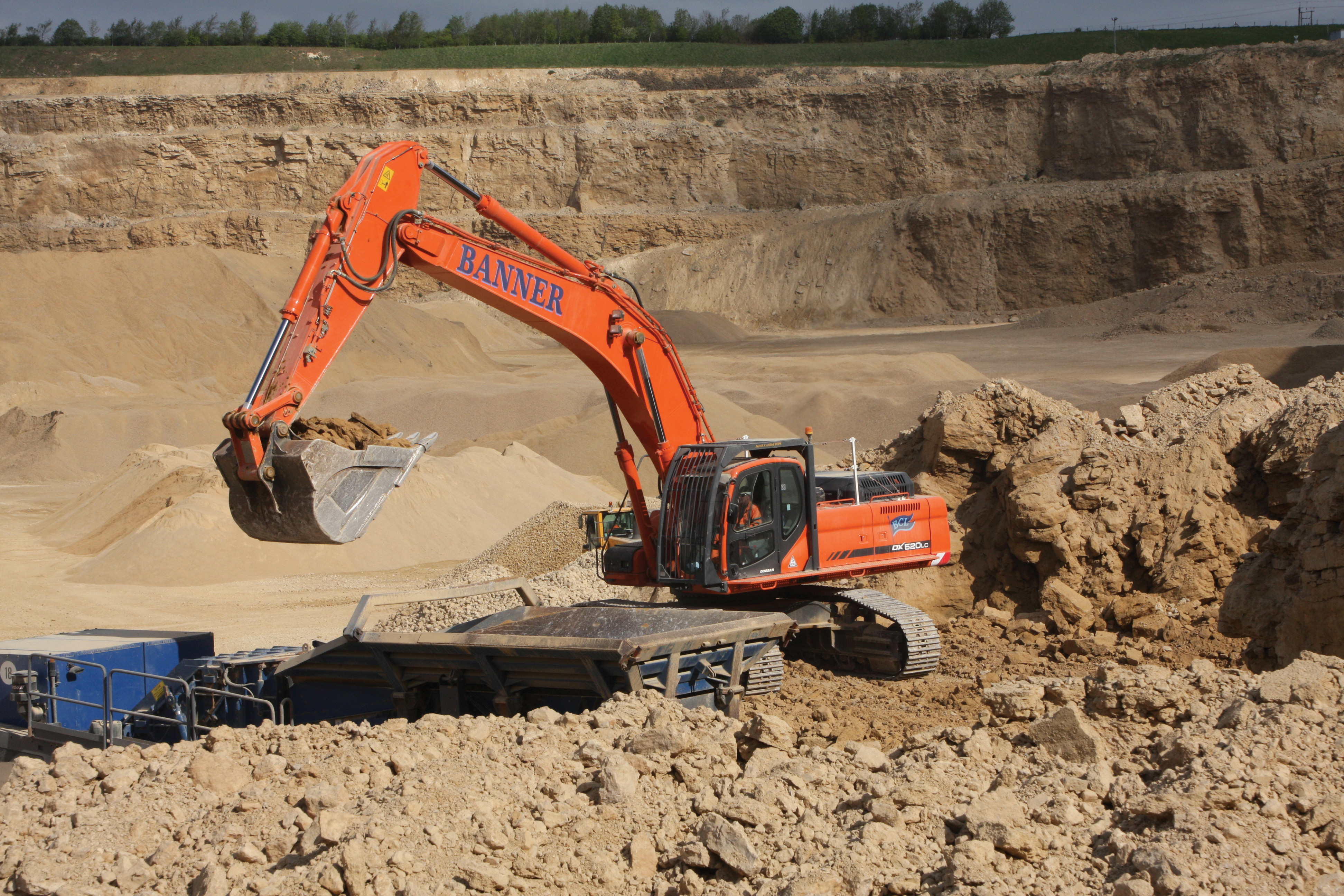
Delivery of a new prime mover at Lafarge's Thrislington limestone quarry is helping to improve productivity
Output at any quarry is always limited by the capacity of the crusher, so to ensure productivity it is important to keep a steady feed of material. Delivery of a new excavator to one of
Face excavation at Lafarge's Thrislington limestone quarry at Ferryhill, Durham has been boosted through the arrival of a new
According to Banner director Jo Banner, the previous Doosan S470LC excavator deployed to the site had put in some sterling work but there was a need for greater productivity. "Our output of crushed rock is governed largely by the rate the crushers can handle it," he explained. "It is essential our prime mover, the new DX520LC, has the ability to ensure the crushers are always working to full capacity." Thrislington extracts around 1.2million tonnes of magnesium limestone each year - half of it is used to manufacture lime products for the steel and iron industry, while the remainder is used as construction aggregates. The quarry needed to raise its output in order to meet demand from its newly installed efficient lime kilns, which have doubled the capacity of the site.
Lafarge asked Banner, which has carried out processing operations at Thrislington for nine years, to help find a solution that would maximise production at the quarry. Banner worked with local Doosan dealer Construction Plant in order to come up with the right machine for the job.
One of the main reasons the 51tonne DX520LC was selected was its 10.75m reach and 9.6m digging height which enables it to reach and dress the edges of the shot blasted areas.
"The quarry's geotechnical assessment requires a machine with the reach to scale faces safely. This makes the DX520LC a good choice," explained Banner.
"It's an important issue and we are pleased to have a machine that performs so well in this area." Sufficient engine and hydraulic power to provide good cycle times was also critical to the task. Nonetheless, operational costs are still good. "The excavator works a 10 hour shift for five days a week which equates to a saving of 100 litres of fuel a week or over 5000 litres for the year," said Banner. "This is an important saving for us." The machine's Electronic Power Optimising System (EPOS) connects the engine to the excavator's hydraulic system via a CAN communications link, helping to ensure optimum power settings are used in respect of the different demands made during digging and loading cycles, and fuel is saved as a result. .
With EPOS, the operator is provided with a power mode which makes 100% of engine power available for heavy work, and there is a normal operating mode which can be selected for general excavation, loading or lifting tasks.
When digging out the shot blasted rock and loading it into the crusher, Banner said that his operator prefers to have the machine set in power mode.
"He reports that cycle times are quicker and the whole working of the machine is smoother," he said. "Output, which can amount to several thousand tonnes each day, is certainly more than enough to ensure the crushers' insatiable appetite is always sated."