentation is important, both for optimising the loading of the quarry’s wheeled loaders as well as for fast throughput at the crusher station.
With the correct dimensions of the rock, the crusher station runs evenly and smoothly, using the right amount of power required to crush the stone while consuming as little energy as possible to minimise costs.
An added advantage is that correctly blasted rounds increase safety and improve the environment for the 45 people at the site by reducing the amount of flyrock and dust.
“Obviously equipment like this costs extra money so you’ve got to get it out at the other end,” Langfjord maintains, “and that’s exactly what we’ve done as we have been able to increase the drill pattern from 8.6 to 9.8 square metres.”
Mats Birkestål, product manager at Atlas Copco’s surface and exploration drilling division, sums up the Brønnøy experience. “What’s important here is that this company has understood the value of each step in the process,” he says. “They plan the holes they are about to drill and follow up after each drilling operation in order to secure the best possible rock fragmentation. They know that this process is the key to total efficiency.
The new FRD Furukawa HCR 1450-ED tophammer crawler drill has been a very welcome addition to Norwegian building and construction firm Parken Solutions’ expanding tool kit.
“The drill is easier to use than others as it’s not so heavy, and it’s still got great quality,” says Jan Ole Parken, Parken Solutions general manager. “You use these machines in dusty, cold, and all-round bad conditions, and with some of the other models the sensors and motors can shut off, so you can’t drill anymore.”
Parken said a colleague had also recommended FRD tophammer crawler drills having successfully used the Dutch headquartered firm’s HCR 1200-ED and HCR 1500-ED models.
Now, Parken says his company is the first in Norway to use the HCR 1450-ED tophammer crawler drill. The model is being used in the drilling and blasting of 30,000m³ of rock as part of a quarry’s gravel production process. “I’ve already used the drill for more than 300 hours and there’s been no trouble with it,” he added.
Fitted with a larger compressor and drifter, the main new features of the HCR 1450-ED tophammer crawler drill are the new Tier4i (Stage 3B) engine and other cosmetic updates, much of which focus on increased operator comfort, ease of maintenance and reduced operating cost.
Speaking at
“Africa has big potential but at the moment the market is struggling. The mining sector in particular is struggling,” said Vitulano, who was due to be among the panellists at the 2015 CECE-CEMA Summit from 23-24 September.
“If you’d asked me two years ago about which continent would see growth, I’d have said Africa. However, there are still problems with corruption and other issues which makes things difficult. Some markets within Africa, like Central Africa, may have possible growth, but it’s tough to forecast.”