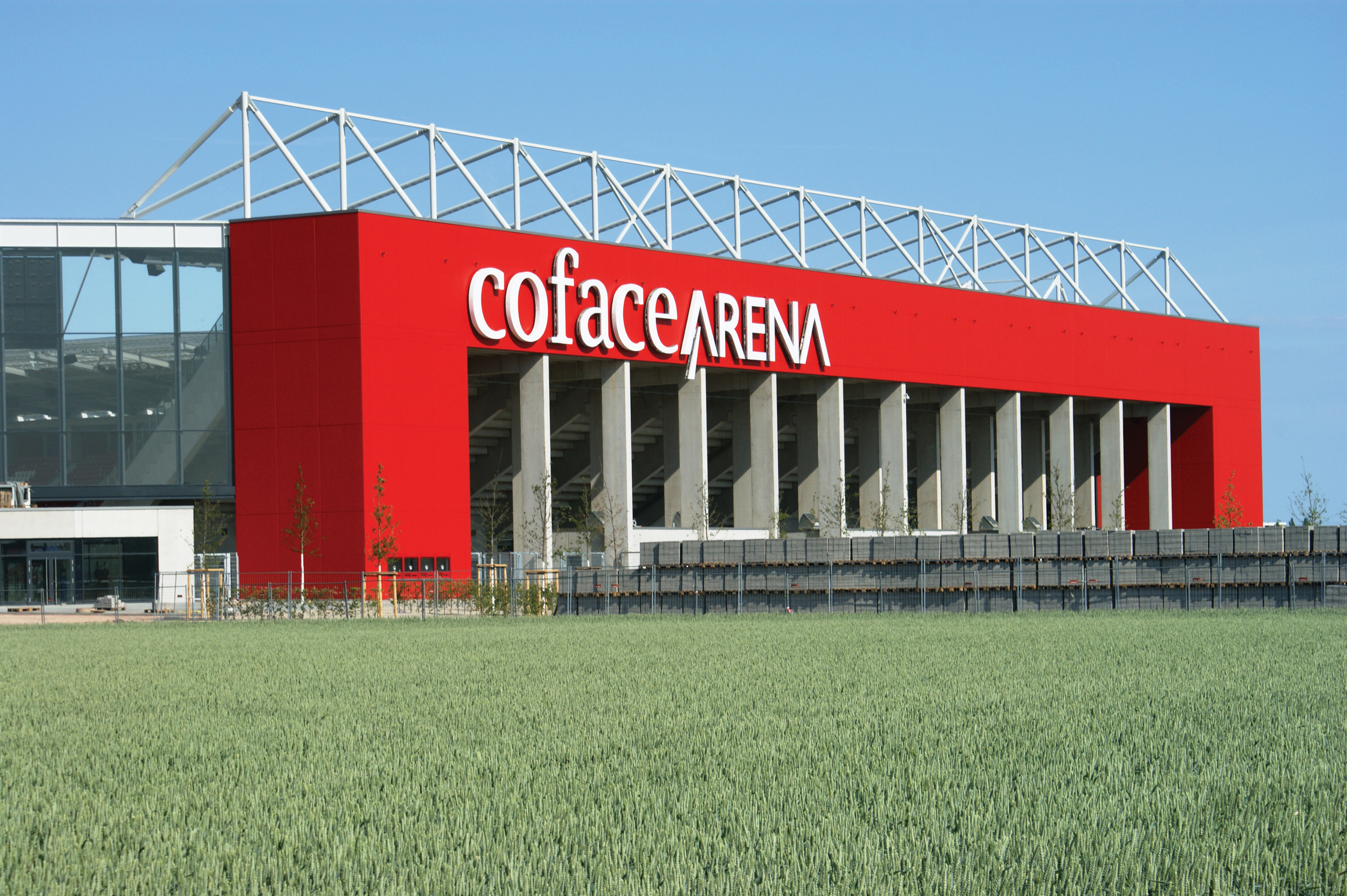
Meeting site logistics while satisfying demands for high quality concrete products can be a complex task. ABE reports on Cemex work to supply material for Germany's Coface Arena
Football fans flocking to Mainz's new Coface Arena may appreciate the ability of the stadium to accommodate 33,500 spectators, but few will appreciate the complexity of the construction work. Nonetheless, state of the art prefabrication of the concrete elements has helped to deliver the concept developed by AGN Niederberghaus & Partner for the Division 1 Mainz 05 football team.
Main contractor HBM Stadien und Sportstättenbau worked closely with
"Prefabricated ceilings and double wall units accelerated the flow of our construction work and gave us certainty as to the meeting of deadlines," said HBM site manager Roland Streb. "Without semi-finished precast concrete components, the construction times scheduled for this project would not have been realistic. Moreover, concrete components have a high surface quality." Prefabricated units were used for the substructure of the main stand where different functional areas are distributed over several floors. They were also used for the construction of ventilating ducts, kiosks and VIP boxes above the stands.
Precast concrete elements for the project were manufactured by Cemex's plants in Bischofsheim and Neuendorf. Bischofsheim's Jürgen Stroh said, "All the ceilings are conceived as flat ceilings and the wide spans are achieved only by means of supports where absolutely necessary and binding joists were dispensed with.
"Our ceiling systems also allow for this structurally complex construction principle. Where there are high lateral forces generated by puncture load application in the area of supports, fixing fillets were employed as mounting parts." Ceiling elements cast by Bischofsheim and Neuendorf measured up to 8m in length and had a standard width of 2.5m and thickness of 0.3m.
HBM used nearly the entire range of Cemex's walling systems to meet the double wall design of the stadium by using a mix of 0.3, 0.25, 0.2 and 0.18m thick units from both the structural and non-structural ranges. The units had shell thicknesses of 50 to 65mm and varied in height from 3 to 5.5m, so ensuring the right element was available for the work underway was a complex task.
The concrete elements were also used to accommodate a sprinkler tank built within the walling systems and Cemex used C30/37 concrete to provide the necessary watertightness. Cemex roughened the surface of the inside of both concrete shells manually in order to intensify the bond with the grouting concrete.
Cemex was delivering up to 1000m2 each of wall and ceiling units to the site every day on specially designed transportation racks that could be lifted, by two 100tonne truck-mounted cranes, direct from the low loader to the area of the site where the elements were needed.
With the main structure complete in July last year, HBM was able to get the internal fitting of the building underway and the new stadium was officially opened on 3 July.