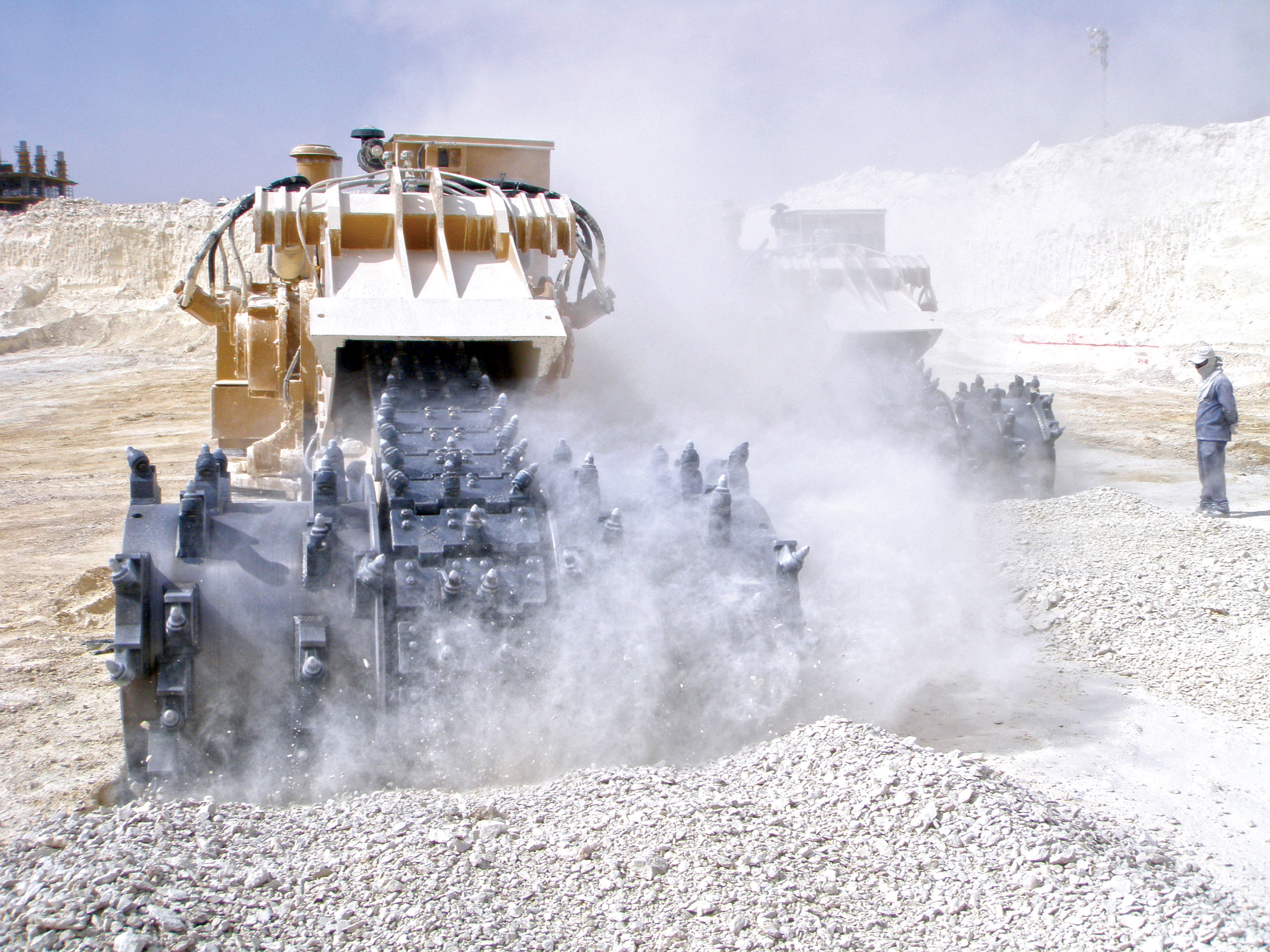
Italian manufacturer
“Conventional drill and blast methods are still the most widely used excavation methods in quarrying and open pit mining, and in many cases they remain the most productive and cost effective techniques,” says Tesmec.
However, it claims that not using explosives can be of primary importance “considering that the use of explosives is being subject to more and more restrictive regulations, controls and limitations throughout the world, and more often environmental constraint can make blasting uneconomical or undesirable.”
The company’s first Tesmec Rock Hawg was built in 2003 when it adapted a drum attachment to its trenchers and this “resulted in an innovative surface miner.”
Tesmec says that since rock cutting is generally a very discontinuous process its special flywheel gearbox is able to store energy for digging and instantly release it when required by the cutting process. It claims this delivers a torque peak up to three times the maximum torque of the hydraulic transmission and allows the Rock Hawg to achieve a much higher cutting effectiveness.
At present two Rock Hawg models are available. The 55tonne 1150XHD is powered by a Cat C13 engine and is able to excavate 3,120mm wide and up to a depth of 500mm, while the 110tonne 1475 Rock Hawg, powered by a C18 Cat engine, can excavate 3,810mm wide and up to 600mm deep.
The company’s latest technical development, now on the 1150 and 1475 models, is the electronic Trenchtronic control system aimed at improving ease of use of the Rock Hawg: increased productivity and less dependence on operator skills.
The company says the Rock Hawg produces small and quite uniform material with a tight particle size.
It points out that the machine has no built-in loader or loading capabilities because it was developed as a pure excavating machine, and “the loading phase can be easily carried out with wheeled loaders at any time.”