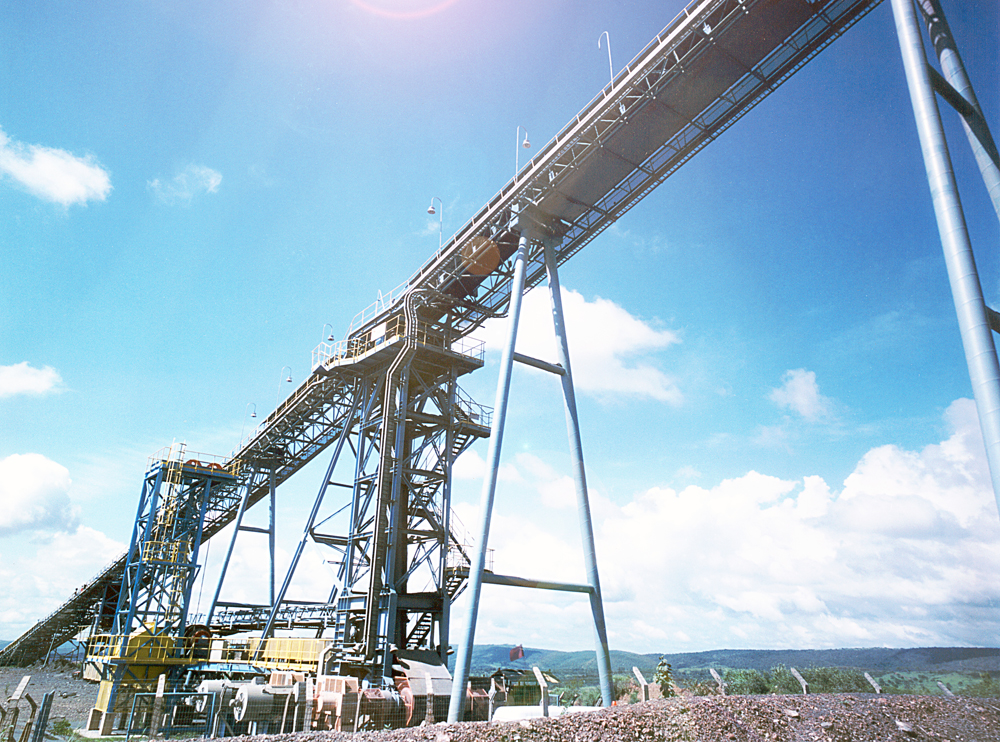
Major quarrying crushing and screening plant players such as Terex Materials Processing brands Powerscreen, Terex Finlay and EvoQuip, and the Wirtgen Group’s Kleemann brand have entered the conveyor belt market in recent years.
Now Metso Outotec has unveiled its first full range of overland conveyors. The range is said to provide economical and reliable bulk material transport for both open-pit and underground operations at the lowest total cost of ownership.
Lars Duemmel, vice president, Bulk Material Handling Systems at Metso Outotec, said: “In mining and minerals processing applications, conveying is one of the most efficient and safest ways to transport bulk material. It is often referred to as the backbone of the entire process. The robust design of our overland conveyors allows for capacities of up to 20,000 tonnes per hour, including over five kilometres on a single flight for a seamless process. What is also important is that you can achieve power savings of up to 30% with the patented Energy Saving Idlers (ESI).”
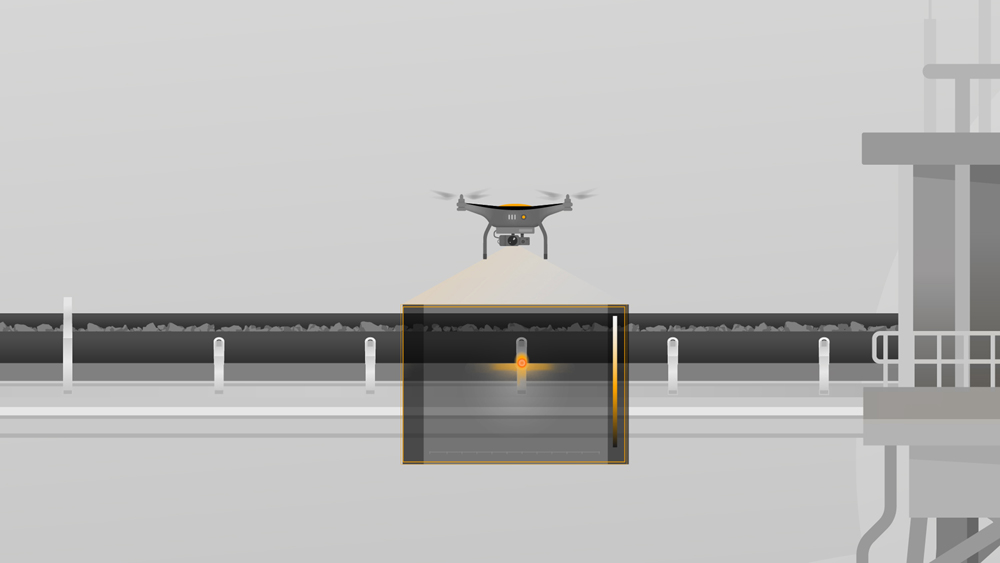
Duemmel said that thanks to Metso Outotec’s extensive process engineering capability and proven installations worldwide, the company can support its customers with complete end-to-end conveyor solutions. He added: “This includes concept studies and definitions for all types of terrains and route types with horizontal and vertical curves. Our expertise also covers post-installation services and maintenance, including a full range of accessories, belts and components featured in the recently launched Conveyor Solutions Handbook.”
Meanwhile, Continental has developed a service solution for monitoring conveyor belt systems to permit early identification of weak points along a conveyor belt before damage resulting in unscheduled and cost-intensive downtimes. The new technology-based approach developed to a prototype stage in the Incubator program of Co-pace, the company’s startup organisation, offers a combination of visual and acoustic inspection. It also permits the highly accurate and efficient, data-assisted planning of maintenance intervals, replacing the conventional and usually very laborious manual process with sensor-based technologies.
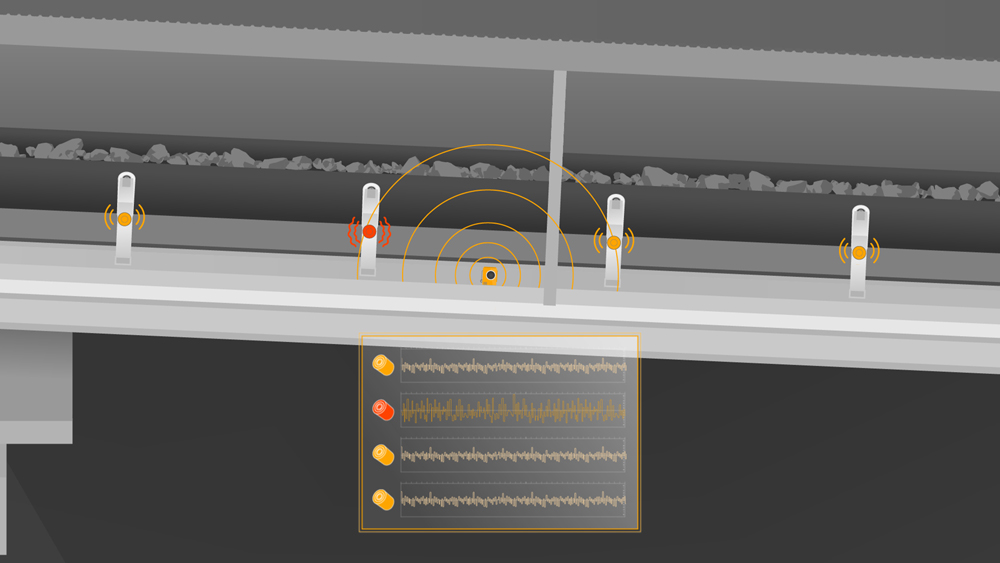
Idlers are essential components of a belt conveyor and are crucial to ensuring smooth conveying operations. A conveyor belt on a medium-sized conveyor with a total belt length of 40 kilometres runs over some 120,000 idlers. Continental notes that around 30% of the operational faults with belt conveyors are attributable to idler defects that cannot be detected promptly. The new service offering is in response to this fact. It comprises a hybrid solution that addresses different applications and sections.
On the one hand, an inspection of open sections and operations is carried out from the air using a drone equipped with infrared and RGB (red, green and blue) cameras that monitor both sides of the belt conveyor. As soon as the drone has flown over the section under inspection, it returns to an autonomous charging station to upload the data collected to the relevant cloud via an IoT (Internet of Things) module during the charging process. The image data is processed with an AI (artificial intelligence)-assisted algorithm and analysed for any detected idler defects.
Continuous maintenance in covered sections or underground conveyors, on the other hand, is carried out using fixed microphones installed every 20 to 25 metres that capture frequency variations in the numerous idlers. The audio recording is conducted twice a day, with the data being uploaded to the cloud specified above. Events that indicate a damaged idler are then analysed using an AI-based algorithm.
“Conventional and often manual inspection methods can be very time-consuming, imprecise or even dangerous for service technicians because of the belt length or local circumstances such as underground routing and enclosed sections. Documentation is also often performed manually, with reports having to be subsequently manually inputted into the relevant datasets. Maintenance intervals also frequently follow a fixed rotational principle, meaning that measures required on short notice to avoid or prevent conveyor failures cannot be carried out in a timely manner,” explains Clemens Panzer. He has played a leading role in the new development as a member of the interdisciplinary team set up for this project.
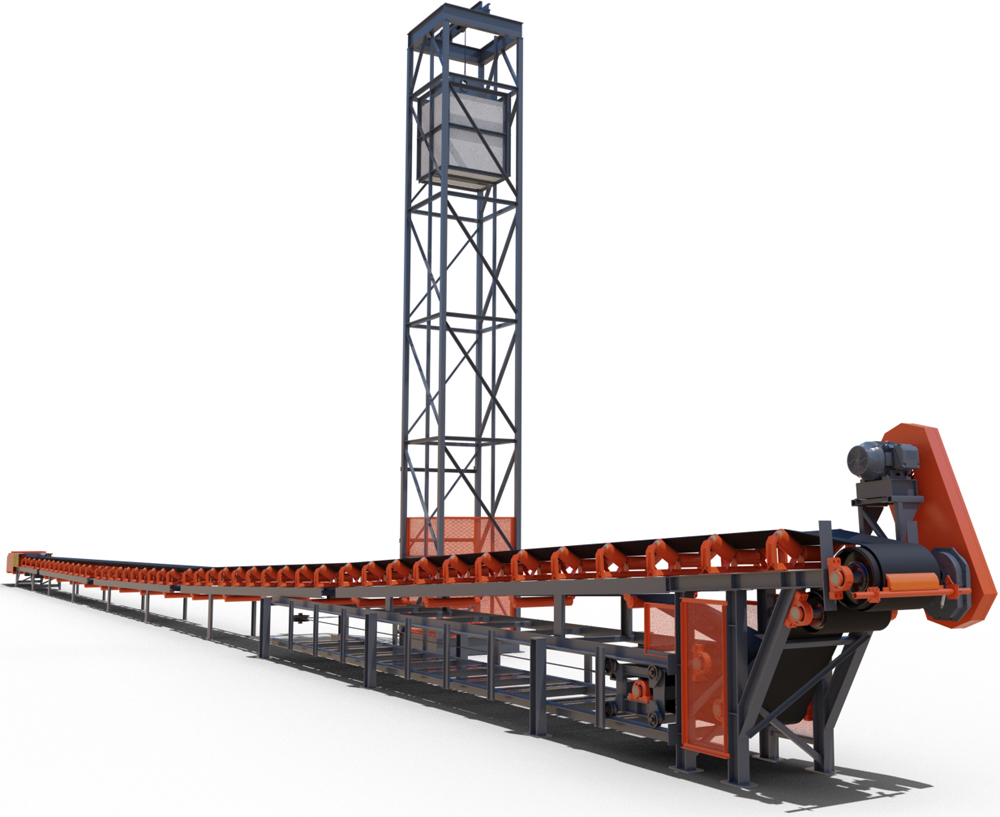
By contrast, sensor-based inspection permits data-assisted remote monitoring of system condition, with the result that potential damage can be detected at an early stage and avoided. Panzer says another benefit is that the data collected will automatically be made available in a digital form in the future via a user-friendly interface. He continues: “The data can be viewed at any time and permits the demand-driven planning of relevant service periods. Changes in the conveyor condition over an extended period can be analysed significantly better using the stored historical data, and the anticipated service life of the components can also be better estimated.”
To date, the Continental solution has tested successfully in initial field trials. Further pilot projects are likely with other interested parties. The system is due to be operational later this year.
The Incubator operated by startup organisation Co-pace provided the necessary environment for the rapid validation of technology- and market-relevant assumptions that underpin the concept and initial data collections and tests for creating the prototype. An expert interdisciplinary team examined the system’s feasibility, viability and attractiveness based on data, interviews with experts and customer feedback. For instance, recording audio signals resulted in the successful analysis of idlers – whereas only a visual inspection had been initially planned. The journey from concept to prototype took just two months.
Superior Industries, a U.S.-based manufacturer and global supplier of bulk material processing and handling systems, is launching a new model of its popular Zipline Overland Conveyors. The new EXT Series expands the modular conveyor product line range for longer and wider material handling applications.
Zipline Conveyors target bulk producers looking for overland conveyors that require little or no pre-engineering for express deliveries and are designed for quick assembly in the field. Today, with the addition of the new EXT Series, Zipline Conveyors are available in lengths up to 2,500 (762m) feet and belt widths up to 48 (1,220mm) inches.
Between the head and tail are a series of 40-foot (12.2m) intermediate sections designed with an 8-inch (200mm) channel and 2-foot (610mm) tall support stands. Standard Zipline Conveyor models are equipped with mechanical take-ups for shorter distances, but the new EXT Series includes a gravity take-up tower to accommodate longer-distance overland conveying.
All of the conveyor components – like the pulleys, idlers and scrapers – are also manufactured in-house. This unique advantage means higher quality, faster deliveries and all-inclusive support from Superior Industries.
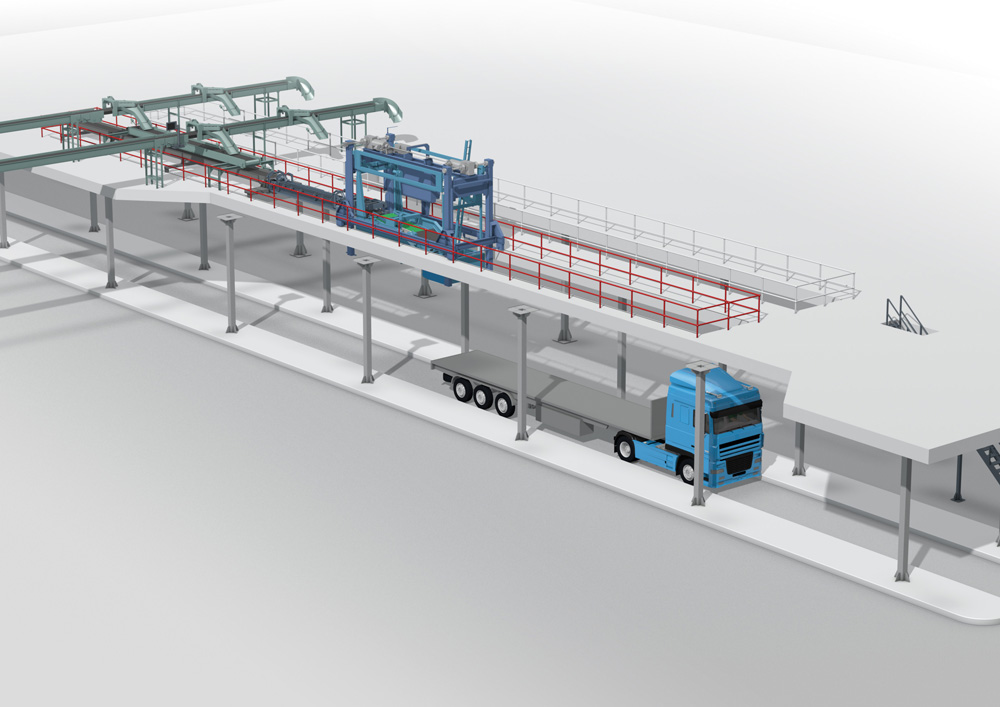
BEUMER’s autopac loading technology has proven a big success among building material product producers and other industry customers for many years – with more than 1,000 machines installed globally.
The latest version of autopac – the 2400/3000 construction series - enables users to automatically load bagged bulk materials like cement on trucks and simultaneously palletise them - quickly and with the desired packing pattern. The BEUMER autopac consumes very little energy, is reliable even in dusty environments and can be easily operated and maintained. The machine is also suitable for paper, HDPE (high-density polyethylene) and PP (polypropylene) valve bags.
The truck with the empty loading space slowly stops under the BEUMER autopac. To load and palletise the cement bags, the employee enters the number of bags, the packing pattern and the desired number of rows and layers in the BEUMER Group Human Machine Interface (HMI). Laser positioning aids have been mounted to the left and right of the BEUMER autopac. They project the outer contours of the machine with a clearly visible red beam on the loading space, helping the operator to position the loading head on the truck.
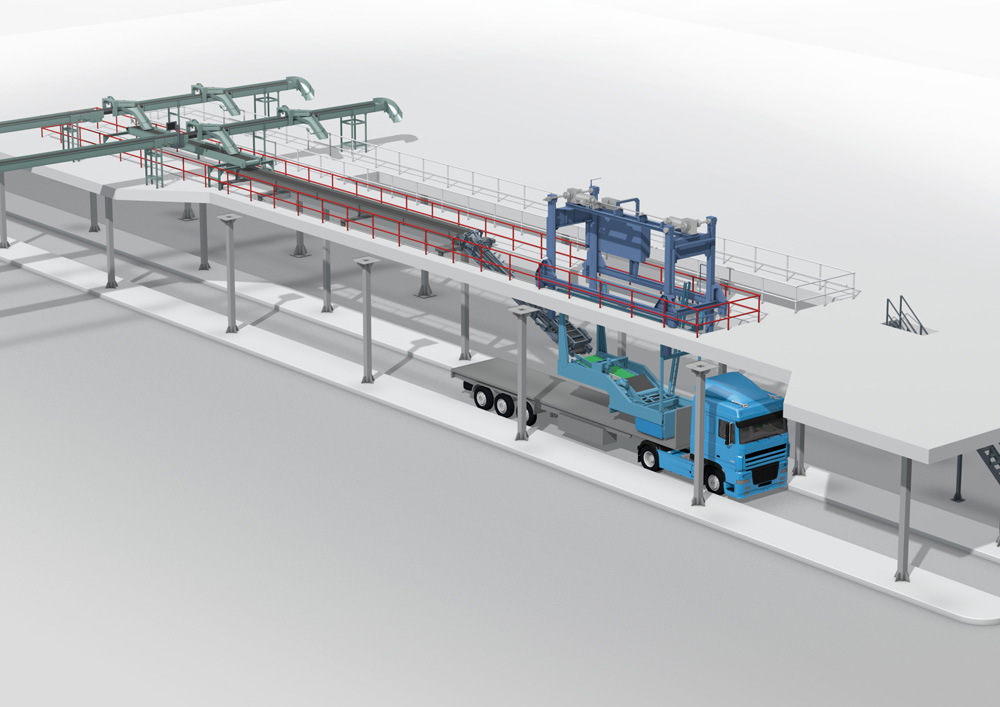
The BEUMER autopac starts the automatic loading process, bag by bag, directly from the filling machine via belt conveyors onto the truck. “With our BEUMER autopac, we have a system in our product range that can load trucks automatically,” explains Markus Peitzmeier, senior sales manager at BEUMER Group. “And it does so extremely reliably.” The use of an electronic bag counting system makes sure that the truck is neither underloaded nor overloaded. Manual corrections are completely omitted. “The program control recalculates the height setting for each layer,” Peitzmeier explains.
In order to attain the highest possible degree of stability for the whole load on the truck, and in order to optimally utilise the loading space, two mirror-inverted layers are palletised next to one another. Two belt conveyors positioned one above the other flatten the bags before the loading process and thus remove the air from them. After being positioned, the bags are also pressed by the loading head, which makes the stack more compact and more stable. Meanwhile, the next layer is already being prepared. The bag feeding lines can be adapted to the customer’s installation conditions. Corresponding technical solutions are available for variable conveyor lines.
“The BEUMER autopac is ideally suited for use in emerging countries, where the transhipment of bagged bulk goods is increasing. In these countries, labour costs are rising, and it is becoming more and more difficult to find appropriate personnel for this kind of work,” says Peitzmeier. Manual truck loading is exhausting and usually requires two people who alternate with their colleagues for each loading process due to the heavy physical work involved. Furthermore, there is the high level of dust formation, which negatively affects the employees’ health. During the manual loading process, the loading performance as well as the quality of the bag stacks often fluctuates. “These problems are eliminated with our BEUMER autopac,” says Peitzmeier. “One employee is able to operate more than one machine.” This enables owners to optimise processes, achieve high loading capacities and work very efficiently from bagging up to loading.
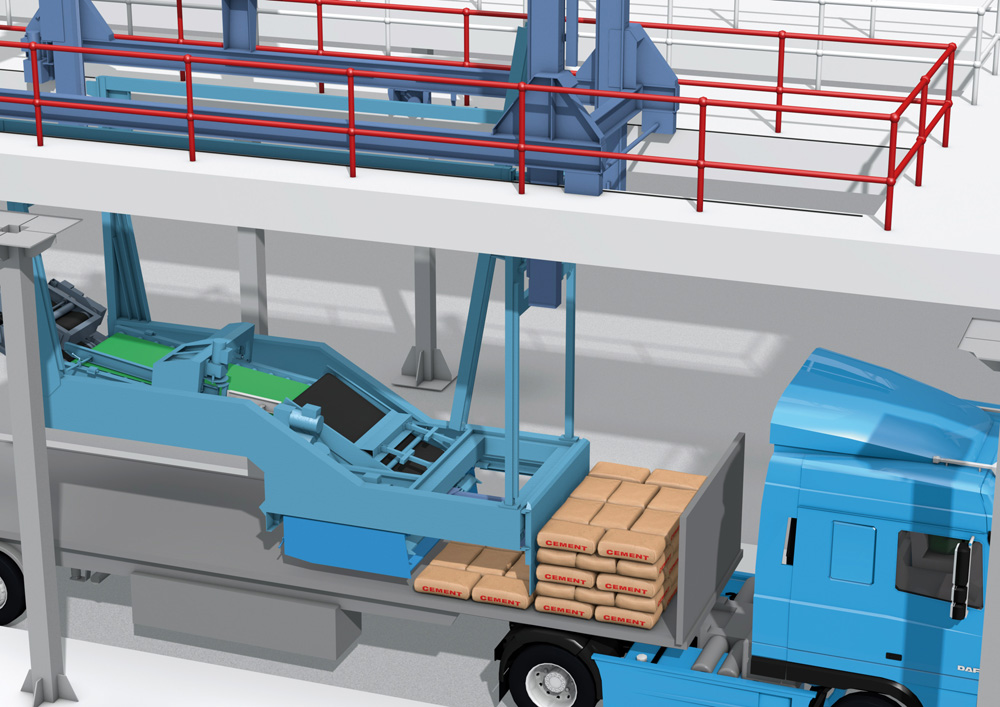
Depending on the bag dimensions and their length and width ratio, the user has flexibility in layer formation. Patterns of ten, twelve and twenty bags per layer are possible. The very low positioning height of the loading head contributes to the gentle handling of the bags, as they are supported during the loading process and not lifted or possibly deformed, as is the case with vacuum suction modules.
The system provider uses the specially developed BEUMER Group HMI for operating the BEUMER autopac. This is a touch panel with optimised user interface and graphic navigation. This operator panel provides users with an easily understandable and intuitive interaction concept, enabling them to define efficient working sequences.
BEUMER Group says it is committed to thoroughly evaluating its products against economy, ecology and social responsibility. “We follow a total value of ownership (TVO) approach. This means, we consider the system in its entirety, not only from its cost side,” says Peitzmeier. “For example, we continuously look to reduce energy and resource consumption in the production cycle and during operation of the systems, all while keeping emissions to a minimum. When loading 3,000 bags per hour, each weighing 50 kilograms, power consumption is held below 0.1 kWh per ton.”
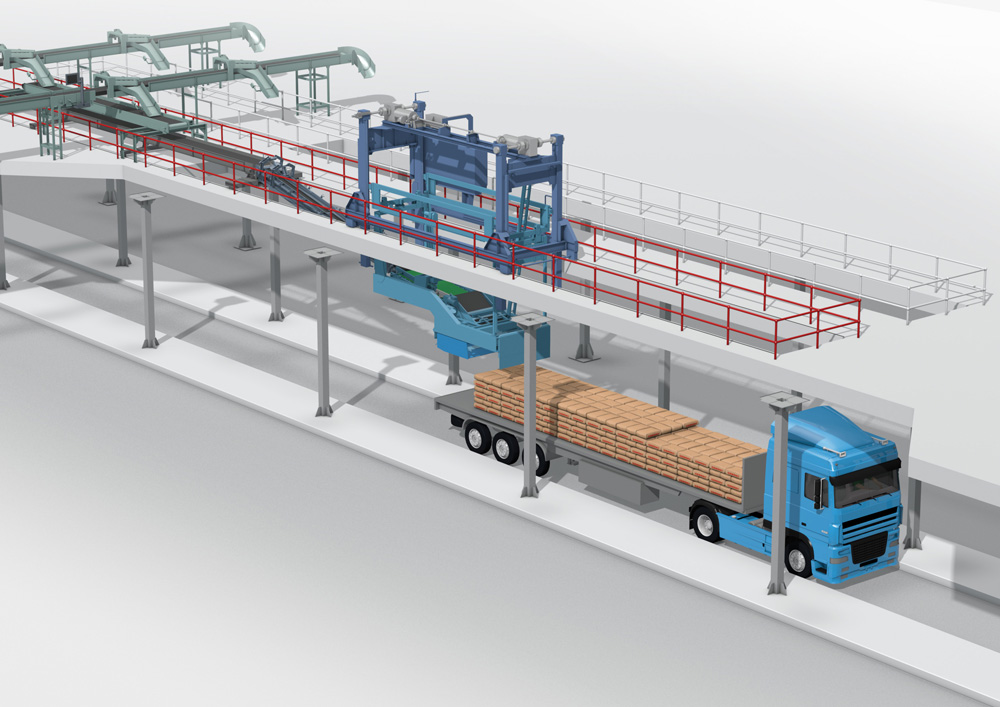
The BEUMER autopac is both energy-efficient and extremely robust, as demonstrated by the many systems that have been in daily use for decades. “The machine has been designed for heavy-duty operation to resist extreme ambient conditions like heat, high air humidity, dust formation and the three-shift operation in packing plants”, says Peitzmeier. In addition, the owner profits from a smaller footprint compared to other loading systems. With its compact design, the BEUMER system can be quickly and easily maintained, is reliable and safe to operate. “This is supported by the fact that we have only integrated electromechanical components,” describes Peitzmeier. “This eliminates the need for hydraulic or pneumatic components, which wear out fast or require expensive compressed air.”
As for the sensors, the system provider installs contactless proximity switches that reliably transmit signals without mechanical contacts. The use of high-quality photocells ensures signal transmission even under difficult environmental conditions. Also, the sensors used increase both machine capacity and product quality and ensure that a wide variety of materials and bags are safely handled with the BEUMER autopac. “Remote maintenance is also possible, around the clock, every day of the week, during which we can connect to the system from the BEUMER site,” says Peitzmeier. “This increases system availability because we can react faster without having to travel long distances.” The pre-assembled modules allow the BEUMER autopac to be quickly installed and commissioned at the customer’s site.
“The fully automatic loading process enables users to achieve a constantly high loading performance and stack quality,” promises Peitzmeier. “Our BEUMER autopac has proven itself in the cement industry worldwide for decades.”