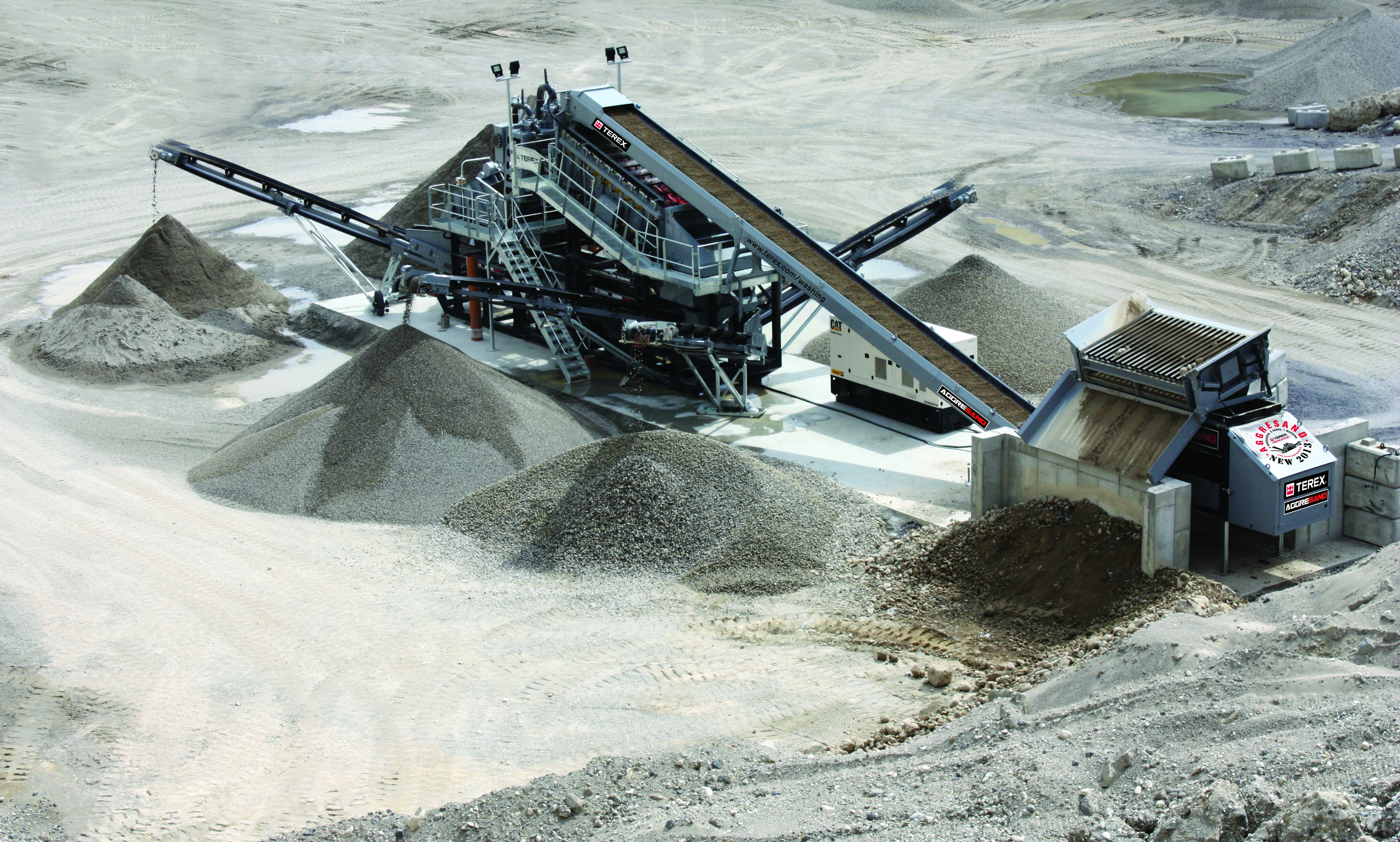
The innovative washing system, which combines aggregate washing and screening with sand processing on a modular chassis, was unveiled at Dowling Quarries’ operation near Abbeyleix, County Laois, where the company also produces concrete.
The new AggreSand, which uses TWS components, is the latest addition to the company’s product portfolio, and has been produced extensive research.
TWS engineers and sales technicians worked with the global distributor network to formulate the concept.
The modular, pre-wired and pre-plumbed plant was moved from Dungannon, County Tyrone, and was erected in around ten hours.
TWS designed a new modular hopper feeder with a 12m³ capacity in keeping with ever-increasing loading shovel sizes, and the AggreSand system has the option of five conveyors: three aggregate and two sand. The two conveyors have an automated radial wheel drive system that increases stockpiling capacity to 350m³.
An automatic tipping grid and a 12ft two-deck vibrating grid complete with variable speed belt feeder are all controlled from the main operator interface and radio control unit.
TWS says the wide feed conveyor has a direct drive electric motor and gearbox arrangement while the company opted for the 165R-3 (three-deck, two-bearing) rinsing screen, saying that its riveted construction reduces the stress associated with welded construction methods. The 165R-3 gives 7.54m² of screening area on all three decks.
Two centrifugal slurry pumps (coarse and fine) are used to pump material from both sides of the sump tank into two hydrocyclones, which remove silts and clay (material below 63micron): these are sent to the water treatment plant. The heavier material (above 63micron) exits the bottom of the hydrocyclones into a rubber lined box where blending can take place if required.
All components are designed so they can be easily dismantled and placed into standard 40ft containers.