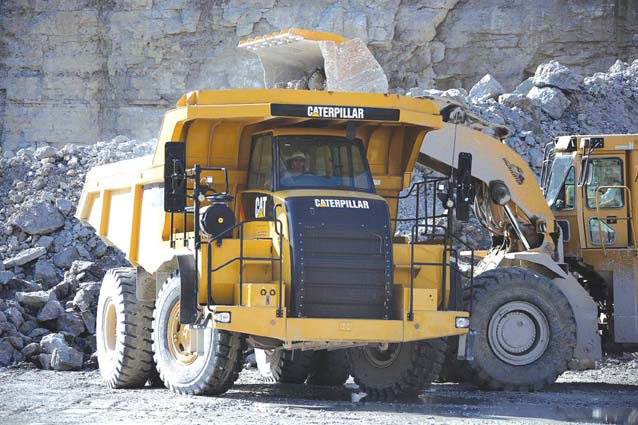
Even when you have the right machines on site, there are still adjustments that can be made to further improve efficiency. Claire Symes reports
Rising energy prices and reducing demand means that many quarry operators are focusing on trying to lower the cost per tonne of production to maximise profitability. But according to
"Matching the right equipment for the task together in the first place is important," said Porri. "But it is possible to make significant savings in production costs by checking processes used in the quarry and just making some simple changes."
Machine selection The choice of machines will depend on a variety of factors - the production requirements of the site, the existing equipment fleet, site conditions, the haul distance and future plans for the quarry. "Whatever the machines, their sizes need to be matched for the best performance," said Porri. "While it would be possible to load a truck in one cycle with a large wheeled loader or excavator, this is not the best use of assets and generally a loader that can load a truck in four to five passes is considered the most efficient." Once the fleet has been established, there are still a number of variable factors affecting the operation - machine availability, the time and fill of the bucket, the load and dump cycle and the haul roads.
"The blasting design will have an impact on loading operations, as will age, condition and availability of the load and haul fleet," explained Porri. "Shift patterns, meal breaks and weather also have an influence.
"Other factors include the length of the haul road, along with the speed of traffic on it, change of grade and condition will impact on costs," explained Porri. "But so will the dump area conditions and waiting times." By using Cat's Fleet Production and Cost software, Porri can accurately point to issues that affect almost any quarry and which can be quickly applied. "The simulation of the quarry operation based on machines and outputs based on different models [for both Cat and other manufacturers] can give an accurate idea of the impact on the cost per tonne of production." The system allows users to input the equipment fleet using machine data, cycle times, costs (to buy, operate and maintain the machines) and availability. Information about haul roads can also be entered in terms of length, grade and resistance for each segment. Cycle times, measured on site, can be added in terms of fill factors and number of passes, along with actual rock data and output.
"Looking at a theoretical 'control' quarry using a 988H wheeled laoder and two 772 trucks to load and haul well shot limestone to produce 522tonnes per hour, it would take it 1913hours to produce 1million tonnes per year, with a cost per tonne of €0.34," said Porri. "Analysis shows that this represents around 60% efficiency - there is plenty of room for improvement." By varying the parameters, Porri demonstrates the impact on overall costs.
"If the quarry was to use a 990H wheeled loader with two 775 rigid dump trucks (RDTs) then the cost per tonne drops to €0.332/tonne but with a 385C excavator and three 771 RDTs, the cost rises to €0.343/tonne," he said.
"Such a quarry could use a large wheeled loader but many sites don't want the high upfront costs and an excavator doesn't have the mobility needed. The target should be a 30 to 40second loading cycle with 90 to 110% bucket fill factor and loading completed in four to five passes. The ideal way to achieve this is V-loading with a wheeled loader completing 1.5 wheel turns from face to truck." Looking at the impact of poor technique, Porri varies the figures to show the impact of a longer loading time. If it takes 1.2 rather than 0.8mins, then the whole cycle time is extended to 9.52minutes which reduces the output to 481tonnes/hour. The impact of this is that it will take 2075hours to meet the target output of 1million tonnes/hour, adding up to €28,743 in extra costs each year.
Bad truck positioning can also impact on cost with cycle times taking longer. With just an increase of just 0.1mins per load and dump, the cycle time rises to 9.36mins and output is 490tonnes/hour. With 2040hours need to meet the target output, costs for the year are €22,546 higher than the 'control' situation.
If bucket fill factor is reduced to 80% and it takes five passes to load the truck, the load would be 42.39tonnes and give a cycle time of 8.49minutes. This gives an output of 455tonnes/hour, so the operation would need 2197hours to reach its target and cost the operator €50,320 extra to achieve.
"The impact is worse if the operator takes more time to achieve a higher bucket fill factor though," said Porri. "At 98%, it would take the operator 0.9 rather than 0.6seconds to fill the bucket. This creates an 11.18minute cycle, as well as having an impact on the fuel consumption, tyre life and structure of the machine. The net effect is that the output is reduced to 423tonnes/hour and it would take 2361hours to reach the quarry's target output for the year and cost €79,544 more." According to Porri, even looking closely at tyre and bucket choices can have an impact on the bottom line. "Many quarries still systematically use tyre chains and it does make sense if tyre life, such as side wall cuts, is a common problem," said Porri. "But on site where it is tyre wear that is the issue, chains may not resolve this. If the wear is the result of poor ground conditions, then it makes more sense to sort this out than to fit chains, although winter conditions can dictate this.
"Use of chains can increase fuel consumption by 5 to 10% and also affect transmission life. If you can get more than 4000hours from tyres, then chains should not be considered." Bucket choice can also have a major impact on productivity levels and Porri believes that smaller, less armoured buckets can offer significant advantages for rock pile penetration. "Serated edge buckets, especially in low abrasion applications, are better for fuel consumption," he said. "It is possible to get 8000hours from such designs and once it is overworn a new front edge can be welded on." Porri said that these individual situations very rarely happen in isolation and may not occur all the time but the cumulative effect may be having a major impact on costs. "The combination of factors can be easily rectified by checking exactly what is happening on site and training operators so they can understand the importance of what may seem like simple operations," he said. "Making a few basic changes means that, without any extra outlay, quarries can make the best of their existing investment."