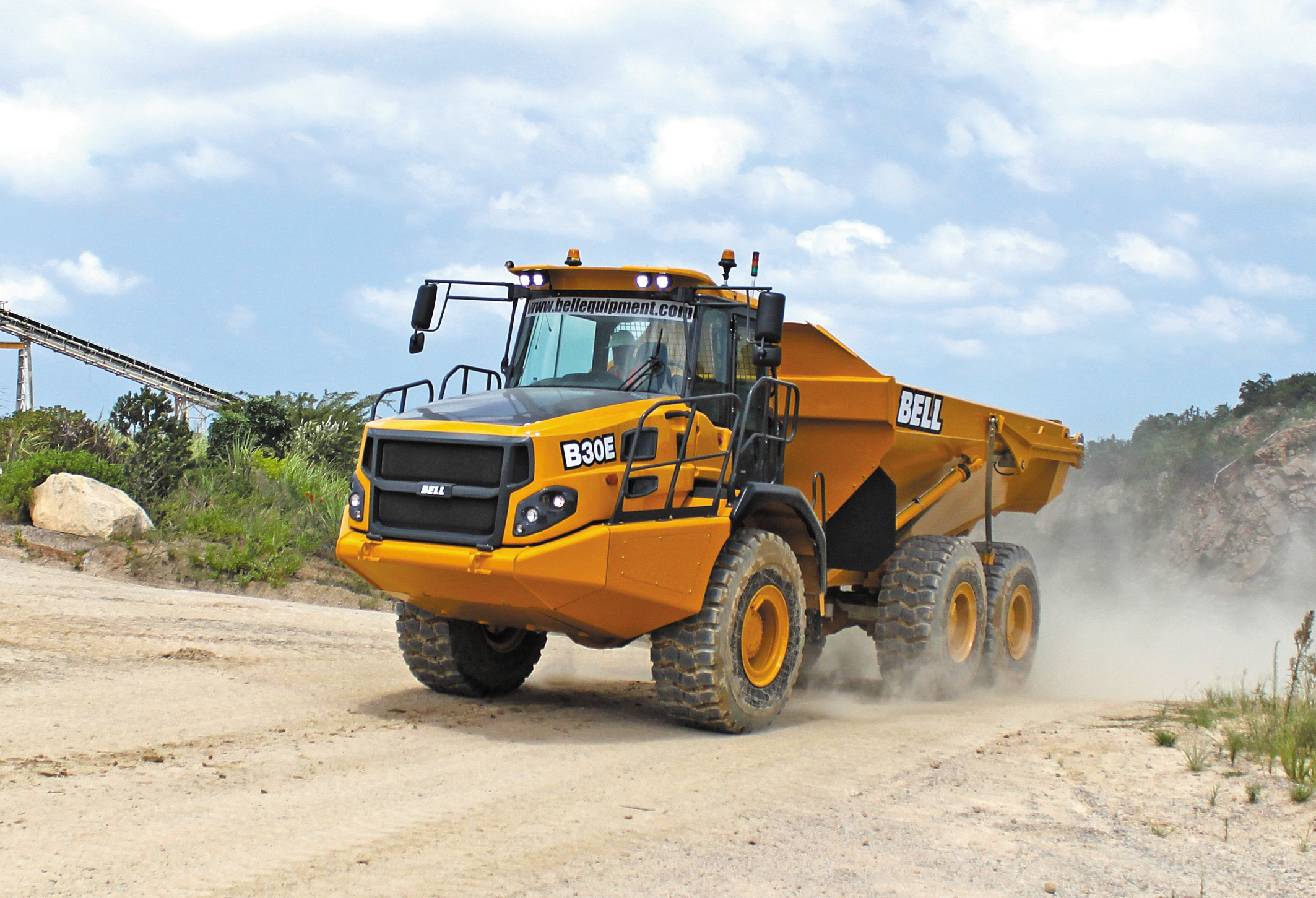
There are many factors to be considered in hauling systems selection but costs can be lowered by making the right choice as Patrick Smith reports
There are various ways in which to move overburden and quarried material from the digging face to the crusher, and from primaries to secondary and tertiary crushing and screening operations.
For many, the rigid dump truck remains the machine of choice; a range of sizes capable of carrying anything from 25tonnes to many hundreds of tonnes efficiently and consistently is a persuasive argument.
However the articulated dump truck (ADT) has become an increasingly popular option in smaller quarries, particularly those where it is difficult to guarantee good haul road conditions. Though primarily an earthmoving and muckshifting machine, the move to 40 and even 50tonne ADTs (
Both truck types are competing for market space with a growing call for long distance conveyors, and for mobile crusher and moveable conveyor operations that put the primary crusher at the quarry face.
For example, at the Marocca Quarry (see Quarry Profile), near the Italian capital Rome, a
The German
To compete, trucks have had to prove that they deliver on a cost per tonne basis, which means driving down fuel consumption and pushing up productivity. In Europe and North American markets engine emissions have been driving truck design, as increasingly stringent standards call for ever-lower output of particulates and exhaust gases such as oxides of nitrogen. Indeed, Bell Equipment is now launching its new B25E and B30E ADTs to its range of equipment that also includes wheeled loaders and excavators. The ADTs use Tier 4 Interim/Stage IIIB compliant Mercedes diesels rated at 210kW for the B25E and 240kW for the B30E and feature selective catalytic reduction (SCR) technology to help reduce emissions, and which also helps lower fuel consumption. The transmissions for the B25E and B30E have been changed to
“We wanted to go to a common family across the range,” says Marc Schürmann, managing director of Bell Equipment Europe.
Meanwhile, choosing which system of hauling to use depends on a variety of factors, says Larry Tate, hauling products segment manager,
“There is no single hauling system that’s best for all jobs. Thorough evaluation of the sites ensures customers can use the hauling systems that will provide the best fit for their local needs,” says Tate.
He says that as an example by choosing the optimum hauling system on a 500,000m³ project savings of up to US$100,000 (€77,000) are possible.
However, there are many factors to be considered in hauling systems selection but costs can be lowered by avoiding carry-back (reduced productivity, increased fuel consumption per tonne); avoiding overload and underload conditions (reduced machine life/equipment underutilisation); minimising wear (reduced machine life/increased repair costs) and avoiding excessive load times (reduced productivity).
“Making do with a smaller excavator with poor pass match results in 29% less production,” says Tate.
He cites a 40tonne off-highway truck example, assuming a target payload of 36,572kg; weight of crushed stone is 1,600kg/m³ and the average load cycle (with exchange time) is 20 seconds. A 49tonne excavator with a bucket capacity of 2.69m³ loading the truck requires eight load cycles to achieve the target at a maximum of 23 trucks loaded each hour, meaning a maximum of 230 trucks loaded in a ten-hour shift and maximum production in that time of 7,747.2tonnes. Using a 74tonne excavator requires six load cycles loading 30 trucks/hour; 300 trucks in a ten-hour shift, resulting in a maximum production of 10,944tonnes in that time.
Swedish Caterpillar dealer Pon Equipment solved customer Flygts Excavation and Transport’s carry-back problem, says the company.
Flygts excavates and transports natural clay for processing, and being a sticky material it was hard to release a full load.
“Our trucks were coming back with large amounts of clay still in the body,” says Peter
“We suggested a try-and-buy. Flygts could try a Cat 730 ejector articulated truck for one year as a rental. If it liked it, Flygts could buy it and deduct the rental cost from the purchase price,” says Anders Carlsson, product manager, Pon Equipment.
Such ejector trucks are used in quarry management for haul road maintenance and reclamation work.
After initial doubts about the system, Peter Flygt saw that the ejector could release a full load with no remaining material.
Pon and Flygts, which now has two Cat 730 Ejector ADTs and three other standard articulated trucks working around the clock, worked together to create a special high, hinged tailgate that covers the entire rear.
A launch date has not yet been revealed for Bell Equipment’s biggest ever truck with a capacity of 55tonnes.
“Our competitors will be the smaller class of rigid haulers,” says Marc Schürmann.
The aim is to offer lower fuel consumption and capital cost while providing a machine with high availability.
Of the new Bell Equipment E series, he added that the increased travel speed is of particular benefit when the trucks are empty and are returning to the loading point, as it means they can be driven faster and reduce overall cycle times, with a benefit to productivity. The load capacity has been increased slightly for both machines, with the B25E able to carry 24tonnes in its 15m³ dump body and the B30E able to carry 28tonnes in its 17.5m³ dump body.
“We can also do remote diagnostics now and it is a big plus point, especially as we are developing into markets such as Russia.”
Meanwhile,
For example, it says a combination of the forward turning point, special tandem bogie and sloping rear frame results in rough and soft terrain capabilities and avoids the need for electronic aids such as traction control.
It also points to the new Payload and Cycle Count Meter for the DA30 and DA40, which uses load sensors to provide a read-out of the payload with an accuracy of +/- 5%. Another feature is a new economy mode developed by Doosan, which controls the engine rated speed on the DA range automatically when it is activated. It is said to be ideal for fuel saving on long distance haul roads.
Doosan also reports orders for 12 new DA30 ADTs from Dutch civil engineering contractor Ploegam, based in Vinkel. Supplied by Lieshout-based
S J Staadegaard & Zonen, the first six ADTs were ordered for work on a project won by a joint venture of Ploegam and the Van den Biggelaar Group. The other six machines were ordered separately for work on another project subsequently won by Ploegam in Lent.
The engine system, a result of thousands of hours of bench and multi-application field testing, and already installed in more than a million Volvo trucks, is set for launch when the new legislation comes into force in January 2014.
Volvo CE will use selective catalytic reduction (SCR) in addition to a diesel particulate filter (DPF) and exhaust gas recirculation (EGR) in order to meet the requirements of the forthcoming Stage IV/Tier 4 Final emissions legislation, in most instances.
“We are in the final stages of developing what constitutes a radical overhaul of our product range, one that will see a large number of new machines launched over the next 12 to 24 months,” says Olney.
Last year Volvo CE received its second red dot best of the best design award win for its A40F ADT (in 2011 its L220G wheeled loader received a red dot product design award for its “fuel efficient and productive design.”) At the 2012
Volvo CE’s A40F articulated hauler is the flagship of its F-Series range of haulers and features improvements in design, functionality and maintenance.
“The potential of the OBW in unlocking the secret of hauler productivity shouldn’t be underestimated, and I’m gratified that the Innovation Awards judges recognised its significance,” says Anders Larsson, head of Volvo CE’s technology function.
OBW-equipped haulers are fitted with a load indicator light mounted outside the machine and clearly visible to the operator of the wheeled loader or excavator that is loading the hauler. A yellow light comes on when at part load, which changes to a green light at nominal load, finally turning red when overloaded.
“The OBW system also offers the ability to unlock a wealth of previously inaccessible information, such as the weight of ‘carry-back’ left in the haul body after tipping. OBW helps show the true productivity of the machine, combining fuel efficiency with tonnes of mass moved. Additionally, it can help in improving operator performance. By measuring number of cycles, total of mass moved and load efficiency, site managers can compare and improve the productivity of its operators,” says Volvo CE.
With growing demand for 100tonne trucks, the EH1700-3 will probably be the most in demand. At a rated 95.2tonnes, the EH1700-3 is powered by a Tier 2
As with the majority of truck manufacturers,
Only recently it completed one of 2013’s biggest ADT deals in the UK when L.Lynch Plant Hire bought 12 Terex TA300s through Terex UK distributor, TDL Equipment, as part of the company’s £12 million (€14.2 million) investment in new equipment.