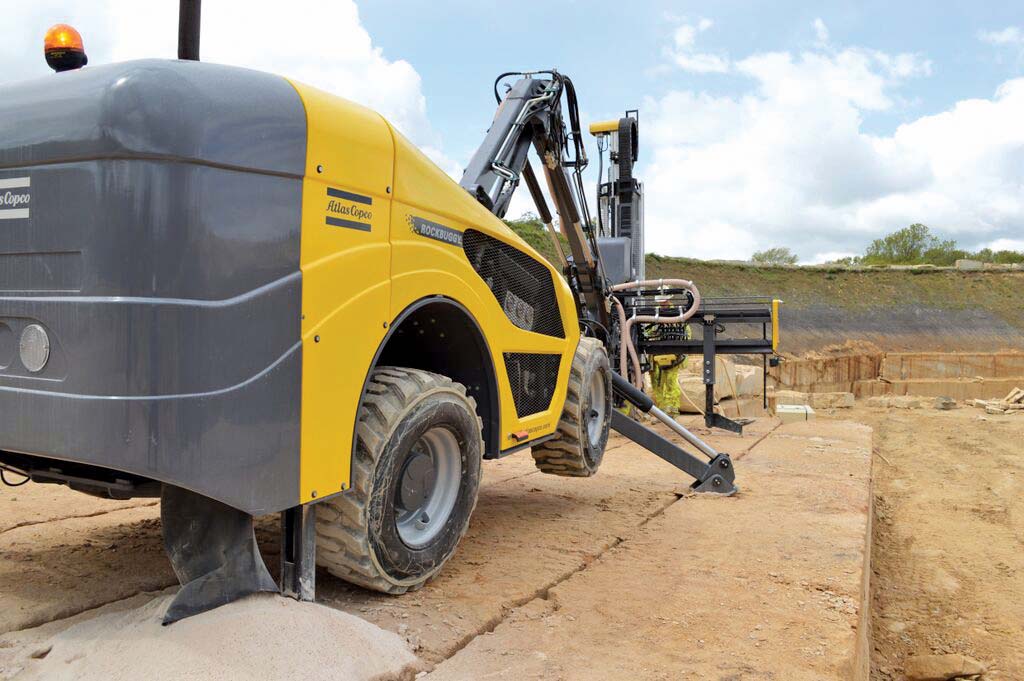
Atlas Copco recently secured the first sale of its new ‘Rock Buggy’.
Purchased by Glebe Stone Sales, in Ancaster, near Grantham, central England, the Rock Buggy comes out of
Glebe Stone is a family owned business, producing quality Ancaster limestone to the masonry industry all over the UK.
Andy Smith, the company’s production director, said: “With the demand for our products, we knew we would have to look at increasing our production to satisfy the expanding market. Examining ways of increasing that productivity, as well as meeting safety, environmental and quality standards led us to selecting the Atlas Copco Rock Buggy.”
After visiting Bagnolo, near Turin, the manufacturing site for Atlas Copco dimensional stone equipment, to see the Rock Buggy production facilities and to trial the equipment, Smith said: “We instantly knew that this could deliver. We had a solution to our production problems.
“After delivery to Glebe Stone, it was an instant success and outperformed all expectations. It reduced our drilling costs both in fuel and man hours. Where it was taking us 30 minutes to set up and drill a hole, now it’s taking two minutes to drill the same hole. And with the automatic drilling we know each hole is exactly where it should be, giving us a quality pre-split. It has also improved the health and safety of our employees thanks to the rig’s remote control system allowing our drillers to work away from the quarry face. Also, the driller is not being exposed to dust because the rigs’ onboard dust collector removes the dust from their immediate working environment.”
The drilling unit is an important part of Glebe’s growth plans; the efficiency achieved via the rig programming system that provides automatically drilled holes, and with excellent quality, means that the Rock Buggy has proved to be the solution to the production problem for the company.
This is the first step for Atlas Copco UK in establishing its Dimensional Stone Industry products into the UK, and Atlas Copco is looking forward to introducing the whole of its DSI range into the UK and hopes to achieve similar success to that of the Atlas Copco surface drilling rigs in the quarrying industry. Through quality, reliability, safety and efficiency there is no reason why it couldn’t achieve that goal.
Another technological innovation is seeing
Inspection types include Technical Analysis (TA1) inspection forms and Preventive Maintenance (PM) checklists. The checklists are serial number specific, which gives users pinpoint guidance to the Cat equipment they depend on every day.
Users can add ratings, make comments and take pictures during the inspection. Subsequent inspection reports lists items requiring attention, from immediate to normal. If users are inspecting machines with optional equipment not listed on their checklists, they can document that equipment and add the information to the form.
Besides eliminating the need for paper, Cat Inspect allows typed or dictated notes, off-line inspections, forwarding to the Cat dealer, and PDF distribution. Important alerts are also sent to VisionLink, so users can get an even better overall view of their fleets. Cat dealers and technicians have tested, improved and used Cat Inspect over the past year, ensuring an outstanding experience for all customers, especially those using a mobile device on inspections for the first time.
Cat Inspect is available at no charge for Android devices through Google Play, for Apple iPhones and iPads through the App Store on iTunes and for Windows 8.1 tablets through the Windows Store.